What is FCCSP Package Substrate?
ผู้ผลิตพื้นผิวแพ็คเกจ FCCSP,FCCSP (Flip Chip Chip Scale Package) package substrate is a high-performance platform used in semiconductor packaging to enhance device efficiency and miniaturization. This substrate supports flip chip technology, where the semiconductor die is mounted upside down, allowing for direct electrical connections through solder bumps. FCCSP substrates provide excellent thermal management, ประสิทธิภาพทางไฟฟ้า, and mechanical stability. They are typically constructed from materials like BT resin or advanced laminates, ensuring reliability and durability. Widely used in applications such as mobile devices, high-speed processors, and telecommunications, FCCSP package substrates enable compact, high-density, and high-performance electronic solutions by reducing interconnect length and enhancing signal integrity.
The substrate used in FCCSP is typically a thin and flat material onto which the chip is mounted. This substrate provides electrical connections between the chip and the external circuitry, as well as mechanical support for the chip.
The term “Package Substrate” in the context of FCCSP likely refers to the substrate component of the overall packaging technology. It plays a crucial role in facilitating the electrical and mechanical connection between the chip and the rest of the electronic system. The substrate may be made of materials such as organic laminate, ceramics, or other advanced materials depending on the specific requirements of the application.
FCCSP Package Substrate design Reference Guide.
The FCCSP Package Substrate Design Reference Guide is an extensive resource providing guidance and best practices for designing substrates used in Flip Chip Chip Scale Package (FCCSP) เทคโนโลยี. It offers comprehensive insights into various aspects of substrate design, including layout considerations, electrical performance optimization, การเลือกวัสดุ, การจัดการความร้อน, and manufacturing processes.
This guide expands to 300 words by delving into the key components:
- Layout Considerations: It covers the arrangement of electrical connections, signal routing, การกระจายพลังงาน, and ground planes on the substrate to ensure optimal signal integrity, minimal crosstalk, and efficient power delivery.
- Electrical Performance Optimization: Discusses techniques for minimizing signal loss, การจับคู่อิมพีแดนซ์, and controlling parasitic effects to enhance the electrical performance of the substrate, ensuring reliable operation of the integrated circuit.
- การเลือกวัสดุ: Provides guidance on selecting suitable substrate materials based on factors such as electrical properties, การนําความร้อน, ความแข็งแรงเชิงกล, and cost-effectiveness, considering the specific requirements of the application.
- การจัดการความร้อน: Addresses strategies for managing heat dissipation within the FCCSP package, including the design of thermal vias, heat spreaders, and thermal interface materials to prevent overheating and ensure the long-term reliability of the device.
- Manufacturing Processes: Offers insights into the fabrication techniques and processes involved in producing FCCSP substrates, such as photolithography, แกะ สลัก, plating, และการประกอบ, highlighting considerations for achieving high yield and quality control.
- ข้อควรพิจารณาด้านความน่าเชื่อถือ: Covers aspects related to substrate reliability, รวมถึงความทนทานทางกล, การปั่นจักรยานความร้อน, solder joint reliability, และการทดสอบด้านสิ่งแวดล้อม, to ensure the durability and longevity of the packaged device.
- Case Studies and Examples: Illustrates real-world examples and case studies of successful FCCSP substrate designs, showcasing best practices and lessons learned from practical implementations.
By following the guidelines outlined in the FCCSP Package Substrate Design Reference Guide, engineers and designers can effectively develop high-performance and reliable substrates for FCCSP technology, ตอบสนองความต้องการที่เข้มงวดของการใช้งานอิเล็กทรอนิกส์สมัยใหม่.
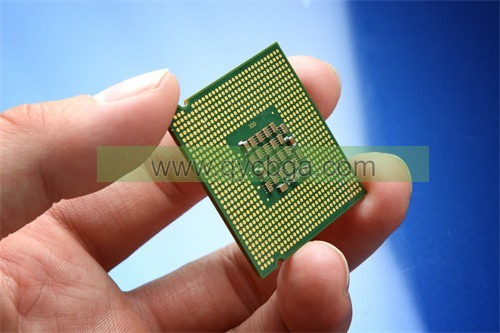
ผู้ผลิตพื้นผิวแพ็คเกจ FCCSP
What are the materials used in FCCSP Package Substrate?
Materials used in FCCSP (Flip Chip Chip Scale Package) package substrates can vary depending on specific requirements, but some common materials include:
- Organic Substrates: Organic substrates, often in the form of laminate materials, are commonly used due to their low cost, lightweight nature, and ease of fabrication. These substrates typically consist of layers of epoxy resin reinforced with glass fibers (FR-4) or other materials.
- พื้นผิวเซรามิก: Ceramic substrates offer excellent thermal conductivity and mechanical properties, making them suitable for applications requiring high reliability and performance. Common ceramic materials used include alumina (อัล 2 โอ 3) and aluminum nitride (อัลเอ็น).
- Metal Core Substrates: Metal core substrates, such as aluminum or copper, are used when enhanced thermal conductivity is required to efficiently dissipate heat generated by the integrated circuit.
- Flex Substrates: Flexible substrates made of polyimide or similar materials are used in applications where bending or flexibility is required, such as in wearable devices or flexible electronics.
- Advanced Substrate Materials: In some cases, advanced substrate materials like liquid crystal polymer (แอลซีพี) may be used to meet specific performance requirements, such as high-frequency applications where low dielectric constant and loss are crucial.
- Adhesive Materials: Adhesive materials are used to bond the semiconductor chip to the substrate and provide mechanical stability. These adhesives are often epoxy-based and selected to provide strong adhesion while accommodating differences in coefficients of thermal expansion between the chip and substrate.
The choice of substrate material depends on various factors, including electrical performance requirements, ความต้องการการจัดการความร้อน, cost considerations, and specific application constraints. Each material offers different advantages and trade-offs, and selecting the most suitable substrate is essential for ensuring the performance, ความน่าเชื่อถือ, and manufacturability of the FCCSP package.
How is FCCSP Package Substrate manufactured?
The manufacturing process for FCCSP (Flip Chip Chip Scale Package) substrates typically involves several steps to create a substrate that provides electrical connections, mechanical support, and thermal management for the integrated circuit (IC) chip. นี่คือภาพรวมของกระบวนการผลิต:
- Substrate Fabrication: The process begins with the fabrication of the substrate material. Depending on the chosen material (such as organic laminate, ceramic, metal core, or flexible substrate), this may involve processes like layering, curing, and cutting to size.
- Surface Preparation: Once the substrate material is prepared, its surface is cleaned and prepared for subsequent processing steps. This typically involves removing any contaminants or residues that could affect the adhesion of subsequent layers.
- Metallization: Metallization is performed to create the conductive traces and pads on the substrate surface. This is often done using techniques like physical vapor deposition (พีวีดี) or chemical vapor deposition (CVD) to deposit thin layers of metal (such as copper) onto the substrate surface.
- Lithography and Etching: Photolithography is used to define the patterns of the conductive traces and pads on the substrate surface. A photoresist material is applied to the substrate, exposed to UV light through a mask with the desired pattern, and then developed to remove the unexposed areas. Etching is then performed to selectively remove the metal in the exposed areas, leaving behind the desired conductor patterns.
- Die Attach: The IC chip is attached to the substrate using a die attach adhesive. This adhesive provides mechanical support and electrical connection between the chip and the substrate.
- Wire Bonding (Optional): In some cases, wire bonding may be performed to make electrical connections between the IC chip and the substrate. อย่างไรก็ตาม, in FCCSP technology, flip chip bonding (directly connecting the chip to the substrate) is more common.
- Encapsulation (Optional): If additional protection is required, the assembled substrate and chip may be encapsulated with a protective material (เช่นอีพ็อกซี่หรือสารประกอบการขึ้นรูป) to safeguard the components from environmental factors and mechanical stress.
- การทดสอบและการตรวจสอบ: The completed FCCSP substrates undergo testing and inspection to ensure they meet the required electrical, เครื่องกล, and thermal performance specifications.
- บรรจุภัณฑ์และการจัดส่ง: Once the substrates pass inspection, they are packaged and shipped to semiconductor manufacturers for integration into electronic devices.
ทั้งหมด, the manufacturing process for FCCSP substrates involves a combination of materials processing, ลวดลาย, สภา, and testing steps to create high-performance substrates suitable for use in advanced electronic devices.
The Application area of FCCSP Package Substrate
FCCSP (Flip Chip Chip Scale Package) substrates find application in various electronic devices and systems across multiple industries due to their compact size, high performance, และความน่าเชื่อถือ. Some common application areas of FCCSP package substrates include:
- เครื่องใช้ไฟฟ้า: FCCSP substrates are extensively used in consumer electronics such as smartphones, แท็บ เล็ต, แล็ป ท็อป, กล้องดิจิตอล, and wearable devices. Their compact size and high electrical performance make them ideal for applications where space is limited and performance is crucial.
- Telecommunications: In telecommunications equipment such as routers, สวิตช์, base stations, and optical networking devices, FCCSP substrates play a vital role in providing high-speed data processing, signal routing, and connectivity.
- อิเล็กทรอนิกส์ยานยนต์: FCCSP substrates are used in automotive electronics for applications such as engine control units (ECU), infotainment systems, advanced driver assistance systems (ADAS), and in-vehicle networking. They offer high reliability and withstand harsh operating conditions.
- Industrial Equipment: In industrial automation, control systems, วิทยาการหุ่นยนต์, and instrumentation, FCCSP substrates contribute to the efficient operation, monitoring, and control of various processes and machinery.
- Medical Devices: FCCSP substrates are employed in medical devices like diagnostic equipment, patient monitoring systems, imaging devices, and implantable devices. Their high reliability and compact size are crucial for medical applications.
- Aerospace and Defense: In aerospace and defense applications, FCCSP substrates are utilized in avionics, ระบบเรดาร์, communication equipment, guidance systems, and electronic warfare systems, where reliability, ruggedness, and performance are paramount.
- IoT (Internet of Things): As IoT devices continue to proliferate, FCCSP substrates are used in smart sensors, connected devices, and IoT gateways to enable efficient data processing, connectivity, and communication in various IoT applications.
- Networking and Data Centers: In networking equipment, data centers, and server applications, FCCSP substrates contribute to high-speed data processing, packet switching, and network connectivity, supporting the increasing demand for bandwidth and performance.
ทั้งหมด, FCCSP package substrates are versatile and widely applicable across a range of industries and electronic devices, contributing to advancements in technology, connectivity, and functionality.
What are the advantages of FCCSP Package Substrate?
FCCSP (Flip Chip Chip Scale Package) substrates offer several advantages over traditional packaging technologies, making them popular choices for integrated circuit (IC) packaging in various applications. Some of the key advantages of FCCSP package substrates include:
- Compact Size: FCCSP substrates have a small form factor, allowing for higher component density and more compact electronic devices. This makes them particularly suitable for applications where space is limited, such as mobile devices and wearables.
- High Electrical Performance: The flip chip bonding technique used in FCCSP enables short interconnection lengths between the IC chip and the substrate, reducing parasitic capacitance and inductance. This results in improved electrical performance, including faster signal propagation, lower power consumption, and better signal integrity.
- Enhanced Thermal Management: FCCSP substrates can incorporate features such as thermal vias, heat spreaders, and advanced thermal interface materials to efficiently dissipate heat generated by the IC chip. This helps in maintaining optimal operating temperatures and prolonging the lifespan of the electronic device.
- Improved Reliability: The direct bonding of the IC chip to the substrate in FCCSP reduces the number of interconnects and solder joints compared to traditional packaging methods, leading to enhanced reliability and reduced susceptibility to mechanical and thermal stresses.
- Cost Efficiency: Despite their advanced features, FCCSP substrates can be manufactured using cost-effective materials and processes. The simplified assembly process and reduced material usage contribute to overall cost savings compared to other packaging technologies.
- Higher Performance: FCCSP substrates support high-frequency operation and high-speed data transmission, making them well-suited for applications requiring high-performance computing, networking, and data processing.
- Design Flexibility: FCCSP substrates offer flexibility in design, allowing for customization of electrical and thermal characteristics to meet specific application requirements. This enables engineers to optimize the performance and functionality of electronic devices.
- Compatibility with Advanced Technologies: FCCSP substrates are compatible with advanced semiconductor technologies, including flip chip bonding, ระบบบนชิป (โซซี) บูรณาการ, and heterogeneous integration, enabling the development of cutting-edge electronic products.
ทั้งหมด, FCCSP package substrates offer a compelling combination of compact size, high performance, ความน่าเชื่อถือ, and cost efficiency, making them preferred choices for a wide range of electronic applications.
How Much Does FCCSP Package Substrate Cost?
The cost of FCCSP (Flip Chip Chip Scale Package) substrates can vary significantly depending on several factors, including substrate material, size, complexity, manufacturing volume, and supplier/vendor pricing. โดยทั่วไป, FCCSP substrates are considered to be cost-effective compared to some other advanced packaging technologies due to their simplified assembly process and relatively low material usage.
อย่างไรก็ตาม, it’s challenging to provide a specific cost estimate without knowing the exact specifications and requirements of the FCCSP substrate in question. Factors that can influence the cost include:
- Substrate Material: Different substrate materials have different costs. Organic laminate substrates are typically less expensive compared to ceramic or metal core substrates.
- Size and Complexity: Larger and more complex substrates with densely packed components may incur higher manufacturing costs due to increased material usage and more intricate manufacturing processes.
- Manufacturing Volume: Higher manufacturing volumes often lead to economies of scale, resulting in lower unit costs per substrate. Conversely, low-volume production may incur higher per-unit costs.
- Supplier/Vendor Pricing: The pricing policies of substrate manufacturers and suppliers can vary, impacting the overall cost of FCCSP substrates.
- Additional Features: If additional features such as advanced thermal management solutions or special surface finishes are required, they may add to the overall cost of the substrate.
To obtain an accurate cost estimate for FCCSP package substrates, it’s advisable to consult with substrate manufacturers or suppliers and provide detailed specifications of the desired substrate, including material type, dimensions, features, and required quantity. They can then provide quotes based on the specific requirements of the project.
คําถามที่พบบ่อย
What is FCCSP Package Substrate?
FCCSP is a packaging technology where the semiconductor chip is flipped upside down and directly attached to the substrate or printed circuit board (PCB). The substrate provides electrical connections and mechanical support for the chip.
What are the advantages of FCCSP Package Substrate?
Advantages include compact size, high electrical performance, enhanced thermal management, improved reliability, cost efficiency, higher performance, and design flexibility.
What materials are used in FCCSP Package Substrate?
Common materials include organic substrates (such as laminate), พื้นผิวเซรามิก, metal core substrates, flex substrates, and advanced materials like liquid crystal polymer (แอลซีพี).
How is FCCSP Package Substrate manufactured?
The manufacturing process typically involves substrate fabrication, surface preparation, metallization, lithography and etching, die attach, wire bonding (optional), encapsulation (optional), การทดสอบและการตรวจสอบ, และบรรจุภัณฑ์และการจัดส่ง.
What are the applications of FCCSP Package Substrate?
Applications include consumer electronics, telecommunications, อุปกรณ์อิเล็กทรอนิกส์ยานยนต์, industrial equipment, อุปกรณ์ทางการแพทย์, aerospace and defense, IoT (Internet of Things), and networking and data centers.
How much does FCCSP Package Substrate cost?
Costs vary depending on substrate material, size, complexity, manufacturing volume, and supplier/vendor pricing. It’s best to consult with substrate manufacturers or suppliers for accurate cost estimates based on specific requirements.
What are the key considerations in designing FCCSP Package Substrate?
Key considerations include layout design, electrical performance optimization, การเลือกวัสดุ, การจัดการความร้อน, กระบวนการผลิต, ความน่าเชื่อถือ, and adherence to application requirements.
What are the differences between FCCSP and other packaging technologies?
FCCSP offers advantages such as smaller size, higher performance, and better thermal management compared to traditional packaging methods like wire bonding and lead frame packaging.