What is 3D IC Package Substrate?
3D IC Fabricante de substrato de pacote,3D IC (Integrated Circuit) package substrate is an innovative technology enabling stacked semiconductor dies in a single package, enhancing performance and density. This substrate facilitates vertical integration of chips, reducing interconnect length and improving signal speed. By stacking chips, 3D IC substrates optimize space utilization and enhance thermal management. Commonly made from materials like silicon interposers or advanced laminates, they offer reliable electrical performance and mechanical stability. Widely used in high-performance computing, artificial intelligence, and data centers, 3D IC package substrates drive advancements in semiconductor packaging, enabling smaller form factors and higher processing power in electronic devices.
A 3D IC package substrate is a key component in three-dimensional integrated circuit (3D IC) technology. In traditional integrated circuits (ICs), electronic components are arranged side by side on a single layer. Contudo, in 3D IC technology, multiple layers of ICs are stacked vertically to increase functionality and performance while reducing the overall footprint.
The 3D IC package substrate serves as a platform for connecting and interconnecting the stacked IC layers. It provides electrical connections between the different layers of ICs, as well as between the ICs and external components such as the printed circuit board (PCB) or other system components.
These substrates are designed to handle the increased heat dissipation and electrical demands associated with 3D IC integration. They often incorporate advanced materials and manufacturing techniques to achieve the necessary performance, fiabilidade, and thermal management requirements.
Geral, the 3D IC package substrate plays a critical role in enabling the integration of multiple IC layers in a compact and efficient manner, thereby facilitating the development of high-performance electronic systems.
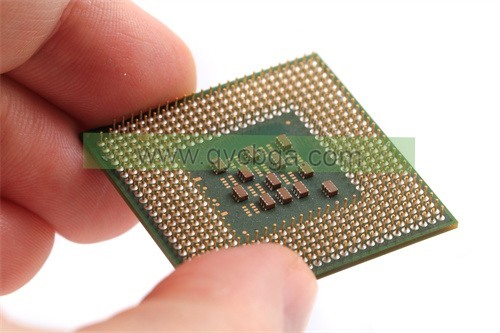
3D IC Fabricante de substrato de pacote
3D IC Package Substrate design Reference Guide.
Designing a 3D IC package substrate requires careful consideration of various factors to ensure optimal performance, fiabilidade, and manufacturability. Here’s a reference guide covering key aspects of 3D IC package substrate design:
- Seleção de materiais: Choose substrate materials with suitable electrical, thermal, and mechanical properties. Common materials include organic substrates (e.g., FR-4), ceramic substrates, and advanced materials like silicon interposers or glass interposers.
- Interconnection Technology: Select appropriate interconnection technologies such as through-silicon vias (TSVs), microbumps, solder balls, or copper pillars. Each technology has its advantages and limitations in terms of pitch, density, e confiabilidade.
- Routing Architecture: Design an efficient routing architecture to facilitate high-speed signal transmission and minimize signal integrity issues such as crosstalk and impedance mismatch. Consider the placement and routing of TSVs, microbumps, and signal traces to optimize electrical performance.
- Power Delivery Network (PDN): Design a robust power delivery network to ensure adequate power distribution and thermal management. Incorporate power planes, decoupling capacitors, and thermal vias to mitigate power noise and heat dissipation issues.
- Integridade do sinal (SI) and Electromagnetic Interference (EMI): Perform SI and EMI analysis to identify and mitigate potential signal integrity and electromagnetic compatibility issues. Utilize signal and power integrity simulation tools to optimize the substrate layout and stackup.
- Gerenciamento térmico: Implement effective thermal management techniques to dissipate heat generated by the stacked IC layers. Incorporate thermal vias, heat spreaders, and thermal interface materials to enhance heat dissipation and thermal conductivity.
- Package Size and Form Factor: Determine the appropriate package size and form factor based on system requirements, including space constraints, electrical performance goals, and integration complexity.
- Considerações de confiabilidade: Address reliability concerns such as mechanical stress, Ciclagem térmica, and solder joint fatigue. Perform reliability simulations and testing to validate the substrate design under various operating conditions.
- Manufacturability and Cost: Optimize the substrate design for manufacturability and cost-effectiveness. Consider factors such as substrate fabrication processes, yield optimization, and assembly techniques to streamline production and minimize manufacturing costs.
- Compliance and Standards: Ensure compliance with industry standards and regulations governing substrate materials, interconnection technologies, and electrical performance specifications.
By carefully addressing these design considerations, engineers can develop 3D IC package substrates that meet the performance, fiabilidade, and cost requirements of advanced electronic systems. Collaboration with substrate suppliers, semiconductor manufacturers, and system integrators is essential to leverage expertise and resources throughout the design process.
What are the materials used in 3D IC Package Substrate?
Several materials are used in the construction of 3D IC package substrates, each offering unique properties suited to specific requirements. Here are some common materials used:
- Organic Substrates: Organic substrates such as FR-4 (Flame Retardant 4) are widely used in traditional PCBs and can also be employed in 3D IC package substrates. FR-4 is cost-effective, lightweight, and offers good electrical insulation properties. Contudo, it may have limitations in terms of thermal conductivity and reliability at higher temperatures.
- Ceramic Substrates: Ceramic substrates, typically made of alumina (Al2O3) or aluminum nitride (AlN), are known for their excellent thermal conductivity, mechanical strength, e confiabilidade. Ceramic substrates are well-suited for applications requiring high power dissipation and thermal management.
- Silicon Interposers: Silicon interposers are silicon wafers with through-silicon vias (TSVs) that provide vertical interconnections between stacked IC layers. Silicon interposers offer high electrical performance, low parasitic capacitance, and compatibility with standard semiconductor processes. They are often used in high-performance applications such as advanced microprocessors and memory devices.
- Glass Interposers: Glass interposers are fabricated using glass substrates with TSVs for vertical interconnections. Glass interposers offer advantages such as low cost, high electrical insulation, and compatibility with large-scale manufacturing processes. They are suitable for applications requiring high-density interconnects and signal integrity.
- Polymer Interposers: Polymer interposers are made of polymer materials such as polyimide or liquid crystal polymer (LCP). Polymer interposers offer flexibility, low cost, and ease of processing compared to ceramic and silicon substrates. They are suitable for applications requiring moderate electrical performance and interconnect density.
- Metal Substrates: Metal substrates such as copper or aluminum can be used as carriers or heat spreaders in 3D IC packaging. Metal substrates offer high thermal conductivity and mechanical strength, making them suitable for thermal management in high-power applications.
- Flexible Substrates: Flexible substrates made of polyimide or other flexible materials are used in applications requiring bendable or stretchable electronics. Flexible substrates offer versatility and conformability to irregular shapes, making them suitable for wearable devices and flexible displays.
The choice of substrate material depends on various factors including electrical performance requirements, thermal management needs, cost considerations, and specific application demands. Designers must carefully evaluate these factors to select the most appropriate substrate material for their 3D IC packaging design.
How is 3D IC Package Substrate manufactured?
Manufacturing 3D IC package substrates involves several intricate processes aimed at creating a robust substrate capable of accommodating multiple stacked IC layers and facilitating efficient electrical connections. Here’s an overview of the typical manufacturing steps:
- Substrate Fabrication: The process begins with the fabrication of the substrate material. Depending on the chosen material (e.g., organic, ceramic, silicon, glass), this may involve techniques such as lamination, deposition, or casting to create the substrate’s base layer.
- Via Formação: For substrates requiring vertical interconnections (e.g., silicon interposers, glass interposers), through-silicon vias (TSVs) or through-glass vias (TGVs) are formed. This process involves etching or drilling holes through the substrate material and filling them with conductive material such as copper or tungsten to establish electrical pathways between stacked IC layers.
- Surface Preparation: The substrate surface is prepared for subsequent processes such as metallization and bonding. This may involve cleaning, surface activation, and chemical treatment to ensure optimal adhesion and compatibility with subsequent layers.
- Metallization: Metal layers are deposited onto the substrate surface to create conductive traces, pads, and interconnects. Techniques such as physical vapor deposition (PVD) or chemical vapor deposition (CVD) are used to deposit metals such as copper, aluminum, or gold onto the substrate surface.
- Dielectric Deposition: Dielectric layers are deposited onto the substrate surface to insulate and protect the underlying metallization layers. Dielectric materials such as polyimide, silicon dioxide, or benzocyclobutene (BCB) are commonly used for this purpose. These layers may also incorporate vias for vertical interconnections.
- Interconnect Formation: The process of forming interconnects between the substrate and the stacked IC layers begins. This may involve techniques such as flip-chip bonding, soldering, or thermo-compression bonding to establish electrical connections between the substrate and the ICs.
- Assembly and Stacking: Once the substrate is prepared, IC chips are assembled onto the substrate surface using precision placement techniques. Multiple IC layers may be stacked on top of each other, with interconnections established through TSVs or other vertical interconnect technologies.
- Encapsulation and Packaging: The assembled substrate and stacked IC layers are encapsulated and packaged to protect them from environmental factors such as moisture, dust, and mechanical stress. This may involve techniques such as molding, underfilling, or encapsulation with epoxy resins or polymers.
- Testing and Quality Assurance: The completed 3D IC package substrates undergo rigorous testing and quality assurance procedures to ensure they meet electrical performance, fiabilidade, and durability requirements. Isso pode incluir testes elétricos, Ciclagem térmica, and mechanical stress testing.
- Inspeção Final e Embalagem: Once testing is completed, the finished 3D IC package substrates are inspected for defects and packaged for shipment to customers or further assembly into electronic systems.
Durante todo o processo de fabricação, stringent process controls, quality assurance measures, and advanced metrology techniques are employed to ensure the reliability, performance, and consistency of the 3D IC package substrates. Collaboration among substrate manufacturers, semiconductor foundries, and assembly partners is often required to optimize the manufacturing process and meet the demanding requirements of advanced electronic systems.
The Application area of 3D IC Package Substrate
The application areas of 3D IC package substrates span a wide range of industries and technologies, driven by the need for enhanced performance, miniaturization, and integration capabilities. Some key application areas include:
- High-Performance Computing (HPC): In HPC systems, such as supercomputers and data centers, 3D IC package substrates enable the integration of multiple processors, memory modules, and accelerators in a compact form factor. This results in increased computational power, reduced latency, and improved energy efficiency.
- Telecommunications and Networking: 3D IC package substrates are used in telecommunications and networking equipment to enhance data processing and routing capabilities. By stacking multiple ICs vertically, these substrates enable the development of high-speed routers, switches, and base stations with improved throughput and scalability.
- Consumer Electronics: In consumer electronics devices such as smartphones, tablets, and wearables, 3D IC package substrates enable the integration of multiple functionalities in a compact and lightweight form factor. This allows for the development of feature-rich devices with improved performance, battery life, and form factor.
- Automotive Electronics: In the automotive industry, 3D IC package substrates are utilized in advanced driver assistance systems (ADAS), infotainment systems, and engine control units (ECUs). These substrates enable the integration of sensors, processors, and memory modules, leading to enhanced safety, eficiência, and connectivity in vehicles.
- Medical Devices: In medical devices and equipment, 3D IC package substrates enable the development of compact and portable solutions for diagnostic imaging, patient monitoring, and therapeutic applications. By integrating multiple functions and sensors, these substrates facilitate the development of advanced medical technologies with improved accuracy and reliability.
- Aerospace and Defense: In aerospace and defense applications, 3D IC package substrates are used in radar systems, avionics, and communication systems. These substrates enable the integration of complex electronics in space-constrained environments, leading to improved performance, fiabilidade, and ruggedness.
- Industrial Automation: In industrial automation and control systems, 3D IC package substrates enable the development of compact and energy-efficient solutions for process control, robotics, and machine vision. By integrating multiple sensors, actuators, and processing units, these substrates enhance productivity, flexibility, and efficiency in manufacturing environments.
- Emerging Technologies: 3D IC package substrates are also being explored for emerging technologies such as Internet of Things (IoT), artificial intelligence (AI), and augmented reality (AR)/virtual reality (VR). These substrates enable the integration of diverse functionalities and sensors, paving the way for innovative applications and services in various industries.
Geral, the application areas of 3D IC package substrates continue to expand as technology advancements drive the demand for higher performance, integration, and miniaturization in electronic systems across diverse industries.
What are the advantages of 3D IC Package Substrate?
3D IC package substrates offer several advantages over traditional 2D packaging solutions, making them increasingly popular for advanced electronic systems. Some of the key advantages include:
- Increased Performance: By vertically stacking multiple IC layers, 3D IC package substrates reduce interconnect lengths and enable shorter signal pathways. This leads to reduced signal propagation delays, lower power consumption, and higher operating speeds, resulting in improved overall system performance.
- Enhanced Integration: 3D IC package substrates facilitate the integration of multiple functionalities, such as processors, memory, sensors, and RF components, within a compact form factor. This enables the development of highly integrated systems-on-chip (SoCs) and system-in-package (SiP) solutions with reduced footprint and improved functionality.
- Higher Bandwidth and Connectivity: Vertical integration in 3D IC package substrates allows for denser interconnects and increased bandwidth between stacked IC layers. This enables faster data transfer rates, improved data throughput, and enhanced connectivity, making them ideal for high-speed communication and data processing applications.
- Improved Power Efficiency: With shorter interconnect lengths and reduced parasitic capacitance, 3D IC package substrates offer improved power efficiency compared to traditional 2D packaging solutions. This leads to lower power consumption, reduced heat generation, and extended battery life in portable and battery-powered devices.
- Gerenciamento térmico: 3D IC package substrates facilitate efficient thermal management by providing a shorter thermal path between the stacked IC layers and external heat sinks. This helps dissipate heat more effectively, mitigating thermal hotspots and improving overall system reliability and longevity.
- Miniaturization and Form Factor Flexibility: By stacking IC layers vertically, 3D IC package substrates enable miniaturization of electronic systems and components, allowing for smaller and more compact designs. This flexibility in form factor enables the development of innovative products for various applications, including wearables, IoT devices, and automotive electronics.
- Heterogeneous Integration: 3D IC package substrates support heterogeneous integration, allowing for the integration of different types of ICs, technologies, and materials within a single package. This enables the co-packaging of diverse functionalities, such as digital, analog, RF, and MEMS components, to meet the specific requirements of complex electronic systems.
- Cost Savings and Yield Improvement: While initial manufacturing costs may be higher for 3D IC package substrates due to the complexity of fabrication processes, they can result in cost savings over the product lifecycle. This is achieved through reduced component count, simplified assembly processes, and improved yield due to smaller form factors and higher integration levels.
Geral, the advantages of 3D IC package substrates, including improved performance, integration, power efficiency, and form factor flexibility, make them an attractive choice for a wide range of advanced electronic applications.
How Much Does 3D IC Package Substrate Cost?
The cost of 3D IC package substrates can vary significantly depending on various factors such as the chosen substrate material, manufacturing complexity, design requirements, and volume production considerations. Here are some key factors that influence the cost:
- Substrate Material: Different substrate materials have different costs associated with their production. For example, organic substrates (e.g., FR-4) are generally more cost-effective compared to ceramic, silicon, or glass substrates, which may require more sophisticated manufacturing processes and materials.
- Manufacturing Complexity: The complexity of the manufacturing process can impact the cost of 3D IC package substrates. Processes such as via formation, metallization, interconnect formation, and stacking may require specialized equipment, materiais, and expertise, which can contribute to higher manufacturing costs.
- Design Requirements: The complexity and sophistication of the substrate design, including features such as via density, trace routing, interconnect pitch, and thermal management solutions, can influence the cost of fabrication. More complex designs may require additional manufacturing steps and materials, leading to higher costs.
- Volume Production: The economies of scale associated with volume production can significantly impact the cost of 3D IC package substrates. Higher production volumes typically lead to lower per-unit costs due to efficiencies in manufacturing processes, materials procurement, and overhead expenses.
- Technology Node and Yield Rates: The adoption of advanced semiconductor processes and technologies, such as smaller feature sizes and higher interconnect densities, may increase manufacturing costs initially. Contudo, as these technologies mature and yield rates improve, the cost per unit may decrease over time.
- Supplier Relationships and Supply Chain Factors: The relationships with substrate suppliers, semiconductor foundries, assembly partners, and other supply chain stakeholders can influence the overall cost of 3D IC package substrates. Collaborative partnerships and strategic sourcing initiatives may help optimize costs and improve competitiveness.
- Market Dynamics and Competition: Market demand, industry trends, and competitive dynamics can also impact the pricing of 3D IC package substrates. Pricing may fluctuate based on supply and demand dynamics, competitive pressures, and technological advancements within the industry.
Geral, while it’s challenging to provide a specific cost figure for 3D IC package substrates due to the numerous variables involved, it’s essential for stakeholders to carefully evaluate cost considerations alongside performance, fiabilidade, and other factors when selecting substrate materials and manufacturing processes for their applications.
FAQs about 3D IC Package Substrate
What is a 3D IC package substrate?
A 3D IC package substrate is a component used in three-dimensional integrated circuit (3D IC) technology. It serves as a platform for connecting and interconnecting multiple stacked IC layers, facilitating high-performance electronic systems in a compact form factor.
How does a 3D IC package substrate differ from traditional IC packaging?
Unlike traditional IC packaging, which involves arranging electronic components side by side on a single layer, 3D IC package substrates enable the vertical stacking of multiple IC layers. This allows for increased functionality, performance, and integration while reducing the overall footprint.
What are the advantages of using a 3D IC package substrate?
Some advantages of 3D IC package substrates include increased performance, enhanced integration, improved power efficiency, better thermal management, and flexibility in form factor design.
What materials are used in 3D IC package substrates?
Common materials used in 3D IC package substrates include organic substrates (e.g., FR-4), ceramic substrates, silicon interposers, glass interposers, polymer interposers, and metal substrates.
How are 3D IC package substrates manufactured?
The manufacturing process for 3D IC package substrates involves substrate fabrication, via formação, surface preparation, metallization, dielectric deposition, interconnect formation, assembly and stacking, encapsulation and packaging, testing and quality assurance, and final inspection and packaging.
What are the applications of 3D IC package substrates?
3D IC package substrates find applications in various industries and technologies, including high-performance computing, telecomunicações, consumer electronics, Eletrônica automotiva, medical devices, aerospace and defense, industrial automation, and emerging technologies such as IoT, AI, and AR/VR.
How much does a 3D IC package substrate cost?
The cost of 3D IC package substrates can vary depending on factors such as substrate material, manufacturing complexity, design requirements, volume production considerations, technology node, yield rates, supplier relationships, and market dynamics.
What are some key considerations when designing with 3D IC package substrates?
Important design considerations include material selection, interconnection technology, routing architecture, power delivery network (PDN), Integridade do sinal (SI) e interferência eletromagnética (EMI), Gerenciamento térmico, package size and form factor, reliability considerations, manufacturability, compliance and standards.