Minimum Clearance LED PCB Manufacturer
Minimum Clearance LED PCB Manufacturer,Minimum Clearance LED PCBs are specialized printed circuit boards designed specifically for LED applications, featuring closely spaced conductive elements optimized for high-density LED configurations. These PCBs play a crucial role in applications requiring compact LED modules, such as LED displays, backlighting systems, and high-power LED arrays. By minimizing the distance between conductive traces and pads, Minimum Clearance LED PCBs enable efficient routing of electrical signals while ensuring reliable performance and electrical integrity. They incorporate advanced manufacturing techniques to achieve fine pitch clearances without compromising reliability or functionality. With a focus on thermal management, electrical insulation, and adherence to industry standards, Minimum Clearance LED PCBs provide the foundation for high-performance LED solutions that meet the demands of modern lighting and display technologies.
What is a Minimum Clearance LED PCB?
A Minimum Clearance LED PCB (Printed Circuit Board) refers to a PCB specifically designed for LED (Light Emitting Diode) โปรแกรม ประยุกต์, where the spacing between the conductive elements (traces, pads, and vias) is minimized to the smallest allowable limit. This minimization is crucial to ensure reliable operation and to meet the electrical and mechanical requirements of compact LED modules.
In LED PCB design, the term “minimum clearance” denotes the smallest distance permissible between different conductive features on the board. This clearance is dictated by several factors, including manufacturing capabilities, electrical insulation requirements, and safety standards. Reducing the clearance to a minimum allows for a more densely packed layout, which is particularly advantageous in applications requiring high LED density, such as in display panels, backlighting, and high-power LED arrays.
Key considerations in designing a Minimum Clearance LED PCB include:
- ความคลาดเคลื่อนในการผลิต: Advanced fabrication processes are required to achieve fine pitch clearances without causing shorts or defects. High-precision etching and laser drilling are commonly used.
- ประสิทธิภาพทางไฟฟ้า: Adequate clearance must be maintained to prevent electrical arcing and crosstalk between adjacent traces, especially in high-voltage LED circuits.
- การจัดการความร้อน: LED PCBs often incorporate thermal management features, such as metal-core substrates or heat sinks, to dissipate heat efficiently. Proper clearance helps in maintaining thermal pathways and ensuring consistent LED performance.
- Reliability and Durability: Ensuring sufficient clearance is essential for the long-term reliability of the PCB, preventing issues like solder bridging and corrosion, which can be exacerbated in high-density designs.
- Compliance with Standards: Adherence to industry standards (such as IPC standards for PCB design) and regulatory requirements (like UL certifications) ensures safety and functionality in the end application.
โดยสรุป, a Minimum Clearance LED PCB is a specialized type of PCB designed to optimize space while ensuring electrical integrity and thermal performance for LED applications. The meticulous design of these PCBs is vital for achieving high-density, reliable, and efficient LED solutions.
What are the PCB Design Guidelines for Minimum Clearance LED PCBs?
PCB design guidelines for Minimum Clearance LED PCBs include considerations such as trace width, spacing between traces, thermal management for LEDs, and component placement to ensure efficient heat dissipation and optimal electrical performance.
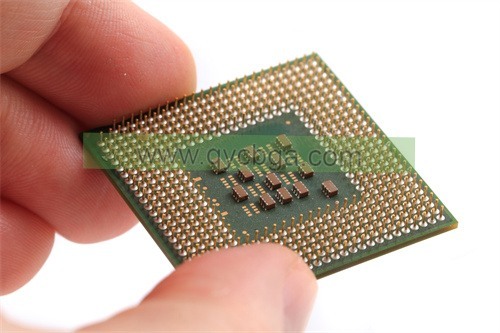
Minimum Clearance LED PCB Manufacturer
What is the Minimum Clearance LED PCB Fabrication Process?
The fabrication process of a Minimum Clearance LED PCB involves several intricate steps that are optimized to achieve the minimal clearance between conductive paths while maintaining functionality and reliability. This process involves advanced manufacturing techniques to accommodate the higher density of components and finer trace widths required by such designs. Here’s an overview of the key steps in the fabrication process:
- Design and Layout: The process begins with a detailed design and layout phase using CAD (การออกแบบโดยใช้คอมพิวเตอร์ช่วย) ซอฟต์แวร์. Engineers design the PCB keeping in mind the minimum clearance rules based on the application’s voltage and current requirements, environmental conditions, and compliance standards. Particular attention is given to trace width, ระยะ ห่าง, and component placement to avoid electrical shorts and ensure reliability.
- การเลือกวัสดุ: For LED PCBs, material selection is crucial due to the thermal management requirements. Materials often include FR-4, Aluminum, or Copper-core substrates. The choice depends on the thermal conductivity needed and the mechanical strength required.
- Photolithography: This step involves transferring the PCB layout from a digital file onto a physical board. A light-sensitive chemical (photoresist) is applied to the copper layers of the substrate. Using a photomask which shields parts of the photoresist from UV light, the exposed areas are developed to create a pattern that matches the PCB design.
- แกะ สลัก: The exposed copper not protected by the developed photoresist is then chemically etched away, leaving behind the copper traces that were covered. Precision etching is essential for maintaining the minimum clearances without errors.
- Drilling and Plating:After etching, holes or vias are drilled to allow electrical connection between different layers of the PCB. These holes are then plated with copper to establish these connections. The accuracy and alignment of drilling are critical in maintaining the integrity of the minimum clearances.
- การประยุกต์ใช้หน้ากากประสาน: A solder mask is then applied over the entire surface except where soldering components are required. This layer prevents accidental solder bridging between closely spaced traces and pads, which is a significant concern in Minimum Clearance PCBs.
- เสร็จสิ้นพื้นผิว: Various surface finishes can be applied to protect the copper from oxidation and to ensure a good solderable surface. Common finishes include HASL (การปรับระดับบัดกรีลมร้อน), เอนิก (นิกเกิลแช่ทองแบบไม่ใช้ไฟฟ้า), and OSP (สารกันบูดความสามารถในการบัดกรีอินทรีย์).
- Assembly and Testing: ในที่สุด, components are mounted onto the PCB using surface-mount technology (SMT), through-hole technology, or a combination of both. After assembly, the PCB undergoes various testing procedures, รวมถึงการทดสอบทางไฟฟ้า (to check for shorts and opens), thermal testing, and sometimes environmental testing, to ensure it meets the specified requirements.
- Quality Control: ตลอดกระบวนการผลิต, quality control measures are implemented. This includes inspection at various stages, such as after etching and drilling, to ensure that the minimum clearances are maintained and that there are no defects.
พื้นที่ Minimum Clearance LED PCB fabrication process requires high precision and control, especially in photolithography, แกะ สลัก, and drilling stages, to maintain the integrity of very small clearances necessary for high-density, high-efficiency LED applications.
How do you manufacture a Minimum Clearance LED PCB?
Manufacturing a Minimum Clearance LED PCB involves several steps, each crucial for achieving the desired level of precision and reliability required for LED applications with closely spaced conductive elements. Here’s a detailed overview of the manufacturing process:
- Design and Layout: Engineers create a detailed PCB layout using specialized software, considering factors such as LED placement, trace routing, and minimum clearance requirements. The design phase is critical for ensuring that the layout meets electrical, ร้อน, และข้อกําหนดทางกล.
- การเลือกวัสดุ: Choose appropriate PCB substrate materials based on factors such as thermal conductivity, dielectric properties, และความแข็งแรงเชิงกล. Common materials include FR-4, Aluminum, and Copper-core substrates, selected based on the specific needs of the LED application.
- การเตรียมพื้นผิว: The chosen substrate material is prepared by cutting it to the required size and cleaning the surface to remove any contaminants. Surface preparation is essential for ensuring proper adhesion of subsequent layers and achieving optimal electrical performance.
- Application of Copper Layer: A thin layer of copper is applied to the substrate surface through processes like electroplating or lamination. This copper layer forms the conductive traces and pads necessary for routing electrical signals on the PCB.
- Photolithography: A layer of photosensitive material, called photoresist, is applied over the copper layer. A photomask containing the PCB design pattern is then used to selectively expose the photoresist to UV light. After exposure, the unexposed areas of the photoresist are removed, leaving behind a pattern that corresponds to the desired PCB layout.
- แกะ สลัก: The exposed copper areas not protected by the developed photoresist are chemically etched away, leaving behind the conductive traces and pads. Precision etching is crucial for maintaining the minimum clearances between adjacent conductive elements.
- เจาะ: Holes or vias are drilled into the PCB substrate to allow for component mounting and interconnection between different layers of the PCB. High-precision drilling equipment is used to ensure accuracy and alignment of the holes, especially in designs with tight clearances.
- การตกแต่งพื้นผิว: Various surface finishes, such as HASL (การปรับระดับบัดกรีลมร้อน), เอนิก (นิกเกิลแช่ทองแบบไม่ใช้ไฟฟ้า), หรือ OSP (สารกันบูดความสามารถในการบัดกรีอินทรีย์), are applied to protect the exposed copper surfaces from oxidation and provide a solderable finish.
- การประยุกต์ใช้หน้ากากประสาน: A solder mask is applied over the entire surface of the PCB, leaving openings only where soldering is required for component attachment. The solder mask protects the conductive traces and pads from environmental damage and prevents solder bridging between closely spaced features.
- Component Placement and Soldering: LED components and other surface-mount or through-hole components are mounted onto the PCB using automated assembly equipment. Solder paste is applied to the component pads, and the components are then soldered to the PCB using reflow soldering or wave soldering techniques.
- Testing and Quality Control: The assembled PCBs undergo rigorous testing to ensure functionality, ความต่อเนื่องทางไฟฟ้า, and adherence to design specifications. Testing may include electrical testing, thermal testing, and inspection for defects using automated optical inspection (อาโอไอ) or other methods.
- บรรจุภัณฑ์และการจัดส่ง: Once the PCBs pass quality control checks, they are packaged according to customer requirements and shipped to their destination for integration into LED lighting systems or other applications.
By following these steps carefully and employing advanced manufacturing techniques, manufacturers can produce Minimum Clearance LED PCBs that meet the stringent requirements of high-density LED applications while ensuring reliability and performance.
How much should a Minimum Clearance LED PCB cost?
The cost of a Minimum Clearance LED PCB can vary widely depending on several factors, รวมถึงความซับซ้อนของการออกแบบ, ปริมาณการสั่งซื้อ, the choice of materials and surface finishes, the manufacturing technology used, and the supplier’s pricing structure. อย่างไรก็ตาม, I can provide a rough estimate based on typical industry standards and considerations:
- ความซับซ้อนของการออกแบบ: More complex designs with intricate routing, ส่วนประกอบพิทช์ละเอียด, and tight minimum clearance requirements may require advanced manufacturing processes, driving up the cost.
- ปริมาณ: Bulk orders typically result in lower per-unit costs due to economies of scale. อย่างไรก็ตาม, small prototype runs or low-volume production may incur higher costs per unit.
- Materials: The choice of PCB substrate material, such as FR-4, Aluminum, or Copper-core, อาจส่งผลกระทบต่อต้นทุน. นอกจากนี้, special materials or laminates with enhanced thermal properties may command higher prices.
- เสร็จสิ้นพื้นผิว: Different surface finishes, such as HASL, เอนิก, หรือ OSP, have varying costs associated with them. More advanced surface finishes may be more expensive but offer superior performance and durability.
- เทคโนโลยีการผลิต:Advanced manufacturing technologies, such as HDI (High-Density Interconnect) or laser drilling, may be required for achieving tight minimum clearance specifications, ซึ่งสามารถเพิ่มต้นทุนการผลิตได้.
- Supplier Pricing: PCB fabrication costs can vary between different suppliers based on factors such as location, equipment capabilities, labor costs, and overhead expenses.
เป็นการประมาณการคร่าวๆ, the cost of a Minimum Clearance LED PCB can range from a few dollars for simple designs in low quantities to tens or hundreds of dollars for complex designs in larger quantities. It’s advisable to obtain quotes from multiple PCB manufacturers and compare pricing, lead times, and quality to ensure the best value for your specific requirements. นอกจากนี้, working closely with your PCB manufacturer to optimize the design for manufacturability can help reduce costs while maintaining performance and reliability.
What is the Minimum Clearance LED PCB base material?
The choice of base material for a Minimum Clearance LED PCB depends on various factors such as thermal conductivity requirements, ความแข็งแรงเชิงกล, and cost considerations. Several materials are commonly used for LED PCB substrates, each offering different properties:
- FR-4 (สารหน่วงไฟ 4): FR-4 is a widely used substrate material for PCBs due to its excellent electrical insulation properties, affordability, and ease of fabrication. It consists of woven fiberglass impregnated with an epoxy resin. While FR-4 offers good electrical performance, it has limited thermal conductivity compared to other materials, which may be a consideration for high-power LED applications.
- Aluminum: Aluminum PCBs feature a thermally conductive aluminum core, which provides superior heat dissipation compared to traditional FR-4 substrates. This makes them suitable for high-power LED applications where efficient thermal management is critical. Aluminum PCBs typically have a higher cost but offer enhanced reliability and performance in demanding LED lighting applications.
- Copper-core:Copper-core PCBs have a layer of copper embedded within the substrate, providing excellent thermal conductivity and heat dissipation properties. They are well-suited for high-power LED applications where heat generation is a concern. Copper-core PCBs offer superior thermal performance compared to FR-4 and are often used in LED lighting fixtures, automotive lighting, and other high-power applications.
- Metal-clad laminates: Metal-clad laminates feature a metal layer bonded to one or both sides of the substrate, providing enhanced thermal conductivity and mechanical strength. Common metals used include aluminum and copper. Metal-clad laminates offer improved thermal performance compared to traditional FR-4 substrates and are suitable for high-power LED applications where efficient heat dissipation is essential.
The choice of base material for a Minimum Clearance LED PCB depends on factors such as thermal management requirements, cost considerations, and performance specifications. Designers must carefully evaluate these factors to select the most suitable substrate material that meets the specific needs of their LED application while ensuring reliability and performance.
Which company makes Minimum Clearance LED PCBs?
There are many companies specializing in Minimum Clearance LED PCB production. Some of these companies are leading global PCB manufacturers and suppliers, such as Foxconn, Lenovo, ASUS, and others. These companies possess advanced manufacturing equipment, เทคโนโลยี, and experience to meet the needs of various LED applications and provide high-quality, reliable, and cost-effective products.
In addition to large PCB manufacturers, there are also some small and medium-sized companies focusing on LED PCBs. These companies typically have flexible production capabilities and offer customized services, able to tailor Minimum Clearance LED PCBs according to customers’ specific requirements, and provide more personalized technical support and solutions.
Our company is also a professional LED PCB manufacturer with extensive experience and expertise. We have advanced production equipment and a technical team capable of meeting various customer needs for Minimum Clearance LED PCBs.
Our production capabilities include:
- Advanced Manufacturing Equipment: We have advanced PCB production equipment, including automated lithography equipment, precision chemical etching machines, and high-precision drilling equipment, capable of achieving high-precision traces and clearances.
- Professional Technical Team:We have an experienced technical team capable of providing comprehensive technical support and solutions to customers. Whether it’s design, process optimization, or quality control, we can provide professional advice and services.
- Strict Quality Control: Our company implements a strict quality management system, conducting strict quality control at every stage from raw material procurement to production, ensuring that products meet customer requirements and standards.
- Customized Services: We can customize Minimum Clearance LED PCBs according to customers’ specific needs, including design, การเลือกวัสดุ, process optimization, ฯลฯ, providing customers with personalized solutions.
- Timely Delivery: We can deliver customer orders on time, ensuring that customers’ production schedules are not affected, and providing timely after-sales service and support.
Through our company’s professional technology and services, we can provide customers with high-quality, reliable, and cost-effective Minimum Clearance LED PCBs, meeting various customer needs for LED applications and achieving win-win cooperation.
คืออะไร 7 คุณภาพของการบริการลูกค้าที่ดี?
Good customer service is characterized by several key qualities that contribute to positive interactions and lasting relationships with customers. นี่คือคุณสมบัติเจ็ดประการของการบริการลูกค้าที่ดี:
- ตอบ สนอง: Good customer service involves being prompt and responsive to customer inquiries, ร้อง ขอ, และความกังวล. Customers appreciate quick and efficient assistance, whether it’s answering questions, resolving issues, or providing support.
- ความเห็นอกเห็นใจ: Empathy is the ability to understand and relate to customers’ feelings, จำ เป็น ต้อง, and perspectives. Good customer service representatives listen actively, show genuine concern for customers’ problems, and strive to address their concerns with compassion and understanding.
- การสื่อสารที่ชัดเจน: Clear communication is essential for effective customer service. Good customer service representatives communicate clearly and effectively, using language that is easy to understand and providing relevant information in a concise manner. They also listen attentively to customers’ concerns and ensure that they understand and are understood.
- ทักษะการแก้ปัญหา: Good customer service involves the ability to effectively resolve customer issues and problems. Customer service representatives should be resourceful, proactive, and solution-oriented, working collaboratively with customers to find satisfactory resolutions to their concerns.
- มือ อาชีพ:Professionalism encompasses various qualities such as courtesy, respect, and integrity. Good customer service representatives conduct themselves in a professional manner at all times, treating customers with courtesy and respect, maintaining confidentiality, and upholding ethical standards.
- Product Knowledge:Good customer service requires a thorough understanding of the products or services being offered. Customer service representatives should possess comprehensive product knowledge and be able to provide accurate information, ตอบคําถาม, and offer recommendations to customers.
- Follow-Up and Follow-Through: Good customer service doesn’t end with resolving the immediate issue. It also involves following up with customers to ensure their satisfaction and following through on commitments made. Customer service representatives should take proactive steps to address any ongoing concerns and maintain open lines of communication with customers.
โดยรวบรวมคุณสมบัติเหล่านี้, businesses can cultivate positive customer experiences, build trust and loyalty, and ultimately, foster long-term relationships with their customers.
คําถามที่พบบ่อย
What is a Minimum Clearance LED PCB?
A Minimum Clearance LED PCB is a printed circuit board specifically designed for LED applications, featuring closely spaced conductive elements to accommodate high-density LED configurations while ensuring electrical integrity and reliability.
Why are Minimum Clearance LED PCBs important?
Minimum Clearance LED PCBs are crucial for applications requiring high-density LED arrays, such as LED displays, backlighting, and high-power LED modules. They allow for compact designs while maintaining adequate spacing between conductive traces to prevent electrical shorts and ensure reliable performance.
What factors should be considered when designing Minimum Clearance LED PCBs?
Key considerations include electrical insulation requirements, การจัดการความร้อน, manufacturing tolerances, compliance with standards, and reliability concerns. Designers must balance these factors to achieve optimal performance and reliability in LED applications.
What are the challenges in manufacturing Minimum Clearance LED PCBs?
Challenges include achieving fine pitch clearances without causing shorts or defects, ensuring adequate thermal management for high-power LED applications, and meeting stringent quality and reliability requirements. Advanced manufacturing processes and quality control measures are essential to overcome these challenges.
What materials are commonly used in Minimum Clearance LED PCBs?
Common materials include FR-4, Aluminum, Copper-core substrates, and metal-clad laminates. The choice of material depends on factors such as thermal conductivity, ความแข็งแรงเชิงกล, and cost considerations.
How can I ensure the reliability of Minimum Clearance LED PCBs?
Reliability can be ensured through proper design, การเลือกวัสดุ, กระบวนการผลิต, and quality control measures. Adhering to industry standards and regulatory requirements also contributes to the reliability of Minimum Clearance LED PCBs.
Where can I source Minimum Clearance LED PCBs?
Minimum Clearance LED PCBs can be sourced from specialized PCB manufacturers and suppliers that offer expertise in LED PCB design and fabrication. It’s essential to choose a reputable supplier with experience in producing high-quality LED PCBs tailored to your specific requirements.