Fabricante de PCB de micro-ondas / microtraço
Fabricante de PCB de micro-ondas / microtraço,Microwave/Microtrace PCBs are specialized printed circuit boards meticulously engineered to operate efficiently at microwave frequencies, typically ranging from 300 MHz to 300 Ghz. These PCBs are crafted with meticulous attention to detail, employing advanced materials and manufacturing techniques to ensure optimal performance in high-frequency applications. They feature controlled impedance traces, microstrip or stripline transmission lines, and low dielectric loss substrates such as ceramic-filled PTFE laminates like Rogers or DuPont. Designed for applications demanding precision and reliability, Microwave/Microtrace PCBs find widespread use in telecommunications, radar systems, satellite communication, microwave antennas, RF/microwave amplifiers, and even microwave ovens. Their ability to maintain signal integrity, minimize losses, and withstand the rigors of high-frequency environments makes them indispensable in modern technology. From intricate design considerations to specialized fabrication processes, these PCBs exemplify the pinnacle of engineering prowess, empowering innovations across a spectrum of industries reliant on high-frequency electronics.
What is a Microwave/Microtrace PCB?
A Microwave PCB, sometimes referred to as Microtrace PCB, is a type of printed circuit board designed to operate at microwave frequencies. These frequencies typically range from about 300 MHz to 300 Ghz. Microwave PCBs are used in various applications, including telecommunications, radar systems, satellite communication, and microwave ovens.
These PCBs are specially engineered to handle the unique challenges posed by high-frequency signals, such as signal loss, Correspondência de impedância, e interferência eletromagnética (EMI). They are constructed using specialized materials that offer low dielectric loss and consistent electrical properties across a wide range of frequencies. Common materials used in microwave PCBs include ceramic-filled PTFE (polytetrafluoroethylene) substrates like Rogers, DuPont, and Taconic.
Adicionalmente, microwave PCBs may incorporate features like controlled impedance traces, microstrip or stripline transmission lines, and plated-through holes (PTHs) filled with conductive materials to ensure signal integrity and minimize losses.
Geral, the design and fabrication of microwave PCBs require precise engineering and manufacturing techniques to meet the stringent performance requirements of high-frequency applications.
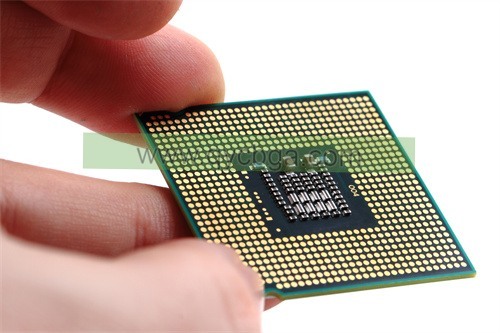
Fabricante de PCB de micro-ondas / microtraço
What are the Microwave/Microtrace PCB Design Guidelines?
Designing microwave or microtrace PCBs requires careful attention to several key guidelines to ensure optimal performance at high frequencies. Here are some important considerations:
- Substrate Selection: Choose a substrate material with low dielectric loss and consistent electrical properties over a wide range of frequencies. Common substrate materials include ceramic-filled PTFE (e.g., Rogers, DuPont) and specialized high-frequency laminates.
- Trace Geometry: Design transmission line traces (e.g., microstrip or stripline) with controlled impedance to match the characteristic impedance of the system. Maintain consistent trace width and spacing to minimize signal loss and impedance mismatches.
- Grounding: Ensure a solid ground plane beneath signal traces to provide return paths for high-frequency signals and minimize electromagnetic interference (EMI). Use vias to connect signal layers to the ground plane for effective grounding.
- Posicionamento do componente: Place high-frequency components, such as amplifiers, filters, and antennas, close to each other to minimize signal path lengths and reduce parasitic effects. Maintain adequate separation between components to avoid interference.
- Via Design: Use high-frequency vias with minimal parasitic effects, such as plated-through holes (PTHs) filled with conductive materials or via-in-pad designs. Avoid stubs and use back-drilling techniques to remove excess via length.
- Impedance Matching: Implement impedance matching techniques, such as tapered traces, stubs, or matching networks, to ensure smooth signal transitions between components and transmission lines, minimizing reflections and signal loss.
- Crosstalk Mitigation: Maintain proper spacing between adjacent signal traces to minimize crosstalk. Use ground planes and signal shielding techniques to isolate sensitive signals from interference.
- Signal Integrity Analysis: Perform simulations and impedance calculations using electromagnetic simulation software to verify the electrical performance of the design. Analyze signal integrity metrics such as insertion loss, return loss, and eye diagrams.
- Gerenciamento térmico: Consider heat dissipation requirements for high-power components and thermal effects on substrate materials. Design adequate heat sinks or thermal vias to dissipate heat efficiently and prevent overheating.
- Capacidade de fabricação: Ensure that the design is manufacturable with the chosen fabrication techniques, considering factors such as trace width, spacing, and minimum feature sizes. Consult with PCB manufacturers experienced in high-frequency PCB fabrication.
Following these guidelines can help ensure the successful design and performance of microwave or microtrace PCBs for high-frequency applications.
What is the Microwave/Microtrace PCB Fabrication Process?
The fabrication process for microwave or microtrace PCBs involves several specialized steps to ensure the precise manufacture of high-frequency circuitry. Here’s a general overview of the fabrication process:
- Substrate Preparation: The process begins with preparing the substrate material, typically a high-frequency laminate such as ceramic-filled PTFE (e.g., Rogers, DuPont). The substrate is cleaned and inspected to ensure its quality and consistency.
- Copper Cladding: A thin layer of copper foil is laminated onto one or both sides of the substrate to form the conductive layers of the PCB. The copper foil is typically treated to improve adhesion and etching properties.
- Laser Drilling and Mechanical Drilling: Holes for through-hole vias and component mounting are drilled using precision drilling techniques. For high-frequency applications, laser drilling is often used to achieve smaller via sizes and better positional accuracy.
- Padronização de Circuito: A photoresist layer is applied to the copper-clad substrate, and the desired circuit patterns are transferred onto the substrate using photolithography. Ultraviolet (UV) light is used to expose the photoresist through a photomask, defining the traces and pads.
- Etching: The exposed copper areas not protected by the photoresist are chemically etched away, leaving behind the desired circuit traces and pads. Etching is controlled to achieve precise trace widths and spacing according to design specifications.
- Surface Finishing: Surface finishing processes such as immersion gold, electroless nickel immersion gold (ENIG), or immersion silver may be applied to the exposed copper surfaces to improve solderability, resistência à corrosão, and electrical performance.
- Via Formação: Through-hole vias are plated with conductive material to establish electrical connections between different layers of the PCB. Techniques such as electroplating or chemical deposition are used to fill the vias with copper or other conductive materials.
- Aplicação de máscara de solda: A solder mask layer is applied over the copper traces to protect them from oxidation and facilitate soldering during assembly. Openings are created in the solder mask layer to expose the pad areas for component attachment.
- Silkscreen Printing: Identifying markings, such as component designators, logos, and polarity indicators, are applied to the PCB surface using silkscreen printing for ease of assembly and identification.
- Testing and Inspection: The fabricated PCBs undergo electrical testing, including continuity checks, impedance measurements, and insulation resistance tests, to ensure they meet design specifications. Visual inspection is also conducted to identify any defects or irregularities.
- Routing and Panelization: After testing and inspection, individual PCBs may be routed out of the panel or remain as part of a larger panel for ease of handling during assembly.
- Inspeção Final e Embalagem: Once the PCBs pass all quality checks, they are inspected one final time before being packaged and shipped to the customer for assembly.
Throughout the fabrication process, strict quality control measures are implemented to ensure the reliability and performance of the microwave or microtrace PCBs for high-frequency applications.
How do you manufacture a Microwave/Microtrace PCB?
Manufacturing a microwave or microtrace PCB involves specialized techniques and processes tailored to meet the stringent requirements of high-frequency applications. Here’s a detailed overview of the manufacturing process:
- Design Preparation: O processo começa com o projeto do layout do PCB usando software especializado de design de PCB. Designers must adhere to high-frequency design guidelines and consider factors such as trace geometry, Correspondência de impedância, e integridade do sinal.
- Seleção de materiais: Selecting the appropriate substrate material is critical for high-frequency PCBs. Common materials include ceramic-filled PTFE (polytetrafluoroethylene) laminates such as Rogers, DuPont, or Taconic. The substrate material should have low dielectric loss, propriedades elétricas consistentes, e excelente estabilidade térmica.
- Panelization: Multiple PCB designs are combined into a single panel for efficient manufacturing. Panelization helps optimize material usage and streamline the fabrication process.
- Substrate Preparation: The substrate material is cleaned and inspected to ensure its quality and uniformity. Any surface contaminants or irregularities are removed to facilitate proper adhesion of subsequent layers.
- Copper Cladding: Thin layers of copper foil are laminated onto one or both sides of the substrate to form the conductive layers of the PCB. The copper foil is typically treated to enhance adhesion and etching properties.
- Padronização de Circuito: The desired circuit patterns are transferred onto the copper-clad substrate using photolithography. A layer of photoresist is applied over the copper surface, exposed to ultraviolet (UV) light through a photomask, and developed to define the circuit traces and pads.
- Etching: Chemical etching is used to selectively remove the exposed copper areas, leaving behind the desired circuit traces and pads. Etching is carefully controlled to achieve precise trace widths and spacing according to the design specifications.
- Via Formação: Holes for through-hole vias and component mounting are drilled using precision drilling techniques. Laser drilling may be employed for high-density via arrays or fine-pitch components. The vias are then plated with conductive material to establish electrical connections between different layers of the PCB.
- Surface Finishing: Surface finishing processes such as immersion gold, electroless nickel immersion gold (ENIG), or immersion silver are applied to the exposed copper surfaces to improve solderability, resistência à corrosão, and electrical performance.
- Aplicação de máscara de solda: A solder mask layer is applied over the copper traces to protect them from oxidation and facilitate soldering during assembly. Openings are created in the solder mask layer to expose the pad areas for component attachment.
- Silkscreen Printing: Identifying markings, such as component designators, logos, and polarity indicators, are applied to the PCB surface using silkscreen printing for ease of assembly and identification.
- Testing and Inspection: The fabricated PCBs undergo electrical testing, including continuity checks, impedance measurements, and insulation resistance tests, to ensure they meet design specifications. Visual inspection is also conducted to identify any defects or irregularities.
- Routing and Separation: After testing and inspection, individual PCBs are routed out of the panel or remain as part of a larger panel for ease of handling during assembly.
- Inspeção Final e Embalagem: Once the PCBs pass all quality checks, they undergo a final inspection before being packaged and shipped to the customer for assembly.
Durante todo o processo de fabricação, stringent quality control measures are implemented to ensure the reliability and performance of the microwave or microtrace PCBs for high-frequency applications.
How much should a Microwave/Microtrace PCB cost?
The cost of a microwave or microtrace PCB can vary widely depending on several factors, including the complexity of the design, the size of the PCB, the choice of materials, the manufacturing processes involved, and the quantity ordered. Here are some key factors that can influence the cost:
- Complexity of the Design: PCBs with intricate layouts, high-density components, and fine-pitch traces may require more sophisticated manufacturing techniques, which can increase the cost.
- Seleção de materiais: High-frequency PCB materials such as ceramic-filled PTFE laminates are more expensive than standard FR-4 materials. The choice of substrate material can significantly impact the overall cost.
- Manufacturing Processes: Specialized processes such as laser drilling, controlled impedance matching, and surface finishing can add to the manufacturing cost. Adicionalmente, advanced fabrication techniques required for high-frequency PCBs may incur additional expenses.
- Quantity: Economies of scale often apply in PCB manufacturing, meaning that larger production quantities typically result in lower per-unit costs. Ordering larger quantities can help reduce the cost per PCB.
- Turnaround Time: Expedited manufacturing services or quick-turn PCB fabrication may come at a premium price. Longer lead times generally allow for more cost-effective manufacturing.
- Additional Services: Additional services such as PCB assembly, teste, and inspection may incur extra costs depending on the specific requirements of the project.
- Supplier Selection: The choice of PCB manufacturer or supplier can impact the overall cost. Different suppliers may offer varying pricing structures and levels of service.
As a rough estimate, the cost of a microwave or microtrace PCB can range from tens to hundreds of dollars per unit, with more complex and specialized designs typically costing more. It’s advisable to obtain quotes from multiple PCB manufacturers and suppliers to compare pricing and ensure that the chosen supplier can meet the requirements of the project within the budget constraints.
What is the Microwave/Microtrace PCB base material?
The base material used for microwave or microtrace PCBs is a critical aspect of their design, as it directly impacts the electrical performance and reliability of the circuitry, especially at high frequencies. The most commonly used base materials for these types of PCBs are specialized high-frequency laminates, which typically consist of a substrate material reinforced with woven glass fibers impregnated with a polymer resin.
One of the most popular types of base material for microwave PCBs is PTFE (polytetrafluoroethylene), often referred to as Teflon. PTFE-based laminates offer excellent electrical properties, low dielectric loss, and stable performance over a wide range of frequencies, making them well-suited for high-frequency applications. Adicionalmente, PTFE-based materials have high thermal stability and are resistant to environmental factors such as moisture and temperature fluctuations.
Within the category of PTFE-based laminates, there are several specific material grades offered by various manufacturers, each with its own set of properties tailored to different application requirements. Some commonly used PTFE-based laminates for microwave PCBs include:
- Corporação Rogers: Rogers manufactures a range of high-frequency laminates, including the RO4000 series and the RT/duroid series, which are widely used in microwave and RF applications.
- DuPont: DuPont offers materials such as the Pyralux LF series and the Teflon PTFE-based substrates, known for their high performance and reliability in high-frequency circuits.
- Taconic: Taconic produces materials like the Taconic RF series, which are designed for high-frequency applications requiring tight tolerance control and excellent signal integrity.
These materials typically feature a PTFE-based core with copper foil bonded to one or both sides to form the conductive layers of the PCB. The choice of base material depends on factors such as frequency range, signal integrity requirements, Gerenciamento térmico, and cost considerations. Designers should carefully select the appropriate base material to ensure optimal performance and reliability of microwave or microtrace PCBs for their specific application.
Which company manufactures Microwave/Microtrace PCBs?
There are many companies specializing in the production of microwave/microtrace PCBs, among which some leading companies include Rogers Corporation, DuPont, Taconic in the United States, and Nippon Mektron in Japan. These companies have rich experience and expertise in high-frequency circuit design and manufacturing, providing high-performance PCB materials and solutions for various high-frequency applications.
Our company is also a professional manufacturer of microwave/microtrace PCBs. We have advanced production equipment and a skilled technical team capable of meeting the strict requirements of customers for high-frequency circuits. We utilize advanced materials and manufacturing processes, such as high-frequency PTFE substrates, precise photolithography, Perfuração a laser, and controlled impedance matching, to ensure that the produced PCBs have excellent signal integrity, low loss, and stability.
We are committed to providing customized solutions to our customers, designing and manufacturing PCBs according to their requirements and specifications. With our experienced engineering team and quality management team, we offer comprehensive technical support and services. Whether it’s for communication, radar, satellite communication, or microwave oven applications, we can provide customers with high-quality and reliable microwave/microtrace PCB products.
If you have any needs or questions about microwave/microtrace PCB manufacturing, please feel free to contact us. We will provide you with the best services and solutions to ensure the success of your project.
Quais são os 7 Qualidades de um bom atendimento ao cliente?
Good customer service is essential for building strong relationships with customers and ensuring their satisfaction. Aqui estão sete qualidades de um bom atendimento ao cliente:
- Responsividade: Um bom atendimento ao cliente envolve atender prontamente às perguntas dos clientes, Preocupações, e solicitações. Being responsive demonstrates that you value the customer’s time and are committed to assisting them in a timely manner.
- Empatia: Empathy involves understanding and empathizing with the customer’s emotions, Preocupações, and needs. It’s important to listen actively, acknowledge the customer’s feelings, and show genuine concern for their well-being.
- Comunicação clara: Effective communication is crucial for providing good customer service. Communicate clearly and concisely, using language that the customer can easily understand. Provide accurate information and avoid jargon or technical terms that may confuse the customer.
- Problem-solving Skills: Good customer service representatives possess strong problem-solving skills to address customer issues and resolve conflicts effectively. They should be able to think critically, analyze situations, and offer practical solutions that meet the customer’s needs.
- Profissionalismo: Professionalism involves maintaining a courteous and respectful demeanor at all times, mesmo em situações desafiadoras. Treat customers with respect, remain calm and composed, and refrain from engaging in confrontational or unprofessional behavior.
- Conhecimento do produto: Good customer service representatives have a deep understanding of the products or services they are supporting. They should be well-informed about product features, functionalities, and troubleshooting procedures to provide accurate and helpful assistance to customers.
- Follow-up and Follow-through: After resolving a customer issue or inquiry, it’s important to follow up to ensure that the customer’s needs have been met satisfactorily. Follow-through involves taking ownership of the customer’s request or concern and seeing it through to resolution, even if it requires additional time or effort.
Ao incorporar essas qualidades, businesses can deliver exceptional customer service experiences that foster loyalty, trust, and satisfaction among their customer base.
Perguntas frequentes
What are Microwave/Microtrace PCBs?
Microwave/Microtrace PCBs are printed circuit boards specifically designed to operate at microwave frequencies, typically ranging from 300 MHz to 300 Ghz. They are engineered with specialized materials and features to ensure optimal performance in high-frequency applications.
What are the key features of Microwave/Microtrace PCBs?
Key features of Microwave/Microtrace PCBs include controlled impedance traces, microstrip or stripline transmission lines, low dielectric loss substrates (such as ceramic-filled PTFE), and precise manufacturing techniques to minimize signal loss and impedance mismatches.
What are the applications of Microwave/Microtrace PCBs?
Microwave/Microtrace PCBs are used in various high-frequency applications, including telecommunications, radar systems, satellite communication, microwave antennas, RF/microwave amplifiers, and microwave ovens.
What materials are used in Microwave/Microtrace PCBs?
Common materials used in Microwave/Microtrace PCBs include ceramic-filled PTFE laminates (e.g., Rogers, DuPont), which offer low dielectric loss, propriedades elétricas consistentes, and thermal stability required for high-frequency applications.
How are Microwave/Microtrace PCBs manufactured?
The manufacturing process for Microwave/Microtrace PCBs involves specialized techniques such as controlled impedance matching, Perfuração a laser, precise etching, and surface finishing to ensure optimal performance at high frequencies.
What are the design considerations for Microwave/Microtrace PCBs?
Design considerations for Microwave/Microtrace PCBs include trace geometry, Aterramento, Posicionamento de componentes, via design, Correspondência de impedância, crosstalk mitigation, Análise de integridade de sinal, Gerenciamento térmico, and manufacturability.
How much do Microwave/Microtrace PCBs cost?
The cost of Microwave/Microtrace PCBs varies depending on factors such as the complexity of the design, size of the PCB, choice of materials, manufacturing processes, and quantity ordered. It’s advisable to obtain quotes from multiple suppliers to compare pricing.