RF 35 Substrate Manufacturer
RF 35 Substrate Manufacturer,RF 35 Substrate is a specialized material utilized in high-frequency RF circuitry for its exceptional electrical properties. Engineered with a low dielectric constant and loss tangent, it ensures minimal signal loss and high signal integrity, crucial for RF applications. Its consistent performance across various frequencies makes it ideal for telecommunications, radar systems, and wireless networking devices. With stringent quality control measures, RF 35 Substrate offers reliability and precision in PCB fabrication. Its versatility allows for customization to meet specific application requirements, establishing it as a cornerstone in the development of advanced RF electronics.
What is RF 35 Substrate?
RF-35 substrate is a type of material commonly used in the construction of printed circuit boards (PCBs) for radio frequency (RF) applications. RF-35 substrates are engineered to have specific electrical properties that make them suitable for high-frequency RF signals, such as low dielectric constant and low loss tangent.
These substrates typically consist of a laminate made of fiberglass reinforced with epoxy resin, combined with a thin layer of copper on one or both sides. The copper layers are used for the etching of circuit traces, which carry the RF signals.
RF-35 substrates offer excellent performance characteristics, including low signal loss, high signal integrity, and good thermal stability. They are often used in applications such as telecommunications, radar systems, wireless networking, and other RF-based electronic devices where high-frequency performance is critical.
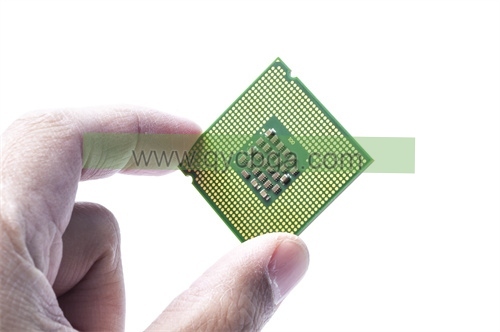
RF 35 Substrate Manufacturer
What are RF 35 Substrate Design Guidelines?
Design guidelines for RF-35 substrates are specific recommendations and considerations that designers should follow when creating printed circuit board (PCB) layouts and circuits using RF-35 substrate material. Here are some general design guidelines for RF-35 substrates:
- Transmission Line Geometry: Maintain controlled impedance transmission lines to ensure signal integrity. Use microstrip or stripline transmission line configurations depending on the specific application requirements.
- Trace Width and Spacing:Determine the appropriate trace width and spacing to achieve the desired impedance. This ensures proper signal propagation and minimizes signal loss.
- Grounding:Ensure adequate grounding by using a solid ground plane on the bottom layer of the PCB. Proper grounding reduces electromagnetic interference (EMI) and improves signal integrity.
- 4. Posicionamento do componente: Place RF components strategically to minimize signal path lengths and impedance mismatches. This helps in reducing signal loss and maintaining RF performance.
- Via Design: Optimize via placement and design to minimize signal reflections and impedance disruptions. Use plated-through vias for signal transition between layers.
- Gerenciamento térmico: Consider thermal management techniques to dissipate heat generated by high-frequency components. Proper thermal vias and heat sinks may be necessary to maintain stable operation.
- Crosstalk Mitigation: Minimize crosstalk between adjacent signal traces by maintaining appropriate spacing and utilizing shielding techniques if necessary.
- Dielectric Thickness: Choose the appropriate dielectric thickness based on the desired electrical properties and mechanical requirements of the PCB.
- Antenna Design: If designing RF antennas on RF-35 substrates, follow antenna design principles such as proper impedance matching, radiation pattern optimization, and ground plane considerations.
- EMI Shielding: Incorporate EMI shielding techniques such as shielding cans or conductive enclosures to minimize interference from external sources and improve overall RF performance.
- Test Points: Include test points for RF signal measurement and testing during PCB manufacturing and assembly processes.
- Capacidade de fabricação: Consider manufacturability aspects such as PCB material availability, fabrication processes, and cost-effectiveness while designing with RF-35 substrates.
These guidelines are not exhaustive and may vary depending on the specific requirements and constraints of each RF design project. It’s essential to consult with RF engineers and PCB layout specialists to optimize the design for performance, fiabilidade, and manufacturability.
What is the RF 35 Substrate Fabrication Process?
The fabrication process for RF-35 substrates involves several steps to produce printed circuit boards (PCBs) with the desired electrical properties for high-frequency RF applications. Here’s a general overview of the RF-35 substrate fabrication process:
- Substrate Preparation: The process begins with preparing the substrate material, which typically consists of fiberglass reinforced with epoxy resin. The substrate material is cut into the desired size and shape, usually as large panels or sheets.
- Copper Cladding:Próximo, a thin layer of copper is applied to one or both sides of the substrate material. This copper cladding serves as the conductive layer for etching circuit traces and components.
- Photoresist Application: A layer of photoresist material is applied to the surface of the copper-clad substrate. The photoresist is sensitive to ultraviolet (UV) light and is used to transfer the circuit pattern onto the copper layer.
- Exposure and Development: The PCB layout, including the desired circuit pattern, is transferred onto the photoresist layer using a photomask and UV exposure. After exposure, the photoresist is developed, leaving behind a pattern of cured resist corresponding to the circuit traces.
- Etching: The exposed copper areas not protected by the cured photoresist are etched away using an appropriate etchant solution. This process removes the unwanted copper, leaving behind the desired circuit traces on the substrate.
- Strip and Clean: The remaining photoresist is stripped away, leaving the bare copper traces on the substrate surface. The PCB is then cleaned to remove any residues or contaminants from the fabrication process.
- Perfuração: Holes for component leads and vias are drilled into the PCB as needed. These holes are plated through with copper to provide electrical connections between layers.
- Acabamento de superfície:A surface finish may be applied to the exposed copper traces to improve solderability and prevent oxidation. Os acabamentos de superfície comuns incluem HASL (hot air solder leveling), ENIG (electroless nickel immersion gold), or OSP (conservante orgânico de soldabilidade).
- Silkscreen and Legend: If required, a silkscreen layer containing component designators, logos, or other markings may be applied to the PCB surface. This layer is typically printed using a screen printing process.
- Final Inspection: The finished PCBs undergo a final inspection to ensure they meet quality standards and specifications. Isso pode incluir testes elétricos, visual inspection, and dimensional checks.
- Panelization and Separation: PCBs are often fabricated in panel form to improve manufacturing efficiency. Após a fabricação, the panels are separated into individual PCBs using methods such as routing, scoring, or milling.
- Controle de qualidade: Throughout the fabrication process, quality control measures are implemented to ensure the integrity and reliability of the finished PCBs. This includes monitoring process parameters, inspecting materials, and testing PCBs for functionality and performance.
These steps outline a typical fabrication process for RF-35 substrates, but variations may exist depending on specific manufacturing technologies, equipment, and requirements of the final application.
How do you manufacture RF 35 Substrate?
Manufacturing RF-35 substrate involves a series of processes to create the specialized material used in printed circuit board (PCB) fabrication for high-frequency RF applications. Here’s an overview of the typical manufacturing process for RF-35 substrate:
- Seleção de materiais: The manufacturing process begins with the selection of high-quality raw materials. RF-35 substrate typically consists of fiberglass cloth impregnated with epoxy resin.
- Prepreg Formation: Fiberglass cloth is impregnated with uncured epoxy resin to create prepreg sheets. These prepreg sheets are partially cured to achieve a semi-solid state, making them easier to handle during subsequent processing steps.
- Lamination: Multiple layers of prepreg sheets are stacked alternately with thin copper foil sheets. The copper foil serves as the conductive layer for the PCB traces. The stack is then placed into a lamination press, where heat and pressure are applied to bond the layers together into a single composite material.
- Curing: The laminated stack undergoes a curing process to fully cross-link the epoxy resin and cure the substrate material. This step ensures the substrate achieves its final mechanical and thermal properties.
- Perfuração: Holes for vias and component leads are drilled into the cured substrate material using precision drilling equipment. These holes will later be plated through with copper to provide electrical connections between layers.
- Copper Deposition: Thin layers of copper are deposited onto the surface of the substrate material through a process such as electroplating or sputtering. This copper deposition creates a conductive surface for the subsequent etching of circuit traces.
- Etching: A photolithography process is used to transfer the PCB layout onto the copper-clad substrate. A photoresist material is applied to the copper surface, exposed to UV light through a photomask, and developed to create a patterned resist mask. The exposed copper areas not protected by the resist are then etched away using an appropriate etchant solution, leaving behind the desired circuit traces.
- Acabamento de superfície: After etching, the exposed copper surfaces are cleaned and treated with a surface finish to improve solderability and prevent oxidation. Os acabamentos de superfície comuns incluem HASL (hot air solder leveling), ENIG (electroless nickel immersion gold), or OSP (conservante orgânico de soldabilidade).
- Controle de qualidade: Durante todo o processo de fabricação, quality control measures are implemented to ensure the integrity and reliability of the RF-35 substrate material. This includes monitoring process parameters, inspecting materials, and testing samples for mechanical, electrical, and thermal properties.
- Inspeção Final e Embalagem: Once the RF-35 substrate material is manufactured, it undergoes final inspection to ensure it meets quality standards and specifications. The material is then packaged and shipped to PCB manufacturers for use in fabricating high-frequency RF circuits.
Each step in the manufacturing process requires precise control of parameters such as temperature, pressure, and chemical composition to produce RF-35 substrate material with the desired electrical properties and performance characteristics.
How much should RF 35 Substrate cost?
The cost of RF-35 substrate can vary depending on various factors such as the manufacturer, quantity ordered, specifications, and market demand. Typically, RF-35 substrate is considered a specialized material designed for high-frequency RF applications, and as such, it tends to be more expensive compared to standard PCB substrate materials.
Several factors contribute to the cost of RF-35 substrate:
- Material Cost: The cost of raw materials used in manufacturing RF-35 substrate, including fiberglass cloth, epoxy resin, and copper foil, influences the overall cost.
- Processo de fabricação: The complexity of the manufacturing process, including lamination, curing, copper deposition, etching, and surface finishing, affects the cost. More intricate processes may require specialized equipment and skilled labor, contributing to higher manufacturing costs.
- Quality Standards: Adherence to stringent quality standards and certifications, such as ISO, UL, or RoHS compliance, can increase manufacturing costs but may be necessary to meet customer requirements and ensure product reliability.
- Customization: Customization of RF-35 substrate to meet specific customer requirements, such as unique thicknesses, copper weights, or surface finishes, may incur additional costs.
- Quantity Ordered: Economies of scale apply in manufacturing, meaning that larger quantities of RF-35 substrate typically result in lower per-unit costs due to bulk discounts and optimized production processes.
- Market Demand: Supply and demand dynamics in the market can influence the pricing of RF-35 substrate. High demand or limited availability of specialized materials may lead to higher prices.
- Supplier Relationships: Established relationships with reliable suppliers can sometimes result in better pricing for RF-35 substrate through negotiated contracts or volume discounts.
Given these factors, the cost of RF-35 substrate can range from a few dollars per square foot for standard-grade material to tens of dollars or more per square foot for high-performance, custom-configured substrates.
It’s essential for buyers to consider not only the upfront cost but also factors such as quality, fiabilidade, and long-term performance when evaluating the overall value of RF-35 substrate for their specific applications. Adicionalmente, obtaining quotes from multiple suppliers and carefully comparing pricing, lead times, and quality assurances can help ensure competitive pricing and satisfactory outcomes.
What is RF 35 Substrate Base Material?
RF-35 substrate base material typically refers to the foundational material used in the construction of printed circuit boards (PCBs) designed for high-frequency RF (radio frequency) applications. The base material of RF-35 substrate consists of a combination of fiberglass cloth and epoxy resin.
- Fiberglass Cloth: Fiberglass cloth, often referred to as fiberglass reinforcement, serves as the primary structural component of the substrate material. It provides mechanical strength, dimensional stability, and resistance to warping or flexing during PCB fabrication and operation. Fiberglass cloth is composed of fine glass fibers woven together to form a flexible and durable sheet.
- Epoxy Resin: Epoxy resin is a thermosetting polymer that acts as the binding agent in the substrate material. It fills the gaps between fiberglass fibers and forms a solid matrix when cured. Epoxy resin provides adhesion between layers, electrical insulation, and protection against environmental factors such as moisture and chemicals. It also contributes to the overall rigidity and stability of the PCB.
The combination of fiberglass cloth and epoxy resin results in a substrate material with specific electrical, mecânico, and thermal properties tailored for RF applications. RF-35 substrate is engineered to have low dielectric constant (permittivity), tangente de baixa perda, and consistent electrical performance across a wide range of frequencies. These properties make RF-35 substrate suitable for high-frequency RF circuitry, such as those found in telecommunications, radar systems, wireless networking, and other RF-based electronic devices.
In summary, the base material of RF-35 substrate comprises fiberglass cloth reinforced with epoxy resin, forming a durable and high-performance substrate for RF PCB applications.
Which company produces RF 35 Substrate?
There are many companies that produce RF 35 substrates, and some of them specialize in PCB materials for high-frequency RF applications. These companies typically have advanced manufacturing technology and extensive experience to provide high-performance RF 35 substrates that meet customer requirements.
As part of our company, we also have the capability to manufacture RF 35 substrates. We have advanced production equipment and technology, as well as an experienced team, to produce high-quality RF 35 substrates that meet the demands of high-frequency RF applications.
Our manufacturing process is carefully designed and strictly controlled to ensure that RF 35 substrates have stable electrical performance and reliable mechanical properties. We select high-quality fiberglass cloth and epoxy resin as base materials and use advanced lamination and curing processes to bond them into sturdy and durable substrates. We use precision machining equipment to ensure the flatness of the PCB surface and adjust the thickness and dielectric constant of the substrate precisely to meet customer-specific requirements.
We are committed to continuously improving our technical capabilities and production capacity to meet the evolving market demand. With a professional R&D team, we can customize various types of RF 35 substrates according to customer needs, including different sizes, thicknesses, dielectric constants, and surface treatments.
In addition to product quality, we also prioritize cooperation and communication with customers. We provide timely technical support and after-sales service to ensure customer satisfaction. Our goal is to become a trusted partner for customers, fostering mutual development and success.
In summary, we have the capability to manufacture RF 35 substrates and are committed to providing customers with high-quality, reliable, and customized solutions. If you are interested in our products or have any requirements, please feel free to contact us, and we will be happy to assist you.
Quais são os 7 Qualidades de um bom atendimento ao cliente?
Good customer service is essential for building positive relationships with customers and ensuring their satisfaction. Here are seven qualities that characterize excellent customer service:
- Responsividade: Responding promptly to customer inquiries, requests, and concerns demonstrates attentiveness and a commitment to addressing their needs in a timely manner. Whether it’s answering phone calls, replying to emails, or assisting customers in person, being responsive shows that you value their time and are dedicated to providing assistance.
- Empatia: Showing empathy involves understanding and acknowledging the customer’s emotions, Preocupações, and perspectives. Empathetic customer service representatives listen actively, validate the customer’s feelings, and demonstrate genuine care and concern. By empathizing with customers, you can build rapport, alleviate frustrations, and create a positive experience.
- Communication Skills:Effective communication is key to conveying information clearly and comprehensively, as well as understanding the customer’s needs and expectations. Good communication involves active listening, asking clarifying questions, and providing relevant information or solutions in a concise and understandable manner. Clear communication helps to prevent misunderstandings and ensures that customers feel informed and valued.
- Profissionalismo: Maintaining professionalism in interactions with customers establishes credibility, trust, and confidence in the company’s products or services. Professional customer service representatives exhibit politeness, courtesy, and respectfulness in all interactions, regardless of the customer’s demeanor or situation. Professionalism also entails adhering to company policies, maintaining confidentiality, and handling sensitive issues with discretion and tact.
- Habilidades de resolução de problemas: Effective problem-solving involves identifying and addressing customer issues or concerns promptly and efficiently. Customer service representatives should be resourceful, proactive, and solution-oriented, striving to resolve problems to the customer’s satisfaction. By demonstrating initiative and creativity in finding solutions, you can enhance the customer’s experience and foster loyalty.
- Conhecimento do produto: Having a thorough understanding of the company’s products or services enables customer service representatives to provide accurate information, offer helpful recommendations, and address customer inquiries effectively. Product knowledge instills confidence in customers and enhances their trust in the company’s expertise and reliability.
- Follow-Up and Follow-Through: Following up with customers after resolving their issues or fulfilling their requests demonstrates a commitment to their satisfaction and reinforces the relationship. Whether it’s checking in to ensure that the problem has been resolved satisfactorily or seeking feedback on their experience, follow-up communication shows that you value their feedback and are dedicated to continuous improvement. Adicionalmente, following through on promises or commitments made to customers builds trust and reliability, fostering long-term relationships.
Ao incorporar essas qualidades, organizations can deliver exceptional customer service experiences that leave a lasting positive impression and cultivate customer loyalty and advocacy.
Perguntas frequentes (Frequently Asked Questions)
What are the key properties of RF 35 substrate?
RF 35 substrate typically exhibits low dielectric constant, tangente de baixa perda, and consistent electrical performance across a wide range of frequencies. These properties are essential for minimizing signal loss and maintaining signal integrity in RF circuits.
What are the applications of RF 35 substrate?
RF 35 substrate is commonly used in RF electronics and telecommunications equipment, such as radar systems, wireless communication devices, satellite communication systems, and microwave circuits. It is also utilized in industries such as aerospace, automotive, and medical devices where high-frequency RF performance is critical.
How does RF 35 substrate differ from standard PCB substrates?
RF 35 substrate is engineered specifically for high-frequency RF applications, whereas standard PCB substrates may not possess the necessary electrical properties required for RF signal transmission. RF 35 substrate typically has lower dielectric constant and loss tangent compared to standard substrates, enabling better RF performance.
What factors should be considered when selecting RF 35 substrate?
When selecting RF 35 substrate, factors such as dielectric constant, loss tangent, thermal stability, dimensional stability, cost, and manufacturability should be considered. It’s important to choose a substrate that meets the electrical and mechanical requirements of the RF circuit while also being compatible with the manufacturing process.
Can RF 35 substrate be customized for specific applications?
Yes, RF 35 substrate can be customized to meet the specific requirements of different RF applications. This customization may include adjustments to the substrate thickness, dielectric constant, copper thickness, surface finish, and other parameters to optimize performance for the intended application.
What are some common challenges in working with RF 35 substrate?
Common challenges in working with RF 35 substrate include ensuring proper impedance matching, minimizing signal loss, controlling electromagnetic interference (EMI), and achieving consistent RF performance across different frequencies. Careful design and manufacturing practices are necessary to address these challenges effectively.