Buried Cavity PCBs Manufacturer
Buried Cavity PCBs Manufacturer,Buried cavity PCBs are advanced printed circuit boards that incorporate recessed areas within the substrate for various purposes. These cavities can be used for embedding components, creating isolated spaces for sensitive circuitry, or enhancing thermal management by allowing airflow or heat dissipation. This design reduces the overall thickness and weight of the PCB while improving its structural integrity and electrical performance. Buried cavity PCBs are crucial in aerospace, ยาน ยนต์, and telecommunications industries where compactness, ความน่าเชื่อถือ, and efficient heat management are paramount. They enable the integration of complex functionalities in smaller form factors, supporting innovation in modern electronic devices.
What is a Buried Cavity PCB?
A Buried Cavity PCB refers to a type of printed circuit board (PCB) design where specific areas of the PCB are hollowed out or “buried” to accommodate components or other structures within the board itself. This design technique allows for more compact and efficient PCB layouts by integrating components into the board’s structure rather than just on its surface.
In a Buried Cavity PCB, the cavities are created by removing portions of the PCB layers during the manufacturing process. These cavities can be used for various purposes such as housing sensitive components, reducing electromagnetic interference (อีเอ็มไอ), improving thermal management by providing space for heat sinks or thermal pads, or simply for reducing the overall size of the PCB.
The advantages of using Buried Cavity PCBs include enhanced reliability due to better protection of components, improved signal integrity by minimizing signal loss and noise, and increased design flexibility for complex electronic systems. อย่างไรก็ตาม, manufacturing Buried Cavity PCBs can be more challenging and expensive compared to traditional PCB designs due to the additional steps involved in creating the cavities and ensuring the integrity of the board.
ทั้งหมด, Buried Cavity PCBs are favored in applications where space is at a premium, and where the benefits of improved performance and reliability outweigh the increased manufacturing complexity and cost.
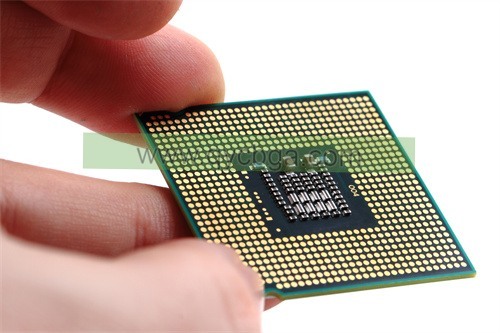
Buried Cavity PCBs Manufacturer
What are Buried Cavity PCB Design Guidelines?
Designing Buried Cavity PCBs requires careful consideration of several guidelines to ensure the integrity, ความน่าเชื่อถือ, and functionality of the board. Here are some key guidelines to follow:
- Component Placement and Orientation: Place components strategically around the cavity to optimize space and ensure proper functionality. Consider the thermal implications of component placement near cavities that may affect heat dissipation.
- Cavity Size and Depth: Determine the size and depth of cavities based on the components or structures they will house. Ensure that cavities are adequately sized to accommodate components without compromising the structural integrity of the PCB.
- การเลือกวัสดุ: Choose PCB materials that can withstand the manufacturing process of creating cavities, such as materials with good mechanical strength and dimensional stability.
- การออกแบบเลเยอร์ Stackup:Plan the layer stackup carefully to accommodate the cavities while maintaining signal integrity and minimizing electromagnetic interference (อีเอ็มไอ). Consider using dedicated ground or power planes around cavities to manage EMI effectively.
- Cavity Wall Thickness: Maintain sufficient wall thickness around cavities to provide mechanical support and prevent structural weaknesses. The thickness should be adequate to withstand mechanical stresses during handling and operation.
- Cavity Plating and Surface Finish: Ensure that cavities are properly plated and finished to maintain electrical conductivity and prevent oxidation. Use suitable surface finishes such as ENIG (นิกเกิลแช่ทองแบบไม่ใช้ไฟฟ้า) or HASL (การปรับระดับบัดกรีลมร้อน) depending on the application requirements.
- ข้อควรพิจารณาเกี่ยวกับความสามารถในการผลิต: Discuss with PCB manufacturers early in the design phase to understand their capabilities and limitations in manufacturing Buried Cavity PCBs. Consider factors such as tooling, เจาะ, and layer registration accuracy.
- การจัดการความร้อน: Implement thermal vias or thermal pads around cavities to enhance heat dissipation from components housed within the cavities. Ensure that thermal paths are optimized to maintain component reliability.
- Signal Integrity and EMI Control: Use proper routing techniques and ground plane management to maintain signal integrity and reduce EMI around cavities. Avoid high-speed signal paths crossing over cavities to minimize signal degradation.
- การทดสอบและการตรวจสอบความถูกต้อง: Conduct thorough testing and validation of prototypes to verify the functionality, ความน่าเชื่อถือ, and performance of Buried Cavity PCBs under operational conditions.
โดยปฏิบัติตามแนวทางเหล่านี้, designers can effectively leverage the advantages of Buried Cavity PCBs while mitigating potential challenges associated with their design and manufacturing processes.
What is the Buried Cavity PCB Fabrication Process?
The fabrication process of Buried Cavity PCBs involves several specialized steps to create the hollowed-out areas within the PCB structure. Here’s a detailed outline of the fabrication process:
- Design Preparation: Begin with a comprehensive PCB design that includes specific dimensions and placements for the cavities. Ensure that the design meets all functional and structural requirements, considering component placements, signal integrity, และการจัดการความร้อน.
- การออกแบบเลเยอร์ Stackup: Define the layer stackup based on the number of layers required for the PCB. Determine the placement of inner layers that will contain the cavities, typically using CAD software that supports complex layer arrangements.
- Cavity Definition: Specify the locations and dimensions of the cavities within the PCB layers. This involves defining the areas where material will be removed to create the cavities, which can be done using CNC (Computer Numerical Control) drilling or routing equipment.
- การเลือกวัสดุ: Choose PCB materials suitable for the fabrication of Buried Cavity PCBs. Opt for materials with good mechanical strength, ความเสถียรของมิติ, and compatibility with the manufacturing processes involved in cavity creation.
- การเตรียมชั้น: Begin with the inner layers of the PCB stackup. Prepare these layers by cleaning and applying a bonding material if necessary, which helps in laminating multiple layers together later in the process.
- Cavity Creation: Use precision CNC equipment to remove material from the specified areas within the inner layers to create the cavities. This process requires precise control to ensure that the cavities are accurately formed without damaging adjacent layers or compromising the structural integrity of the PCB.
- เคลือบ: After creating the cavities in the inner layers, laminate all layers together using heat and pressure. This step bonds the inner layers with the outer layers of the PCB stackup, encapsulating the cavities within the finished PCB structure.
- Drilling and Plating: Drill holes for vias and through-hole components as per the PCB design requirements. Ensure that the drilled holes do not intersect with the cavities. Plate the drilled holes to establish electrical connections between different layers and components.
- รูปแบบวงจร: Apply the circuit pattern using processes like etching or deposition to create conductive traces and pads on the outer layers of the PCB. This step completes the electrical connectivity across the entire PCB, including components within the cavities.
- การตกแต่งพื้นผิว: Apply a suitable surface finish such as ENIG (นิกเกิลแช่ทองแบบไม่ใช้ไฟฟ้า) or HASL (การปรับระดับบัดกรีลมร้อน) to protect exposed copper traces and pads, ensuring solderability and corrosion resistance.
- การทดสอบและการตรวจสอบ: Conduct comprehensive testing and inspection of the fabricated PCB to verify functionality, ความต่อเนื่องทางไฟฟ้า, and structural integrity. This includes electrical testing, visual inspection, and possibly functional testing depending on the application.
- Final Assembly: If required, proceed with the final assembly of components onto the PCB using soldering or assembly processes. Ensure that components housed within cavities are securely mounted and thermally managed as per design specifications.
By following these steps meticulously, PCB manufacturers can produce Buried Cavity PCBs that meet stringent quality standards and functional requirements for various advanced electronic applications.
How do you manufacture a Buried Cavity PCB?
Manufacturing a Buried Cavity PCB involves a specialized process to create hollowed-out areas within the PCB structure to house components or facilitate specific design requirements. Here’s a step-by-step outline of the manufacturing process:
- Design Preparation: Begin with a detailed PCB design that includes specifications for cavity locations, dimensions, and layer stackup. Use CAD software to define the cavity areas within the inner layers of the PCB.
- การเลือกวัสดุ: Choose PCB materials suitable for Buried Cavity PCBs, considering factors such as mechanical strength, thermal properties, and compatibility with the manufacturing processes involved in cavity creation.
- การออกแบบเลเยอร์ Stackup: Design the layer stackup based on the number of layers required and the locations of the cavities. Specify the sequence of inner layers that will contain the cavities, ensuring adequate spacing and material properties.
- Cavity Definition: Use CNC (Computer Numerical Control) equipment to precisely remove material from designated areas within the inner layers to create the cavities. This process requires high precision to avoid damage to adjacent layers and ensure the cavities meet design specifications.
- Bonding and Lamination: Prepare the inner layers by cleaning and applying bonding materials as necessary. Laminate the prepared layers together under heat and pressure to form a single PCB structure with cavities encapsulated between the layers.
- Drilling and Plating: Drill holes for vias and through-hole components according to the PCB design. Ensure that drilled holes do not intersect with cavities. Plate the drilled holes to establish electrical connections between layers and components.
- รูปแบบวงจร: Apply the circuit pattern on the outer layers of the PCB using processes such as etching or deposition. Create conductive traces and pads to establish electrical connectivity across the entire PCB, including components within the cavities.
- การตกแต่งพื้นผิว: Apply a suitable surface finish such as ENIG (นิกเกิลแช่ทองแบบไม่ใช้ไฟฟ้า) or HASL (การปรับระดับบัดกรีลมร้อน) to protect exposed copper traces and pads, ensuring solderability and corrosion resistance.
- การทดสอบและการตรวจสอบ: Perform rigorous testing and inspection to verify the functionality, ความต่อเนื่องทางไฟฟ้า, and structural integrity of the Buried Cavity PCB. This includes electrical testing, visual inspection, and potentially functional testing depending on application requirements.
- Component Assembly: If required, proceed with the assembly of components onto the PCB using soldering or assembly processes. Ensure that components housed within cavities are securely mounted and thermally managed according to design specifications.
- การประกันคุณภาพ: Implement quality assurance measures throughout the manufacturing process to ensure compliance with design specifications and industry standards. This includes monitoring process parameters, conducting periodic inspections, and addressing any deviations promptly.
- Documentation and Packaging: Document all manufacturing processes and test results for traceability and quality control purposes. Package the finished Buried Cavity PCBs appropriately for shipment or further assembly stages.
By following these steps systematically and leveraging advanced manufacturing technologies, PCB manufacturers can produce high-quality Buried Cavity PCBs tailored to meet the demands of complex electronic applications.
How much should a Buried Cavity PCB cost?
The cost of a Buried Cavity PCB can vary widely depending on several factors:
- ความซับซ้อนของการออกแบบ: The complexity of the PCB design, รวมถึงจํานวนชั้น, size and number of cavities, and the overall size of the board, directly impacts the cost. More complex designs with intricate cavity layouts will generally be more expensive.
- การเลือกวัสดุ:The choice of PCB materials affects the cost. High-performance materials with specific mechanical or thermal properties required for Buried Cavity PCBs can be more expensive than standard FR4 materials.
- กระบวนการผลิต: The fabrication processes involved in creating Buried Cavity PCBs, such as CNC drilling or routing for cavity creation, lamination under heat and pressure, and precise plating and surface finishing, add to the manufacturing cost.
- Quantities and Batch Size: การประหยัดจากขนาดนําไปใช้ในการผลิต PCB. Larger quantities typically reduce the per-unit cost due to bulk discounts and optimized production setups.
- Additional Features:Any additional features such as special surface finishes (เช่น, เอนิก), specific tolerances, and advanced testing requirements can increase the cost.
- ซัพพลายเออร์และที่ตั้ง: Costs can vary between different PCB manufacturers and regions due to labor costs, ค่าสู้หุ้ย, และสภาวะตลาดในท้องถิ่น.
เป็นการประมาณการคร่าวๆ, Buried Cavity PCBs are generally more expensive than standard PCBs due to their specialized manufacturing processes and material requirements. Prices can range from a few dollars to several hundred dollars per board, ขึ้นอยู่กับปัจจัยข้างต้น. For a precise cost estimate, it’s best to consult with PCB manufacturers or suppliers, providing them with detailed specifications and quantities needed for your project.
What is Buried Cavity PCB base material?
The base material used for Buried Cavity PCBs typically needs to meet specific requirements to support the cavity creation process and ensure the structural integrity and functionality of the board. Here are some common base materials used:
- FR4 (สารหน่วงไฟ 4): This is the most common and widely used base material for PCBs. FR4 is composed of a woven fiberglass cloth impregnated with an epoxy resin binder. It provides good mechanical strength, ความเสถียรของมิติ, and is cost-effective. อย่างไรก็ตาม, for more complex Buried Cavity PCBs, additional reinforcement or specialized variants of FR4 may be required.
- High-Tg FR4: High-Tg (Glass Transition Temperature) FR4 variants are used when higher thermal stability is needed. These materials have a higher Tg value, typically around 170°C or higher, which helps in maintaining mechanical and electrical properties at elevated temperatures during soldering or operation.
- Rogers Materials: Some Buried Cavity PCBs may require specialized laminates from Rogers Corporation or similar manufacturers. These materials offer specific dielectric properties, การนําความร้อน, and dimensional stability suitable for high-frequency applications or where stringent performance requirements must be met.
- โพลีอิไมด์:For applications requiring flexibility or high-temperature resistance, polyimide-based materials (such as Kapton) may be used. These materials can withstand extreme temperatures and have good chemical resistance, making them suitable for harsh environments or flexible circuit applications.
- Metal Core (MCPCB): In cases where thermal management is critical, Metal Core PCBs (MCPCBs) with aluminum or copper cores may be used as the base material. These provide efficient heat dissipation, which is beneficial when components within the cavities generate significant heat.
The choice of base material for Buried Cavity PCBs depends on factors such as thermal requirements, ความแข็งแรงเชิงกล, electrical properties, and the specific manufacturing processes involved in creating the cavities. Designers and manufacturers select the most suitable base material based on the application’s needs and performance criteria.
Which company makes Buried Cavity PCBs?
There are many companies that manufacture Buried Cavity PCBs, primarily specialized PCB manufacturers and suppliers. These companies typically have advanced manufacturing equipment and technologies to meet the design and manufacturing needs of complex electronic systems.
Some well-known PCB manufacturing companies capable of producing Buried Cavity PCBs include TPC from Taiwan, Nippon Mektron, Ltd. from Japan, and WUS Group from the United States. These companies ensure PCB designs meet specifications and provide high-quality manufacturing services through their professional teams and advanced manufacturing processes.
ที่บริษัทของเรา, we also have the capability to manufacture and supply Buried Cavity PCBs. We possess advanced PCB manufacturing equipment and a skilled technical team capable of handling complex layer stack designs and special cavity structures. Our manufacturing process includes:
- Professional Design Support: Our engineering team collaborates closely with customers to provide tailored design support, ensuring PCB designs meet technical and performance requirements. We handle intricate layer stackups and cavity designs to optimize PCB space utilization and functional layout.
- Advanced Manufacturing Equipment: We invest in advanced CNC drilling and routing equipment to precisely control and create internal cavity structures within PCBs. Through precise manufacturing processes, we ensure accuracy and consistency of cavities while maintaining PCB structural integrity and reliability.
- Strict Quality Control: We implement rigorous quality control processes, conducting precise inspections and testing at every stage from material procurement to manufacturing. This ensures that every produced Buried Cavity PCB meets high-quality standards and customer expectations.
- Customized Solutions: We offer customized Buried Cavity PCB solutions tailored to specific customer requirements, including material selection, layer stackup, cavity design, and surface finishes. We are committed to providing flexible solutions to meet technical and performance requirements across various application fields.
Therefore, if you need Buried Cavity PCB manufacturing or have any PCB manufacturing requirements, our company has extensive experience and expertise to provide customized solutions and high-quality manufacturing services. We look forward to collaborating with you to elevate your electronic products to new heights.
What are the qualities of good customer service?
Good customer service is characterized by several key qualities that contribute to positive interactions and relationships between a business and its customers. Here are the qualities of good customer service:
- Excellent Communication Skills: Effective communication is crucial. Customer service representatives should listen actively to understand customer needs and concerns, and respond clearly and empathetically.
- Empathy and Understanding:Showing empathy demonstrates care and understanding towards customers’ issues or challenges. It involves putting oneself in the customer’s shoes and addressing their concerns with sensitivity.
- Patience and Attentiveness: Dealing with customer queries or complaints requires patience. Attentiveness ensures that customers feel heard and valued throughout their interaction with customer service.
- Knowledge and Competence: Good customer service involves having a deep knowledge of the company’s products or services. Being competent enables representatives to provide accurate information and effective solutions promptly.
- ทักษะการแก้ปัญหา: Resolving customer issues effectively requires problem-solving skills. Customer service should be proactive in finding solutions and addressing customer concerns promptly.
- มือ อาชีพ: Maintaining professionalism creates a positive impression. It involves being courteous, สุภาพ, and maintaining a positive attitude even during challenging situations.
- ตอบ สนอง: Customers appreciate prompt responses. Good customer service ensures timely follow-up and resolution of customer inquiries or problems.
- Personalization: Tailoring interactions to individual customer needs makes them feel valued. This includes addressing customers by name, acknowledging their preferences, and offering personalized solutions where possible.
- ความสอดคล้อง:Consistency in service delivery builds trust and reliability. Customers should receive consistent service quality regardless of the channel or representative they interact with.
- Feedback Handling: Listening to customer feedback and using it constructively to improve services demonstrates a commitment to continuous improvement and customer satisfaction.
ทั้งหมด, good customer service is about creating positive experiences for customers by addressing their needs effectively, building trust and loyalty, and ensuring they feel valued throughout their interactions with the company.
คําถามที่พบบ่อย (คําถามที่พบบ่อย)
What are typical applications of Buried Cavity PCBs?
Buried Cavity PCBs are used in applications where space savings, enhanced reliability, and improved performance are critical. Common applications include telecommunications equipment, อุปกรณ์ทางการแพทย์, aerospace systems, and high-density electronic products.
How are Buried Cavity PCBs manufactured?
The manufacturing process involves creating cavities within the PCB structure using CNC drilling or routing techniques. These cavities are then encapsulated within the layers of the PCB during the lamination process. Precise planning of layer stackup, การเลือกวัสดุ, and cavity design is essential for successful fabrication.
What materials are used for Buried Cavity PCBs?
Common materials include standard FR4 (สารหน่วงไฟ 4), high-Tg FR4 for higher temperature stability, specialized laminates from companies like Rogers Corporation for specific performance requirements, and sometimes metal-core materials for enhanced thermal management.
What are the challenges of manufacturing Buried Cavity PCBs?
Challenges include the complexity of design and manufacturing processes, increased cost compared to standard PCBs due to specialized techniques, and ensuring structural integrity and reliability with cavities.
How do Buried Cavity PCBs impact design considerations?
Designers must carefully plan component placement, routing of traces around cavities to maintain signal integrity, and manage thermal considerations effectively. Collaboration between PCB designers and manufacturers is crucial to optimize design for manufacturability.
What are the cost considerations for Buried Cavity PCBs?
The cost varies based on factors like design complexity, วัสดุที่ใช้, manufacturing processes involved, and quantities ordered. Buried Cavity PCBs generally cost more than standard PCBs due to specialized manufacturing techniques and materials.
Can Buried Cavity PCBs be repaired or modified?
Repairing or modifying Buried Cavity PCBs can be challenging due to the internal cavities. Depending on the nature of the repair or modification, it may require specialized techniques and equipment to access and work within the cavities.
What should I consider when choosing a manufacturer for Buried Cavity PCBs?
Look for a manufacturer with experience in producing complex PCBs, including Buried Cavity designs. Consider their capabilities in design support, manufacturing technology, quality control measures, and their ability to meet your specific requirements and standards.