Ceramics Substrate Manufacturer
Ceramics Substrate Manufacturer,Ceramics substrates are the backbone of modern electronic devices, providing a sturdy foundation for a wide range of components and circuits. Composed of advanced ceramic materials such as alumina, Нитрид алюминия, and silicon carbide, these substrates offer exceptional thermal conductivity, Электроизоляционные, и механическая стабильность. Their ability to dissipate heat efficiently makes them ideal for applications requiring high power and reliability, such as power electronics and automotive systems. Ceramics substrates are manufactured through precise processes including shaping, обжиг, и обработка поверхности, ensuring uniformity and quality in every piece. Customizable to meet specific requirements, they come in various sizes, shapes, and thicknesses, accommodating diverse electronic designs. With their durability, environmental friendliness, and versatility, ceramics substrates play a vital role in powering the innovations of today’s technology-driven world.
What is a Ceramics Substrate?
A ceramics substrate is a base material typically made of ceramic compounds that are used in various electronic and semiconductor applications. These substrates are engineered to provide a stable and reliable foundation for electronic components, such as integrated circuits (HCR), resistors, capacitors, and other electronic devices.
Ceramics substrates offer several advantages over other materials like plastics or metals. They possess excellent thermal conductivity, which helps in dissipating heat generated by electronic components, thus ensuring the reliability and longevity of the devices. Дополнительно, ceramics substrates exhibit good electrical insulation properties, which are crucial for preventing electrical interference and ensuring proper functioning of electronic circuits.
These substrates come in different forms, including sheets, boards, and packages, and can be customized to meet specific requirements such as size, форма, and thermal properties. They are widely used in industries such as telecommunications, automotive, аэрокосмический, and consumer electronics for applications ranging from power electronics to microelectronics.
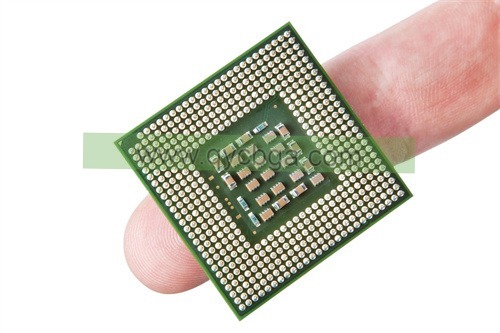
Ceramics Substrate Manufacturer
What are Ceramics Substrate Design Guidelines?
Design guidelines for ceramics substrates are crucial to ensure the optimal performance and reliability of electronic components and circuits. Here are some common ceramics substrate design guidelines:
- Выбор материала: Choose a ceramic material with appropriate properties for the application, такие как теплопроводность, коэффициент теплового расширения (КЛТР), диэлектрическая проницаемость, механическая прочность, and cost. Common ceramics used include alumina (Ал2О3), Нитрид алюминия (AlN), and silicon carbide (SiC).
- Стабильность размеров: Ensure that the substrate material exhibits minimal dimensional changes over a range of operating temperatures to prevent stress on attached components.
- Управление температурным режимом: Design the substrate to efficiently dissipate heat generated by electronic components. This includes optimizing the substrate thickness, thermal vias, and heat sink attachment points.
- Электроизоляционные: Maintain adequate electrical insulation between conductive traces and components to prevent short circuits. This involves proper selection of dielectric materials and careful design of insulation layers.
- Signal Integrity: Minimize signal loss and electromagnetic interference (EMI) by optimizing trace layout, impedance matching, and signal routing techniques.
- Mechanical Stability: Ensure the substrate can withstand mechanical stresses encountered during assembly, handling, and operation without compromising its structural integrity.
- Component Mounting: Design mounting features such as pads, Вьяс, and holes to facilitate the attachment of electronic components through soldering, Проволочное соединение, or flip-chip bonding.
- Технологичность: Consider manufacturability aspects such as substrate fabrication techniques (например., thick-film, thin-film, or co-fired processes), Допуски, and scalability to ensure cost-effective production.
- Экологические соображения: Account for environmental factors such as humidity, temperature extremes, and exposure to chemicals or contaminants that may affect the substrate’s performance over time.
- Тестирование и контроль качества: Implement testing protocols to verify the substrate’s electrical, термический, и механические свойства, as well as reliability testing to ensure long-term performance under anticipated operating conditions.
Придерживаясь этих рекомендаций по проектированию, engineers can develop ceramics substrates that meet the specific requirements of their electronic applications while ensuring reliability, performance, and cost-effectiveness.
How do you manufacture a Ceramics Substrate?
Manufacturing ceramics substrates typically involves several steps, включая подготовку материала, формирование, обжиг, and post-processing. Here’s an overview of the manufacturing process:
- Material Selection: Choose the appropriate ceramic material based on the desired properties such as thermal conductivity, диэлектрическая проницаемость, и механическая прочность. Common ceramic materials used for substrates include alumina (Ал2О3), Нитрид алюминия (AlN), and silicon carbide (SiC).
- Подготовка материала: The selected ceramic material is initially in the form of powder. It undergoes various processing steps such as milling, mixing, and shaping to achieve the desired consistency and composition. Additives may be included to enhance properties like sinterability and electrical insulation.
- Формирование: The prepared ceramic material is shaped into the desired form of the substrate. This can be achieved through various techniques such as pressing (uniaxial or isostatic), литье под давлением, or tape casting. Pressing involves compressing the ceramic powder into a mold under high pressure, while injection molding utilizes a heated ceramic slurry injected into a mold cavity. Tape casting involves casting a ceramic slurry onto a flat surface to form thin sheets.
- Сушка: After shaping, the green ceramic substrates undergo a drying process to remove excess moisture. Care must be taken during drying to prevent cracking or warping of the substrates.
- Обжиг (Спекание): The dried green substrates are then fired in a kiln at high temperatures typically ranging from several hundred to over a thousand degrees Celsius. This process, known as sintering, causes the ceramic particles to bond together and form a dense, solid structure. The firing temperature and duration are carefully controlled to achieve the desired densification and mechanical properties.
- Поверхностная обработка: После спекания, the substrates may undergo surface treatments such as polishing, grinding, or metallization to prepare them for subsequent processing steps or to improve surface flatness and conductivity.
- Металлизация: Metallization involves depositing conductive metal layers onto the substrate surface to create circuit traces, Колодки, and vias. This can be accomplished through techniques such as screen printing, разбрызгивание, или толстопленочным осаждением.
- Post-Processing: Additional post-processing steps may be performed depending on the specific application requirements. This could include laser cutting, сверление, or coating with protective or insulating materials.
- Контроль качества: На протяжении всего производственного процесса, quality control measures are implemented to ensure the substrates meet the required specifications for dimensional accuracy, surface finish, electrical properties, и надежность.
By following these manufacturing steps and quality control measures, ceramics substrates can be produced with the necessary properties to meet the demands of various electronic applications.
How much should a Ceramics Substrate cost?
The cost of ceramics substrates can vary widely depending on several factors, including the type of ceramic material used, the substrate size and thickness, Производственные процессы, Сложность конструкции, and desired properties such as thermal conductivity and electrical insulation.
Вообще, ceramics substrates tend to be more expensive than substrates made from other materials like FR-4 (a common epoxy-based laminate) due to the specialized manufacturing processes involved and the properties offered by ceramic materials such as high thermal conductivity and excellent electrical insulation.
В качестве приблизительной оценки, the cost of ceramics substrates can range from a few dollars for simple, small-sized substrates to several hundred dollars or more for larger, custom-designed substrates with specific properties and complex features.
To get an accurate cost estimate for a ceramics substrate for a particular application, it’s best to consult with manufacturers or suppliers who can provide quotes based on the specific requirements and quantities needed. Дополнительно, factors such as economies of scale, order volume, and negotiation may also impact the final cost.
What is Ceramics Substrate base material?
The base material of ceramics substrates is typically a ceramic compound. The choice of ceramic material depends on the specific requirements of the application, такие как теплопроводность, Электроизоляционные, механическая прочность, and cost. Some common ceramic materials used for substrates include:
- Глинозем (Ал2О3): Alumina is one of the most widely used ceramic materials for substrates. It offers excellent mechanical strength, теплопроводность, and electrical insulation properties. Alumina substrates are often used in high-power applications and harsh environments due to their durability and resistance to temperature extremes and corrosion.
- Нитрид алюминия (AlN):Aluminum nitride exhibits high thermal conductivity, making it ideal for applications requiring efficient heat dissipation, such as power electronics and high-frequency circuits. AlN substrates also offer good electrical insulation and dimensional stability.
- Silicon Carbide (SiC): Silicon carbide substrates have exceptional thermal conductivity, механическая прочность, and resistance to high temperatures and harsh chemicals. SiC substrates are commonly used in high-power and high-frequency applications, as well as in environments with extreme conditions such as aerospace and automotive.
- Оксид бериллия (BeO): Beryllium oxide offers very high thermal conductivity, second only to diamond among ceramics. Однако, due to health and safety concerns associated with beryllium exposure, its use is restricted in many applications.
These ceramic materials provide a stable and reliable foundation for electronic components and circuits, Обеспечение баланса тепловых температур, электрический, and mechanical properties tailored to specific application requirements. Depending on the application, ceramics substrates may also incorporate additional layers or coatings to enhance performance or facilitate specific functions such as metallization for creating conductive traces.
Which company makes Ceramics Substrates?
Many companies produce ceramic substrates, including well-known names such as Kyocera, Murata, NGK, Coorstek, и другие. These companies are highly reputed in the electronics, полупроводник, and other industries, offering various types and specifications of ceramic substrates to meet the needs of different applications.
As for our company, we also manufacture ceramic substrates. Мы располагаем передовым производственным оборудованием и технологиями, along with an experienced engineering team capable of designing and producing customized ceramic substrates according to customer requirements.
The production process of ceramic substrates in our company covers multiple stages, включая подготовку материала, формирование, спекание, surface treatment, and quality control. We use high-quality ceramic materials such as alumina, Нитрид алюминия, or silicon carbide, selecting the appropriate materials and processes based on customer specifications.
На протяжении всего производственного процесса, we maintain strict quality control to ensure that the ceramic substrates meet customer specifications and standards. Our production team possesses extensive experience and expertise, capable of meeting the requirements of various complex applications.
In addition to standard specifications, we also offer customization services, designing and manufacturing ceramic substrates according to specific customer requirements. Whether it’s material selection, size customization, surface treatment, or special requirements, we can provide professional advice and solutions.
Резюме, our company has the technological strength and professional capabilities required for ceramic substrate production, enabling us to deliver high-quality, customized products and services to customers.
Какие бывают 7 Качества хорошего обслуживания клиентов?
Good customer service is essential for building strong relationships with customers and ensuring their satisfaction. Here are seven qualities that characterize good customer service:
- Оперативность: Хорошее обслуживание клиентов предполагает оперативное реагирование на запросы клиентов, Проблемы, и просит. Responding to customer needs in a timely manner shows that you value their time and are committed to helping them resolve issues quickly.
- Сочувствие: Empathy is the ability to understand and share the feelings of others. Good customer service representatives empathize with customers’ situations, listen attentively to their concerns, and demonstrate genuine concern for their well-being.
- Ясность: Clear communication is key to providing good customer service. Customer service representatives should convey information in a concise and understandable manner, avoiding jargon or technical language that may confuse customers.
- Компетентность: Good customer service requires having a thorough understanding of the products or services offered, as well as company policies and procedures. Customer service representatives should be knowledgeable enough to answer customer questions accurately and provide relevant information or assistance.
- Профессионализм: Professionalism encompasses behaviors such as politeness, respectfulness, и поддержание позитивного настроя, Даже в сложных ситуациях. Customer service representatives should conduct themselves professionally at all times, treating customers with courtesy and professionalism.
- Flexibility: Good customer service involves being flexible and adaptable to meet the diverse needs of customers. This may include accommodating special requests, offering alternative solutions, or adjusting policies when necessary to ensure customer satisfaction.
- Follow-up: Following up with customers after resolving their issues or inquiries demonstrates a commitment to customer satisfaction and helps to ensure that their needs have been met. Good customer service representatives follow up with customers to ensure they are satisfied with the resolution and to address any further concerns or feedback.
Воплощая эти качества, businesses can deliver exceptional customer service experiences that foster loyalty, build trust, and enhance their reputation.
ЧАСТО ЗАДАВАЕМЫЕ ВОПРОСЫ
What are ceramics substrates used for?
Ceramics substrates are used as the base material for electronic components and circuits. They provide a stable foundation for mounting and interconnecting various electronic devices, such as integrated circuits, resistors, capacitors, and sensors.
What types of ceramic materials are used for substrates?
Common ceramic materials used for substrates include alumina (Ал2О3), Нитрид алюминия (AlN), silicon carbide (SiC), and beryllium oxide (BeO). Each material offers different properties suited to specific applications, такие как теплопроводность, Электроизоляционные, и механическая прочность.
What are the advantages of ceramics substrates?
Ceramics substrates offer several advantages, в том числе с высокой теплопроводностью, отличная электроизоляция, механическая стабильность, and resistance to temperature extremes and harsh environments. These properties make ceramics substrates well-suited for use in demanding electronic applications.
How are ceramics substrates manufactured?
Ceramics substrates are typically manufactured through processes such as shaping, drying, обжиг (спекание), surface treatment, and quality control. The specific manufacturing methods may vary depending on the type of ceramic material used and the desired substrate properties.
What factors should be considered when selecting ceramics substrates?
When selecting ceramics substrates, factors to consider include the material composition, теплопроводность, диэлектрическая проницаемость, механическая прочность, Стабильность размеров, and cost. The choice of substrate should be based on the specific requirements of the application.
Can ceramics substrates be customized?
Да, ceramics substrates can be customized to meet the specific requirements of different applications. Customization options may include substrate size, форма, толщина, surface finish, and metallization patterns, Среди прочих.
Are ceramics substrates environmentally friendly?
Ceramics substrates are generally considered to be environmentally friendly materials, as they are durable, non-toxic, and chemically inert. Однако, certain ceramic materials may require special handling or disposal procedures due to their composition or manufacturing processes.