Microtrace BGA Substrates Manufacturer
Microtrace BGA Substrates Manufacturer,Microtrace BGA substrates represent cutting-edge packaging solutions meticulously engineered by Microtrace for semiconductor devices. These substrates serve as the vital bridge between the chip and the printed circuit board (Печатная плата), employing Ball Grid Array (BGA) architecture renowned for its efficiency and reliability.
Crafted with precision, Microtrace BGA substrates boast a myriad of advanced features. Their high-density interconnects facilitate seamless electrical connections, ensuring optimal performance even in demanding applications. With embedded passive components and innovative thermal management solutions, these substrates excel in dissipating heat effectively, enhancing the overall reliability and longevity of semiconductor devices.
What sets Microtrace BGA substrates apart is their commitment to quality and innovation. Each substrate undergoes rigorous testing and inspection to meet stringent standards, guaranteeing exceptional performance and durability. Whether in consumer electronics, telecommunications, automotive, or aerospace industries, Microtrace BGA substrates stand as the epitome of excellence, empowering devices with unparalleled functionality and reliability.
What is a Microtrace BGA substrate?
A Microtrace BGA substrate is a type of Ball Grid Array (BGA) substrate manufactured by Microtrace, a company specializing in advanced packaging solutions for semiconductor devices. BGA substrates are used in integrated circuits to provide electrical connections between the chip and the printed circuit board (Печатная плата).
Microtrace BGA substrates are likely to offer high-density interconnects, precise alignment features, and possibly advanced materials or manufacturing techniques to meet the demands of modern electronics. These substrates may also incorporate features such as embedded passive components, thermal management solutions, or enhanced signal integrity characteristics.
The specific features and capabilities of Microtrace BGA substrates would depend on the product line and the requirements of the application they’re intended for.
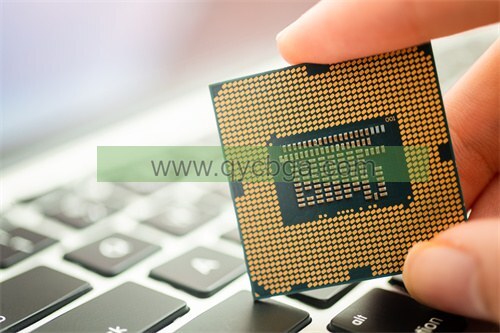
Microtrace BGA Substrates Manufacturer
What are the Microtrace BGA Substrate Design Guidelines?
As of my last update, specific design guidelines for Microtrace BGA substrates may not be publicly available or may vary depending on the particular product line or application requirements. Однако, typical design guidelines for BGA substrates in general include:
- Pitch and Layout: Follow recommended pitch guidelines for BGA balls or pads, ensuring proper spacing for reliable soldering and electrical connections.
- Pad and Via Design: Design appropriate pad sizes and via structures to accommodate signal, power, and ground connections while maintaining signal integrity and thermal performance.
- Thermal Considerations: Incorporate thermal vias or other thermal management features to efficiently dissipate heat generated by the BGA package.
- Signal Integrity: Minimize signal trace lengths and maintain controlled impedance for high-speed signal routing to prevent signal degradation and ensure reliable data transmission.
- Power Distribution: Design robust power delivery networks with low impedance paths to ensure stable power distribution and minimize voltage drops.
- Assembly and Soldering: Consider assembly and soldering processes during substrate design, including solder mask design, solder paste stencil design, and alignment features for accurate assembly.
- Component Placement: Optimize component placement to minimize signal path lengths, reduce cross-talk, and facilitate efficient routing of traces.
- Package Size and Thickness: Choose appropriate package size and thickness to meet mechanical and electrical requirements while considering space constraints and manufacturing feasibility.
- Соображения по поводу надежности: Design for reliability by considering factors such as thermal cycling, mechanical stress, and environmental conditions that may affect the performance and longevity of the BGA substrate.
- Соответствие и стандарты: Ensure compliance with industry standards and specifications relevant to BGA substrates, such as IPC (Association Connecting Electronics Industries) standards.
For specific design guidelines tailored to Microtrace BGA substrates, it’s recommended to consult directly with Microtrace or refer to any documentation provided by the company. They may offer application notes, datasheets, or technical support to assist with substrate design.
What is the Microtrace BGA Substrate Fabrication Process?
The specific fabrication process for Microtrace BGA substrates may not be publicly disclosed, but I can outline a general overview of the typical fabrication process for BGA substrates:
- Выбор материала основания: The process starts with selecting the appropriate substrate material based on the desired electrical, термический, и механические свойства. Common substrate materials include FR-4 (epoxy-based laminate), полиимид, or more specialized materials like ceramic or high-performance laminates.
- Preparation of Substrate Material: The selected substrate material is prepared by cutting it into the desired size and shape, typically using automated cutting equipment.
- Подготовка поверхности: The substrate surface is cleaned and prepared to ensure proper adhesion of subsequent layers and materials. This may involve processes such as surface roughening, cleaning with solvents, and applying adhesion-promoting layers.
- Circuit Patterning: Circuit patterns, including signal traces, Экраны питания, и наземные самолеты, are defined on the substrate using processes such as photolithography, screen printing, or laser ablation. These processes create the conductive pathways required for electrical connections.
- Additive Processes (Необязательный): Additional features such as embedded passive components, thermal vias, or special materials may be added using additive processes like screen printing or inkjet printing.
- Осаждение диэлектрического слоя: Dielectric layers are deposited over the circuit patterns to insulate the conductive traces and provide mechanical support. These layers may be deposited using techniques such as thin-film deposition or lamination of pre-fabricated dielectric sheets.
- Формирование переходных отверстий: Vias (plated or non-plated holes) are drilled or punched through the substrate to establish connections between different layers of the substrate and provide access to inner circuitry. Vias are typically formed using mechanical drilling, Лазерное сверление, or chemical etching processes.
- Plating and Metallization: Conductive materials such as copper are deposited onto the substrate surface and into the vias using processes like electroplating or sputtering. This step forms the conductive pathways required for interconnections between layers and for attaching semiconductor devices.
- Нанесение паяльной маски: A solder mask layer is applied over the substrate surface, leaving openings (exposed pads) for soldering the BGA balls or leads. The solder mask provides insulation and protection for the circuitry while defining the soldering areas.
- Обработка поверхности: The exposed metal surfaces are coated with a surface finish such as immersion gold, electroless nickel immersion gold (ЭНИГ), or tin-lead solder to enhance solderability and prevent oxidation.
- Final Inspection and Testing: The fabricated BGA substrates undergo rigorous inspection and testing to ensure they meet quality standards and specifications. This may include visual inspection, electrical testing, и тестирование надежности.
It’s important to note that the fabrication process may vary depending on factors such as substrate material, Сложность конструкции, and specific requirements of the application or industry. For precise details on the Microtrace BGA substrate fabrication process, it’s best to consult directly with Microtrace or refer to any documentation provided by the company.
How do you manufacture a Microtrace BGA Substrate?
While the exact manufacturing process for Microtrace BGA substrates is proprietary information and may not be publicly available, I can provide a general overview of the steps involved in manufacturing BGA substrates, which may be similar to the processes used by Microtrace:
- Design and Layout: The manufacturing process begins with the design and layout of the BGA substrate. This involves determining the electrical connections, Маршрутизация сигналов, component placement, and overall substrate architecture according to the specific requirements of the application.
- Выбор материала основания: The appropriate substrate material is selected based on factors such as electrical properties, теплопроводность, механическая прочность, и соображения по стоимости. Common substrate materials include FR-4 (epoxy-based laminate), полиимид, керамический, or high-performance laminates.
- Preparation of Substrate Material: The substrate material is prepared by cutting it into the desired size and shape using automated cutting equipment. The surface of the substrate may be cleaned and prepared to ensure proper adhesion of subsequent layers.
- Circuit Patterning: Circuit patterns, including signal traces, Экраны питания, и наземные самолеты, are defined on the substrate using processes such as photolithography, screen printing, or laser ablation. These processes create the conductive pathways required for electrical connections.
- Additive Processes (Необязательный): Additional features such as embedded passive components, thermal vias, or special materials may be added using additive processes like screen printing or inkjet printing.
- Осаждение диэлектрического слоя: Dielectric layers are deposited over the circuit patterns to insulate the conductive traces and provide mechanical support. These layers may be deposited using techniques such as thin-film deposition or lamination of pre-fabricated dielectric sheets.
- Формирование переходных отверстий: Vias (plated or non-plated holes) are drilled or punched through the substrate to establish connections between different layers of the substrate and provide access to inner circuitry. Vias are typically formed using mechanical drilling, Лазерное сверление, or chemical etching processes.
- Metallization and Plating: Conductive materials such as copper are deposited onto the substrate surface and into the vias using processes like electroplating or sputtering. This step forms the conductive pathways required for interconnections between layers and for attaching semiconductor devices.
- Нанесение паяльной маски: A solder mask layer is applied over the substrate surface, leaving openings (exposed pads) for soldering the BGA balls or leads. The solder mask provides insulation and protection for the circuitry while defining the soldering areas.
- Обработка поверхности: The exposed metal surfaces are coated with a surface finish such as immersion gold, electroless nickel immersion gold (ЭНИГ), or tin-lead solder to enhance solderability and prevent oxidation.
- Final Inspection and Testing: The manufactured BGA substrates undergo rigorous inspection and testing to ensure they meet quality standards and specifications. This may include visual inspection, electrical testing, и тестирование надежности.
На протяжении всего производственного процесса, quality control measures are implemented to ensure the consistency, надёжность, and performance of the Microtrace BGA substrates. Дополнительно, the manufacturing process may be customized or optimized to meet the specific requirements of different applications and industries.
How much should a Microtrace BGA Substrate cost?
The cost of a Microtrace BGA substrate can vary significantly depending on several factors, including:
- Size and Complexity: Larger and more complex substrates typically cost more due to the increased material and manufacturing requirements.
- Materials:The choice of substrate material can greatly impact the cost. High-performance materials or specialized substrates may incur higher costs compared to standard materials.
- Сложность конструкции: Intricate designs with tight tolerances, multiple layers, embedded components, and advanced features may increase the manufacturing cost.
- Volume: The quantity of BGA substrates ordered can affect the unit cost. Larger volume orders often result in economies of scale and lower per-unit costs.
- Настройка: Настраиваемые функции, Особые требования, and unique specifications may add to the overall cost.
- Quality and Reliability Standards: Meeting specific quality and reliability standards may involve additional testing and validation processes, contributing to the overall cost.
- Отношения с поставщиками: Establishing long-term partnerships or bulk purchasing agreements with Microtrace or its authorized distributors may lead to negotiated pricing.
Since Microtrace BGA substrates are proprietary products, the exact pricing information would likely be provided directly by Microtrace or its authorized distributors. It’s recommended to contact Microtrace for a customized quote based on your specific requirements and volume needs.
What is Microtrace BGA Substrate base material?
The specific base material used for Microtrace BGA substrates may not be publicly disclosed, as it could be proprietary information. Однако, BGA substrates typically utilize materials such as:
- ФР-4 (Flame Retardant 4): FR-4 is a commonly used epoxy-based laminate material known for its low cost, хорошие электроизоляционные свойства, and ease of fabrication. It’s widely used in consumer electronics and low- to mid-range applications.
- Polyimide: Polyimide substrates offer excellent thermal stability, flexibility, and resistance to heat and chemicals. They are often used in applications where high-temperature operation or flexibility is required, such as aerospace and automotive electronics.
- High-Performance Laminates: High-performance laminates encompass a range of advanced materials with superior electrical, термический, и механические свойства. These materials may include ceramic-filled laminates, liquid crystal polymer (LCP), or other specialty materials optimized for specific applications or demanding environments.
- Ceramic: Ceramic substrates provide exceptional thermal conductivity, Стабильность размеров, и надежность, making them suitable for high-power and high-frequency applications. They are commonly used in RF/microwave, Силовая электроника, and automotive applications.
The choice of base material depends on various factors such as electrical performance requirements, thermal management needs, механическая прочность, Соображения по стоимости, and specific application demands. For precise information on the base material used in Microtrace BGA substrates, it’s best to contact Microtrace directly or refer to any documentation provided by the company.
Which company makes Microtrace BGA Substrates?
Microtrace BGA substrates are manufactured by Microtrace. Microtrace is a company specialized in advanced packaging solutions, dedicated to providing innovative packaging solutions for semiconductor devices. Our company has advanced technology and extensive experience to design, manufacture, and supply high-quality Microtrace BGA substrates.
We have state-of-the-art manufacturing equipment and a skilled technical team capable of meeting various complex BGA substrate manufacturing needs. We employ advanced materials and processes to ensure that Microtrace BGA substrates have excellent electrical, термический, и механические свойства. We are committed to continuous innovation and process optimization to ensure that our products maintain a competitive edge in the market.
Our company emphasizes quality control and customer satisfaction. We strictly adhere to international quality standards and specifications, ensuring that each Microtrace BGA substrate undergoes rigorous inspection and testing to ensure its quality and reliability. We have established long-term partnerships with customers, earning their trust and support by providing high-quality products and excellent service.
In conclusion, our company has the capability to design, manufacture, and supply Microtrace BGA substrates, and has earned recognition from customers for our excellent quality and service. We will continue to strive to provide innovative solutions, meet the evolving needs of customers, and contribute to the advancement of the semiconductor industry.
Какие бывают 7 Качества хорошего обслуживания клиентов?
Good customer service is characterized by several key qualities that contribute to a positive customer experience. Here are seven qualities of good customer service:
- Оперативность:Good customer service involves being prompt and responsive to customer inquiries, Проблемы, и просит. This includes acknowledging customers promptly, providing timely assistance, and addressing their needs in a timely manner.
- Сочувствие: Empathy involves understanding and empathizing with the customer’s perspective, feelings, and situation. Good customer service representatives demonstrate empathy by actively listening to customers, showing understanding of their concerns, and offering appropriate solutions or support.
- Профессионализм: Professionalism entails maintaining a courteous, почтительный, and professional demeanor when interacting with customers. This includes communicating clearly and effectively, adhering to company policies and standards, and handling challenging situations with professionalism and composure.
- Компетентность: Good customer service representatives are knowledgeable about the products, Услуги, and policies of the company. They are able to provide accurate information, answer questions effectively, and offer helpful recommendations or solutions to customers.
- Надёжность: Reliability involves consistently delivering on promises and commitments made to customers. This includes following through on service guarantees, fulfilling orders accurately and on time, and providing reliable support and assistance whenever needed.
- Навыки решения проблем: Good customer service representatives possess strong problem-solving skills to effectively address customer issues and resolve conflicts. They are proactive in identifying and addressing customer concerns, finding creative solutions to problems, and ensuring customer satisfaction.
- Positive Attitude: A positive attitude is essential for delivering excellent customer service. Good customer service representatives maintain a positive and friendly demeanor, Даже в сложных ситуациях. They strive to leave customers with a positive impression of their interaction with the company.
Воплощая эти качества, companies can cultivate a customer-centric culture and build strong relationships with their customers, ultimately leading to increased customer satisfaction, loyalty, and retention.
ЧАСТО ЗАДАВАЕМЫЕ ВОПРОСЫ
What are Microtrace BGA substrates?
Microtrace BGA substrates are advanced packaging solutions designed and manufactured by Microtrace for semiconductor devices. They provide electrical connections between the chip and the printed circuit board (Печатная плата), typically using a Ball Grid Array (BGA) format.
What are the key features of Microtrace BGA substrates?
Microtrace BGA substrates may offer high-density interconnects, precise alignment features, advanced materials, and manufacturing techniques. They may also incorporate embedded passive components, thermal management solutions, and enhanced signal integrity characteristics.
What applications are Microtrace BGA substrates suitable for?
Microtrace BGA substrates are suitable for a wide range of applications in industries such as consumer electronics, telecommunications, Автомобильная электроника, аэрокосмический, и многое другое. They are commonly used in devices requiring high-performance packaging solutions.
What is the fabrication process for Microtrace BGA substrates?
The fabrication process for Microtrace BGA substrates involves several steps, including substrate material selection, circuit patterning, via formation, металлизация, Нанесение паяльной маски, surface finish, and final inspection and testing. The exact process may vary depending on specific requirements.
What are the benefits of using Microtrace BGA substrates?
The benefits of using Microtrace BGA substrates include improved electrical performance, enhanced thermal management, increased reliability, and space-saving design. They can help optimize the performance and functionality of semiconductor devices.
Where can I find more information about Microtrace BGA substrates?
For more information about Microtrace BGA substrates, including technical specifications, product offerings, and application support, you can contact Microtrace directly or visit their official website for documentation and resources.