พื้นผิวแพ็คเกจ MIS คืออะไร?
ผู้ผลิตพื้นผิวแพ็คเกจ MIS,ม. (พื้นผิวเชื่อมต่อระหว่างกันแบบขึ้นรูป) วัสดุพิมพ์แพ็คเกจเป็นโซลูชันที่ซับซ้อนสําหรับชุดประกอบอิเล็กทรอนิกส์ขนาดกะทัดรัดและมีประสิทธิภาพสูง. พื้นผิวนี้รวมทั้งวงจรและโครงสร้างทางกลไว้ในส่วนประกอบแม่พิมพ์เดียว, ลดความจําเป็นในการใช้เลเยอร์และตัวเชื่อมต่อเพิ่มเติม. พื้นผิว MIS ให้ประสิทธิภาพทางไฟฟ้าที่ยอดเยี่ยม, เสถียรภาพทางกล, และการจัดการความร้อน. มักใช้ในยานยนต์, ทางการแพทย์, และอุปกรณ์อิเล็กทรอนิกส์สําหรับผู้บริโภค, ซึ่งการประหยัดพื้นที่และความน่าเชื่อถือเป็นสิ่งสําคัญ. โดยทั่วไปจะสร้างจากวัสดุ เช่น อีพอกซีเรซินหรือเทอร์โมพลาสติก, พื้นผิวบรรจุภัณฑ์ MIS ช่วยให้กระบวนการผลิตมีประสิทธิภาพและอํานวยความสะดวกในการพัฒนาอุปกรณ์อิเล็กทรอนิกส์ที่มีขนาดเล็กและทนทาน, มั่นใจได้ถึงประสิทธิภาพสูงสุดในการใช้งานที่หลากหลาย.
ม. (โลหะ-ฉนวน-เซมิคอนดักเตอร์) พื้นผิวบรรจุภัณฑ์หมายถึงประเภทของพื้นผิวบรรจุภัณฑ์ที่ใช้ในอุปกรณ์เซมิคอนดักเตอร์. เป็นส่วนประกอบพื้นฐานในวงจรรวม, จัดเตรียมแพลตฟอร์มสําหรับการติดตั้งและเชื่อมต่อชิปเซมิคอนดักเตอร์ภายในแพ็คเกจ.
พื้นผิวแพ็คเกจ MIS โดยทั่วไปประกอบด้วยหลายชั้น, รวมถึงชั้นโลหะ, ชั้นฉนวน, และชั้นเซมิคอนดักเตอร์. ชั้นโลหะใช้สําหรับการเชื่อมต่อระหว่างอุปกรณ์เซมิคอนดักเตอร์และวงจรภายนอก. ชั้นฉนวนให้การแยกทางไฟฟ้าระหว่างส่วนประกอบต่างๆ บนพื้นผิว. ชั้นเซมิคอนดักเตอร์, มักเป็นซิลิกอน, อาจใช้เพื่อวัตถุประสงค์ต่างๆ เช่น การรวมอุปกรณ์หรือฟังก์ชันเพิ่มเติม.
ทั้งหมด, พื้นผิวแพ็คเกจ MIS มีบทบาทสําคัญในประสิทธิภาพ, ความน่าเชื่อถือ, และการจัดการความร้อนของอุปกรณ์เซมิคอนดักเตอร์โดยให้การเชื่อมต่อทางไฟฟ้าและการสนับสนุนโครงสร้างในขณะที่หุ้มฉนวนส่วนประกอบต่างๆ จากกัน.
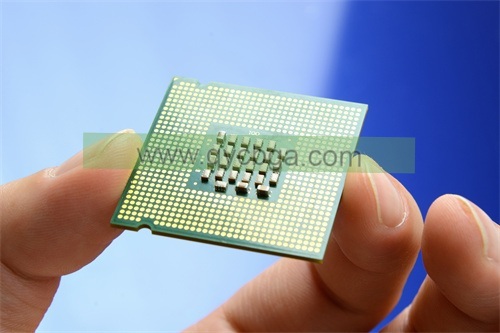
ผู้ผลิตพื้นผิวแพ็คเกจ MIS
คู่มืออ้างอิงการออกแบบพื้นผิวแพ็คเกจ MIS.
การออกแบบ ม. (โลหะ-ฉนวน-เซมิคอนดักเตอร์) วัสดุพิมพ์แพ็คเกจ ต้องพิจารณาปัจจัยต่างๆ อย่างรอบคอบเพื่อให้มั่นใจถึงประสิทธิภาพสูงสุด, ความน่าเชื่อถือ, และความสามารถในการผลิต. นี่คือคู่มืออ้างอิงที่สรุปประเด็นสําคัญของการออกแบบพื้นผิวบรรจุภัณฑ์ MIS:
- การเลือกวัสดุ: เลือกวัสดุสําหรับแต่ละชั้นของพื้นผิวตามไฟฟ้า, ร้อน, และคุณสมบัติทางกล. วัสดุทั่วไป ได้แก่ ซิลิกอนสําหรับชั้นเซมิคอนดักเตอร์, วัสดุฉนวน เช่น ซิลิคอนไดออกไซด์หรือซิลิกอนไนไตรด์, และโลหะต่างๆสําหรับชั้นเชื่อมต่อ.
- การกําหนดค่าเลเยอร์: กําหนดการกําหนดค่าโลหะที่เหมาะสมที่สุด, ฉนวน, และชั้นเซมิคอนดักเตอร์ตามความต้องการเฉพาะของอุปกรณ์เซมิคอนดักเตอร์. พิจารณาปัจจัยต่างๆ เช่น การกําหนดเส้นทางสัญญาณ, การกระจายพลังงาน, และการจัดการความร้อน.
- การออกแบบการเชื่อมต่อโครงข่าย: ออกแบบเค้าโครงการเชื่อมต่อโครงข่ายเพื่อลดความล่าช้าของสัญญาณ, ครอสทอล์ค, และการสูญเสียพลังงาน. ใช้เทคนิคต่างๆ เช่น การจับคู่อิมพีแดนซ์, การป้องกันสัญญาณ, และการกระจายกราวด์และพลังงานที่เหมาะสมเพื่อเพิ่มประสิทธิภาพทางไฟฟ้า.
- ความสมบูรณ์ของสัญญาณ: ทําการวิเคราะห์ความสมบูรณ์ของสัญญาณเพื่อให้แน่ใจว่าการออกแบบพื้นผิวเป็นไปตามข้อกําหนดทางไฟฟ้าที่กําหนด, เช่นเวลาสัญญาณ, ระดับแรงดันไฟฟ้า, และขอบเสียงรบกวน. ใช้เครื่องมือจําลองเพื่อสร้างแบบจําลองพฤติกรรมของสัญญาณและตรวจสอบการออกแบบ.
- ผู้จัดการความร้อนt: รวมคุณสมบัติต่างๆ เช่น จุดแวะระบายความร้อน, ฮีตซิงก์, และแผ่นระบายความร้อนเพื่อกระจายความร้อนที่เกิดจากอุปกรณ์เซมิคอนดักเตอร์อย่างมีประสิทธิภาพ. ตรวจสอบให้แน่ใจว่าการออกแบบพื้นผิวสามารถรองรับภาระความร้อนได้โดยไม่เกินขีดจํากัดอุณหภูมิที่อาจลดประสิทธิภาพหรือความน่าเชื่อถือของอุปกรณ์.
- ความสามารถในการผลิต: ออกแบบพื้นผิวโดยคํานึงถึงความสามารถในการผลิต, พิจารณาปัจจัยต่างๆ เช่น การจัดตําแหน่งเลเยอร์, ความแม่นยําในการลงทะเบียน, และความเข้ากันได้กับกระบวนการกับเทคนิคการผลิต เช่น โฟโตลิโธกราฟี, แกะ สลัก, และการฝาก.
- ข้อควรพิจารณาด้านความน่าเชื่อถือ: จัดการกับข้อกังวลด้านความน่าเชื่อถือ เช่น ความเครียดเชิงกล, การย้ายถิ่นทางไฟฟ้า, และการหมุนเวียนความร้อนโดยการเพิ่มประสิทธิภาพการออกแบบพื้นผิวและเลือกวัสดุและกระบวนการผลิตที่เหมาะสม. ทําการทดสอบความน่าเชื่อถือเพื่อตรวจสอบการออกแบบภายใต้สภาวะการทํางานที่หลากหลาย.
- การรวมแพ็คเกจ: ประสานงานการออกแบบพื้นผิวกับการออกแบบบรรจุภัณฑ์โดยรวมเพื่อให้แน่ใจว่าเข้ากันได้กับกระบวนการประกอบและอินเทอร์เฟซภายนอก. พิจารณาปัจจัยต่างๆ เช่น ขนาดบรรจุภัณฑ์, ฟอร์มแฟคเตอร์, และความเข้ากันได้กับเทคโนโลยีบรรจุภัณฑ์มาตรฐาน.
- เอกสารและแนวทางปฏิบัติ: จัดทําเอกสารการออกแบบพื้นผิวอย่างละเอียด, รวมถึงข้อมูลจําเพาะ, ไดอะแกรมเค้าโครง, คําแนะนําในการผลิต, และแนวทางการออกแบบ. ให้แนวทางที่ชัดเจนสําหรับการผลิต, สภา, การทดสอบ, และการประกันคุณภาพเพื่อให้มั่นใจถึงความสม่ําเสมอและความน่าเชื่อถือในการผลิต.
- การเพิ่มประสิทธิภาพแบบทําซ้ํา: ทําซ้ําอย่างต่อเนื่องในการออกแบบพื้นผิวตามข้อเสนอแนะจากการจําลอง, การทดสอบ, และประสบการณ์การผลิตเพื่อปรับปรุงประสิทธิภาพ, ความน่าเชื่อถือ, และความคุ้มค่าเมื่อเวลาผ่านไป.
โดยปฏิบัติตามหลักเกณฑ์และแนวทางปฏิบัติที่ดีที่สุดเหล่านี้, คุณสามารถออกแบบพื้นผิวแพ็คเกจ MIS ที่ตรงตามข้อกําหนดที่เข้มงวดของอุปกรณ์เซมิคอนดักเตอร์สมัยใหม่ในขณะที่มั่นใจได้ถึงประสิทธิภาพสูง, ความน่าเชื่อถือ, และความสามารถในการผลิต.
วัสดุที่ใช้ในพื้นผิวแพ็คเกจ MIS คืออะไร?
วัสดุที่ใช้ใน ม. (โลหะ-ฉนวน-เซมิคอนดักเตอร์) วัสดุพิมพ์แพ็คเกจ ถูกเลือกตามไฟฟ้า, ร้อน, และคุณสมบัติทางกล. วัสดุทั่วไป ได้แก่:
- ชั้นเซมิคอนดักเตอร์: ซิลิกอนมักใช้เป็นวัสดุเซมิคอนดักเตอร์เนื่องจากเข้ากันได้กับกระบวนการผลิตเซมิคอนดักเตอร์และคุณสมบัติทางไฟฟ้าที่ดีเยี่ยม.
- ชั้นฉนวน: วัสดุฉนวน เช่น ซิลิคอนไดออกไซด์ (ซิโอทู), ซิลิกอนไนไตรด์ (Si3N4), และโพลีเมอร์ประเภทต่างๆ ถูกนํามาใช้เพื่อให้การแยกทางไฟฟ้าระหว่างส่วนประกอบต่างๆ บนพื้นผิว. วัสดุเหล่านี้ยังมีเสถียรภาพทางความร้อนและความแข็งแรงเชิงกลที่ดี.
- ชั้นโลหะ: โลหะต่างๆ เช่น อะลูมิเนียม (อัล), ทองแดง (คิว), และทองคํา (Au) ใช้สําหรับชั้นการเชื่อมต่อโครงข่ายเพื่อกําหนดเส้นทางสัญญาณไฟฟ้าระหว่างอุปกรณ์เซมิคอนดักเตอร์และวงจรภายนอก. โลหะเหล่านี้ได้รับการคัดเลือกให้มีค่าการนําไฟฟ้าสูง, ความต้านทานต่ํา, และความเข้ากันได้กับกระบวนการผลิตขนาดเล็ก.
- ชั้นอิเล็กทริก: วัสดุอิเล็กทริก เช่น โพลีอิไมด์หรือเบนโซไซโคลบิวทีน (บีซีบี) อาจใช้เป็นชั้นฉนวนเพิ่มเติมหรือเป็นวัสดุพื้นผิวสําหรับโครงสร้างหลายชั้น. วัสดุเหล่านี้ให้ฉนวนไฟฟ้าและการสนับสนุนทางกลในขณะที่ช่วยให้สามารถรวมจุดแวะผ่านซิลิกอนได้ (TSV) และคุณสมบัติบรรจุภัณฑ์ขั้นสูงอื่น ๆ.
- เลเยอร์ทู่: วัสดุทู่ เช่น ซิลิกอนไนไตรด์ (Si3N4) หรือซิลิกอนออกไซด์ (ซิโอทู) ถูกนําไปใช้เพื่อปกป้องอุปกรณ์เซมิคอนดักเตอร์พื้นฐานจากปัจจัยแวดล้อม เช่น ความชื้น, สารปนเปื้อน, และความเสียหายทางกล.
- ชั้นกาว: วัสดุกาว เช่น อีพ็อกซี่หรือโพลีอิไมด์ใช้เพื่อยึดพื้นผิวกับส่วนประกอบอื่นๆ ของชุดบรรจุภัณฑ์, ให้เสถียรภาพทางกลและมั่นใจในการเชื่อมต่อทางไฟฟ้าที่เชื่อถือได้.
โดยการเลือกและบูรณาการวัสดุเหล่านี้อย่างระมัดระวัง, พื้นผิวแพ็คเกจ MIS สามารถออกแบบให้ตอบสนองความต้องการของอุปกรณ์เซมิคอนดักเตอร์สมัยใหม่, รวมถึงการทํางานความเร็วสูง, การจัดการความร้อน, และความน่าเชื่อถือ.
พื้นผิวแพ็คเกจ MIS ผลิตอย่างไร?
กระบวนการผลิต MIS (โลหะ-ฉนวน-เซมิคอนดักเตอร์) วัสดุพิมพ์บรรจุภัณฑ์มีหลายขั้นตอน, รวมถึงการเตรียมสารตั้งต้น, การสะสมวัสดุ, ลวดลาย, และการประกอบ. นี่คือภาพรวมทั่วไปของกระบวนการผลิต:
- การเตรียมพื้นผิว:
– กระบวนการผลิตโดยทั่วไปเริ่มต้นด้วยการเตรียมวัสดุพื้นผิว, เช่นเวเฟอร์ซิลิกอนหรือแผงกระจก. พื้นผิวได้รับการทําความสะอาดและบําบัดเพื่อให้พื้นผิวสะอาดและความสม่ําเสมอ.
- การสะสมวัสดุ:
– วัสดุต่างๆ จะถูกสะสมลงบนพื้นผิวในรูปแบบฟิล์มบางโดยใช้เทคนิคต่างๆ เช่น การสะสมไอทางกายภาพ (พีวีดี), การสะสมไอสารเคมี (CVD), หรือการสะสมชั้นอะตอม (ALD).
– ชั้นเซมิคอนดักเตอร์, ชั้นฉนวน, ชั้นโลหะ, และชั้นการทํางานอื่น ๆ จะถูกฝากลงบนพื้นผิวตามลําดับตามข้อกําหนดการออกแบบ.
- ลวดลาย:
– โฟโตลิโธกราฟีใช้เพื่อกําหนดรูปแบบบนชั้นที่ฝาก. วัสดุโฟโตรีซิสต์ถูกนําไปใช้กับพื้นผิว, สัมผัสกับแสงผ่านโฟโตมาสก์, และพัฒนาขึ้นเพื่อเลือกกําจัดบางส่วนของโฟโตรีซิสต์.
– พื้นที่ที่สัมผัสของชั้นด้านล่างจะถูกแกะสลักออกโดยใช้กระบวนการแกะสลักแบบเปียกหรือแห้ง, ทิ้งคุณสมบัติที่มีลวดลายที่ต้องการ เช่น การเชื่อมต่อระหว่างโลหะ, จุดร่วม, และชั้นฉนวน.
- การบูรณาการและการเชื่อมต่อโครงข่าย:
– หลังจากแพทเทิร์น, ชั้นเพิ่มเติมอาจถูกฝากและกําหนดรูปแบบตามความจําเป็นเพื่อสร้างโครงสร้างของพื้นผิว.
– ช่องผ่านซิลิกอน (TSV) อาจเกิดขึ้นเพื่อให้การเชื่อมต่อโครงข่ายในแนวตั้งระหว่างชั้นต่างๆ ของพื้นผิว.
– อุปกรณ์เซมิคอนดักเตอร์ (เศษ) โดยทั่วไปจะติดกับพื้นผิวโดยใช้เทคนิคการยึดติด เช่น การเชื่อมแบบพลิกชิปหรือการเชื่อมลวด. อาจใช้วัสดุกาวเพื่อยึดชิปให้เข้าที่.
- บรรจุภัณฑ์และการประกอบ:
– เมื่อวัสดุพิมพ์ถูกประดิษฐ์ขึ้นอย่างสมบูรณ์, มันถูกรวมเข้ากับชุดแพ็คเกจเซมิคอนดักเตอร์โดยรวม.
– ส่วนประกอบเพิ่มเติม เช่น ฮีตซิงก์, ฝา, และขั้วต่อภายนอกอาจติดเข้ากับแพ็คเกจได้ตามต้องการ.
– จากนั้นบรรจุภัณฑ์จะถูกปิดผนึกและห่อหุ้มด้วยวัสดุป้องกัน, เช่นอีพ็อกซี่หรือสารประกอบการขึ้นรูป, เพื่อให้ความแข็งแรงเชิงกลและการปกป้องสิ่งแวดล้อม.
- การทดสอบและการประกันคุณภาพ:
– บรรจุภัณฑ์สําเร็จรูปผ่านการทดสอบอย่างเข้มงวดเพื่อให้แน่ใจว่าเป็นไปตามระบบไฟฟ้าที่กําหนด, ร้อน, และข้อกําหนดทางกล.
– การทดสอบอาจรวมถึงการทดสอบความต่อเนื่องทางไฟฟ้า, การทดสอบความสมบูรณ์ของสัญญาณ, การปั่นจักรยานความร้อน, และการทดสอบความน่าเชื่อถือภายใต้สภาวะการทํางานต่างๆ.
โดยทําตามขั้นตอนการผลิตเหล่านี้, พื้นผิวแพ็คเกจ MIS สามารถผลิตได้ด้วยความแม่นยําและความน่าเชื่อถือสูงเพื่อตอบสนองความต้องการของอุปกรณ์เซมิคอนดักเตอร์ที่ทันสมัย.
พื้นที่การใช้งานของพื้นผิวแพ็คเกจ MIS
ม. (โลหะ-ฉนวน-เซมิคอนดักเตอร์) พื้นผิวบรรจุภัณฑ์พบการใช้งานในด้านต่างๆ ของอุตสาหกรรมเซมิคอนดักเตอร์, โดยเฉพาะอย่างยิ่งในการประกอบและบรรจุภัณฑ์ของวงจรรวม (ไอซี) และอุปกรณ์ไมโครอิเล็กทรอนิกส์. พื้นที่การใช้งานทั่วไปบางส่วน ได้แก่:
- ไมโครโปรเซสเซอร์และไมโครคอนโทรลเลอร์: พื้นผิวแพ็คเกจ MIS ใช้กันอย่างแพร่หลายในบรรจุภัณฑ์ของไมโครโปรเซสเซอร์และไมโครคอนโทรลเลอร์สําหรับอุปกรณ์คอมพิวเตอร์, รวมถึงคอมพิวเตอร์เดสก์ท็อป, แล็ป ท็อป, เซิร์ฟเวอร์, และระบบฝังตัว. พื้นผิวเหล่านี้ให้การเชื่อมต่อทางไฟฟ้า, การจัดการความร้อน, และการสนับสนุนทางกลสําหรับชิปเซมิคอนดักเตอร์.
- อุปกรณ์หน่วยความจํา: พื้นผิวแพ็คเกจ MIS ถูกนํามาใช้ในบรรจุภัณฑ์ของอุปกรณ์หน่วยความจํา เช่น หน่วยความจําการเข้าถึงแบบสุ่มแบบไดนามิก (DRAM), หน่วยความจําเข้าถึงแบบสุ่มแบบคงที่ (SRAM), และหน่วยความจําแฟลช. พื้นผิวเหล่านี้ช่วยให้สามารถถ่ายโอนข้อมูลความเร็วสูงได้, ฟอร์มแฟคเตอร์ขนาดกะทัดรัด, และการทํางานที่เชื่อถือได้ของโมดูลหน่วยความจําในอุปกรณ์อิเล็กทรอนิกส์ต่างๆ.
- หน่วยประมวลผลกราฟิก (จีพียู): ในกราฟิกการ์ดและแอพพลิเคชั่นคอมพิวเตอร์ประสิทธิภาพสูงอื่นๆ, พื้นผิวแพ็คเกจ MIS มีบทบาทสําคัญในการบรรจุ GPU และให้การจัดการความร้อนที่มีประสิทธิภาพสําหรับการจัดการพลังงานสูงที่เกี่ยวข้องกับการประมวลผลกราฟิก.
- ระบบบนชิป (โซซี) อุปกรณ์: พื้นผิวแพ็คเกจ MIS เป็นส่วนประกอบสําคัญในบรรจุภัณฑ์ของอุปกรณ์ SoC, ซึ่งรวมฟังก์ชันหลายอย่างไว้ในชิปเดียว. พื้นผิวเหล่านี้ช่วยให้สามารถรวมส่วนประกอบที่หลากหลาย เช่น โปรเซสเซอร์, ความจำ, วงจรอะนาล็อก, และโมดูลการสื่อสารไร้สายเป็นแพ็คเกจขนาดกะทัดรัดและประหยัดพลังงาน.
- อุปกรณ์เครือข่ายและการสื่อสาร: พื้นผิวแพ็คเกจ MIS ใช้ในอุปกรณ์เครือข่าย, เรา เตอร์, สวิตช์, และอุปกรณ์สื่อสารเพื่อบรรจุอินเทอร์เฟซความเร็วสูง, ตัวควบคุมอีเธอร์เน็ต, เครื่องรับส่งสัญญาณไร้สาย, และส่วนประกอบอื่นๆ ที่สําคัญสําหรับการส่งข้อมูลและการเชื่อมต่อ.
- อิเล็กทรอนิกส์ยานยนต์: ในอุตสาหกรรมยานยนต์, พื้นผิวบรรจุภัณฑ์ MIS ใช้ในบรรจุภัณฑ์ของชุดควบคุมอิเล็กทรอนิกส์ (ECU), เซน เซอร์, แอคชูเอเตอร์, และส่วนประกอบอื่นๆ ที่ใช้ในระบบยานพาหนะ เช่น การควบคุมเครื่องยนต์, ระบบความปลอดภัย, สาระบันเทิง, และระบบช่วยเหลือผู้ขับขี่.
- เครื่องใช้ไฟฟ้า: พื้นผิวบรรจุภัณฑ์ MIS พบได้ในผลิตภัณฑ์อิเล็กทรอนิกส์สําหรับผู้บริโภคหลากหลายประเภท, รวมถึงสมาร์ทโฟน, แท็บ เล็ต, สวมใส่ได้, กล้องดิจิตอล, เกมคอนโซล, และเครื่องใช้ในบ้าน, โดยที่พวกเขาจัดหาโซลูชันบรรจุภัณฑ์และการเชื่อมต่อโครงข่ายที่จําเป็นสําหรับอุปกรณ์เซมิคอนดักเตอร์.
- อิเล็กทรอนิกส์อุตสาหกรรมและการแพทย์: พื้นผิวบรรจุภัณฑ์ MIS ถูกนํามาใช้ในระบบอัตโนมัติทางอุตสาหกรรม, วิทยาการหุ่นยนต์, อุปกรณ์ทางการแพทย์, เครื่องมือวัด, และระบบควบคุม, ที่พวกเขาให้ความน่าเชื่อถือ, ความทนทาน, และประสิทธิภาพที่จําเป็นสําหรับสภาพแวดล้อมการทํางานที่รุนแรงและการใช้งานที่สําคัญ.
ทั้งหมด, พื้นผิวบรรจุภัณฑ์ MIS มีบทบาทสําคัญในการประกอบ, บรรจุ ภัณฑ์, และการรวมอุปกรณ์เซมิคอนดักเตอร์ในอุตสาหกรรมต่างๆ, ช่วยให้สามารถพัฒนาระบบอิเล็กทรอนิกส์ขั้นสูงพร้อมฟังก์ชันการทํางานที่ได้รับการปรับปรุง, การแสดง, และความน่าเชื่อถือ.
ข้อดีของพื้นผิวแพ็คเกจ MIS คืออะไร?
ม. (โลหะ-ฉนวน-เซมิคอนดักเตอร์) พื้นผิวบรรจุภัณฑ์มีข้อดีหลายประการในอุตสาหกรรมเซมิคอนดักเตอร์, ทําให้เป็นตัวเลือกที่ต้องการสําหรับบรรจุภัณฑ์วงจรรวมและอุปกรณ์ไมโครอิเล็กทรอนิกส์. ข้อได้เปรียบที่สําคัญบางประการ ได้แก่:
- ประสิทธิภาพทางไฟฟ้า: พื้นผิวแพ็คเกจ MIS ให้คุณสมบัติทางไฟฟ้าที่ดีเยี่ยม, รวมถึงความจุปรสิตต่ํา, การต่อต้าน, และการเหนี่ยวนํา, เปิดใช้งานการส่งสัญญาณความเร็วสูงและลดการเสื่อมสภาพของสัญญาณ. ส่งผลให้ประสิทธิภาพของอุปกรณ์และความสมบูรณ์ของสัญญาณดีขึ้น.
- การย่อขนาด: พื้นผิวแพ็คเกจ MIS รองรับการรวมอุปกรณ์เซมิคอนดักเตอร์หลายตัว, ส่วนประกอบแบบพาสซีฟ, และเชื่อมต่อกันเป็นแพ็คเกจขนาดกะทัดรัดและหนาแน่น. สิ่งนี้ทําให้ระบบอิเล็กทรอนิกส์มีขนาดเล็กลง, ลดความต้องการพื้นที่และช่วยให้สามารถพัฒนาอุปกรณ์ที่มีขนาดเล็กและเบากว่า.
- การจัดการความร้อน: พื้นผิวแพ็คเกจ MIS นําเสนอโซลูชันการจัดการความร้อนที่มีประสิทธิภาพ, รวมถึงการรวมจุดแวะระบายความร้อน, ฮีตซิงก์, และแผ่นระบายความร้อน, เพื่อกระจายความร้อนที่เกิดจากอุปกรณ์เซมิคอนดักเตอร์. สิ่งนี้ช่วยในการรักษาอุณหภูมิในการทํางานที่เหมาะสม, ยืดอายุการใช้งานของอุปกรณ์, และรับประกันประสิทธิภาพที่เชื่อถือได้ภายใต้สภาวะที่มีอุณหภูมิสูง.
- ความน่าเชื่อถือ: พื้นผิวแพ็คเกจ MIS ได้รับการออกแบบมาเพื่อตอบสนองความต้องการด้านความน่าเชื่อถือที่เข้มงวด, รวมถึงความทนทานทางกล, เสถียรภาพทางความร้อน, และความต้านทานต่อปัจจัยแวดล้อม เช่น ความชื้น, ความชื้น, และการปั่นจักรยานความร้อน. สิ่งนี้ทําให้มั่นใจได้ถึงความน่าเชื่อถือและความทนทานในระยะยาวของอุปกรณ์เซมิคอนดักเตอร์, แม้ในการใช้งานที่มีความต้องการสูง.
- การปรับแต่งและความยืดหยุ่น: พื้นผิวแพ็คเกจ MIS สามารถปรับแต่งให้ตรงตามข้อกําหนดการออกแบบเฉพาะ, รวมถึงวัสดุพื้นผิว, การกําหนดค่าเลเยอร์, รูปแบบการเชื่อมต่อโครงข่าย, และขนาดแพ็คเกจ. ความยืดหยุ่นนี้ช่วยให้สามารถพัฒนาโซลูชันที่ปรับให้เหมาะกับการใช้งานและตัวชี้วัดประสิทธิภาพที่หลากหลาย.
- ความคุ้มค่า: พื้นผิวบรรจุภัณฑ์ MIS นําเสนอโซลูชันบรรจุภัณฑ์ที่คุ้มค่าเมื่อเทียบกับเทคโนโลยีบรรจุภัณฑ์ทางเลือก เช่น บรรจุภัณฑ์เซรามิกหรือบรรจุภัณฑ์ขนาดชิป. การใช้กระบวนการผลิตเซมิคอนดักเตอร์มาตรฐานและวัสดุช่วยลดต้นทุนการผลิตในขณะที่ยังคงคุณภาพและประสิทธิภาพสูง.
- ความเข้ากันได้: พื้นผิวแพ็คเกจ MIS เข้ากันได้กับกระบวนการผลิตเซมิคอนดักเตอร์ที่หลากหลาย, รวมถึง CMOS (โลหะออกไซด์-เซมิคอนดักเตอร์เสริม), ไบซีเอ็มเอส (ไบโพลาร์ CMOS), และ MEMS (ระบบไมโครไฟฟ้าเครื่องกล), ช่วยให้สามารถผสานรวมกับเวิร์กโฟลว์และเทคโนโลยีการผลิตที่มีอยู่ได้อย่างราบรื่น.
- ความสามารถในการปรับขนาด: พื้นผิวแพ็คเกจ MIS รองรับการออกแบบที่ปรับขนาดได้ซึ่งสามารถรองรับความก้าวหน้าทางเทคโนโลยีในอนาคต, รวมถึงความหนาแน่นของอุปกรณ์ที่สูงขึ้น, เพิ่มฟังก์ชันการทํางาน, และปรับปรุงประสิทธิภาพ. ความสามารถในการปรับขนาดนี้ช่วยให้สามารถพัฒนาอุปกรณ์เซมิคอนดักเตอร์และระบบอิเล็กทรอนิกส์รุ่นต่อไปที่มีความสามารถที่เพิ่มขึ้น.
ทั้งหมด, ข้อดีของพื้นผิวแพ็คเกจ MIS ทําให้เป็นตัวเลือกที่น่าสนใจสําหรับอุปกรณ์เซมิคอนดักเตอร์บรรจุภัณฑ์, ให้ประสิทธิภาพทางไฟฟ้าที่ดีขึ้น, การย่อขนาด, การจัดการความร้อน, ความน่าเชื่อถือ, ความยืดหยุ่น, ความคุ้มค่า, ความเข้ากันได้, และความสามารถในการปรับขนาด.
วัสดุพิมพ์แพ็คเกจ MIS ราคาเท่าไหร่?
ค่าใช้จ่ายของ MIS (โลหะ-ฉนวน-เซมิคอนดักเตอร์) พื้นผิวบรรจุภัณฑ์อาจแตกต่างกันไปขึ้นอยู่กับปัจจัยหลายประการ, รวมถึงความซับซ้อนของการออกแบบพื้นผิว, การเลือกใช้วัสดุ, กระบวนการผลิตที่ใช้, และปริมาณการผลิต. ต่อไปนี้คือปัจจัยบางประการที่อาจส่งผลต่อต้นทุน:
- ความซับซ้อนของการออกแบบ: ความซับซ้อนของการออกแบบพื้นผิว, รวมถึงจํานวนชั้น, ความหนาแน่นของการเชื่อมต่อระหว่างกัน, การปรากฏตัวของช่องผ่านซิลิกอน (TSV), และการผสานรวมคุณสมบัติขั้นสูง เช่น โซลูชันการจัดการความร้อน, อาจส่งผลกระทบต่อต้นทุน. การออกแบบที่ซับซ้อนมากขึ้นอาจต้องใช้เทคนิคและวัสดุการผลิตเฉพาะทาง, ซึ่งสามารถเพิ่มต้นทุนการผลิตได้.
- การเลือกวัสดุ: การเลือกใช้วัสดุสําหรับชั้นพื้นผิว, รวมถึงวัสดุเซมิคอนดักเตอร์, วัสดุฉนวน, การเชื่อมต่อระหว่างโลหะ, และชั้นทู่, อาจส่งผลต่อต้นทุน. วัสดุบางชนิดอาจมีราคาแพงกว่าหรือต้องใช้เทคนิคการประมวลผลเฉพาะทาง, เพิ่มต้นทุนโดยรวมของวัสดุพิมพ์.
- กระบวนการผลิต: กระบวนการผลิตที่ใช้ในการประดิษฐ์พื้นผิว, รวมถึงการสะสม, ลวดลาย, แกะ สลัก, พันธะ, และขั้นตอนการบรรจุหีบห่อ, สามารถมีอิทธิพลต่อต้นทุน. เทคนิคการผลิตขั้นสูง เช่น โฟโตลิโธกราฟี, การสะสมไอสารเคมี (CVD), และการสะสมชั้นอะตอม (ALD) อาจก่อให้เกิดต้นทุนอุปกรณ์และการดําเนินงานที่สูงขึ้น.
- ปริมาณการผลิต: ปริมาณการผลิตมีบทบาทสําคัญในการกําหนดต้นทุนของพื้นผิวบรรจุภัณฑ์ MIS. ปริมาณที่สูงขึ้นมักนําไปสู่การประหยัดจากขนาด, เป็นต้นทุนคงที่ เช่น การติดตั้งอุปกรณ์, ขับ รถ, และค่าใช้จ่ายค่าโสหุ้ยจะกระจายไปตามหน่วยจํานวนมาก, ส่งผลให้ต้นทุนต่อหน่วยลดลง.
- ซัพพลายเออร์และที่ตั้ง: การเลือกซัพพลายเออร์และสถานที่ผลิตอาจส่งผลต่อต้นทุนของพื้นผิวบรรจุภัณฑ์ MIS. ซัพพลายเออร์ที่มีความสามารถในการผลิตขั้นสูงและต้นทุนแรงงานหรือค่าโสหุ้ยที่ต่ํากว่าอาจเสนอราคาที่แข่งขันได้มากขึ้น.
- บริการเพิ่มเติม: บริการเพิ่มเติม เช่น การสนับสนุนการออกแบบ, การทดสอบ, การประกันคุณภาพ, และการปรับแต่งอาจมีค่าใช้จ่ายเพิ่มเติม แต่สามารถเพิ่มมูลค่าให้กับแพ็คเกจโดยรวมได้.
สิ่งสําคัญคือต้องพิจารณาปัจจัยเหล่านี้และทํางานอย่างใกล้ชิดกับผู้ผลิตพื้นผิวเพื่อเพิ่มประสิทธิภาพกระบวนการออกแบบและการผลิตเพื่อให้ได้ความสมดุลระหว่างต้นทุนที่ต้องการ, การแสดง, และความน่าเชื่อถือสําหรับการใช้งานเซมิคอนดักเตอร์เฉพาะ.
คําถามที่พบบ่อยเกี่ยวกับ MIS Package Substrate
พื้นผิวแพ็คเกจ MIS คืออะไร?
พื้นผิวแพ็คเกจ MIS เป็นส่วนประกอบพื้นฐานที่ใช้ในบรรจุภัณฑ์เซมิคอนดักเตอร์เพื่อติดตั้งและเชื่อมต่อชิปเซมิคอนดักเตอร์ภายในแพ็คเกจ. โดยทั่วไปจะประกอบด้วยโลหะ, ฉนวน, และชั้นเซมิคอนดักเตอร์.
ข้อดีของการใช้พื้นผิวแพ็คเกจ MIS คืออะไร?
พื้นผิวแพ็คเกจ MIS มีข้อดี เช่น ประสิทธิภาพทางไฟฟ้าที่ยอดเยี่ยม, การย่อขนาด, การจัดการความร้อนที่มีประสิทธิภาพ, ความน่าเชื่อถือ, ความยืดหยุ่นในการปรับแต่ง, ความคุ้มค่า, ความเข้ากันได้, และความสามารถในการปรับขนาด.
วัสดุใดที่ใช้ในพื้นผิวแพ็คเกจ MIS?
วัสดุที่ใช้กันทั่วไปในพื้นผิวแพ็คเกจ MIS ได้แก่ ซิลิกอนสําหรับชั้นเซมิคอนดักเตอร์, วัสดุฉนวน เช่น ซิลิคอนไดออกไซด์หรือซิลิกอนไนไตรด์, โลหะต่างๆสําหรับชั้นเชื่อมต่อ, วัสดุอิเล็กทริก, วัสดุทู่, และวัสดุกาว.
พื้นผิวบรรจุภัณฑ์ MIS ผลิตอย่างไร?
กระบวนการผลิตมักเกี่ยวข้องกับการเตรียมพื้นผิว, การสะสมวัสดุ, ลวดลาย, บูรณาการ, สภา, การทดสอบ, และการประกันคุณภาพ. เทคนิคการประดิษฐ์ต่างๆ เช่น การสะสม, โฟโตลิโธกราฟี, แกะ สลัก, และการยึดติดใช้เพื่อสร้างโครงสร้างพื้นผิว.
การใช้งานของพื้นผิวแพ็คเกจ MIS คืออะไร?
พื้นผิวแพ็คเกจ MIS พบการใช้งานในไมโครโปรเซสเซอร์, อุปกรณ์หน่วยความจํา, หน่วยประมวลผลกราฟิก (จีพียู), ระบบบนชิป (โซซี) อุปกรณ์, อุปกรณ์เครือข่ายและการสื่อสาร, อุปกรณ์อิเล็กทรอนิกส์ยานยนต์, เครื่องใช้ไฟฟ้า, อิเล็กทรอนิกส์อุตสาหกรรมและการแพทย์, และอื่น ๆ.
ปัจจัยใดบ้างที่มีอิทธิพลต่อต้นทุนของพื้นผิวบรรจุภัณฑ์ MIS?
ต้นทุนของพื้นผิวแพ็คเกจ MIS ขึ้นอยู่กับปัจจัยต่างๆ เช่น ความซับซ้อนในการออกแบบ, การเลือกวัสดุ, กระบวนการผลิต, ปริมาณการผลิต, ผู้ให้, สถานที่, และบริการเพิ่มเติม.
ฉันจะเพิ่มประสิทธิภาพการออกแบบและการผลิตพื้นผิวแพ็คเกจ MIS สําหรับการใช้งานเฉพาะของฉันได้อย่างไร?
การเพิ่มประสิทธิภาพการออกแบบและการผลิตพื้นผิวบรรจุภัณฑ์ MIS เกี่ยวข้องกับการพิจารณาปัจจัยต่างๆ เช่น ประสิทธิภาพทางไฟฟ้า, การจัดการความร้อน, ความน่าเชื่อถือ, ความต้องการในการปรับแต่ง, ข้อจํากัดด้านต้นทุน, และข้อกําหนดด้านความสามารถในการปรับขนาด. การทํางานอย่างใกล้ชิดกับผู้ผลิตพื้นผิวและใช้ประโยชน์จากความเชี่ยวชาญของพวกเขาสามารถช่วยให้บรรลุความสมดุลที่ต้องการระหว่างปัจจัยเหล่านี้.