What is Ceramic Package Substrate?
ผู้ผลิตพื้นผิวแพ็คเกจเซรามิก,Ceramic package substrate is a robust and high-performance material used in advanced electronic packaging. It is renowned for its excellent thermal conductivity, high electrical insulation, and superior mechanical strength. These substrates can withstand extreme temperatures and harsh environments, making them ideal for aerospace, military, and high-power applications. นอกจากนี้, ceramic substrates offer minimal signal loss and are highly resistant to corrosion and wear. Their stable dielectric properties ensure reliable performance in high-frequency applications. This makes ceramic package substrates a preferred choice for integrating and protecting semiconductor devices in demanding conditions, ensuring longevity and efficiency in various electronic systems.
Here are some key characteristics and features of ceramic package substrates:
- วัตถุ: Ceramic substrates are typically made from materials such as alumina (อัล 2 โอ 3) or aluminum nitride (อัลเอ็น). These materials offer excellent thermal conductivity, electrical insulation, and mechanical stability, making them suitable for high-performance applications.
- การจัดการความร้อน: One of the primary advantages of ceramic package substrates is their superior thermal conductivity compared to organic substrates (such as those made from fiberglass-reinforced epoxy resins). This allows for efficient heat dissipation from the integrated circuit, which is crucial for maintaining device reliability and performance.
- ประสิทธิภาพทางไฟฟ้า: Ceramic substrates provide good electrical insulation, which helps prevent short circuits and interference between adjacent conductive traces. They also offer high dielectric strength, enabling reliable operation at high voltages.
- การย่อขนาด: Ceramic substrates can be manufactured with fine features and tight tolerances, allowing for the miniaturization of electronic devices. This is particularly important in modern electronics, where space-saving and compact designs are often required.
- ความเข้ากันได้: Ceramic package substrates are compatible with various chip attachment methods, including wire bonding, flip-chip bonding, and soldering. They can also accommodate different types of IC packages, such as surface-mount packages (เช่น, quad flat packages) and through-hole packages.
- ความน่าเชื่อถือ: Due to their robust mechanical properties and high-temperature tolerance, ceramic package substrates offer excellent reliability and durability in harsh operating environments.
ทั้งหมด, ceramic package substrates play a critical role in semiconductor packaging by providing a stable and high-performance platform for mounting integrated circuits while ensuring efficient thermal management and reliable electrical connections.
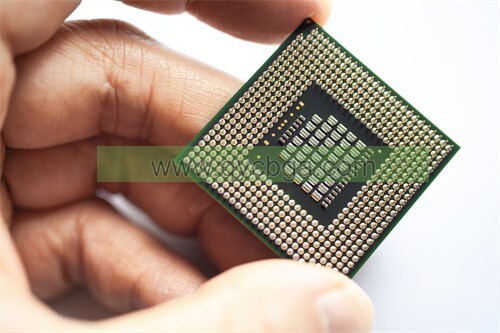
ผู้ผลิตพื้นผิวแพ็คเกจเซรามิก
Ceramic Package Substrate design Reference Guide.
While I can’t provide a specific reference guide due to the limitations of my training data, I can offer some general guidelines and resources that can help you in designing ceramic package substrates:
- Manufacturer’s Documentation: Many semiconductor packaging material suppliers offer design guides, application notes, and technical datasheets that provide detailed information on ceramic package substrate design considerations. These documents often include guidelines for material selection, substrate layout, routing techniques, การจัดการความร้อน, and reliability assessment.
- Industry Standards: Standards organizations such as the International Electrotechnical Commission (IEC), Joint Electron Device Engineering Council (JEDEC), and Institute of Electrical and Electronics Engineers (IEEE) publish standards and guidelines related to semiconductor packaging and substrate design. These standards can serve as valuable references for ensuring compliance with industry best practices.
- Books and Publications: There are several books and academic publications available that cover topics related to semiconductor packaging and substrate design. These resources can provide in-depth insights into fundamental principles, advanced techniques, and emerging trends in the field.
- Online Forums and Communities: Participating in online forums and communities focused on semiconductor packaging and electronics design can be a great way to seek advice, share experiences, and learn from industry professionals and fellow enthusiasts. Websites like Stack Exchange’s Electrical Engineering community and forums hosted by professional organizations often feature discussions on substrate design topics.
- Professional Training and Courses: Many universities, technical institutes, and professional organizations offer courses, workshops, and training programs on semiconductor packaging and substrate design. These educational opportunities can provide structured learning experiences and hands-on training in designing ceramic package substrates.
- Simulation and Modeling Tools: Utilizing simulation and modeling software tools can be invaluable in the design process, allowing you to analyze thermal performance, electrical characteristics, signal integrity, and mechanical reliability of ceramic package substrates. Tools like ANSYS, COMSOL Multiphysics, and Cadence Allegro PCB Designer offer capabilities for substrate modeling and analysis.
By leveraging these resources and approaches, you can gain the knowledge and expertise needed to design ceramic package substrates effectively, meeting the requirements of your specific application and ensuring optimal performance and reliability.
What are the materials used in Ceramic Package Substrate?
Ceramic package substrates are typically made from high-performance ceramic materials chosen for their excellent thermal, electrical, และคุณสมบัติทางกล. The most common materials used in ceramic package substrates include:
- Alumina (อัล 2 โอ 3): Alumina is a widely used ceramic material in semiconductor packaging due to its high thermal conductivity, good electrical insulation properties, และความแข็งแรงเชิงกล. It is particularly suitable for applications requiring efficient heat dissipation and high reliability.
- Aluminum Nitride (อัลเอ็น): Aluminum nitride offers even higher thermal conductivity than alumina, making it an excellent choice for applications where superior thermal management is critical. It also exhibits good electrical insulation and thermal expansion properties, contributing to its suitability for high-power and high-frequency electronic devices.
- Beryllium Oxide (BeO): Beryllium oxide is known for its exceptional thermal conductivity, which surpasses that of alumina and aluminum nitride. อย่างไรก็ตาม, its use is limited due to safety concerns associated with beryllium exposure, as beryllium compounds can be toxic if mishandled.
- Silicon Nitride (Si3N4): Silicon nitride offers a unique combination of properties, including high thermal conductivity, excellent mechanical strength, and good chemical resistance. It is often used in demanding applications where resistance to thermal shock and mechanical stress is crucial.
- Glass-Ceramics: Glass-ceramic materials are composed of crystalline and glassy phases, offering a balance of thermal, electrical, และคุณสมบัติทางกล. They can be tailored to specific application requirements through precise control of composition and processing parameters.
These ceramic materials can be fabricated into package substrates using various manufacturing techniques, including green tape (or thick-film) เทคโนโลยี, co-firing processes, and direct ceramic machining (DCM). Each material has its advantages and limitations, and the choice depends on factors such as the specific application requirements, operating conditions, and cost considerations. นอกจากนี้, hybrid substrates combining different ceramic materials or incorporating metal layers may be used to achieve specific performance targets.
How is Ceramic Package Substrate manufactured?
Manufacturing ceramic package substrates involves several steps, including material preparation, shaping, firing, metallization, and testing. นี่คือภาพรวมทั่วไปของกระบวนการผลิต:
- Material Selection and Preparation:
– High-quality ceramic materials such as alumina (อัล 2 โอ 3), aluminum nitride (อัลเอ็น), or silicon nitride (Si3N4) are selected based on the desired properties for the specific application.
– The raw ceramic powders are carefully formulated to achieve the desired composition and properties, including thermal conductivity, ค่าคงที่ไดอิเล็กทริก, และความแข็งแรงเชิงกล.
- Shaping:
– The ceramic powders are mixed with binders and additives to form a slurry or paste with suitable rheological properties for shaping.
– Shaping techniques such as tape casting, extrusion, or injection molding are used to form the green ceramic substrates into the desired shape and dimensions.
– For complex substrate designs, multiple layers of ceramic tape may be stacked and laminated to create multilayer structures.
- Drying:
– The green ceramic substrates are dried to remove excess moisture and organic binders, typically through air drying or controlled heating in ovens.
- Firing (Sintering):
– The dried green substrates are fired in a high-temperature kiln in a process called sintering.
– During sintering, the ceramic particles bond together and densify, resulting in a strong, dense ceramic structure with the desired mechanical and thermal properties.
– The firing process may involve multiple stages with controlled heating and cooling rates to prevent cracking and ensure uniform densification.
- Metallization:
– After sintering, metal conductive traces and pads are applied to the ceramic substrate surface through techniques such as screen printing, thin-film deposition, or plating.
– The metallization process typically involves depositing metals such as gold, silver, or copper to provide electrical connectivity between the integrated circuits (ไอซี) and external components.
- Die Attachment and Wire Bonding (Optional):
– In some cases, integrated circuits (ไอซี) are attached to the ceramic substrate using die attach materials such as epoxy adhesives or solder pastes.
– Wire bonding or flip-chip bonding techniques are then used to establish electrical connections between the ICs and the metallized traces on the substrate.
- Additional Processing (Optional):
– Depending on the specific application requirements, additional processing steps such as laser machining, coating, or encapsulation may be performed to enhance substrate performance and reliability.
- Testing and Quality Control:
– The finished ceramic package substrates undergo rigorous testing to ensure they meet specified electrical, เครื่องกล, and thermal performance criteria.
– Quality control measures are implemented throughout the manufacturing process to identify and rectify any defects or deviations from the desired specifications.
โดยทําตามขั้นตอนเหล่านี้, manufacturers can produce ceramic package substrates with precise dimensions, excellent mechanical integrity, and tailored electrical properties to meet the demanding requirements of modern semiconductor packaging applications.
The Application area of Ceramic Package Substrate
Ceramic package substrates find applications across various industries and technologies where high-performance, ความน่าเชื่อถือ, and thermal management are essential. Some of the key application areas include:
- Semiconductor Packaging: Ceramic package substrates are extensively used in the packaging of integrated circuits (ไอซี), microprocessors, อุปกรณ์หน่วยความจํา, and other semiconductor components. They provide a stable platform for mounting and interconnecting chips while offering superior thermal conductivity for efficient heat dissipation.
- High-Frequency and RF Devices: Ceramic substrates are well-suited for high-frequency and radio frequency (อาร์เอฟ) applications due to their low dielectric losses and excellent electrical properties. They are commonly used in RF amplifiers, filters, antennas, and other wireless communication devices.
- Power Electronics: Ceramic package substrates are employed in power electronic modules and devices where high-power densities and reliable thermal management are critical. They are used in applications such as power converters, inverters, motor drives, and energy storage systems.
- LED Packaging: Ceramic substrates are preferred for packaging light-emitting diodes (LEDs) due to their excellent thermal conductivity and stability at high temperatures. They help dissipate heat generated by the LEDs, prolonging their lifespan and ensuring consistent performance in lighting applications.
- อิเล็กทรอนิกส์ยานยนต์: Ceramic package substrates are increasingly used in automotive electronics for applications such as engine control units (ECU), power modules, เซน เซอร์, and LED lighting systems. They offer robustness, ความน่าเชื่อถือ, and thermal stability required for automotive environments.
- Aerospace and Defense: Ceramic package substrates are utilized in aerospace and defense systems for their ability to withstand harsh environmental conditions, including extreme temperatures, vibrations, and mechanical shock. They are used in radar systems, avionics, communication equipment, and missile guidance systems.
- Medical Devices: Ceramic substrates are employed in medical devices and equipment where reliability, biocompatibility, and sterilization resistance are essential. They are used in applications such as implantable devices, medical sensors, diagnostic equipment, and surgical instruments.
- เครื่องใช้ไฟฟ้า: Ceramic package substrates are found in various consumer electronic devices, รวมถึงสมาร์ทโฟน, แท็บ เล็ต, แล็ป ท็อป, and wearables. They are used in microelectronics packaging to ensure compact designs, efficient thermal management, and reliable performance.
ทั้งหมด, ceramic package substrates play a critical role in enabling advanced electronic systems across a wide range of industries, offering benefits such as high thermal conductivity, excellent electrical properties, เสถียรภาพทางกล, and reliability in demanding operating environments.
What are the advantages of Ceramic Package Substrate?
Ceramic package substrates offer several advantages over other packaging materials, making them widely used in various electronic applications. ข้อได้เปรียบที่สําคัญบางประการ ได้แก่:
- High Thermal Conductivity: Ceramic materials such as alumina (อัล 2 โอ 3) and aluminum nitride (อัลเอ็น) have excellent thermal conductivity, allowing for efficient dissipation of heat generated by integrated circuits (ไอซี). This helps prevent overheating and ensures the reliability and longevity of electronic devices.
- Excellent Electrical Insulation: Ceramic substrates provide excellent electrical insulation properties, preventing short circuits and signal interference between adjacent conductive traces. This is particularly important in high-frequency and high-power applications where electrical isolation is critical.
- Mechanical Stability and Strength: Ceramic materials exhibit high mechanical strength and stability, making them resistant to mechanical stress, vibration, และการปั่นจักรยานความร้อน. This ensures the integrity of the package substrate and helps protect the enclosed electronic components.
- Miniaturization and High Density Integration: Ceramic package substrates can be manufactured with fine features and tight tolerances, allowing for the miniaturization of electronic devices and high-density integration of components. This is essential for achieving compact designs and optimizing space utilization in modern electronic systems.
- Compatibility with High Temperatures: Ceramic materials can withstand high operating temperatures without degradation, making them suitable for applications in harsh environments, including automotive, อวกาศ, and industrial settings. They offer stability and reliability over a wide temperature range.
- Chemical and Environmental Resistance: Ceramic package substrates exhibit resistance to chemical corrosion, moisture, and environmental contaminants, ensuring long-term reliability in diverse operating conditions. This makes them suitable for use in challenging environments where exposure to harsh chemicals or outdoor conditions may occur.
- Customization and Tailored Properties: Ceramic substrates can be tailored to specific application requirements by adjusting composition, processing parameters, and material properties. This flexibility allows for customization of thermal conductivity, ค่าคงที่ไดอิเล็กทริก, and mechanical characteristics to meet the needs of different electronic devices and systems.
- Compatibility with Various Packaging Technologies: Ceramic package substrates are compatible with a wide range of packaging technologies, including wire bonding, flip-chip bonding, and surface-mount technology (SMT). This versatility enables seamless integration into different manufacturing processes and package designs.
ทั้งหมด, ceramic package substrates offer a compelling combination of thermal performance, electrical insulation, เสถียรภาพทางกล, and environmental resilience, making them an ideal choice for demanding electronic applications across industries.
How Much Does Ceramic Package Substrate Cost?
The cost of ceramic package substrates can vary significantly depending on several factors, including the material composition, size, complexity of design, กระบวนการผลิต, and volume of production. Here are some key factors that influence the cost:
- วัตถุ: Different ceramic materials have varying costs associated with their production. เช่น, alumina (อัล 2 โอ 3) tends to be less expensive compared to materials like aluminum nitride (อัลเอ็น) or beryllium oxide (BeO), which offer superior thermal conductivity but may come at a higher cost.
- กระบวนการผลิต: The manufacturing process used to produce ceramic package substrates can impact the cost. Techniques such as tape casting, extrusion, injection molding, and direct ceramic machining (DCM) each have associated costs related to equipment, materials, labor, and energy consumption.
- ความซับซ้อนของการออกแบบ: ความซับซ้อนของการออกแบบพื้นผิว, รวมถึงจํานวนชั้น, features, and tolerances, can affect manufacturing costs. More intricate designs may require additional processing steps, specialized equipment, and tighter quality control, which can increase overall production costs.
- ปริมาณการผลิต: Economies of scale play a significant role in determining the cost of ceramic package substrates. Higher production volumes typically result in lower unit costs due to efficiencies in material utilization, labor, and overhead expenses. Conversely, low-volume or custom production runs may incur higher costs per unit.
- Additional Processing and Finishing: Additional processing steps such as metallization, die attachment, wire bonding, and testing can add to the overall cost of ceramic package substrates. Advanced surface finishes, coatings, and quality control measures may also contribute to higher costs.
- Supplier and Market Factors: Pricing may vary among different suppliers based on factors such as geographic location, market demand, competition, and supplier capabilities. นอกจากนี้, fluctuations in raw material prices, labor costs, and economic conditions can impact overall substrate costs.
It’s important to note that ceramic package substrates are typically considered a higher-end option compared to organic substrates (เช่น, fiberglass-reinforced epoxy resins), and as such, they may command a premium price. อย่างไรก็ตาม, the specific cost of ceramic package substrates can vary widely depending on the aforementioned factors and should be evaluated based on the requirements and constraints of each individual application.
FQA
What is a ceramic package substrate?
A ceramic package substrate is a type of substrate used in semiconductor packaging to provide a stable platform for mounting integrated circuits (ไอซี) and facilitating electrical connections.
What materials are used in ceramic package substrates?
Ceramic package substrates are typically made from materials such as alumina (อัล 2 โอ 3), aluminum nitride (อัลเอ็น), beryllium oxide (BeO), ซิลิกอนไนไตรด์ (Si3N4), and glass-ceramics.
What are the advantages of ceramic package substrates?
Ceramic package substrates offer advantages such as high thermal conductivity, excellent electrical insulation, เสถียรภาพทางกล, compatibility with high temperatures, and resistance to environmental factors.
How are ceramic package substrates manufactured?
The manufacturing process for ceramic package substrates involves steps such as material preparation, shaping, firing (sintering), metallization, and optional additional processing like die attachment and wire bonding.
What are the applications of ceramic package substrates?
Ceramic package substrates find applications in semiconductor packaging, high-frequency and RF devices, power electronics, LED packaging, อุปกรณ์อิเล็กทรอนิกส์ยานยนต์, aerospace and defense, อุปกรณ์ทางการแพทย์, และอุปกรณ์อิเล็กทรอนิกส์สําหรับผู้บริโภค.
How much do ceramic package substrates cost?
The cost of ceramic package substrates varies depending on factors such as material composition, กระบวนการผลิต, complexity of design, ปริมาณการผลิต, and supplier factors.
What are the considerations for designing ceramic package substrates?
Design considerations for ceramic package substrates include thermal management, ประสิทธิภาพทางไฟฟ้า, mechanical integrity, compatibility with packaging technologies, and reliability in specific application environments.