What is Microtrace Substrate?
Producător de substraturi Microtrace,Microtrace substrate is an advanced material used in microelectronic applications for precise traceability and authentication. It integrates microscopic identifiers, such as encoded patterns or unique markers, directly into the substrate material. This enables secure and reliable product authentication, anti-counterfeiting measures, and supply chain tracking. Microtrace substrates offer high durability, chemical resistance, and compatibility with various manufacturing processes. They find applications in industries such as pharmaceuticals, electronics, and luxury goods, where product authenticity and traceability are paramount. Microtrace substrates provide an effective solution for enhancing brand protection and consumer trust in the market.
Microtrace Substrate typically refers to a specialized material used in various scientific and industrial applications for purposes such as microscopy, microelectronics, and microfabrication. The exact composition and properties of Microtrace Substrate can vary depending on the specific application requirements, but it is often designed to have precise dimensions, high purity, and specific surface characteristics conducive to the intended use.
In microscopy, Microtrace Substrates can refer to materials such as glass slides or silicon wafers that are used as a base for mounting samples for observation under a microscope. In microelectronics and microfabrication, they can refer to substrates such as silicon, silicon dioxide, or various types of semiconductor materials used as a base for fabricating electronic devices or integrated circuits.
The term “Microtrace” may also be associated with trace analysis or forensic science, where it might refer to substrates or materials used for collecting and analyzing microscopic traces of evidence, such as fibers, particles, or chemical residues. In this context, Microtrace Substrates would be selected or prepared to optimize the collection, preservation, and analysis of such traces.
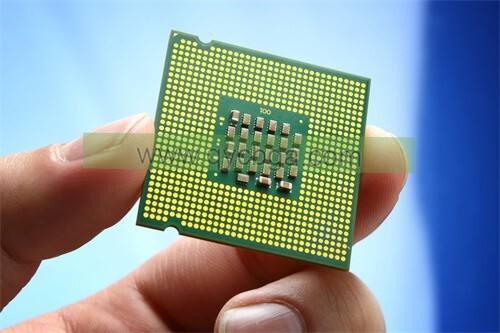
Producător de substraturi Microtrace
Microtrace Substrate design Reference Guide.
- Selectarea materialelor: Choose a substrate material suitable for the intended application. Common substrate materials include glass, silicon, silicon dioxide, and various types of polymers. Consider factors such as transparency, thermal and chemical resistance, and compatibility with analytical techniques.
- Surface Properties: Tailor the surface properties of the substrate to optimize trace collection and analysis. This may involve surface treatments such as cleaning, coating, or functionalization to enhance adhesion, reduce background interference, or promote specific interactions with trace analytes.
- Dimensional Control: Ensure precise control over the dimensions and geometry of the substrate to facilitate accurate trace deposition and analysis. This may involve techniques such as photolithography, laser micromachining, or chemical etching to pattern the substrate surface with features of the desired size and shape.
- Uniformity and Reproducibility: Maintain uniformity and reproducibility in substrate fabrication to ensure consistent performance across multiple samples and experiments. Use quality control measures to monitor substrate quality and minimize variations in surface properties and performance.
- Compatibility with Analytical Techniques: Consider the compatibility of the substrate with the analytical techniques used for trace analysis. For example, choose a substrate material and surface treatment that minimize background interference and optimize signal detection for techniques such as microscopy, spectroscopy, or mass spectrometry.
- Application-Specific Considerations: Take into account any specific requirements or constraints imposed by the application or analytical method. For example, in forensic trace analysis, consider factors such as sample collection methods, preservation techniques, and chain of custody requirements.
While there may not be a single comprehensive reference guide for Microtrace Substrate design, these principles can serve as a starting point for designing substrates tailored to specific microtrace applications. Suplimentar, consulting scientific literature, technical journals, and expert opinions in the field can provide valuable insights and guidance for substrate design and optimization.
What are the materials used in Microtrace Substrate?
Microtrace substrates can be made from various materials depending on the specific application requirements. Some common materials used in microtrace substrate fabrication include:
- Glass: Glass substrates, such as microscope slides or coverslips, are commonly used in microscopy applications due to their transparency, flatness, and compatibility with optical microscopy techniques. They can also be surface-treated or coated to modify their properties for specific applications.
- Silicon: Silicon substrates are widely used in microelectronics and semiconductor manufacturing due to their excellent electrical properties, mechanical stability, and compatibility with integrated circuit fabrication processes. Silicon substrates can also be used in microfabrication techniques such as photolithography and etching to create microstructured surfaces.
- Silicon Dioxide (Silica): Silicon dioxide substrates, often in the form of silicon wafers with a silicon dioxide layer, are commonly used in semiconductor manufacturing and microfabrication processes. Silicon dioxide provides excellent surface properties, including high thermal and chemical stability, making it suitable for various microtrace applications.
- Polymers: Various polymers, such as polydimethylsiloxane (PDMS), polymethyl methacrylate (PMMA), and polyimide, are used as substrates in microfluidics, microelectromechanical systems (MEMS), and flexible electronics. Polymers offer advantages such as flexibility, biocompatibility, and ease of fabrication, making them suitable for diverse microtrace applications.
- Metals: Metals such as gold, silver, and platinum are used as substrates in applications requiring conductive surfaces or metal-enhanced detection techniques. Metal substrates can be functionalized or coated with organic layers to modify their surface properties for specific applications.
- Ceramics: Ceramic substrates, such as alumina (aluminum oxide) or titania (titanium dioxide), are used in high-temperature and harsh-environment applications where thermal and chemical stability are crucial. Ceramic substrates can also be engineered to have specific surface properties, such as hydrophobicity or biocompatibility, for microtrace applications.
These are just a few examples of the materials used in microtrace substrate fabrication. The choice of substrate material depends on factors such as the intended application, required properties (De ex., optical transparency, electrical conductivity, biocompatibility), and fabrication techniques employed.
How is Microtrace Substrate manufactured?
The manufacturing process for microtrace substrates can vary depending on the material, desired properties, and intended application. Însă, here’s a generalized overview of the manufacturing steps involved:
- Selectarea materialelor: The process begins with selecting the appropriate substrate material based on the requirements of the application. Common materials include glass, silicon, polymers, metals, and ceramics.
- Pregătirea substratului: The chosen substrate material is prepared for further processing. This may involve cutting, shaping, cleaning, and surface treatment to achieve the desired dimensions, geometry, and surface properties.
- Surface Modification: Depending on the application, the substrate surface may undergo various modifications to enhance its performance. Tratamente de suprafață, cum ar fi curățarea, coating, or functionalization may be applied to improve adhesion, reduce background interference, or promote specific interactions with trace analytes.
- Patterning and Structuring: În unele cazuri, the substrate surface may need to be patterned or structured to create specific features or geometries. This can be achieved through techniques such as photolithography, laser micromachining, chemical etching, or nanoimprint lithography.
- Quality Control: Pe tot parcursul procesului de fabricație, quality control measures are implemented to ensure the consistency and reliability of the substrates. This may involve inspection, testing, and characterization of substrate properties such as dimensional accuracy, surface roughness, and chemical composition.
- Packaging and Handling: Odată fabricat, the substrates are typically packaged and handled with care to prevent contamination or damage during storage, transport, and use. Proper packaging materials and procedures are employed to maintain substrate integrity and performance.
- Application-Specific Processing: Depending on the intended application, additional processing steps may be required to customize the substrates for specific uses. For example, in microelectronics, substrates may undergo further processing steps such as doping, metallization, or encapsulation to fabricate electronic devices or integrated circuits.
General, the manufacturing of microtrace substrates involves a combination of material preparation, surface modification, patterning, quality control, and application-specific processing steps to create substrates optimized for microanalysis and trace detection applications.
The Application area of Microtrace Substrate
Microtrace substrates find applications across various fields where precise sample preparation, observation, and analysis of microscopic features or traces are essential. Some common application areas include:
- Microscopy: Microtrace substrates are widely used in microscopy applications for mounting and observing samples under optical, electron, or scanning probe microscopes. They provide a stable and transparent platform for sample observation, facilitating detailed analysis of microstructures, particles, cells, and other biological or material samples.
- Microanalysis and Forensics: In forensic science and trace analysis, microtrace substrates play a crucial role in collecting, preserving, and analyzing microscopic traces of evidence such as fibers, hairs, paints, gunshot residue, and biological fluids. Substrates with tailored surface properties may enhance trace adhesion, minimize contamination, and optimize detection sensitivity in analytical techniques such as spectroscopy, chromatography, and microscopy.
- Microelectronics and Semiconductor Manufacturing: Microtrace substrates are used in the fabrication and testing of semiconductor devices, integrated circuits, and microelectromechanical systems (MEMS). Silicon wafers and other semiconductor substrates serve as the foundation for building electronic components, while specialized substrates may be used for tasks such as wafer bonding, thin-film deposition, and lithography patterning.
- Biomedical Research and Diagnostics: Microtrace substrates play a role in biomedical research, drug discovery, and diagnostics by enabling the preparation and analysis of biological samples at the microscale. They are used in techniques such as cell culture, immunohistochemistry, DNA microarrays, and protein microarrays for studying cellular behavior, biomolecular interactions, and disease mechanisms.
- Microfluidics and Lab-on-a-Chip Devices: Microtrace substrates are integral components of microfluidic devices and lab-on-a-chip systems, where they provide the structural support for microchannels, reaction chambers, and detection zones. Polymer substrates such as PDMS are commonly used in microfluidics for their flexibility, biocompatibility, and ease of fabrication, allowing for miniaturized and integrated platforms for chemical analysis, biosensing, and point-of-care diagnostics.
- Surface Science and Materials Research: Microtrace substrates are employed in surface science and materials research for studying surface properties, interface phenomena, and thin film deposition processes at the micro- and nanoscale. They serve as model surfaces for investigating surface chemistry, adhesion, friction, and corrosion behavior, as well as for developing advanced materials with tailored surface functionalities.
These are just a few examples of the diverse applications of microtrace substrates across scientific, industrial, and biomedical disciplines. Their versatility and importance in enabling microscale analysis and manipulation make them indispensable tools in various research, development, and quality control applications.
What are the advantages of Microtrace Substrate?
Microtrace substrates offer several advantages across different applications due to their unique properties and capabilities. Some of the key advantages include:
- Precision and Control: Microtrace substrates enable precise manipulation, observation, and analysis of microscopic features, particles, and traces. They provide a controlled environment for sample preparation and experimentation, allowing researchers to study phenomena at the micro- and nanoscale with high accuracy and reproducibility.
- Versatility: Microtrace substrates are compatible with a wide range of analytical techniques and applications, including microscopy, spectroscopy, chromatography, microfluidics, and semiconductor fabrication. Their versatility makes them suitable for diverse research, development, and quality control tasks across scientific, industrial, and biomedical fields.
- Customization: Microtrace substrates can be tailored to specific application requirements by selecting appropriate materials, surface treatments, and geometries. Customization options include modifying surface properties, patterning features, and integrating functional coatings or biomolecules to enhance substrate performance and functionality for particular tasks.
- Enhanced Sensitivity and Detection: By optimizing surface properties and characteristics, microtrace substrates can enhance detection sensitivity and signal-to-noise ratios in analytical techniques such as spectroscopy, mass spectrometry, and biosensing. Tailored surface treatments and coatings may improve analyte adhesion, reduce background interference, and enhance detection limits for trace analysis applications.
- Miniaturization and Integration: Microtrace substrates enable miniaturization and integration of experimental setups, devices, and systems, leading to compact, portable, and high-throughput platforms for chemical analysis, biosensing, and point-of-care diagnostics. Miniaturized substrates facilitate sample handling, reduce reagent consumption, and enable rapid analysis of small sample volumes with minimal waste.
- Compatibility with Automation: Microtrace substrates are compatible with automated handling, imaging, and analysis systems, allowing for streamlined workflows and high-throughput data acquisition. Automated processes such as robotic sample loading, image acquisition, and data analysis enhance efficiency, reproducibility, and scalability in research, manufacturing, and diagnostic applications.
- Cost-Effectiveness: Microtrace substrates offer cost-effective solutions for sample preparation, analysis, and experimentation compared to traditional methods. They enable efficient use of reagents, consumables, and equipment, reducing experimental costs, labor, and time-to-results in research, development, and quality control tasks.
General, the advantages of microtrace substrates stem from their ability to provide precise, versatile, and customizable platforms for microscale analysis and manipulation, enabling breakthroughs in scientific discovery, industrial innovation, and biomedical diagnostics.
How Much Does Microtrace Substrate Cost?
The cost of microtrace substrates can vary widely depending on several factors, including the material, size, complexitate, surface treatment, and quantity required. Here are some general considerations that can influence the cost:
- Material: Different substrate materials have different costs associated with them. For example, glass substrates are often more affordable compared to silicon wafers, which are commonly used in semiconductor manufacturing. Specialty materials such as polymers or ceramics may also vary in cost depending on their properties and manufacturing processes.
- Size and Thickness: The size and thickness of the substrate can impact its cost, with larger and thicker substrates generally being more expensive. Suplimentar, substrates with customized dimensions or non-standard sizes may incur additional manufacturing costs.
- Surface Treatment and Coating: Certain surface treatments or coatings may be applied to microtrace substrates to enhance their performance for specific applications. These treatments can add to the overall cost of the substrate.
- Manufacturing Process: The manufacturing process used to produce the substrates can influence their cost. Techniques such as photolithography, laser micromachining, or chemical etching may involve additional equipment, Materiale, and labor costs.
- Quantity: Bulk orders of microtrace substrates may be eligible for volume discounts, reducing the cost per unit. Conversely, smaller quantities or custom orders may incur higher costs due to setup and handling fees.
- Supplier and Quality: The choice of supplier can also impact the cost of microtrace substrates. Suppliers offering high-quality substrates with consistent performance may charge a premium compared to lower-cost alternatives.
Given these factors, it’s challenging to provide a specific cost range for microtrace substrates without knowing the exact specifications and requirements of the application. Typically, pricing information can be obtained from manufacturers or suppliers specializing in microtrace substrates, who can provide quotes based on the specific needs of the project.
FAQs about Microtrace Substrate
What is a microtrace substrate?
A microtrace substrate is a specialized material used in various scientific and industrial applications for precise sample preparation, observation, and analysis of microscopic features, particles, or traces.
What are the common materials used in microtrace substrates?
Common materials include glass, silicon, polymers, metals, and ceramics. The choice of material depends on the specific requirements of the application, such as optical clarity, mechanical stability, or compatibility with analytical techniques.
What are the advantages of using microtrace substrates?
Advantages include precision and control over sample manipulation, versatility across different applications and analytical techniques, customization options for tailored performance, enhanced sensitivity and detection capabilities, miniaturization and integration for compact systems, compatibility with automation, and cost-effectiveness compared to traditional methods.
How are microtrace substrates manufactured?
The manufacturing process involves material selection, substrate preparation, surface modification, patterning, quality control, and application-specific processing steps. Techniques such as cutting, cleaning, coating, photolithography, and quality testing are used to create substrates optimized for microanalysis and trace detection applications.
What are the applications of microtrace substrates?
Applications include microscopy, microanalysis, and forensics; microelectronics and semiconductor manufacturing; biomedical research and diagnostics; microfluidics and lab-on-a-chip devices; surface science and materials research; and many others where precise observation and analysis of microscopic features or traces are required.
How much do microtrace substrates cost?
The cost can vary widely depending on factors such as material, size, complexitate, surface treatment, quantity, manufacturing process, and supplier. Pricing information can be obtained from manufacturers or suppliers based on specific project requirements.