ZBC2000 Materials PCB Manufacturer
ZBC2000 Materials PCB Manufacturer,ZBC2000 Materials PCBs utilize advanced materials known for their high thermal conductivity and excellent electrical properties. These PCBs are designed to handle high-frequency signals and power efficiently, making them ideal for applications in RF/microwave communication systems, ระบบเรดาร์, and aerospace electronics. ZBC2000 Materials PCBs offer low loss tangent and stable dielectric constant across a wide range of frequencies, ensuring reliable signal transmission and minimal signal distortion. They are crucial in industries where precise signal integrity and high-performance reliability are paramount. ZBC2000 Materials PCBs are engineered with precision to meet stringent requirements for high-speed data transfer and electromagnetic compatibility (อีเอ็มซี).
What is a ZBC2000 Materials PCB?
A ZBC2000 Materials PCB refers to a type of high-frequency circuit board that utilizes ZBC (Zirconium Boron Carbide) ceramic materials. ZBC2000 is known for its excellent thermal conductivity, low dielectric constant, and high mechanical strength, making it ideal for applications requiring high-frequency performance and reliability.
These PCBs are often used in RF/microwave applications where signal integrity and minimal signal loss are critical. The ZBC2000 material’s properties help in reducing signal attenuation and ensuring stable electrical performance across a range of frequencies. These boards are typically used in telecommunications, ระบบเรดาร์, การสื่อสารผ่านดาวเทียม, and other advanced electronic systems where high-speed data transfer and precision are essential.
Manufacturing ZBC2000 Materials PCBs involves specialized processes to ensure the ceramic material’s properties are maintained, including precise layering, sintering at high temperatures, and ensuring uniformity in dielectric constant and thermal conductivity across the board. This attention to detail is crucial for achieving consistent and reliable performance in demanding applications.
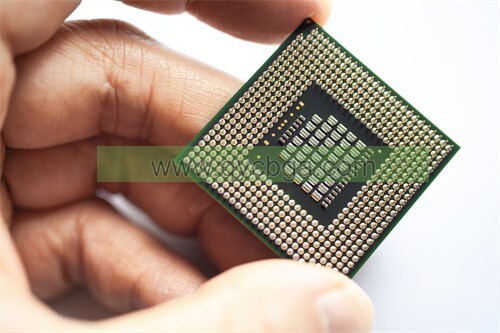
ZBC2000 Materials PCB Manufacturer
What are ZBC2000 Materials PCB Design Guidelines?
Designing PCBs with ZBC2000 materials involves several key guidelines to ensure optimal performance and reliability:
- Dielectric Constant and Loss Tangent: Understand and account for the dielectric constant (εr) and loss tangent (δ สีแทน) of ZBC2000. These properties affect signal propagation, so accurate characterization and simulation are essential.
- Material Thickness: ZBC2000 PCBs come in various thicknesses. Choose thicknesses appropriate for your application to achieve desired impedance and mechanical stability.
- การซ้อนชั้น:Design an appropriate layer stackup considering the impedance control, signal integrity, and thermal management requirements. อย่างเป็นแบบฉบับ, ZBC2000 PCBs may have multiple layers to accommodate complex RF designs.
- Transmission Line Design: Use controlled impedance transmission lines to minimize signal loss and reflections. Match the trace widths and spacing to achieve the desired characteristic impedance based on the dielectric constant of ZBC2000.
- ผ่านการออกแบบ: Optimize via structures to minimize impedance mismatch and signal loss. Use proper via design techniques such as microvias or blind/buried vias depending on the density and complexity of the PCB layout.
- การจัดการความร้อน: ZBC2000 has good thermal conductivity, but heat dissipation can still be a concern in high-power applications. Design for adequate heat sinking and thermal vias if needed to maintain PCB reliability.
- ตําแหน่งส่วนประกอบ: Place critical components strategically to minimize signal path lengths and reduce parasitic effects. Ensure adequate clearance and spacing to maintain signal integrity.
- Manufacturing Considerations: Communicate with PCB manufacturers experienced in handling ZBC2000 materials. They can provide insights into fabrication techniques, such as sintering temperatures and handling procedures, to ensure consistent material properties throughout the PCB.
โดยปฏิบัติตามแนวทางเหล่านี้, designers can leverage the unique properties of ZBC2000 materials to achieve high-performance RF/microwave PCBs that meet stringent requirements for signal integrity, ความน่าเชื่อถือ, และการจัดการความร้อน.
What is the ZBC2000 Materials PCB Fabrication Process?
The fabrication process of ZBC2000 Materials PCB involves several specialized steps to ensure the material’s properties are preserved and the PCB meets performance requirements:
- การเตรียมวัสดุ: ZBC2000 ceramic materials are prepared in a controlled environment to ensure purity and consistency. The materials are typically in powder form and undergo stringent quality control measures to meet specific dielectric constant and thermal conductivity requirements.
- Mixing and Forming: The ZBC2000 powder is mixed with binders and solvents to form a slurry or paste. This mixture is then shaped into green sheets using methods like tape casting or extrusion. The green sheets are carefully handled to maintain uniform thickness and density.
- Layering and Lamination: Multiple green sheets are stacked according to the PCB’s layer stackup design. Conductive patterns are often printed on each layer using techniques like screen printing or inkjet printing. The layers are then laminated together under controlled pressure and temperature to form a solid composite.
- Via Formation: หลังจากเคลือบ, via holes are drilled or laser drilled through the PCB stack where interconnections are required between different layers. Special attention is paid to via design to ensure signal integrity and impedance control.
- Metallization:The PCB is metallized by depositing thin layers of conductive materials such as copper onto the surfaces and inside the vias. This metallization process is critical for forming electrical connections and ensuring conductivity throughout the PCB.
- Etching and Patterning: Excess copper is etched away using chemical processes, leaving behind the desired conductive traces and pads according to the PCB design. Advanced techniques like plasma etching may be used to achieve precise trace geometries.
- การตกแต่งพื้นผิว:Surface finishes such as immersion gold, เอนิก (นิกเกิลแช่ทองแบบไม่ใช้ไฟฟ้า), หรือ OSP (สารกันบูดความสามารถในการบัดกรีอินทรีย์) are applied to protect exposed copper and ensure solderability during assembly.
- การประกันคุณภาพ: ตลอดกระบวนการผลิต, quality checks are performed to verify dimensional accuracy, layer registration, metallization thickness, and overall adherence to design specifications. Non-destructive testing methods may be employed to ensure reliability.
- Final Testing and Inspection: Once fabrication is complete, the PCB undergoes electrical testing and inspection to verify functionality, การจับคู่อิมพีแดนซ์, and overall performance characteristics. This ensures that the PCB meets stringent quality standards before being shipped to customers.
By following these steps with precision and expertise, manufacturers can produce ZBC2000 Materials PCBs that offer superior performance in high-frequency and RF/microwave applications, characterized by low loss, high thermal conductivity, and excellent reliability.
How do you manufacture a ZBC2000 Materials PCB?
Manufacturing a ZBC2000 Materials PCB involves a series of specialized steps to ensure the material’s properties are preserved and the PCB meets stringent performance requirements:
- การเตรียมวัสดุ: ZBC2000 ceramic materials, known for their high thermal conductivity and low dielectric constant, are carefully prepared in powder form. Quality control measures are implemented to ensure the material meets precise specifications for purity and consistency.
- Formulation and Mixing: The ZBC2000 powder is mixed with binders, solvents, and additives to create a homogeneous slurry or paste. This mixture is crucial in forming the green sheets that will become the layers of the PCB.
- Green Sheet Formation: The slurry or paste is then processed into green sheets through methods like tape casting or extrusion. These green sheets are handled delicately to maintain uniform thickness and density, crucial for ensuring consistent electrical properties across the PCB.
- การซ้อนชั้นและการเคลือบ: Multiple green sheets are stacked according to the PCB’s design requirements. Conductive patterns are applied to each layer using techniques such as screen printing or inkjet printing. The layers are then laminated together under controlled temperature and pressure to form a solid composite structure.
- Via Formation: หลังจากเคลือบ, via holes are drilled or laser drilled through the PCB stack where interconnections are needed between different layers. Careful attention is given to via design to maintain signal integrity and impedance control throughout the PCB.
- Metallization:The PCB undergoes a metallization process where thin layers of conductive materials, typically copper, are deposited onto the surfaces and inside the vias. This step is critical for creating electrical pathways and ensuring conductivity throughout the PCB.
- Etching and Patterning: Excess copper is removed through chemical etching processes, leaving behind the desired conductive traces and pads as per the PCB design specifications. Advanced techniques like plasma etching may be employed for precise trace definition and geometry.
- การตกแต่งพื้นผิว: Surface finishes such as immersion gold, เอนิก (นิกเกิลแช่ทองแบบไม่ใช้ไฟฟ้า), หรือ OSP (สารกันบูดความสามารถในการบัดกรีอินทรีย์) are applied to protect exposed copper and ensure solderability during assembly processes.
- Quality Control: ตลอดกระบวนการผลิต, rigorous quality checks are performed to verify dimensional accuracy, layer registration, metallization thickness, and adherence to design specifications. Non-destructive testing methods may be used to ensure the PCB’s reliability and performance.
- Final Testing and Inspection: Once fabrication is complete, the PCB undergoes comprehensive electrical testing and inspection to validate functionality, การจับคู่อิมพีแดนซ์, and overall performance characteristics. This ensures that the ZBC2000 Materials PCB meets high standards of quality and reliability before being released for use in RF/microwave applications.
โดยทําตามขั้นตอนการผลิตเหล่านี้อย่างพิถีพิถัน, PCB manufacturers can produce ZBC2000 Materials PCBs that offer exceptional performance in high-frequency environments, characterized by minimal signal loss, excellent thermal management, and reliability under demanding operational conditions.
How much should a ZBC2000 Materials PCB cost?
The cost of ZBC2000 Materials PCBs can vary significantly based on several factors:
- Board Size and Complexity: Larger boards or those with intricate designs requiring more layers, tighter trace widths, and complex via structures will generally cost more due to increased material and manufacturing time.
- Material Cost: ZBC2000 ceramic materials are specialized and may be more expensive compared to standard FR4 or other conventional PCB substrates. The cost of the raw material itself can significantly influence the overall PCB cost.
- Manufacturing Processes: Specialized processes such as lamination under controlled conditions, precise drilling of vias, and high-precision etching techniques may add to the manufacturing cost compared to standard PCB fabrication.
- ปริมาณ: การประหยัดจากขนาดนําไปใช้ในการผลิต PCB. Larger production runs typically lower the cost per unit due to efficiencies in material usage, setup, and manufacturing processes.
- Surface Finish and Additional Features: Different surface finishes like immersion gold or ENIG, as well as additional features like impedance control, controlled dielectric constant, and specific tolerances, can affect the overall cost of the PCB.
- ซัพพลายเออร์และที่ตั้ง: PCB costs can also vary based on the supplier’s location, their expertise in handling ZBC2000 materials, and their production capabilities.
Given these factors, it’s challenging to provide an exact cost without specific details about the PCB’s design, size, quantity, and additional requirements. เพื่อการกําหนดราคาที่ถูกต้อง, it’s recommended to consult with PCB manufacturers experienced in producing ZBC2000 Materials PCBs. They can provide detailed quotations based on your specific project needs and requirements.
What is a ZBC2000 Materials PCB base material?
A ZBC2000 Materials PCB base material refers to the substrate or core material used in the fabrication of PCBs that utilizes ZBC2000 ceramic. ZBC2000 (Zirconium Boron Carbide) is a specialized ceramic material known for its high thermal conductivity, low dielectric constant, and excellent mechanical properties, making it ideal for high-frequency and RF/microwave applications.
In the context of PCB fabrication, ZBC2000 is typically used as a substrate material where conductive traces and components are integrated to form electronic circuits. The PCB base material made from ZBC2000 ceramic provides several advantages:
- High Thermal Conductivity: ZBC2000 has excellent thermal conductivity properties, which helps in efficiently dissipating heat generated during operation, crucial for high-power applications.
- Low Dielectric Constant: The low dielectric constant of ZBC2000 reduces signal loss and improves signal integrity in high-frequency applications, supporting stable and reliable electrical performance.
- Mechanical Strength: ZBC2000 ceramic materials offer high mechanical strength and durability, providing robustness to the PCB against physical stresses and environmental conditions.
- Compatibility with High Frequencies: Due to its low loss tangent and stable dielectric properties, ZBC2000 is well-suited for RF/microwave PCBs where maintaining signal integrity across a wide range of frequencies is essential.
Manufacturing ZBC2000 Materials PCBs involves specialized processes to ensure the ceramic’s properties are preserved and optimized for electronic applications, including precise layering, metallization, and surface finishing techniques tailored to the material’s characteristics.
ทั้งหมด, ZBC2000 Materials PCB base materials are chosen for their superior performance in high-frequency applications, offering designers and engineers a reliable solution for demanding electronic designs requiring high thermal efficiency and signal integrity.
Which company makes ZBC2000 Materials PCB?
ปัจจุบัน, there are several companies producing ZBC2000 material PCBs, mainly focusing on high-frequency and microwave electronic applications. ZBC2000 is a ceramic material known for its excellent thermal conductivity and low dielectric constant, making it particularly suitable for high-frequency PCB designs requiring reliability.
In the PCB industry, companies manufacturing ZBC2000 material PCBs typically possess advanced material processing and manufacturing technologies to ensure the material’s properties are effectively preserved and optimized during the PCB manufacturing process. These companies not only have high-precision machining capabilities but also customize complex PCB structures according to customer requirements to meet various high-frequency electronic application demands.
As a specialized PCB manufacturing company, we are also capable of producing ZBC2000 material PCBs. We have advanced production equipment and an experienced technical team capable of handling high-performance materials such as ZBC2000, ensuring high-quality standards are met throughout the manufacturing process.
Specifically, our company offers the following services and advantages:
- Technical Expertise: With years of PCB manufacturing experience, particularly in the high-frequency and microwave PCB fields, our engineering team possesses deep technical knowledge to understand and apply the characteristics of ZBC2000 material. We provide professional design advice and solutions to customers.
- Customization Capability: We can customize ZBC2000 material PCBs according to specific customer requirements, including complex layer stack designs, precise impedance control, specific size and shape requirements, etc. Our manufacturing processes and equipment support multi-layer, high-density PCB production to meet various technical challenges and performance requirements.
- การประกันคุณภาพ:We strictly adhere to international standards and quality management systems to ensure every PCB produced meets customer specifications and expected performance. We conduct comprehensive testing and inspection to verify electrical characteristics, dimensional accuracy, และความน่าเชื่อถือ, ensuring high-quality products upon delivery.
- Customer Service: We emphasize communication and collaboration with customers, committed to providing satisfactory solutions and excellent service. Our team is always ready to engage actively with customers on design details, technical requirements, and production progress to ensure smooth project completion and achieve expected goals.
โดยสรุป, as a proficient manufacturer capable of producing ZBC2000 material PCBs, we are dedicated to providing global customers with high-quality, high-performance electronic solutions. We possess competitive technical capabilities and production capacities, eager to cooperate with customers to advance the development and application of high-frequency electronic technology.
คืออะไร 7 คุณภาพของการบริการลูกค้าที่ดี?
The seven qualities of good customer service are:
- ตอบ สนอง: รวดเร็วและทันเวลาในการตอบคําถามของลูกค้า, ร้อง ขอ, และประเด็น. Customers appreciate quick responses that show their concerns are valued.
- ความเห็นอกเห็นใจ: Understanding and showing empathy towards customers’ feelings, situations, และความต้องการ. Empathetic responses help build rapport and trust with customers.
- ความชัดเจน: Communicating clearly and effectively to ensure customers understand the information provided. Avoiding jargon and using simple language can enhance clarity.
- มือ อาชีพ: Conducting interactions with professionalism, including being courteous, สุภาพ, and maintaining a positive attitude, even in challenging situations.
- ความรู้: Possessing sufficient knowledge about products, บริการ, and policies to provide accurate information and solutions to customers’ queries and problems.
- Efficiency:Completing transactions, resolving issues, and delivering service in a timely manner without unnecessary delays or complications.
- Proactivity: Anticipating customer needs and taking initiative to provide solutions or suggestions before issues arise. Proactive service can exceed customer expectations.
These qualities collectively contribute to a positive customer experience and help in building long-term relationships with customers.
คําถามที่พบบ่อย
What is ZBC2000 material?
ZBC2000 is a ceramic material known for its high thermal conductivity and low dielectric constant, making it ideal for high-frequency and RF/microwave applications in PCBs.
What are the benefits of using ZBC2000 Materials PCBs?
ZBC2000 Materials PCBs offer superior thermal management, low signal loss, excellent mechanical strength, and stability across a wide range of frequencies, crucial for high-performance electronic applications.
What types of applications are ZBC2000 Materials PCBs suitable for?
ZBC2000 Materials PCBs are used in telecommunications, ระบบเรดาร์, การสื่อสารผ่านดาวเทียม, อวกาศ, and other high-frequency electronic devices requiring reliable signal transmission and thermal efficiency.
How are ZBC2000 Materials PCBs fabricated?
The fabrication process involves preparing ZBC2000 ceramic into green sheets, layering them with conductive patterns, drilling vias, metallizing, แกะ สลัก, and applying surface finishes to create functional PCBs that meet specific design requirements.
What are the key considerations when designing with ZBC2000 Materials PCBs?
Designers should focus on impedance control, การจัดการความร้อน, signal integrity, and mechanical stability. Understanding ZBC2000’s dielectric properties and thermal conductivity is crucial for optimal PCB performance.
Where can ZBC2000 Materials PCBs be sourced?
Several specialized PCB manufacturers and suppliers produce ZBC2000 Materials PCBs, offering custom fabrication services tailored to specific application needs.
What are the cost considerations for ZBC2000 Materials PCBs?
Costs vary based on factors such as board size, complexity, material thickness, surface finishes, and production volume. Consulting with PCB manufacturers can provide detailed cost estimates based on specific project requirements.