Producător de substraturi de aviație
Producător de substraturi de aviație,Aviation Substrate is a high-performance material specifically designed for the aviation industry, combining lightweight properties with high strength. It is primarily used in aircraft structures and interior components, ensuring exceptional performance under high pressure and high-temperature environments. The unique features of Aviation Substrate include outstanding corrosion resistance and fatigue resistance, significantly extending the lifespan of aircraft. Suplimentar, this material offers excellent machinability, meeting the complex design requirements of various aerospace manufacturers. With its environmental friendliness and reliability, Aviation Substrate is gradually becoming a key material in the aviation industry, driving advancements and innovation in modern aviation technology.
What is Aviation Substrate (AS)?
Aviation Substrate (AS) refers to the foundational framework and infrastructure that supports various aviation systems, operations, and technologies. It encompasses a wide range of components, including but not limited to hardware, software, communication networks, sensors, and data processing capabilities. AS serves as the backbone for aviation systems, facilitating the integration of different subsystems and enabling efficient and safe operation of aircraft.
At its core, AS is designed to ensure reliable communication, navigation, and surveillance (CNS) capabilities, which are essential for the functioning of modern aviation. This includes systems such as Automatic Dependent Surveillance-Broadcast (ADS-B), which enables aircraft to broadcast their positions, enhancing situational awareness and air traffic management. AS also includes navigation aids like GPS and ground-based systems, which provide accurate positioning information to pilots and air traffic controllers.
Mai mult, AS incorporates elements of cybersecurity to protect aviation systems from potential threats and ensure the integrity and confidentiality of data transmitted across networks. This is particularly crucial in an era where aviation systems are increasingly interconnected and reliant on digital technologies.
In essence, Aviation Substrate forms the technological foundation upon which the entire aviation ecosystem is built, enabling safe, efficient, and interconnected air transportation systems. Its continued development and evolution are essential for meeting the growing demands and challenges of modern aviation.
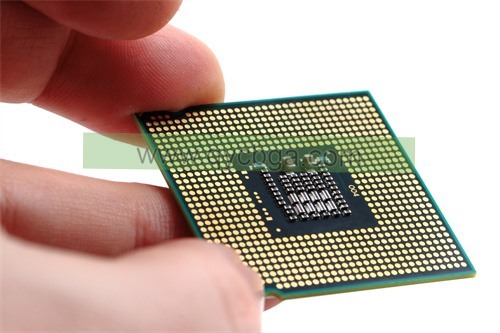
Producător de substraturi de aviație
What are the Aviation Substrate (AS) Design Guidelines?
Aviation Substrate (AS) Design Guidelines encompass a comprehensive set of principles and standards aimed at ensuring the robustness, fiabilitate, and interoperability of aviation infrastructure and systems. These guidelines are crucial for the development, implementation, and maintenance of AS components to support safe and efficient aviation operations. Here are key aspects of AS design guidelines:
- Safety-Criticality: AS design prioritizes safety above all else. Systems must be engineered to withstand failures and ensure redundancy where necessary, minimizing the risk of accidents or incidents.
- Interoperability: AS components must be designed to seamlessly integrate with existing aviation infrastructure and systems. This interoperability facilitates smooth communication and data exchange between different subsystems, enhancing overall efficiency and effectiveness.
- Scalability: AS design guidelines emphasize scalability to accommodate varying levels of demand and future technological advancements. Systems should be flexible enough to adapt to changing requirements without compromising performance or safety.
- Modularity: AS architecture promotes modularity, allowing for the development of reusable components and subsystems. This modular approach streamlines the design process, facilitates maintenance, and enables easier upgrades or replacements of individual elements.
- Standards Compliance: AS design adheres to established industry standards and regulations, such as those set forth by organizations like the International Civil Aviation Organization (ICAO), the Federal Aviation Administration (FAA), and the European Aviation Safety Agency (EASA). Compliance with these standards ensures consistency, interoperability, and safety across aviation systems.
- Cybersecurity: Given the increasing reliance on digital technologies, AS design guidelines include robust cybersecurity measures to safeguard against cyber threats and ensure the integrity and confidentiality of aviation data. This includes encryption, authentication, and intrusion detection mechanisms to protect against unauthorized access and malicious activities.
- Resilience: AS components are designed with resilience in mind, capable of withstanding environmental hazards, cyberattacks, and other disruptive events. Redundancy, failover mechanisms, and contingency plans are incorporated to ensure continuity of operations even in adverse conditions.
- Usability and Human Factors: AS design takes into account human factors and usability considerations to ensure that systems are intuitive, user-friendly, and conducive to safe and efficient human-machine interaction. User interfaces, procedures, and training materials are designed with the end user in mind to minimize errors and enhance operational effectiveness.
- Lifecycle Management: AS design guidelines address the entire lifecycle of aviation infrastructure and systems, from initial development and deployment to ongoing maintenance and eventual decommissioning. This holistic approach ensures that systems remain reliable, up-to-date, and compliant with evolving requirements throughout their operational lifespan.
By adhering to these Aviation Substrate Design Guidelines, stakeholders in the aviation industry can create robust, interoperable, and future-proof infrastructure and systems that support the safe and efficient operation of aircraft worldwide.
What is the Aviation Substrate (AS) Fabrication Process?
The Aviation Substrate (AS) fabrication process involves the manufacturing and assembly of various components and subsystems that form the foundational framework for aviation systems and infrastructure. While the specifics of the fabrication process can vary depending on the type of AS component being produced, as well as the materials and technologies involved, there are several general stages typically involved:
- Design and Engineering: The fabrication process begins with the design and engineering phase, where the specifications, requirements, and functionality of the AS component are defined. This stage may involve computer-aided design (CAD) software, simulations, and prototype development to ensure that the final product meets the desired standards and objectives.
- Selectarea materialelor: Once the design is finalized, appropriate materials are selected for fabrication. These materials must possess the necessary properties such as strength, durability, conductivity, and corrosion resistance, depending on the specific application of the AS component.
- Manufacturing: The actual manufacturing of AS components involves various techniques and processes, including machining, casting, molding, 3D printing, and composite fabrication. These processes transform raw materials into finished components according to the specifications outlined in the design phase.
- Assembly: Once individual components are fabricated, they are assembled into larger subsystems or complete AS structures. This assembly process may involve mechanical fastening, welding, adhesive bonding, or other joining techniques to securely integrate the components and ensure structural integrity.
- Testing and Quality Assurance: Before deployment, AS components undergo rigorous testing to verify their performance, fiabilitate, and compliance with industry standards and regulations. This testing may include functional tests, stress tests, environmental tests, and validation against design specifications.
- Integration: After successful testing and quality assurance, AS components are integrated into the broader aviation infrastructure or systems for which they were designed. This integration process involves connecting the AS components with other subsystems, interfaces, and networks to ensure seamless operation and interoperability.
- Deployment and Maintenance: Once integrated, the AS components are deployed for operational use. Regular maintenance, inspection, and monitoring are essential to ensure the continued functionality and safety of the aviation infrastructure. This may involve preventive maintenance, troubleshooting, and periodic upgrades or replacements as needed.
Throughout the entire fabrication process, adherence to quality control measures, safety standards, and regulatory requirements is paramount to ensure the reliability, safety, and performance of Aviation Substrate components in supporting aviation operations.
How do you manufacture Aviation Substrate (AS)?
Manufacturing Aviation Substrate (AS) involves a multi-step process that includes design, fabrication, adunare, testing, and integration. Here’s a breakdown of each step:
- Design and Engineering: The process begins with designing the AS components based on specifications and requirements. This phase involves conceptualizing the structure, selecting materials, and using computer-aided design (CAD) software to create detailed plans.
- Selectarea materialelor: Materials are chosen based on their properties, such as strength, durability, conductivity, and weight. Common materials include metals like aluminum and titanium, composites, plastics, and specialized alloys.
- Fabrication: The chosen materials are then fabricated into AS components using various manufacturing techniques. These techniques can include machining, casting, forging, 3D printing, or composite layup, depending on the complexity and requirements of the component.
- Assembly: Once individual components are fabricated, they are assembled into larger structures or subsystems. This can involve welding, riveting, adhesive bonding, or other joining methods to securely connect the components.
- Testing and Quality Control: AS components undergo rigorous testing to ensure they meet quality standards and performance requirements. This includes structural testing, material testing, and functional testing to verify integrity, fiabilitate, and compatibility.
- Integration: After passing testing, AS components are integrated into larger aviation systems or infrastructure. This involves connecting them with other components, subsystems, and networks to ensure seamless operation and interoperability.
- Deployment and Maintenance: În cele din urmă, AS components are deployed for operational use in aviation systems. Regular maintenance, inspection, and monitoring are conducted to ensure continued functionality and safety. This may involve preventive maintenance, troubleshooting, and occasional upgrades or replacements.
Pe tot parcursul procesului de fabricație, adherence to industry standards, safety regulations, and quality control measures is essential to produce reliable and high-quality Aviation Substrate components that support safe and efficient aviation operations.
How much should Aviation Substrate (AS) cost?
Determining the cost of Aviation Substrate (AS) can be complex and depends on various factors such as the specific components, Materiale, technologies, complexitate, scale, and quality standards involved. Here are some considerations that can influence the cost:
- Design Complexity: More complex AS components may require sophisticated engineering and design efforts, which can increase development costs.
- Materials: The choice of materials significantly impacts cost. High-quality materials may be more expensive but can offer better performance and durability, while cheaper materials may compromise on quality.
- Manufacturing Processes: The manufacturing techniques used to fabricate AS components can affect costs. Advanced manufacturing methods like additive manufacturing (3D printing) may be more costly upfront but can offer benefits such as reduced waste and faster production times.
- Volume: Economies of scale apply to AS manufacturing, meaning that larger production volumes can often result in lower per-unit costs due to efficiencies in materials purchasing, Procese de fabricație, și cheltuieli generale.
- Testing and Quality Control: Rigorous testing and quality assurance measures are essential for ensuring the reliability and safety of AS components. These activities incur additional costs but are necessary to meet industry standards and regulatory requirements.
- Integration and Deployment: Costs associated with integrating AS components into aviation systems, as well as deployment and installation expenses, should also be considered.
- Maintenance and Lifecycle Costs: Beyond initial acquisition costs, ongoing maintenance, repair, and lifecycle management expenses should be factored into the overall cost of AS. This includes costs associated with upgrades, replacements, and obsolescence management over the lifespan of the components.
- Regulatory Compliance: Compliance with aviation regulations and certification requirements may incur additional costs for testing, documentation, and regulatory approvals.
Given the wide range of factors influencing the cost of Aviation Substrate, it’s challenging to provide a specific figure without more detailed information about the project or components in question. Typically, AS costs are determined through detailed cost estimation and budgeting processes conducted during the project planning and development stages, taking into account all relevant factors and considerations.
What is Aviation Substrate (AS) base material?
The base material used in Aviation Substrate (AS) can vary depending on the specific component, application, and performance requirements. Însă, several common materials are frequently used in the fabrication of AS components due to their desirable properties such as strength, durability, lightweight, and resistance to corrosion. Some of these materials include:
- Aluminum: Aluminum and its alloys are widely used in aviation due to their lightweight nature, high strength-to-weight ratio, and corrosion resistance. They are commonly used in the construction of airframes, wings, and structural components.
- Titanium: Titanium is valued for its exceptional strength, corrosion resistance, and high temperature resistance. It is often used in critical components such as landing gear, engine components, and structural elements where strength and durability are paramount.
- Steel:Certain steel alloys are utilized in aviation for their strength, toughness, and fatigue resistance. They are commonly employed in landing gear components, engine mounts, and structural elements requiring high strength and reliability.
- Composite Materials: Composite materials, such as carbon fiber reinforced polymers (CFRP) and fiberglass, are increasingly used in aviation due to their lightweight properties and high strength-to-weight ratios. They are commonly used in aircraft structures, fuselage components, and aerodynamic surfaces.
- Nickel-based Alloys: Nickel-based alloys are utilized in aviation applications that require high-temperature performance, such as jet engine components. These alloys offer excellent strength, corrosion resistance, and thermal stability at elevated temperatures.
- Copper and Copper Alloys: Copper and its alloys are used in electrical and electronic components within aviation systems due to their excellent electrical conductivity and thermal properties. They are commonly found in wiring, connectors, and electrical conductors.
- Plastics and Polymers: Various plastics and polymers are used in aviation for their lightweight properties, versatility, and resistance to corrosion and chemicals. They are often employed in interior components, insulation, and non-structural elements.
The selection of base materials for AS components is based on factors such as performance requirements, environmental conditions, regulatory compliance, Considerații privind costurile, and manufacturability. Engineers and designers carefully evaluate these factors to choose the most suitable materials for each application, ensuring the safety, fiabilitate, and efficiency of aviation systems.
Which company manufactures Aviation Substrate (AS)?
Currently, many companies play a significant role in manufacturing Aviation Substrate (AS), including major aerospace manufacturers, technology suppliers, and system integrators. These companies possess advanced manufacturing facilities, technical expertise, and industry experience to design, develop, and produce various AS components and systems to support the safe and reliable operations of the aviation industry.
Our company is one of these manufacturers. We have a professional team and advanced manufacturing capabilities to produce various types of Aviation Substrate. We prioritize quality control and innovative research and development to provide customers with high-quality and reliable AS products.
As an AS manufacturer, our capabilities include, but are not limited to:
- Design and Engineering: We have experienced design and engineering teams capable of customizing designs according to customer requirements to develop AS components and systems that meet specifications.
- Material Selection and Processing: We select high-quality materials and utilize advanced processing technologies such as CNC machining, 3D printing, and composite manufacturing to produce various AS components, ensuring their performance and durability.
- Quality Control and Testing: We strictly adhere to quality control standards, monitoring and testing each production process to ensure that AS components meet customer requirements and industry standards.
- Integration and Deployment: We can integrate AS components according to customer requirements and provide deployment and installation support to ensure seamless system operation and connectivity.
- After-Sales Service and Maintenance:We offer comprehensive after-sales service and maintenance support, including system updates, repairs, and troubleshooting, to ensure the long-term stable operation of AS components.
Through our manufacturing capabilities and professional services, customers can obtain high-quality, reliable Aviation Substrate products to meet the needs of the aviation industry and improve operational efficiency. We are committed to establishing long-term partnerships with customers to drive the development and innovation of aviation technology.
Care sunt 7 Calitățile unui bun serviciu pentru clienți?
Good customer service is characterized by several key qualities that contribute to positive customer experiences and satisfaction. Here are seven essential qualities:
- Reacţie: Good customer service is prompt and responsive to customer inquiries, Preocupările, and needs. Customers appreciate timely assistance and solutions to their issues, whether it’s through phone, E-mail, chat, or in-person interactions.
- Empatie: Empathy involves understanding and empathizing with customers’ feelings, Preocupările, and perspectives. Effective customer service representatives listen attentively, show genuine concern, and strive to put themselves in the customer’s shoes to better address their needs.
- Profesionalism: Professionalism entails maintaining a courteous, respectful, and professional demeanor in all customer interactions. Customer service representatives should communicate clearly, remain calm under pressure, and uphold company values and standards at all times.
- Knowledgeability: Good customer service requires a deep understanding of products, services, policies, and procedures. Customer service representatives should be knowledgeable and well-trained to provide accurate information, answer questions, and resolve issues effectively.
- Adaptability: Adaptability is the ability to adjust and tailor the customer service approach to meet the unique needs and preferences of each customer. Flexibility in communication style, problem-solving techniques, and service delivery is essential to accommodate diverse customer situations and personalities.
- Abilități de rezolvare a problemelor: Effective problem-solving skills are crucial for addressing customer issues and resolving conflicts efficiently. Customer service representatives should be resourceful, proactive, and creative in finding solutions to customer problems while keeping the customer’s best interests in mind.
- Follow-Up and Accountability: Good customer service includes following up with customers to ensure that their issues have been resolved satisfactorily and that they are satisfied with the outcome. Suplimentar, taking ownership of customer issues, following through on commitments, and holding oneself accountable for delivering excellent service are vital aspects of building trust and credibility with customers.
Întruchipând aceste calități, organizations can deliver exceptional customer service experiences that foster loyalty, Cuvânt în gură pozitiv, and long-term customer relationships.
Întrebări frecvente
What is Aviation Substrate (AS)?
Aviation Substrate (AS) refers to the foundational framework and infrastructure that supports various aviation systems, operations, and technologies. It encompasses hardware, software, communication networks, sensors, and data processing capabilities essential for safe and efficient aviation operations.
What are the components of Aviation Substrate?
The components of Aviation Substrate can vary but typically include communication systems, navigation aids, surveillance systems, cybersecurity measures, data processing capabilities, and infrastructure for air traffic management.
Why is Aviation Substrate important?
Aviation Substrate is essential for the safe and efficient operation of aviation systems. It provides the technological foundation for communication, navigation, surveillance, and data management, enabling air traffic controllers and pilots to coordinate and navigate aircraft safely within the airspace.
How does Aviation Substrate contribute to aviation safety?
Aviation Substrate enhances safety by providing reliable communication, navigation, and surveillance capabilities, which are critical for maintaining situational awareness, avoiding collisions, and managing air traffic efficiently. It also incorporates cybersecurity measures to protect aviation systems from cyber threats.
Who develops and manufactures Aviation Substrate?
Aviation Substrate is developed and manufactured by various companies, including aerospace manufacturers, technology suppliers, and system integrators. These companies possess expertise in design, engineering, manufacturing, and integration of aviation systems and components.
What are the latest advancements in Aviation Substrate technology?
Advancements in Aviation Substrate technology include the integration of artificial intelligence, machine learning, and automation to enhance the efficiency, fiabilitate, and safety of aviation systems. Suplimentar, improvements in cybersecurity measures and the adoption of satellite-based navigation systems are notable developments.
How can organizations benefit from implementing Aviation Substrate?
Organizations can benefit from implementing Aviation Substrate by improving operational efficiency, enhancing safety and security, reducing delays and congestion in air traffic, and enabling the adoption of advanced technologies to support future aviation needs.