Flip Chip RF Package Substrates Manufacturer
Flip Chip RF Package Substrates Manufacturer,Flip Chip RF Package Substrates are crucial components in advanced electronic assemblies, particularly suited for high-frequency RF applications. These substrates facilitate the direct attachment of integrated circuits via flip chip technology, where ICs are connected using solder bumps directly onto the substrate. This arrangement minimizes signal paths and reduces parasitic capacitance and inductance, enhancing signal integrity and performance. Commonly made from materials like high-frequency laminates or ceramics, these substrates are tailored for excellent thermal management and electrical properties. They are integral in technologies such as telecommunications, automotive radar, and satellite communications, where reliability and high performance are critical.
What are Flip Chip RF Package Substrates?
Flip chip RF package substrates are specialized substrates used in the assembly of radio frequency (RF) integrated circuits (Ics) through flip chip technology. In flip chip packaging, the IC is flipped upside down and its active side is bonded directly to the substrate using solder bumps, instead of wire bonding used in traditional packaging methods. This configuration offers several advantages such as shorter signal paths, reduced parasitic capacitance and inductance, and better thermal performance.
These substrates are designed to support high-frequency RF applications, providing stable electrical performance and reliability. They typically consist of multiple layers of dielectric materials, such as high-frequency laminate materials or ceramic materials, with patterned conductive traces and vias for interconnections between the IC, other components, and external connections.
Key considerations in the design of flip chip RF package substrates include impedance matching, signal integrity, Managementul termic, and compatibility with high-frequency RF signals. They are commonly used in applications such as wireless communication systems, radar systems, satellite communication, and automotive radar.
Manufacturers often optimize the materials and design of flip chip RF package substrates to meet the specific requirements of different RF applications, balancing performance, cost, and manufacturability. The continued development of flip chip packaging technology and materials enables advancements in RF system miniaturization, performanță, and reliability.
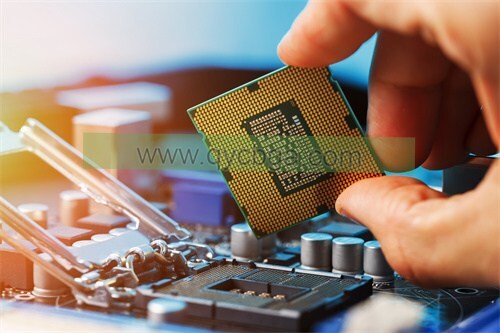
Flip Chip RF Package Substrates Manufacturer
What are the Flip Chip RF Package Substrate Design Guidelines?
Design guidelines for flip chip RF package substrates ensure optimal performance and reliability in high-frequency applications. Here are some key considerations:
- Selectarea materialelor: Choose substrate materials with low dielectric loss, stable electrical properties over frequency, and high thermal conductivity. Common materials include high-frequency laminate (De ex., RO4000 series) or ceramic materials (De ex., Alumină, LTCC).
- Substrate Thickness: Optimize substrate thickness to achieve the desired electrical performance and thermal management. Thinner substrates reduce signal propagation delay and improve thermal dissipation.
- Dielectric Constant (Dk) and Dissipation Factor (Df): Maintain tight control over the dielectric constant and dissipation factor to ensure consistent electrical performance across the RF spectrum.
- Impedance Matching: Design transmission lines and interconnects to match the characteristic impedance of the RF circuitry to minimize signal reflections and maximize power transfer.
- Grounding and Signal Integrity: Implement proper grounding techniques, such as via stitching and solid ground planes, to minimize ground loops and ensure signal integrity.
- Routing and Via Design: Optimize routing and via placement to minimize signal losses, impedance mismatches, and electromagnetic interference (EMI). Use short, straight traces and minimize vias to reduce parasitic capacitance and inductance.
- Managementul termic: Incorporate thermal vias, thermal pads, or metal heat spreaders to dissipate heat generated by the RF IC and maintain optimal operating temperatures.
- Solder Bump Design: Ensure uniform solder bump size and placement for reliable electrical connections between the RF IC and substrate. Consider factors such as solder composition, bump pitch, and bump height.
- Package Size and Shape: Design the package size and shape to meet the mechanical and space constraints of the application while minimizing parasitic capacitance and inductance.
- Reliability Testing: Perform rigorous reliability testing, including thermal cycling, mechanical shock, and vibration tests, to ensure the long-term performance and reliability of the flip chip RF package substrate.
By following these design guidelines, engineers can develop flip chip RF package substrates that meet the stringent requirements of high-frequency RF applications, including wireless communication systems, radar systems, and automotive radar.
What is the Flip Chip RF Package Substrate Fabrication Process?
The fabrication process of flip chip RF package substrates involves several steps to create a substrate that meets the stringent requirements of high-frequency RF applications. Here’s a general overview of the process:
- Pregătirea substratului: The process begins with the preparation of the substrate material, which can be a high-frequency laminate or a ceramic material. The substrate is typically in the form of a sheet or panel.
- Layer Formation: Multiple layers of dielectric material are laminated or deposited onto the substrate to create the desired substrate thickness. These dielectric layers provide insulation between conductive traces and vias.
- Circuit Patterning: Conductive traces, signal lines, Planuri de sol, and other features are patterned onto the substrate using photolithography and etching techniques. This step creates the interconnects necessary for routing RF signals and power throughout the substrate.
- Via Formation: Vias, which are holes filled with conductive material, are formed to provide vertical interconnections between different layers of the substrate. Vias are typically formed using laser drilling or mechanical drilling followed by metallization.
- Aplicarea măștii de lipit: A solder mask is applied to the substrate to protect the conductive traces and vias from oxidation and to define areas for solder attachment. The solder mask is typically applied using a photolithography process.
- Solder Bump Formation: Solder bumps are deposited onto the substrate at the locations where the RF IC will be attached. The solder bumps serve as the electrical and mechanical connection between the IC and the substrate. Solder bump formation can be achieved using various techniques such as stencil printing, solder jetting, or solder ball placement.
- Assembly: The RF IC is flipped upside down and aligned with the solder bumps on the substrate. The assembly is then heated to reflow the solder, forming a reliable electrical connection between the IC and the substrate.
- Testare și inspecție: The assembled flip chip RF package substrate undergoes testing and inspection to ensure that it meets the required electrical and mechanical specifications. Testing may include electrical continuity testing, impedance measurement, thermal cycling, and visual inspection.
- Packaging: Once the flip chip RF package substrate passes testing and inspection, it may be encapsulated or packaged to protect it from environmental factors such as moisture, dust, și stres mecanic. Packaging options include ceramic packages, plastic encapsulation, or conformal coating.
- Final Testing and Quality Assurance: The packaged flip chip RF module undergoes final testing and quality assurance checks to verify its performance and reliability before being shipped to customers.
By following this fabrication process, manufacturers can produce flip chip RF package substrates that meet the stringent requirements of high-frequency RF applications, including wireless communication systems, radar systems, and automotive radar.
How do you manufacture a Flip Chip RF Package Substrate?
Manufacturing a flip chip RF package substrate involves several intricate steps to ensure high performance and reliability. Here’s a detailed overview of the process:
- Substrate Selection: Choose a substrate material suitable for high-frequency RF applications, such as high-frequency laminate materials (De ex., RO4000 series) or ceramic materials (De ex., Alumină, LTCC).
- Pregătirea substratului: Cut the substrate material into appropriate sizes or shapes for the desired application. Clean the substrate surface to remove any contaminants that could affect subsequent processing steps.
- Dielectric Layer Deposition: Deposit multiple layers of dielectric material onto the substrate using techniques such as lamination, chemical vapor deposition (CVD), or physical vapor deposition (PVD). These dielectric layers provide insulation between conductive traces and vias.
- Conductor Patterning: Apply a thin layer of conductive material (De ex., copper) onto the dielectric layers using techniques such as sputtering or electroplating. Pattern the conductive material to create the desired circuitry, including signal lines, Planuri de sol, and pads.
- Photolithography: Apply a photoresist layer onto the conductive material and expose it to UV light through a photomask, which defines the desired circuit pattern. Develop the photoresist to remove the exposed areas, leaving behind the patterned conductive traces and features.
- Gravură: Use chemical etching techniques to remove the unprotected areas of the conductive material, leaving behind the desired circuit pattern on the substrate. Rinse and clean the substrate to remove any remaining photoresist and etchant residues.
- Via Formation: Drill holes (Vias) through the substrate to provide vertical interconnections between different layers. Vias can be formed using techniques such as laser drilling or mechanical drilling, followed by metallization to fill the vias with conductive material.
- Aplicarea măștii de lipit: Apply a solder mask layer onto the substrate to protect the conductive traces and define areas for solder attachment. Use photolithography to pattern the solder mask layer, exposing the areas where solder bumps will be deposited.
- Solder Bump Deposition: Deposit solder bumps onto the exposed areas of the substrate using techniques such as stencil printing, solder jetting, or solder ball placement. The solder bumps serve as the electrical and mechanical connection points for attaching the RF IC.
- Flip Chip Assembly: Align the RF IC with the solder bumps on the substrate and bond them together using a controlled heating process (reflow soldering). This forms a reliable electrical connection between the IC and the substrate.
- Testare și inspecție: Conduct electrical testing and visual inspection to verify the integrity of the flip chip assembly and ensure that it meets the required specifications for high-frequency RF applications.
- Packaging:Optionally, encapsulate the flip chip RF package substrate in a protective housing or package to shield it from environmental factors and mechanical stress.
- Final Testing and Quality Assurance: Perform final testing and quality assurance checks on the packaged flip chip RF module to ensure its performance and reliability before it is shipped to customers.
By following these manufacturing steps with precision and attention to detail, manufacturers can produce flip chip RF package substrates that meet the stringent requirements of high-frequency RF applications, including wireless communication systems, radar systems, and automotive radar.
How much should a Flip Chip RF Package Substrate cost?
The cost of a flip chip RF package substrate can vary significantly depending on several factors including:
- Material: The type of substrate material used (De ex., high-frequency laminate, ceramică) can greatly influence the cost. Ceramic substrates tend to be more expensive than laminate materials due to their superior electrical properties and thermal performance.
- Complexity:The complexity of the substrate design, inclusiv numărul de straturi, circuit density, and features such as blind vias or buried vias, can impact the manufacturing cost. More complex designs typically require additional processing steps and higher precision, which can increase costs.
- Size and Thickness: Larger substrates or substrates with greater thickness may require more material and processing time, leading to higher costs.
- Quality and Reliability Requirements: Substrates intended for critical applications with stringent quality and reliability requirements may undergo additional testing and inspection processes, which can increase manufacturing costs.
- Volume: The volume of substrates being produced can affect the cost per unit. Higher volumes generally allow for economies of scale and lower unit costs.
- Supplier and Manufacturing Location: The choice of supplier and manufacturing location can impact costs due to differences in labor costs, overhead expenses, and shipping fees.
- Additional Services: Additional services such as design consultation, testing, packaging, and customization may incur additional costs.
Given these factors, it’s challenging to provide a specific cost without knowing the detailed specifications and requirements of the flip chip RF package substrate. Însă, in general, flip chip RF package substrates can range in cost from a few dollars to several hundred dollars per unit, with prices typically decreasing with higher volumes and standardization of designs. For precise pricing, it’s advisable to consult with substrate manufacturers or suppliers and provide them with specific requirements for a customized quote.
What is Flip Chip RF Package Substrate base material?
The base material for flip chip RF package substrates can vary depending on the specific requirements of the application, but there are two main categories commonly used: high-frequency laminate materials and ceramic materials.
- High-Frequency Laminate Materials: These materials are composed of layers of fiberglass reinforced with epoxy resin, impregnated with a filler material to provide high-frequency performance. Examples of high-frequency laminate materials include those from the RO4000 series, which are popular choices for RF applications due to their low dielectric loss, stable electrical properties over frequency, and relatively low cost compared to ceramics. High-frequency laminate materials are often used for less demanding RF applications where cost-effectiveness and ease of manufacturing are priorities.
- Ceramic Materials: Ceramică, cum ar fi alumina (Al2O3) and low-temperature co-fired ceramic (LTCC) are also commonly used as base materials for flip chip RF package substrates, especially in applications requiring superior electrical performance, conductivitate termică, and reliability. Ceramics offer excellent electrical properties, such as high dielectric constant (permitting miniaturization) and low loss tangent, making them suitable for high-frequency RF circuits. They also exhibit excellent thermal conductivity, which aids in heat dissipation, and they have high mechanical strength. Însă, ceramic substrates tend to be more expensive and challenging to manufacture compared to laminate materials.
The choice between high-frequency laminate materials and ceramic materials depends on factors such as the desired electrical performance, thermal management requirements, Considerații privind costurile, and manufacturing feasibility for a specific application. Both types of materials have their advantages and limitations, and the selection should be based on a comprehensive assessment of the application’s needs.
Which company makes Flip Chip RF Package Substrates?
Currently, several companies manufacture Flip Chip RF Package Substrates. Some well-known manufacturers include Murata Manufacturing Co., Ltd., Taiyo Yuden Co., Ltd., TDK Corporation, and Rogers Corporation. These companies have rich experience and advanced manufacturing technologies in the high-frequency field, offering various types of substrate materials and packaging solutions to meet the needs of different applications.
For our company, we also have the capability to produce Flip Chip RF Package Substrates. We have advanced manufacturing equipment and a skilled technical team specializing in the design and production of high-frequency electronic devices. Our production process includes the following key steps:
- Material Selection and Procurement: We choose high-quality substrate materials such as high-frequency laminates or ceramic materials to ensure excellent electrical performance and reliability in high-frequency applications.
- Design and Engineering: Our engineering team has extensive experience in custom design according to customer requirements and application scenarios. We verify designs through simulation and experimentation to ensure they meet the requirements of high-frequency circuits, including impedance matching and signal integrity.
- Manufacturing and Processing: We have advanced manufacturing equipment capable of producing multilayer circuit boards, including processes such as chemical processing, photolithography, Gravură, and metallization.
- Soldering and Assembly: We use advanced soldering techniques to bond Flip Chip ICs to the substrate. We ensure soldering quality and stability to guarantee the reliability of electrical connections.
- Testing and Quality Control: Throughout the production process, we conduct rigorous testing and quality control, including electrical testing, reliability testing, and visual inspection, to ensure that products meet customer requirements and standards.
Through the above manufacturing process, our company is able to produce high-quality, high-performance Flip Chip RF Package Substrates to meet the needs of various high-frequency applications. We are committed to providing customized solutions to our customers and continuously improving and innovating to meet evolving market demands.
Care sunt 7 Calitățile unui bun serviciu pentru clienți?
Good customer service is crucial for maintaining customer satisfaction and loyalty. Here are seven key qualities that define excellent customer service:
- Attentiveness: Being fully present and engaged with the customer. This involves listening carefully to understand their needs, Preocupările, and feedback. Attentive service ensures that customers feel valued and understood.
- Effective Communication: Clear and concise communication is essential. This includes both verbal and written communication. Customers should receive information that is easy to understand, and customer service representatives should be able to explain solutions or processes clearly.
- Empatie: Demonstrating empathy means understanding and sharing the feelings of the customer. When customers feel that their concerns are genuinely understood and appreciated, it builds trust and rapport.
- Knowledgeability: Customer service representatives should have a thorough understanding of the products or services offered by their company. This allows them to answer questions accurately, provide helpful information, and resolve issues efficiently.
- Abilități de rezolvare a problemelor: The ability to address and resolve customer issues effectively is a cornerstone of good customer service. This includes being resourceful, thinking on one’s feet, and finding satisfactory solutions quickly.
- Răbdare: Customers may sometimes be frustrated or confused. Patience is critical in these situations to ensure that representatives remain calm and composed, providing support without getting flustered.
- Reacţie: Timely responses to customer inquiries and issues are vital. Customers appreciate quick acknowledgment and swift resolution of their concerns. Being proactive in communication and follow-ups also enhances the customer experience.
Întruchipând aceste calități, customer service teams can create positive interactions that contribute to customer satisfaction and loyalty, ultimately driving the success of the business.
Întrebări frecvente (Întrebări frecvente)
What is a Flip Chip RF Package Substrate?
A Flip Chip RF Package Substrate is a type of substrate used in RF (radio frequency) integrated circuits where the IC is flipped and bonded directly to the substrate using solder bumps. This method reduces signal path lengths, improves thermal management, and enhances electrical performance.
What materials are commonly used for Flip Chip RF Package Substrates?
Common materials include high-frequency laminates such as the RO4000 series and ceramic materials like alumina and low-temperature co-fired ceramic (LTCC). These materials are chosen for their low dielectric loss, stability, and high thermal conductivity.
What are the advantages of using Flip Chip RF Package Substrates?
Advantages include reduced parasitic capacitance and inductance, improved thermal performance, shorter signal paths, better impedance matching, and overall enhanced electrical performance, making them suitable for high-frequency applications.
What applications typically use Flip Chip RF Package Substrates?
They are commonly used in wireless communication systems, radar systems, satellite communication, automotive radar, and other high-frequency RF applications requiring reliable and high-performance packaging.
How do you ensure the reliability of Flip Chip RF Package Substrates?
Reliability is ensured through rigorous testing and quality control measures, including thermal cycling, mechanical shock and vibration tests, electrical continuity tests, and visual inspections. Ensuring uniform solder bump placement and quality also contributes to reliability.
What factors influence the cost of Flip Chip RF Package Substrates?
Costs are influenced by the type of materials used, the complexity of the design, the number of layers, size and thickness of the substrate, quality and reliability requirements, volume of production, and additional services like design consultation and testing.
Can Flip Chip RF Package Substrates be customized for specific applications?
Yes, they can be customized to meet specific application requirements. This includes tailored material selection, customized circuit design, specific thermal management solutions, and precise impedance matching to ensure optimal performance.