Multilayer Ceramic Substrates Manufacturer
We are a professional Multilayer Ceramic Substrates Manufacturer, we mainly produce ultra-small bump pitch substrate, ultra-small trace and spacing packaging substrate and PCBs.
Multilayer Ceramic Substrates (MCS) are sophisticated electronic components crucial for the miniaturization and performance optimization of various electronic devices. Comprising multiple thin ceramic layers, typically alumina or aluminum nitride, MCS provides a robust platform for mounting and interconnecting electronic components. Embedded within these layers are intricate conductive traces and vias, facilitating efficient signal routing and power distribution. MCS offers numerous advantages, including high reliability, excellent thermal conductivity, and compatibility with high-frequency signals, making it indispensable in applications like smartphones, อุปกรณ์อิเล็กทรอนิกส์ยานยนต์, อุปกรณ์ทางการแพทย์, และอื่น ๆ. The manufacturing process involves precise fabrication techniques such as screen printing, layer stacking, firing, and conductor plating to achieve the desired structural integrity and electrical properties. With their compact design and superior performance characteristics, MCS continues to drive innovation in the ever-evolving landscape of electronic technology.
What is a Multilayer Ceramic Substrate (MCS)?
A Multilayer Ceramic Substrate (MCS) is a critical component in electronic devices, particularly in the realm of microelectronics and integrated circuit (IC) บรรจุ ภัณฑ์. It’s essentially a layered structure composed of thin ceramic layers, typically alumina (อัล 2 โอ 3) หรืออลูมิเนียมไนไตรด์ (อัลเอ็น), with conductive traces and vias patterned on them.
These substrates serve as the foundation for mounting and interconnecting various electronic components such as IC chips, resistors, capacitors, and inductors. They provide electrical insulation, การจัดการความร้อน, and mechanical support for the components.
The multilayer design allows for dense integration of electronic components in a small footprint, making MCS ideal for applications where space is at a premium, such as smartphones, แท็บ เล็ต, สวมใส่ได้, and automotive electronics.
The fabrication process of MCS involves several steps including ceramic green tape casting, screen printing of conductive and dielectric pastes, layer stacking, and firing at high temperatures to sinter the layers into a solid structure.
The key advantages of MCS include high reliability, excellent thermal conductivity, low electrical impedance, and compatibility with high-frequency signals. These properties make MCS essential in high-performance electronic devices where signal integrity, ความน่าเชื่อถือ, and miniaturization are paramount concerns.
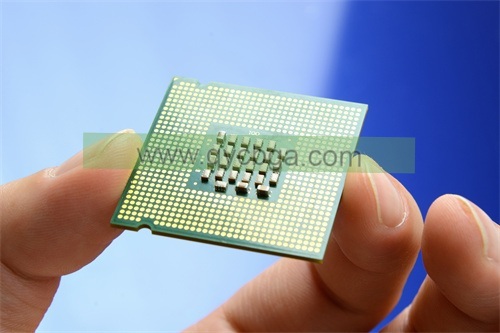
Multilayer Ceramic Substrates Manufacturer
What are the MCS Design Guidelines?
Designing Multilayer พื้นผิวเซรามิก (MCS) requires careful consideration of various factors to ensure optimal performance and reliability. Here are some general design guidelines:
- การซ้อนชั้น: Determine the number of layers needed based on the complexity of the circuit and the required electrical performance. Considerations include signal routing, การกระจายพลังงาน, and ground planes.
- Dielectric Material Selection: Choose the appropriate ceramic material (เช่น, alumina, aluminum nitride) based on factors such as dielectric constant, การนําความร้อน, และความแข็งแรงเชิงกล.
- Trace and Via Placement: Place traces and vias strategically to minimize signal interference, ครอสทอล์ค, and impedance mismatches. Keep high-speed signal traces short and direct to reduce signal propagation delays.
- ความสมบูรณ์ของสัญญาณ: Maintain controlled impedance for high-speed signal traces by controlling trace width, ระยะ ห่าง, and dielectric thickness. Ensure proper termination of transmission lines to minimize signal reflections.
- การจัดการความร้อน: Design adequate thermal vias and thermal pads to dissipate heat from high-power components. Ensure efficient heat transfer to the substrate and consider thermal expansion mismatches between materials.
- Power Distribution: Design power planes to minimize voltage drops and ensure uniform distribution of power across the substrate. Use multiple power and ground planes to reduce noise and provide stable power rails.
- Component Placement and Routing: Place components strategically to minimize signal path lengths and optimize layout for efficient assembly and soldering. Follow best practices for component placement, such as grouping related components and avoiding high-frequency signal crossings.
- Design for Manufacturability: Consider manufacturing constraints such as minimum feature size, layer alignment accuracy, and solder mask requirements. Ensure that the design can be manufactured reliably and cost-effectively.
- ข้อควรพิจารณาด้านความน่าเชื่อถือ: Design for mechanical stability and thermal cycling reliability. Avoid sharp corners and stress concentrations, and ensure adequate clearance between components to prevent electrical shorts.
- ความเข้ากันได้ทางแม่เหล็กไฟฟ้า (อีเอ็มซี): Design the substrate to minimize electromagnetic interference (อีเอ็มไอ) emissions and susceptibility. Use shielding techniques and layout optimization to reduce EMI effects on neighboring components.
By following these design guidelines, engineers can create Multilayer Ceramic Substrates that meet the performance, ความน่าเชื่อถือ, and manufacturability requirements of modern electronic devices.
What is the MCS Fabrication Process?
The fabrication process of Multilayer Ceramic Substrates (MCS) involves several steps to create the layered structure with embedded conductive traces and vias. Here’s a general overview of the MCS fabrication process:
- การเตรียมพื้นผิว: The process begins with preparing ceramic green tapes. These tapes are typically made of alumina (อัล 2 โอ 3) หรืออลูมิเนียมไนไตรด์ (อัลเอ็น) and are cast into thin, flexible sheets with controlled thickness and composition.
- Printing of Conductive and Dielectric Layers: Conductive and dielectric pastes are screen-printed onto the green tapes to create the desired circuit patterns. Conductive paste contains metals such as silver, gold, or copper, while dielectric paste provides insulation between conductive traces.
- Layer Stacking: Multiple layers of green tapes with printed patterns are stacked together to form the complete substrate structure. Alignment of the layers is critical to ensure proper interconnection between conductive traces and vias.
- เคลือบ:The stacked green tape layers are then subjected to high pressure and temperature in a lamination process. This compresses the layers together, removing any air gaps and bonding them into a solid structure.
- Via Formation: หลังจากเคลือบ, small holes are drilled or punched through the substrate at designated locations for vias. These vias will later provide vertical interconnection between different layers of the substrate.
- Firing: The substrate undergoes a firing process in a kiln at high temperatures (typically above 1000°C) to sinter the ceramic material and remove organic binders from the green tapes. This transforms the substrate into a dense, ceramic structure with embedded conductive traces.
- Conductor Plating: After firing, the vias are typically filled with conductive material through processes such as electroplating or screen printing. This ensures electrical continuity between different layers of the substrate.
- การตกแต่งพื้นผิว:The substrate surface may undergo additional processing such as grinding, polishing, or coating with protective layers to improve flatness, surface quality, and solderability.
- Final Inspection and Testing: The finished MCS undergoes inspection and testing to ensure adherence to design specifications, including dimensional accuracy, ความต่อเนื่องทางไฟฟ้า, and insulation resistance.
- บรรจุภัณฑ์และการประกอบ: Once validated, the MCS can be packaged and assembled with electronic components such as integrated circuits, resistors, capacitors, and inductors to create functional electronic devices.
ทั้งหมด, the fabrication process of Multilayer Ceramic Substrates is a complex series of steps that require precision, control, and expertise to produce high-quality substrates for various electronic applications.
How do you manufacture an MCS?
Manufacturing Multilayer Ceramic Substrates (MCS) involves a detailed process that combines ceramic technology with precision manufacturing techniques. Here’s a step-by-step guide to manufacturing an MCS:
- การเลือกวัสดุ: Choose the appropriate ceramic material based on the specific requirements of the application. Common materials include alumina (อัล 2 โอ 3) and aluminum nitride (อัลเอ็น), each offering different properties such as thermal conductivity, ค่าคงที่ไดอิเล็กทริก, และความแข็งแรงเชิงกล.
- Green Tape Production: Formulate ceramic slurry composed of ceramic powders, binders, solvents, and additives. Cast the slurry into thin sheets using a doctor blade or tape casting machine. Dry the sheets to remove excess solvent and form flexible green tapes.
- Conductor and Dielectric Paste Preparation: Prepare conductive and dielectric pastes by mixing metal powders (เช่น, silver, gold, ทองแดง) or dielectric materials with appropriate binders and solvents. These pastes will be used to print conductive traces and insulating layers onto the green tapes.
- Screen Printing: Use screen printing techniques to deposit conductive and dielectric pastes onto the green tapes, forming the desired circuit patterns and layers. Precision screen printing equipment ensures accurate deposition of paste layers with controlled thickness.
- การซ้อนชั้นและการเคลือบ: Stack multiple green tape layers with printed patterns in a precise sequence to create the multilayer structure. Apply pressure and heat during lamination to bond the layers together, forming a monolithic structure.
- Via Formation: Punch or drill holes through the laminated substrate at designated locations for vias, which provide vertical interconnection between different layers. The vias may be filled with conductive material later in the process.
- Firing (Sintering): Subject the laminated substrate to high temperatures in a kiln or furnace to sinter the ceramic material and remove organic binders. This process densifies the substrate, transforming it into a rigid ceramic structure with embedded conductive traces.
- Conductor Plating (Optional): Electroplate the vias with conductive material (เช่น, ทองแดง) to ensure electrical continuity between layers and improve solderability.
- การตกแต่งพื้นผิว: Grind, polish, or coat the substrate surface to achieve the desired flatness, smoothness, and surface quality. Apply protective coatings or finishes to enhance durability and solderability.
- Inspection and Testing: Conduct thorough inspection and testing of the finished MCS to verify dimensional accuracy, ความต่อเนื่องทางไฟฟ้า, insulation resistance, and adherence to design specifications.
- บรรจุภัณฑ์และการจัดส่ง: Package the finished MCS in suitable containers to protect them during storage and transportation. Ship the substrates to customers or assembly facilities for integration into electronic devices.
ตลอดกระบวนการผลิต, strict quality control measures are implemented to ensure consistency, ความน่าเชื่อถือ, and performance of the MCS for various electronic applications. Collaboration between materials scientists, engineers, and manufacturing specialists is essential to optimize the manufacturing process and produce high-quality substrates efficiently.
How much should an MCS cost?
The cost of Multilayer Ceramic Substrates (MCS) can vary widely depending on several factors, including:
- Materials: The cost of ceramic materials, such as alumina or aluminum nitride, can significantly impact the overall cost of the MCS. High-purity materials with specific properties may be more expensive.
- Manufacturing Complexity: The complexity of the MCS design and fabrication process affects manufacturing costs. More intricate designs, tighter tolerances, and additional features such as buried vias or specialized surface finishes can increase production costs.
- Production Volume: Economies of scale play a significant role in determining the cost of MCS. Higher production volumes generally lead to lower per-unit costs due to efficiencies in material usage, equipment utilization, and overhead expenses.
- Technology Requirements: Advanced technologies, such as fine-line printing, laser processing, and precision inspection equipment, may incur higher capital and operational costs, which can impact the overall cost of the MCS.
- มาตรฐานคุณภาพ: Compliance with industry standards and customer-specific quality requirements may involve additional testing, documentation, and quality assurance processes, adding to the overall cost.
- Supplier Relationships: The choice of MCS supplier and the nature of the relationship (เช่น, long-term contracts, strategic partnerships) can influence pricing negotiations and cost competitiveness.
- Market Conditions: Supply and demand dynamics, raw material prices, and competitive pressures within the MCS market can also affect pricing.
Given these factors, it’s challenging to provide a specific cost estimate for MCS without knowing the details of the project, including the design requirements, production volume, and quality expectations. อย่างไรก็ตาม, MCS prices typically range from a few dollars to several hundred dollars per unit, with custom or specialized substrates commanding higher prices. Large-scale production orders generally benefit from lower unit costs compared to small-batch or prototype orders.
What is MCS base material?
The base material used in Multilayer Ceramic Substrates (MCS) is typically ceramic, chosen for its excellent electrical insulation properties, การนําความร้อน, ความแข็งแรงเชิงกล, and compatibility with high-temperature processes. The most common ceramic materials used for MCS are:
- Alumina (อัล 2 โอ 3): Alumina is a widely used ceramic material in MCS fabrication due to its high dielectric strength, การนําความร้อน, and chemical resistance. It is suitable for various electronic applications, including high-frequency circuits, power modules, and LED substrates.
- Aluminum Nitride (อัลเอ็น): Aluminum nitride offers superior thermal conductivity compared to alumina, making it particularly suitable for applications requiring efficient heat dissipation, such as power electronics, RF/microwave devices, and high-power LED modules. AlN-based MCS can handle high power densities and thermal cycling stresses.
These ceramic materials are available in different grades and formulations tailored to specific application requirements, such as dielectric constant, thermal expansion coefficient, และคุณสมบัติทางกล. The choice of base material depends on factors such as the operating environment, performance specifications, and cost considerations.
Which company makes MCS?
There are many companies that manufacture Multilayer Ceramic Substrates (MCS), with some of the major manufacturers including Murata Manufacturing Co., Ltd., Kyocera Corporation, Hitachi Chemical Co., Ltd., and Murata Manufacturing. These companies have extensive experience and expertise in MCS manufacturing, offering various customized solutions to meet the needs of different industries and applications.
As for our company, we are a specialized manufacturer of high-performance electronic materials and devices, with advanced technology and production facilities capable of producing various types of Multilayer Ceramic Substrates. Our production capacity and expertise enable us to provide customized solutions to customers to meet their specific design requirements and performance needs.
Our company’s main advantages include:
- Advanced Manufacturing Technology: We employ state-of-the-art manufacturing technology and equipment, including precise printing, เคลือบ, firing, and plating processes, to ensure the production of high-quality MCS.
- Customization Capability: We can customize MCS according to the specific requirements of customers, including customized layer stack-up, electrical characteristics, dimensions, and surface treatments.
- Quality Control: We strictly adhere to ISO quality management systems, implementing comprehensive quality control measures to ensure that each MCS meets design specifications and quality standards.
- Quick Response and Delivery: We have flexible production schedules and supply chain management, enabling us to respond quickly to customer demands and deliver high-quality products promptly.
- Technical Support and Service: Our team possesses extensive technical knowledge and experience, providing comprehensive technical support and solutions in MCS design, manufacturing, and application.
โดยสรุป, our company is committed to providing customers with high-performance, reliable Multilayer Ceramic Substrates to meet various electronic application needs. Our expertise, advanced technology, and quality service make us a trusted partner for customers.
คืออะไร 7 คุณภาพของการบริการลูกค้าที่ดี?
Good customer service is essential for building strong relationships with customers and fostering loyalty. Here are seven qualities that characterize excellent customer service:
- ตอบ สนอง: Respond promptly to customer inquiries, เกี่ยว ข้อง กับ, และคําขอ. Customers appreciate timely assistance and expect quick resolution of their issues.
- ความเห็นอกเห็นใจ: Show empathy and understanding towards customers’ needs and emotions. Listen actively, acknowledge their concerns, and demonstrate genuine care and concern.
- มือ อาชีพ: Maintain professionalism in all interactions with customers. Be courteous, สุภาพ, and knowledgeable about products or services. Present a positive and competent image of the company.
- ความน่าเชื่อถือ: Consistently deliver on promises and commitments made to customers. Build trust by providing accurate information, meeting deadlines, and following through on resolutions.
- Flexibility: Adapt to customers’ preferences and accommodate their individual needs whenever possible. Offer flexible solutions and options to address diverse customer requirements.
- ทักษะการแก้ปัญหา: Possess strong problem-solving abilities to address customer issues effectively. Take ownership of problems, explore solutions proactively, and strive to resolve issues to the customer’s satisfaction.
- Personalization: Provide personalized service by recognizing and addressing customers by name, understanding their preferences, and tailoring interactions to suit their individual preferences and past experiences.
โดยรวบรวมคุณสมบัติเหล่านี้, businesses can create positive experiences for customers, เพิ่มระดับความพึงพอใจ, and build long-lasting relationships that drive loyalty and advocacy.
คําถามที่พบบ่อย
What are the advantages of MCS?
MCS offers several advantages, including high reliability, excellent thermal conductivity, low electrical impedance, and compatibility with high-frequency signals. It enables dense integration of electronic components in a small footprint, making it ideal for space-constrained applications.
What applications are MCS used in?
MCS finds applications in a wide range of electronic devices, รวมถึงสมาร์ทโฟน, แท็บ เล็ต, สวมใส่ได้, อุปกรณ์อิเล็กทรอนิกส์ยานยนต์, อุปกรณ์ทางการแพทย์, aerospace systems, and industrial equipment.
What materials are used in MCS?
The base material for MCS is typically ceramic, such as alumina (อัล 2 โอ 3) หรืออลูมิเนียมไนไตรด์ (อัลเอ็น). These materials offer excellent electrical insulation, การนําความร้อน, and mechanical strength required for electronic applications.
How are MCS manufactured?
The fabrication process of MCS involves steps such as preparing ceramic green tapes, printing conductive and dielectric layers, stacking and laminating layers, via formation, firing (sintering) in a kiln, conductor plating, การตกแต่งพื้นผิว, and final inspection and testing.
What factors affect the cost of MCS?
The cost of MCS can vary depending on factors such as materials used, manufacturing complexity, production volume, technology requirements, quality standards, and market conditions.
What companies manufacture MCS?
Several companies manufacture MCS, including Murata Manufacturing Co., Ltd., Kyocera Corporation, Hitachi Chemical Co., Ltd., and others. These companies have extensive experience and expertise in MCS manufacturing.
What are the key considerations for MCS design?
Key considerations for MCS design include layer stackup, trace and via placement, signal integrity, การจัดการความร้อน, การกระจายพลังงาน, component placement and routing, design for manufacturability, reliability considerations, and electromagnetic compatibility (อีเอ็มซี).