Semiconductor Glass Substrates Manufacturer
Semiconductor Glass Substrates Manufacturer,Semiconductor Glass Substrates are specialized materials used in the fabrication of semiconductor devices. These substrates are made from glass-ceramic materials engineered to provide high thermal stability, low coefficient of thermal expansion (CTE), and excellent electrical insulation properties. Semiconductor Glass Substrates support the integration of semiconductor components with precise microstructures and interconnects, enabling miniaturization and improved performance in electronic devices. They are crucial in applications requiring high reliability, such as microelectronics, optoelectronics, and sensor technology. Semiconductor Glass Substrates offer superior dimensional stability and thermal management, making them suitable for advanced semiconductor packaging and high-density interconnect applications in modern electronic systems.
What is a Semiconductor Glass Substrate?
A Semiconductor Glass Substrate refers to a specialized material used as a base for semiconductor devices like integrated circuits (ICs). It’s typically made from high-purity glass that undergoes precise manufacturing processes to achieve specific properties like thermal stability, electrical insulation, and mechanical strength. These substrates play a crucial role in supporting and connecting semiconductor components within electronic devices, ensuring reliable performance and longevity. Semiconductor glass substrates are favored for their uniformity, dimensional stability, and the ability to accommodate intricate circuit patterns through advanced manufacturing techniques. They are essential in modern electronics, enabling the miniaturization and efficiency improvements seen in various semiconductor applications, from consumer electronics to telecommunications and beyond.
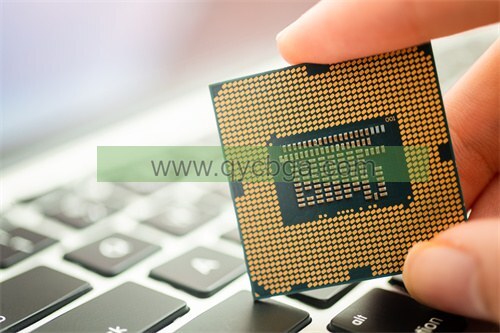
Semiconductor Glass Substrates Manufacturer
What are the Semiconductor Glass Substrate Design Guidelines?
Design guidelines for Semiconductor Glass Substrates typically include several key aspects to ensure optimal performance and manufacturability:
- Material Selection: Choose a glass substrate with appropriate thermal expansion properties, electrical insulation characteristics, and mechanical strength suitable for the intended application.
- Dimensional Tolerances: Specify precise dimensions and tolerances for the substrate to ensure compatibility with assembly processes and device requirements.
- Surface Finish: Define surface finish requirements to facilitate proper adhesion of semiconductor materials and to minimize defects that could affect performance.
- Circuit Layout: Design the circuit layout considering the electrical routing, signal integrity, and thermal management requirements of the semiconductor device.
- Via and Hole Design: Optimize the design of vias and holes for interconnections to ensure reliable electrical connectivity and to accommodate specific manufacturing processes.
- Alignment and Registration: Specify alignment features and registration marks to ensure accurate assembly and alignment during the manufacturing process.
- Testing and Inspection: Plan for testing and inspection methods to verify substrate quality and performance before integrating semiconductor components.
- Environmental Considerations: Consider environmental factors such as temperature extremes, humidity, and mechanical stress that may impact substrate reliability over time.
These guidelines help ensure that Semiconductor Glass Substrates meet the stringent requirements of semiconductor manufacturing, leading to reliable and high-performance electronic devices.
What is the Semiconductor Glass Substrate Fabrication Process?
The fabrication process of Semiconductor Glass Substrates involves several key steps to achieve the required material properties and dimensions:
- Material Selection: High-purity glass with suitable thermal expansion coefficients and electrical insulation properties is chosen based on the specific application requirements.
- Cleaning and Preparation: The glass substrates undergo thorough cleaning to remove contaminants and ensure a pristine surface for subsequent processing.
- Etching:Etching processes may be used to define circuit patterns and vias on the glass substrate. This can involve photolithography techniques similar to those used in semiconductor wafer fabrication.
- Deposition: Thin film deposition techniques such as sputtering or evaporation are employed to deposit conductive or insulating layers onto the substrate. These layers form the basis for circuitry and interconnections.
- Laser Machining: Laser cutting or machining processes may be used to create precise features such as vias, holes, or edge profiles in the glass substrate.
- Surface Treatment: Surface treatments such as polishing or coating with protective layers may be applied to enhance electrical properties, ensure adhesion of subsequent layers, or provide mechanical stability.
- Quality Control:Throughout the fabrication process, stringent quality control measures are implemented to verify dimensional accuracy, surface quality, and material properties.
- Final Inspection: Finished Semiconductor Glass Substrates undergo final inspection and testing to ensure they meet the specified design requirements and performance standards.
The fabrication of Semiconductor Glass Substrates requires precision manufacturing techniques to achieve uniformity, reliability, and compatibility with semiconductor device integration processes. Each step in the process contributes to the substrate’s ability to support and enhance the performance of electronic components and devices.
How do you manufacture Semiconductor Glass Substrates?
Manufacturing Semiconductor Glass Substrates involves a series of specialized processes to create high-quality substrates suitable for semiconductor device integration. Here’s a general overview of the manufacturing steps:
- Material Selection: High-purity glass is chosen based on its thermal expansion coefficient, electrical insulation properties, and mechanical strength, tailored to the specific requirements of semiconductor applications.
- Cleaning and Preparation: The glass sheets undergo thorough cleaning to remove contaminants and ensure a clean surface for subsequent processing steps.
- Etching: Photolithography techniques are used to define circuit patterns and features on the glass substrate. This involves applying a photoresist, exposing it to UV light through a mask with the desired pattern, developing the resist to reveal the pattern, and then etching the glass using chemical or plasma processes.
- Deposition: Thin film deposition techniques such as sputtering or evaporation are employed to deposit layers of conductive and insulating materials onto the substrate. These layers form the circuitry and interconnects necessary for semiconductor device functionality.
- Laser Processing: Laser cutting or machining may be used to create precise features such as vias, holes, or edge profiles in the glass substrate, ensuring accurate alignment and connectivity in the final semiconductor assembly.
- Surface Treatment: Surface treatments such as polishing or coating with protective layers may be applied to enhance electrical properties, improve adhesion of subsequent layers, or provide mechanical stability.
- Quality Assurance: Throughout the manufacturing process, rigorous quality control measures are implemented to verify dimensional accuracy, surface quality, and material integrity. This includes inspection of critical dimensions, electrical conductivity, and adherence to design specifications.
- Final Testing: Finished Semiconductor Glass Substrates undergo final testing and inspection to ensure they meet performance requirements and reliability standards before being packaged and shipped for semiconductor device integration.
Manufacturing Semiconductor Glass Substrates requires advanced manufacturing technologies and precise control over each step to produce substrates that can support the high-performance demands of modern semiconductor devices. The process integrates aspects of traditional glass manufacturing with semiconductor fabrication techniques to achieve the required material properties and dimensional accuracy.
How much should Semiconductor Glass Substrates cost?
The cost of Semiconductor Glass Substrates can vary widely depending on several factors, including the specifications, manufacturing complexity, volume of production, and supplier. Here’s a general breakdown of factors that influence the cost:
- Material Quality and Type: Higher purity and specialty glass types designed for specific semiconductor applications can be more expensive.
- Manufacturing Complexity: Processes like photolithography, thin film deposition, and laser machining add to the cost. The more complex and precise the features, the higher the cost.
- Thickness and Size: Larger and thicker substrates generally cost more due to the increased material usage and potential for more complex handling and processing requirements.
- Surface Treatments and Coatings: Additional treatments, such as polishing, coating, or specialized surface modifications, can increase costs.
- Volume of Production: Higher volumes typically reduce the per-unit cost due to economies of scale. Small batch or custom orders can be significantly more expensive.
- Quality Control and Testing: Rigorous quality control and testing procedures, which are essential for ensuring reliability and performance, contribute to the overall cost.
As a rough estimate, the cost of semiconductor glass substrates can range from a few dollars per unit for simple, small-scale substrates to several hundred dollars or more for larger, highly specialized substrates with complex features. For high-volume production, the cost per unit can be lower, while prototypes and low-volume production runs can be considerably more expensive.
To get precise pricing, it’s best to request quotes from suppliers or manufacturers, providing them with detailed specifications and requirements. This will allow for a more accurate cost assessment based on the specific needs of your application.
What is Semiconductor Glass Substrate base material?
Semiconductor Glass Substrates are typically made from high-purity glasses that are carefully selected based on their thermal, mechanical, and electrical properties. The base material used for Semiconductor Glass Substrates often includes:
- Borosilicate Glass: This type of glass is known for its low coefficient of thermal expansion, making it less prone to thermal stress and cracking during temperature changes.
- Aluminosilicate Glass: Offering improved mechanical strength and durability compared to borosilicate glass, aluminosilicate glass is used in applications requiring higher reliability and resistance to mechanical stress.
- Quartz Glass (Fused Silica): Quartz glass is used for its excellent optical and thermal properties, along with high purity and resistance to high temperatures. It’s often used in specialized semiconductor applications requiring extreme thermal stability.
- Soda-Lime Glass: While less common for semiconductor substrates due to its higher coefficient of thermal expansion and lower thermal stability, soda-lime glass may be used in less demanding applications or for cost-sensitive designs.
The choice of base material depends on the specific requirements of the semiconductor application, including thermal management, electrical insulation, mechanical stability, and compatibility with semiconductor manufacturing processes. Each type of glass offers different advantages in terms of performance and cost, allowing manufacturers to select the most suitable material for their particular application needs.
Which company makes Semiconductor Glass Substrates?
Semiconductor Glass Substrates are manufactured by several companies, including well-known manufacturers such as Corning, SCHOTT, AGC, Hoya, and others. These companies have extensive experience and technological expertise in the field of semiconductor glass substrates, offering a variety of customized solutions to meet the needs of different semiconductor devices.
In this field, the manufacturing process of glass substrates requires highly precise process control and quality management to ensure dimensional accuracy, surface smoothness, and material purity that meet strict semiconductor manufacturing requirements. High-end glass substrates typically utilize advanced technologies such as photolithography, thin film deposition, laser processing, and others to achieve complex circuit patterns and fine structural requirements.
Our company is also capable of producing Semiconductor Glass Substrates and is committed to providing high-quality customized solutions. We have advanced production equipment and a skilled technical team capable of developing and optimizing production processes according to specific customer requirements, ensuring product stability and reliability. Our manufacturing processes adhere strictly to international standards and industry best practices, supported by rigorous quality control measures to guarantee product consistency and quality.
Our Semiconductor Glass Substrates find wide application in various semiconductor devices, including integrated circuits (ICs), sensors, optoelectronic devices, and more. Whether for small-batch customization or large-scale industrial production, we offer flexible solutions and dedicated technical support to meet evolving technological and market demands.
Through continuous technological innovation and quality improvement, we strive to be a trusted partner in the field of semiconductor glass substrates, delivering the highest quality products and services to our customers.
What are the 7 qualities of good customer service?
Good customer service typically encompasses several key qualities that contribute to a positive customer experience. Here are seven important qualities:
- Responsiveness: Good customer service involves promptly responding to customer inquiries, requests, or issues. This shows customers that their concerns are valued and that their needs are being addressed in a timely manner.
- Empathy: Empathy is crucial in understanding and acknowledging the customer’s perspective and feelings. It involves listening actively, showing compassion, and demonstrating an understanding of the customer’s situation or problem.
- Clarity: Providing clear and concise information is essential for effective communication in customer service. Clear communication helps prevent misunderstandings and ensures that customers receive accurate and helpful information.
- Patience: Dealing with customer issues or questions may require patience, especially when customers are frustrated or have difficulty explaining their concerns. Patient customer service representatives remain calm and composed, even in challenging situations.
- Professionalism: Maintaining professionalism in interactions with customers reflects positively on the company’s image. Professionalism includes being courteous, respectful, and maintaining a positive attitude throughout the customer interaction.
- Knowledgeability:Customer service representatives should possess sufficient knowledge about the company’s products or services to provide accurate information and assistance. Knowledgeable staff can offer solutions and guidance effectively, enhancing customer satisfaction.
- Problem-Solving Skills: Effective customer service involves the ability to identify and resolve customer problems or issues efficiently. Problem-solving skills enable representatives to address customer concerns effectively and find appropriate solutions.
By focusing on these qualities, organizations can cultivate a customer-centric approach that builds trust, loyalty, and satisfaction among their customer base.
FAQs
What are Semiconductor Glass Substrates used for?
Semiconductor Glass Substrates are used as a base material for manufacturing semiconductor devices such as integrated circuits (ICs), sensors, and optoelectronic components. They provide a stable platform for building intricate circuitry and supporting electronic components.
What are the advantages of Semiconductor Glass Substrates?
Semiconductor Glass Substrates offer advantages such as high thermal stability, excellent electrical insulation properties, uniformity in material composition, and compatibility with advanced manufacturing processes like photolithography and thin film deposition.
What types of glass are used in Semiconductor Glass Substrates?
Common types of glass used include borosilicate glass, aluminosilicate glass, quartz glass (fused silica), and specialty glasses tailored for specific semiconductor applications. Each type offers different thermal, mechanical, and electrical properties.
How are Semiconductor Glass Substrates manufactured?
The manufacturing process involves steps such as glass selection, cleaning, etching to define circuit patterns, deposition of thin films for circuitry, laser machining for vias and holes, surface treatments, and rigorous quality control to ensure dimensional accuracy and material integrity.
What are the considerations for selecting Semiconductor Glass Substrates?
Selection factors include thermal expansion coefficient, electrical insulation capabilities, mechanical strength, surface smoothness, compatibility with manufacturing processes, and specific requirements of the semiconductor application.
Can Semiconductor Glass Substrates be customized?
Yes, Semiconductor Glass Substrates can be customized to meet specific size, shape, thickness, and performance requirements. Customization may involve tailored surface treatments, coatings, or unique circuit designs depending on the application needs.
Where can I purchase Semiconductor Glass Substrates?
Semiconductor Glass Substrates are available from specialized manufacturers and suppliers that focus on semiconductor materials. Companies like Corning, SCHOTT, AGC, and Hoya are known for producing high-quality semiconductor glass substrates.