Radar HF Substrate Manufacturer
Radar HF Substrate Manufacturer,Radar HF substrates are specialized materials crucial for constructing high-frequency radar systems, enabling the transmission and reception of radio waves in the HF (High Frequency) band, typically ranging from 3 MHz to 30 MHz. These substrates boast specific properties tailored to the demands of radar applications, including high dielectric constants to support efficient signal propagation, low dielectric losses to minimize signal attenuation, and excellent thermal conductivity for effective heat dissipation. Manufactured through precise processes like material deposition, металлизация, and surface finishing, Radar HF substrates undergo rigorous quality control measures to ensure reliability and performance consistency. Their applications span various industries, including military and defense for surveillance and reconnaissance, weather monitoring for accurate meteorological data collection, and satellite communication systems for long-range transmission. Selecting the right Radar HF substrate involves considering factors such as operating frequency range, signal integrity requirements, and compatibility with other radar components, emphasizing the critical role these substrates play in the functionality and reliability of radar systems.
What is Radar HF substrate?
The term “Radar HF substrate” doesn’t appear to directly refer to a widely recognized specific material or technology in the field of radar systems as of my last update. Однако, we can break down the components of the phrase to speculate on what it might involve:
- Radar: This refers to a system used for detecting, ranging (determining the distance of), and mapping objects such as aircraft, ships, and rain. Radar systems emit radio waves and analyze the echoes returned after these waves bounce off objects.
- HF: Typically stands for “High Frequency,” which in the context of radio communications refers to the frequency band ranging from 3 MHz to 30 MHz. HF radar systems are particularly good for over-the-horizon radar applications due to their ability to reflect off the ionosphere and cover long distances.
- Substrate: In electronic and communication devices, a substrate often refers to the underlying material or base layer that supports circuits or other electronic components. Substrates are crucial in determining the performance and reliability of electronic devices and circuits.
Putting these together, “Radar HF substrate” could hypothetically refer to the material base used in constructing high-frequency radar systems. Such substrates would need to have specific electrical and mechanical properties to support the efficient operation of HF radar, including stability, low loss characteristics at high frequencies, and durability under various environmental conditions.
If you’re dealing with a specific context where this term was used, such as a technical document or a specific technology sector, additional details from that context would be necessary to provide a more precise explanation.
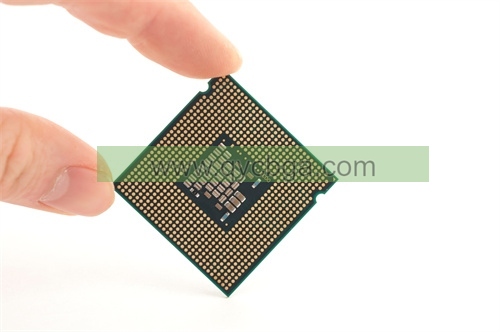
Radar HF Substrate Manufacturer
What are the Radar HF substrate Design Guidelines?
Design guidelines for Radar HF substrates would typically focus on ensuring the optimal performance of the radar system at high frequencies. While specific guidelines may vary depending on the application, here are some general considerations that might be included:
- Dielectric Constant (ε_r): The dielectric constant of the substrate material is crucial for determining the propagation velocity of electromagnetic waves through the substrate. At high frequencies, maintaining a consistent dielectric constant is essential to minimize signal distortion and phase errors.
- Loss Tangent (tan δ): Loss tangent quantifies the amount of energy lost as heat within the substrate material. For high-frequency radar applications, substrates with low loss tangents are preferred to minimize signal attenuation and maximize the efficiency of the radar system.
- Substrate Thickness: The thickness of the substrate can affect the impedance matching between components and transmission lines. Design guidelines may specify the optimal substrate thickness based on the desired operating frequency and the characteristics of other components in the radar system.
- Материал основания: Different substrate materials offer varying electrical and mechanical properties. Common materials used for high-frequency radar substrates include ceramic materials (such as alumina), specialized laminates (например., Rogers Corporation’s RO4000 series), and semiconductor materials (например., gallium arsenide). The choice of substrate material depends on factors such as cost, performance requirements, and manufacturing capabilities.
- Temperature Stability:Radar systems may be deployed in harsh environments with wide temperature fluctuations. Design guidelines may specify substrate materials with excellent temperature stability to ensure consistent performance across operating conditions.
- Manufacturing Tolerances: Tolerances for substrate thickness, диэлектрическая проницаемость, and other parameters should be defined to ensure consistency and reliability in mass production. Design guidelines may provide recommendations for manufacturing processes and quality control measures to meet these tolerances.
- Signal Integrity and Crosstalk: High-frequency radar systems require careful design to minimize signal reflections, crosstalk between transmission lines, and electromagnetic interference. Design guidelines may include recommendations for substrate layout, grounding techniques, and shielding to optimize signal integrity and reduce interference.
These are just a few examples of the design guidelines that might be considered when designing Radar HF substrates. The specific requirements will depend on the application, performance goals, and constraints of the radar system.
What is the Radar HF substrate Fabrication Process?
The fabrication process for Radar HF substrates involves several steps to create the substrate material with the desired electrical and mechanical properties. While specific processes can vary depending on the substrate material and manufacturing technology, here is a generalized overview of the fabrication process:
- Выбор материала: The process begins with selecting a suitable substrate material based on the desired electrical characteristics, mechanical properties, and environmental considerations. Common materials used for Radar HF substrates include ceramics (например., глинозем), specialized laminates (например., PTFE-based materials), and semiconductor materials (например., gallium arsenide).
- Preparation of Substrate Material: The selected substrate material is prepared for further processing. This may involve cutting the material into appropriate sizes or shapes to match the specifications of the radar system.
- Очистка и обработка поверхностей:The substrate material undergoes cleaning and surface treatment to remove any contaminants and prepare the surface for subsequent processing steps. Surface treatment techniques may include chemical cleaning, plasma treatment, or mechanical abrasion.
- Печатная плата (Печатная плата) Fabrication (если применимо): If the Radar HF substrate includes printed circuitry, such as transmission lines or antenna elements, PCB fabrication processes are employed. This typically involves photolithography, офорт, and plating steps to create the desired circuit patterns on the substrate surface.
- Осаждение диэлектрического слоя:In cases where the substrate requires a dielectric layer with specific electrical properties, such as a low dielectric constant or controlled thickness, dielectric materials are deposited onto the substrate surface. Deposition techniques may include chemical vapor deposition (ССЗ), physical vapor deposition (PVD), or spin coating.
- Curing and Annealing: The deposited dielectric layers may undergo curing or annealing processes to enhance their mechanical strength, adhesion to the substrate, and electrical properties. Curing is typically achieved through heat treatment or exposure to ultraviolet (UV) light.
- Metalization: Metal layers are deposited onto the substrate surface to create conductive traces, Колодки, and vias for interconnecting components and forming RF transmission lines. Common metalization techniques include sputtering, evaporation, or electroplating.
- Etching and Patterning: Metal layers are selectively etched to define the desired circuit patterns and features on the substrate surface. Photolithography, combined with chemical or plasma etching, is often used to achieve high precision in patterning.
- Обработка поверхности: The substrate surface may undergo surface finishing processes to improve solderability, corrosion resistance, and overall reliability. Common surface finishes include immersion gold, ХАСЛ (Выравнивание припоя горячим воздухом), ЭНИГ (Химический никель иммерсионное золото), and OSP (Органические консерванты для паяния).
- Quality Control and Testing: На протяжении всего процесса изготовления, quality control measures are implemented to ensure that the substrate material meets the specified requirements for electrical performance, Точность размеров, и надежность. Testing techniques such as impedance measurements, dielectric constant characterization, and visual inspection are employed to validate the quality of the fabricated substrates.
- Packaging and Assembly: После изготовления, the Radar HF substrates may be packaged and assembled into complete radar systems or integrated into larger electronic assemblies according to the specific application requirements.
Полный, the fabrication process for Radar HF substrates involves a combination of material preparation, deposition, patterning, and testing steps to produce substrates with the desired electrical characteristics and performance for high-frequency radar applications.
How do you manufacture a Radar HF substrate?
Manufacturing Radar HF substrates involves a series of steps to create the specialized material that forms the foundation of radar systems operating at high frequencies. Here’s a generalized overview of the manufacturing process:
- Выбор материала: Radar HF substrates can be made from various materials, including ceramics, specialized laminates, and semiconductor materials. The choice of material depends on factors such as desired electrical properties, механическая прочность, and cost. Common materials include alumina, PTFE-based laminates, and gallium arsenide.
- Preparation of Substrate Material: The selected material is prepared for further processing. This may involve cutting the material into sheets or blocks of appropriate sizes using techniques such as sawing or laser cutting.
- Очистка и обработка поверхностей: The substrate material undergoes cleaning and surface treatment to remove contaminants and prepare the surface for subsequent processing steps. Surface treatment may involve chemical cleaning, plasma treatment, or mechanical polishing.
- Deposition of Dielectric Layers (if necessary): Depending on the substrate material and design requirements, dielectric layers with specific electrical properties may need to be deposited onto the substrate surface. This can be done using techniques such as chemical vapor deposition (ССЗ) или физическое осаждение из газовой фазы (PVD).
- Металлизация: Metal layers are deposited onto the substrate surface to create conductive traces, Колодки, and vias for interconnecting components and forming RF transmission lines. Metallization techniques include sputtering, evaporation, or electroplating.
- Patterning: The metal layers are selectively etched to define the desired circuit patterns and features on the substrate surface. This is typically done using photolithography combined with chemical or plasma etching.
- Обработка поверхности: The substrate surface may undergo surface finishing processes to improve solderability, corrosion resistance, and overall reliability. Common surface finishes include immersion gold, ХАСЛ (Выравнивание припоя горячим воздухом), ЭНИГ (Химический никель иммерсионное золото), and OSP (Органические консерванты для паяния).
- Quality Control and Testing: На протяжении всего производственного процесса, quality control measures are implemented to ensure that the substrate material meets the specified requirements for electrical performance, Точность размеров, и надежность. Testing techniques such as impedance measurements, dielectric constant characterization, and visual inspection are employed to validate the quality of the manufactured substrates.
- Packaging and Assembly:Once manufactured, the Radar HF substrates may be packaged and assembled into complete radar systems or integrated into larger electronic assemblies according to the specific application requirements.
- Final Testing and Inspection: Finished radar systems or assemblies undergo final testing and inspection to verify their performance and reliability before being deployed in the field.
Полный, manufacturing Radar HF substrates requires precision, attention to detail, and adherence to strict quality control standards to ensure the reliable operation of radar systems at high frequencies.
How much should a Radar HF substrate cost?
The cost of Radar HF substrates can vary widely depending on several factors, включая используемый материал, the complexity of the design, the size of the substrate, задействованные производственные процессы, and the supplier’s pricing structure. Here are some key considerations that can influence the cost:
- Стоимость материалов: The cost of the substrate material itself is a significant factor. Different materials, such as ceramics, specialized laminates, or semiconductor materials, have varying costs based on factors like availability, purity, and processing complexity.
- Производственные процессы: The fabrication processes involved in producing Radar HF substrates can range from relatively simple to highly complex, depending on the design requirements. Processes such as deposition, металлизация, patterning, and surface finishing contribute to the overall cost.
- Сложность конструкции: Сложность конструкции подложки, в том числе количество слоев, circuit density, and precision requirements, can impact manufacturing costs. More intricate designs typically require additional processing steps and may involve higher material and labor costs.
- Объем и масштаб: Economies of scale play a significant role in determining the cost of Radar HF substrates. Larger production volumes generally result in lower per-unit costs due to efficiencies in manufacturing and purchasing. Наоборот, smaller production runs may incur higher costs per unit.
- Требования к качеству и надежности: Meeting stringent quality and reliability standards often entails additional testing, inspection, and quality control measures, which can add to the overall cost of production.
- Supplier Pricing and Markup: Supplier pricing policies, including profit margins and overhead expenses, can influence the final cost of Radar HF substrates. Different suppliers may offer competitive pricing based on their capabilities, expertise, and market positioning.
Given the variability of these factors, it’s challenging to provide a specific cost without detailed information about the substrate’s specifications and manufacturing requirements. Дополнительно, costs can fluctuate over time due to changes in material prices, technology advancements, and market dynamics.
For accurate pricing information, it’s recommended to consult with substrate manufacturers or suppliers directly, providing them with detailed specifications and volume requirements for a customized quotation.
What is Radar HF substrate base material?
The choice of base material for Radar HF substrates depends on various factors such as the desired electrical properties, механическая прочность, thermal stability, и соображения по стоимости. Several types of materials are commonly used as base materials for Radar HF substrates:
- Ceramics: Ceramics such as alumina (Ал2О3) и нитрид алюминия (AlN) are widely used for Radar HF substrates. They offer excellent electrical insulation, high thermal conductivity, и хорошая механическая прочность. Alumina substrates are often preferred for their cost-effectiveness, while aluminum nitride substrates provide superior thermal management capabilities.
- Specialized Laminates:Certain laminates, such as those based on polytetrafluoroethylene (PTFE), are designed specifically for high-frequency applications. These laminates, often referred to as PTFE-based substrates, offer low dielectric loss and consistent electrical properties over a wide range of frequencies. Examples include Rogers Corporation’s RO4000 series and Taconic’s TLY series.
- Semiconductor Materials: Semiconductor materials such as gallium arsenide (GaAs) and silicon (Si) are used for Radar HF substrates in some specialized applications. These materials offer high electron mobility, which is advantageous for high-frequency signal processing and RF applications. GaAs substrates, in particular, are used in the manufacture of high-frequency integrated circuits (HCR) for radar and communication systems.
- Other Dielectric Materials: Various other dielectric materials may be used as base materials for Radar HF substrates, depending on specific application requirements. Examples include polyimide, liquid crystal polymer (LCP), and glass-reinforced epoxy (ФР-4). These materials offer different combinations of electrical, механический, and thermal properties to suit diverse application needs.
The choice of base material depends on factors such as the operating frequency range, signal integrity requirements, thermal management needs, and cost constraints. Designers typically select the base material that best balances these factors to achieve the desired performance and reliability in Radar HF systems.
Which company manufactures Radar HF substrates?
Some companies specialize in manufacturing Radar HF substrates, including well-known companies such as Rogers Corporation, Taconic Advanced Dielectric Division, DuPont, Mitsubishi Electric, and Isola Group. These companies have extensive experience and technological expertise in the field of Radar HF substrates, offering various types of substrate materials to meet different application requirements.
As for our company, we are also capable of manufacturing Radar HF substrates. With advanced manufacturing equipment and a skilled technical team, we can provide high-quality, high-performance Radar HF substrates. Our manufacturing process covers various stages including material selection, surface treatment, металлизация, photolithography, офорт, testing, и многое другое, ensuring that our products meet customers’ requirements and standards.
Our Radar HF substrates have the following characteristics and advantages:
- Diverse material selection:We can offer Radar HF substrates made from various materials including ceramics, specialized laminates, и так далее., to meet different application scenarios and performance requirements.
- 2. Highly customizable: We provide customized Radar HF substrate solutions tailored to customers’ design requirements, encompassing design, manufacturing, testing, и так далее., to ensure that the products fully meet customers’ needs.
- Reliable quality: We strictly adhere to quality management systems to ensure the reliability of our products. We utilize advanced testing equipment and technologies to conduct comprehensive inspections and tests to ensure that our products meet industry standards and customer requirements.
- Fast delivery: With efficient production and supply chain management teams, we can respond promptly to customer demands and ensure on-time delivery of products.
Резюме, as our company, we have the capability and experience to manufacture Radar HF substrates, providing customers with high-quality, high-performance customized products to meet various application requirements.
What are the qualities of good customer service?
Good customer service is characterized by several key qualities that contribute to positive interactions and relationships between businesses and their customers. Here are some essential qualities of good customer service:
- Оперативность: Хорошее обслуживание клиентов предполагает оперативное реагирование на запросы клиентов, Проблемы, и просит. Responding to customers in a timely manner demonstrates attentiveness and respect for their time.
- Сочувствие: Effective customer service representatives show empathy and understanding towards customers’ emotions, Проблемы, and needs. Empathetic interactions help build rapport and trust with customers, fostering positive relationships.
- Четкая коммуникация: Четкая и лаконичная коммуникация имеет важное значение для передачи информации, оказание помощи, and resolving issues effectively. Customer service representatives should communicate in a friendly and professional manner, using language that is easy to understand.
- Знание продукта: Good customer service requires a thorough understanding of the products or services offered by the business. Customer service representatives should be knowledgeable about their company’s offerings, Функции, pricing, and policies to provide accurate information and assistance to customers.
- Навыки решения проблем: Customer service representatives should possess strong problem-solving skills to address customer issues and resolve conflicts effectively. They should be proactive in finding solutions and demonstrating a willingness to help customers overcome challenges.
- Patience: Dealing with diverse customer inquiries and concerns may require patience and composure. Customer service representatives should remain calm and composed, Даже в сложных ситуациях, to ensure positive interactions with customers.
- Adaptability: Good customer service involves being adaptable and flexible to meet the unique needs and preferences of different customers. Customer service representatives should be able to adjust their approach and communication style based on the situation and the customer’s personality.
- Follow-Up: Following up with customers after resolving their issues or inquiries shows dedication and commitment to their satisfaction. Customer service representatives should ensure that customers are satisfied with the resolution and offer assistance if further support is needed.
- Consistency: Consistency in service delivery is crucial for building trust and loyalty with customers. Providing consistent levels of service across all customer interactions helps reinforce the company’s reputation and brand image.
- Positive Attitude: Maintaining a positive and friendly attitude creates a welcoming atmosphere and leaves a lasting impression on customers. Customer service representatives should strive to make each interaction a positive experience for the customer.
Воплощая эти качества, businesses can deliver exceptional customer service that fosters loyalty, satisfaction, and positive word-of-mouth referrals.
ЧАСТО ЗАДАВАЕМЫЕ ВОПРОСЫ
What are Radar HF substrates?
Radar HF substrates are specialized materials used as the base for constructing high-frequency radar systems. These substrates are designed to support the transmission and reception of high-frequency radio waves, which are essential for radar applications.
What materials are used for Radar HF substrates?
Various materials can be used for Radar HF substrates, including ceramics (например., глинозем, Нитрид алюминия), specialized laminates (например., PTFE-based materials), semiconductor materials (например., gallium arsenide), and other dielectric materials (например., polyimide, liquid crystal polymer).
What are the key properties of Radar HF substrates?
Key properties of Radar HF substrates include high dielectric constant, low dielectric loss, excellent thermal conductivity, механическая прочность, Стабильность размеров, and compatibility with high-frequency signals.
How are Radar HF substrates manufactured?
The manufacturing process for Radar HF substrates typically involves steps such as material selection, preparation, deposition of dielectric layers (if necessary), металлизация, patterning, Отделка поверхности, quality control, и тестирование. Specific processes may vary depending on the substrate material and design requirements.
What are the applications of Radar HF substrates?
Radar HF substrates are used in a variety of applications, including military and defense radar systems, weather monitoring radar, air traffic control radar, marine radar, automotive radar, and satellite communication systems.
What factors should be considered when selecting Radar HF substrates?
When selecting Radar HF substrates, factors to consider include the operating frequency range, signal integrity requirements, thermal management needs, механическая прочность, Соображения по стоимости, and compatibility with other components in the radar system.
Where can I purchase Radar HF substrates?
Radar HF substrates can be purchased from specialized substrate manufacturers, electronic component distributors, and suppliers of RF and microwave materials. It’s essential to choose a reputable supplier that can provide substrates with the desired specifications and quality.
How can I ensure the reliability of Radar HF substrates?
To ensure the reliability of Radar HF substrates, it’s essential to adhere to quality control measures throughout the manufacturing process, conduct thorough testing and inspection, and follow best practices for substrate handling, storage, and installation in radar systems. Working with experienced suppliers and manufacturers can also help ensure the reliability of substrates.