Micro LED Substrate Manufacturer
Micro LED Substrate Manufacturer,Micro LED substrates serve as the fundamental building blocks for Micro LED displays, offering a solid foundation for the integration of individual Micro LEDs. These substrates are meticulously engineered to provide mechanical support, electrical connectivity, and thermal management for the tiny, high-performance LEDs.
Crafted from materials like silicon, glass, or flexible polymers, Micro LED substrates undergo a precise fabrication process. Thin-film deposition techniques create layers conducive to electrical conductivity and insulation, while advanced patterning methods define the layout for Micro LED placement. Each Micro LED is then carefully integrated onto the substrate, ensuring uniformity and alignment.
These substrates play a pivotal role in the creation of high-resolution displays with exceptional brightness, energy efficiency, and color performance. With ongoing advancements in manufacturing processes and materials, Micro LED substrates are driving innovation in various industries, from consumer electronics to automotive displays and beyond. Their versatility and reliability continue to expand the possibilities for next-generation display technologies.
What is a Micro LED Substrate?
A Micro LED substrate is a fundamental component in Micro LED display technology. Micro LEDs are tiny, individual light-emitting diodes (LEDs) that are much smaller than traditional LEDs, often on the scale of micrometers. These LEDs can be individually controlled, allowing for high-resolution displays with exceptional brightness and energy efficiency.
The substrate serves as the foundation upon which the Micro LEDs are fabricated. It typically consists of a flat surface, often made of materials like silicon or glass, onto which the Micro LEDs are precisely deposited or transferred. The substrate provides mechanical support, electrical connectivity, and thermal management for the Micro LEDs.
Key characteristics of a Micro LED substrate include:
- Precision: The substrate must be manufactured with extremely high precision to ensure that each Micro LED is positioned accurately, allowing for seamless integration and alignment.
- Electrical Conductivity: The substrate must provide electrical pathways to power each individual Micro LED, typically through thin-film transistors (TFTs) or other circuitry integrated directly onto the substrate.
- การจัดการความร้อน: Micro LEDs can generate heat, so the substrate often incorporates features to dissipate heat efficiently, preventing overheating and maintaining optimal performance.
- Durability: Since Micro LED displays are often intended for use in a variety of applications, including consumer electronics and large-scale displays, the substrate must be durable and resistant to damage.
ทั้งหมด, the substrate plays a critical role in the performance and reliability of Micro LED displays, enabling the creation of high-resolution, energy-efficient, and vibrant displays for various applications.
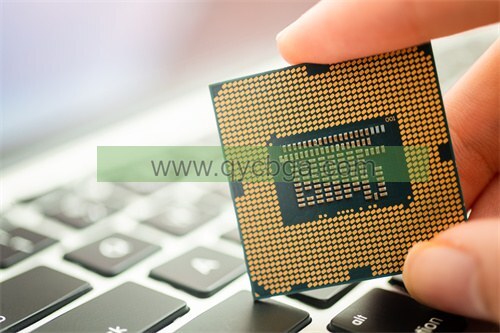
Micro LED Substrate Manufacturer
What are Micro LED Substrate Design Guidelines?
Micro LED substrate design guidelines encompass a range of considerations to ensure optimal performance and reliability of Micro LED displays. Here are some key design guidelines:
- Pixel Density and Size: Determine the desired pixel density and size of the Micro LEDs on the substrate based on the application requirements. Higher pixel density enables higher resolution displays, but it also increases manufacturing complexity and cost.
- Substrate Material: Choose an appropriate substrate material that offers good thermal conductivity, electrical insulation, and mechanical stability. Common substrate materials include silicon, glass, and flexible polymers like polyimide.
- Uniformity and Alignment: Ensure uniformity and precise alignment of Micro LEDs on the substrate to avoid visual defects such as non-uniform brightness or color variation. Advanced manufacturing techniques like photolithography and transfer printing can help achieve this.
- Electrical Connectivity:Design the substrate to provide efficient electrical connectivity to each Micro LED, typically through thin-film transistor (TFT) arrays or other circuitry. Minimize resistance and capacitance to reduce power consumption and improve signal integrity.
- การจัดการความร้อน: Incorporate features for effective thermal management to dissipate heat generated by the Micro LEDs. This can include heat sinks, thermal vias, or thermally conductive substrates to prevent overheating and ensure long-term reliability.
- Mechanical Durability: Ensure the substrate is mechanically robust to withstand handling during manufacturing and operation. Consider factors such as substrate thickness, flexural strength, and resistance to mechanical stress.
- Process Compatibility: Design the substrate fabrication process to be compatible with the deposition and transfer techniques used for Micro LED integration. Compatibility with existing semiconductor manufacturing processes can streamline production and reduce costs.
- Encapsulation and Protection: Implement appropriate encapsulation and protection layers to shield the Micro LEDs from environmental factors such as moisture, oxygen, และความเสียหายทางกล, which can degrade performance and longevity.
- Testing and Quality Control:Develop testing protocols and quality control measures to verify substrate performance, ensure uniformity, and detect defects early in the manufacturing process.
โดยปฏิบัติตามแนวทางการออกแบบเหล่านี้, manufacturers can develop Micro LED substrates that meet the requirements for high-performance displays across various applications, from consumer electronics to automotive displays and beyond.
What is the Micro LED Substrate Fabrication Process?
พื้นที่ Micro LED substrate fabrication process involves several steps to create the foundation upon which Micro LEDs are deposited or transferred. While specific details may vary depending on the technology and materials used, here’s a general overview of the process:
- การเตรียมพื้นผิว: The fabrication process begins with preparing the substrate material, which is typically a flat surface made of silicon, glass, or flexible polymers like polyimide. The substrate surface may undergo cleaning and treatment processes to ensure optimal adhesion and compatibility with subsequent layers.
- Thin-Film Deposition: Thin-film deposition techniques such as physical vapor deposition (พีวีดี) or chemical vapor deposition (CVD) are used to deposit layers of materials onto the substrate. These layers may include conductive materials for electrical connectivity, insulating materials for isolation, and barrier layers for protection against environmental factors.
- Pattern Formation: Photolithography or other patterning techniques are employed to define the precise layout of features on the substrate, such as electrode pads, interconnects, and thin-film transistor (TFT) arrays. Photomasks are used to selectively expose photoresist material on the substrate, which is then developed to create the desired patterns.
- แกะ สลัก: Etching processes, such as wet etching or dry etching, are used to remove unwanted material from the substrate surface based on the pattern defined in the previous step. This step creates recesses or trenches for the subsequent deposition of active components.
- Active Component Deposition: Micro LEDs are either directly deposited or transferred onto the prepared substrate. Direct deposition methods involve growing or assembling Micro LEDs directly on the substrate surface using techniques like metal-organic chemical vapor deposition (MOCVD) or molecular beam epitaxy (MBE). Transfer methods involve fabricating Micro LEDs on a separate substrate and then transferring them onto the target substrate using techniques like pick-and-place or elastomer stamping.
- Encapsulation and Protection: Once the Micro LEDs are integrated onto the substrate, encapsulation layers are applied to protect them from environmental factors such as moisture, oxygen, และความเสียหายทางกล. These layers may include transparent materials like glass or polymers, applied through techniques such as spin coating, spray coating, or lamination.
- Testing and Quality Control: The fabricated Micro LED substrates undergo rigorous testing and quality control to ensure uniformity, functionality, และความน่าเชื่อถือ. Various tests may be performed, รวมถึงการทดสอบทางไฟฟ้า, optical inspection, and reliability testing under different environmental conditions.
โดยทําตามขั้นตอนเหล่านี้, manufacturers can fabricate Micro LED substrates that serve as the foundation for high-performance displays with exceptional brightness, resolution, and energy efficiency.
How do you manufacture a Micro LED Substrate?
Manufacturing a Micro LED substrate involves a series of complex processes to create a foundation suitable for the integration of Micro LEDs. Here’s a step-by-step overview of the manufacturing process:
- Substrate Selection: Choose a suitable substrate material based on the application requirements. Common substrate materials include silicon, glass, or flexible polymers like polyimide. The substrate should have properties such as good thermal conductivity, electrical insulation, and mechanical stability.
- การเตรียมพื้นผิว: Clean the substrate surface thoroughly to remove any contaminants or particles that could interfere with subsequent processing steps. Treat the substrate surface to enhance adhesion and promote uniform film deposition.
- Thin-Film Deposition: Use techniques such as physical vapor deposition (พีวีดี) or chemical vapor deposition (CVD) to deposit thin films of materials onto the substrate surface. These films may include conductive layers for electrical connectivity, insulating layers for isolation, and barrier layers for protection.
- ลวดลาย: Employ photolithography or other patterning techniques to define the layout of features on the substrate, such as electrode pads, interconnects, and thin-film transistor (TFT) arrays. Photomasks are used to selectively expose photoresist material on the substrate, which is then developed to create the desired patterns.
- แกะ สลัก: Use etching processes, such as wet etching or dry etching, to remove unwanted material from the substrate surface based on the defined patterns. This step creates recesses or trenches for the subsequent integration of active components.
- Active Component Integration: Micro LEDs are either directly fabricated or transferred onto the prepared substrate. Direct fabrication methods involve growing or assembling Micro LEDs directly on the substrate surface using techniques like metal-organic chemical vapor deposition (MOCVD) or molecular beam epitaxy (MBE). Transfer methods involve fabricating Micro LEDs on a separate substrate and then transferring them onto the target substrate using techniques like pick-and-place or elastomer stamping.
- Encapsulation and Protection: Apply encapsulation layers to protect the integrated Micro LEDs from environmental factors such as moisture, oxygen, และความเสียหายทางกล. These layers may include transparent materials like glass or polymers, applied through techniques such as spin coating, spray coating, or lamination.
- Testing and Quality Control: Conduct rigorous testing and quality control to ensure the uniformity, functionality, and reliability of the fabricated Micro LED substrates. Various tests may be performed, รวมถึงการทดสอบทางไฟฟ้า, optical inspection, and reliability testing under different environmental conditions.
By following these manufacturing steps with precision and attention to detail, manufacturers can produce Micro LED substrates that form the basis for high-performance displays in various applications.
How much should a Micro LED Substrate cost?
The cost of a Micro LED substrate can vary significantly depending on various factors such as the size of the substrate, the complexity of the design, the quality of materials used, the manufacturing process employed, และปริมาณการผลิต. As of my last update, the cost of Micro LED substrates remains relatively high compared to traditional LED or LCD display substrates due to the intricate fabrication processes involved and the nascent stage of Micro LED technology.
อย่างไรก็ตาม, as manufacturing techniques improve, economies of scale are achieved, and technological advancements reduce production costs, the cost of Micro LED substrates is expected to decrease over time. นอกจากนี้, competition in the Micro LED market and advancements in materials science and manufacturing efficiency may further drive down costs.
It’s challenging to provide an exact cost estimate for a Micro LED substrate without specific details about the size, specifications, and manufacturing process. โดยทั่วไป, Micro LED substrates can range from hundreds to thousands of dollars per square meter, with larger substrates and higher-resolution displays commanding higher prices.
As Micro LED technology matures and becomes more widespread, it is anticipated that the cost of Micro LED substrates will become more competitive with existing display technologies, making them more accessible for various applications such as consumer electronics, automotive displays, and large-scale signage.
What is Micro LED Substrate base material?
The base material for Micro LED substrates can vary depending on the specific application and manufacturing process. Some common materials used as the substrate base for Micro LED displays include:
- Silicon: Silicon substrates are widely used in semiconductor manufacturing due to their excellent thermal conductivity, เสถียรภาพทางกล, and compatibility with integrated circuit fabrication processes. Silicon substrates can be rigid or flexible, depending on the application requirements.
- Glass: Glass substrates offer high optical transparency, chemical inertness, and flatness, making them suitable for high-resolution displays where image quality is paramount. Glass substrates are often used in consumer electronics such as smartphones, แท็บ เล็ต, and televisions.
- Flexible Polymers: Flexible polymer substrates, such as polyimide or transparent flexible substrates like polyethylene terephthalate (PET), are used in flexible and bendable displays. These substrates enable the fabrication of lightweight, thin, and flexible Micro LED displays suitable for wearable devices, curved displays, and other applications requiring flexibility.
- Metal Foils: Metal foils, such as copper or aluminum foils, can be used as flexible substrates for Micro LED displays. Metal foils offer good electrical conductivity and mechanical flexibility, making them suitable for applications requiring bendable or conformable displays.
- Ceramics: Ceramic substrates, such as aluminum oxide (อัล 2 โอ 3) หรืออลูมิเนียมไนไตรด์ (อัลเอ็น), offer excellent thermal conductivity and mechanical strength, making them suitable for high-power applications where heat dissipation is critical.
The choice of substrate base material depends on various factors such as thermal management requirements, mechanical flexibility, optical properties, and cost considerations. Each material has its advantages and limitations, and the selection of the substrate material is crucial for achieving the desired performance and reliability of Micro LED displays.
Which company makes Micro LED Substrates?
ปัจจุบัน, many companies are developing and manufacturing Micro LED substrates, with some well-known companies including Samsung, LG, BOE Technology, Intel, Sony, and Taiwan’s PlayNitride, among others. These companies have rich experience and technological capabilities in the research, development, and application of Micro LED technology.
In our company, we are also committed to the production of Micro LED substrates. As a company specializing in advanced display technologies, we have advanced process technology and extensive manufacturing experience to meet the demand for high-performance Micro LED substrates.
Our production process covers the entire process from substrate preparation to Micro LED integration. We use advanced materials and equipment to ensure the flatness, conductivity, การจัดการความร้อน, and mechanical stability of the substrates. Our engineering team has extensive experience and can customize Micro LED substrates of different specifications and sizes according to customer requirements.
In terms of quality control, we strictly adhere to the ISO quality management system and implement a series of inspection and testing measures to ensure the quality and reliability of each production step. Our products undergo rigorous testing and validation to ensure compliance with customer requirements and industry standards.
Our company is committed to providing customers with high-quality, high-performance Micro LED substrates, providing a reliable foundation for display devices in various application fields. We continuously innovate and improve our production processes to meet market demands and provide customers with the best solutions.
คืออะไร 7 คุณภาพของการบริการลูกค้าที่ดี?
Seven qualities of good customer service include:
- ความเห็นอกเห็นใจ: Empathizing with customers involves understanding their needs, เกี่ยว ข้อง กับ, and emotions. Good customer service representatives listen actively, show genuine concern, and strive to put themselves in the customer’s shoes to provide effective assistance.
- ความอดทน: Patience is essential in customer service, especially when dealing with frustrated or confused customers. Good customer service representatives remain calm, composed, and attentive, even in challenging situations, and take the time to address customer concerns thoroughly.
- ทักษะการสื่อสาร: Effective communication is key to providing good customer service. Customer service representatives should communicate clearly, courteously, and professionally, whether in person, over the phone, or through written correspondence. They should be able to convey information accurately and understand the customer’s perspective.
- Product Knowledge: Good customer service representatives have a deep understanding of the products or services offered by the company. They should be knowledgeable about features, specifications, pricing, and other relevant information to provide accurate answers to customer inquiries and offer helpful recommendations.
- ความสามารถในการแก้ปัญหา: Good customer service involves resolving customer issues and complaints efficiently and effectively. Customer service representatives should be resourceful, proactive, and creative in finding solutions to customer problems, and they should follow through to ensure that issues are fully resolved.
- มือ อาชีพ: Professionalism is essential in all interactions with customers. Good customer service representatives maintain a positive attitude, exhibit professionalism in their demeanor and appearance, and adhere to company policies and procedures. They strive to build trust and credibility with customers through their actions and behavior.
- ความสามารถในการปรับตัว: Customer service representatives should be adaptable and flexible in responding to diverse customer needs and preferences. They should be able to adjust their approach based on the specific situation and the individual preferences of each customer. Adaptability allows them to provide personalized service and ensure customer satisfaction.
โดยรวบรวมคุณสมบัติเหล่านี้, companies can deliver exceptional customer service experiences that foster loyalty, satisfaction, and positive brand reputation.
คําถามที่พบบ่อย
What is a Micro LED substrate?
A Micro LED substrate is the foundation upon which Micro LEDs are fabricated or integrated. It provides mechanical support, electrical connectivity, and thermal management for the individual Micro LEDs.
What materials are commonly used for Micro LED substrates?
Common materials for Micro LED substrates include silicon, glass, flexible polymers like polyimide, and ceramic materials like aluminum oxide or aluminum nitride.
What are the advantages of Micro LED substrates?
Micro LED substrates enable the creation of high-resolution displays with exceptional brightness, energy efficiency, and color performance. They offer flexibility in design and can be customized for various applications.
How are Micro LED substrates manufactured?
The manufacturing process for Micro LED substrates involves steps such as substrate preparation, thin-film deposition, ลวดลาย, active component integration (Micro LED placement), encapsulation, and testing for quality control.
What are the key considerations in Micro LED substrate design?
Key considerations in Micro LED substrate design include pixel density and size, substrate material selection, uniformity and alignment of Micro LEDs, electrical connectivity, การจัดการความร้อน, mechanical durability, process compatibility, and encapsulation for protection.
What companies produce Micro LED substrates?
Companies involved in the production of Micro LED substrates include industry leaders such as Samsung, LG, BOE Technology, Intel, Sony, PlayNitride, and others.
What are the cost factors associated with Micro LED substrates?
The cost of Micro LED substrates depends on factors such as substrate size, complexity of design, วัสดุที่ใช้, กระบวนการผลิต, and production volume. โดยทั่วไป, Micro LED substrates are relatively expensive compared to traditional LED or LCD substrates due to the advanced technology involved.