HF Radar PCB Manufacturer
HF Radar PCB Manufacturer,HF Radar PCBs are specialized circuit boards designed for high-frequency radar systems. These PCBs are engineered to handle the rigorous demands of radar applications, offering exceptional signal integrity and reliability. They feature advanced materials with high thermal conductivity and low dielectric loss, ensuring efficient transmission and reception of radar signals. HF Radar PCBs support precise signal processing and data acquisition necessary for radar functions like target detection, navigation, and surveillance. Their robust construction and optimized design make them ideal for military, aerospace, maritime, and weather monitoring radar systems where accuracy and performance are critical.
What is an HF Radar PCB?
HF Radar PCB (High-Frequency Radar Printed Circuit Board) is specifically designed for high-frequency radar applications, commonly used in military, aerospace, meteorological monitoring, and civilian radar systems. Its primary function is to support the transmission and processing of high-frequency signals for target detection, tracking, and imaging.
HF Radar PCBs have specific design requirements to ensure performance at high frequencies. These requirements include low loss, low latency, and high stability. Since high-frequency signals experience significant attenuation during propagation, the choice of materials is crucial. Common materials include polytetrafluoroethylene (PTFE), fluorinated polyimide (FEP), and other low-loss dielectrics to minimize signal loss and improve transmission efficiency.
Adicionalmente, the manufacturing process of HF Radar PCBs demands high precision to ensure the accuracy and stability of signal pathways. This may involve miniaturized designs, ultra-fine line manufacturing, and multi-layer board lamination techniques to meet high-frequency and high-bandwidth requirements.
HF Radar PCBs are widely used in various applications, including weather forecasting, air traffic management, ocean monitoring, and military reconnaissance. As technology advances and radar capabilities evolve, the design and manufacturing techniques for HF Radar PCBs continue to progress to meet increasing performance demands and application scenarios.
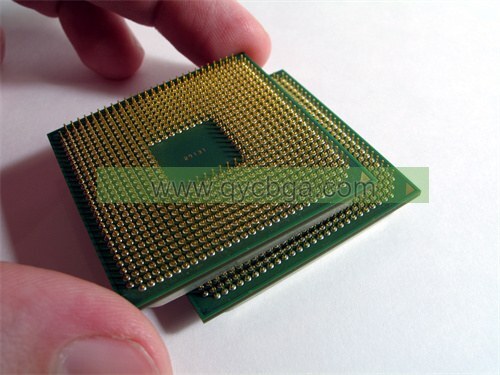
HF Radar PCB Manufacturer
What are the HF Radar PCB Design Guidelines?
Designing HF Radar PCBs involves several critical guidelines to ensure optimal performance. Here are some key considerations:
- Seleção de materiais: Use low-loss dielectric materials, such as PTFE or advanced ceramics, to minimize signal attenuation. Ensure the material has suitable thermal and mechanical properties for radar applications.
- Layer Stack-Up: Optimize the layer stack-up to minimize signal interference. Multi-layer designs can help separate power and ground planes from signal layers.
- Impedance Control: Maintain consistent characteristic impedance (typically 50 Ohms) throughout the PCB to prevent signal reflections. Use controlled impedance traces and differential pairs where applicable.
- Trace Width and Spacing: Design trace widths and spacing based on the frequency of operation and material properties. Utilize calculators to determine appropriate dimensions for controlled impedance.
- Minimize Via Usage: Limit the number of vias, as they can introduce inductance and degrade high-frequency performance. When necessary, use blind or buried vias to reduce signal path length.
- Grounding: Implement solid grounding strategies, such as ground planes, to reduce electromagnetic interference (EMI) and ensure stable signal return paths.
- Gerenciamento térmico: Consider thermal dissipation in the design to prevent overheating of components, particularly in high-power applications.
- EMI Shielding: Use proper shielding techniques, such as metal enclosures or ground planes, to mitigate interference from external sources.
- Simulation and Testing: Utilize simulation tools for signal integrity and electromagnetic compatibility analysis during the design phase. Perform thorough testing on prototypes to validate performance.
- Manufacturing Considerations: Collaborate with the PCB manufacturer to ensure that design specifications align with their fabrication capabilities, especially for high-frequency applications.
Following these guidelines can significantly enhance the performance and reliability of HF Radar PCBs in various applications.
What is the HF Radar PCB Fabrication Process?
The fabrication process for HF Radar PCBs involves several key steps to ensure high precision and performance. Here’s an overview:
- Design Preparation: Begin with detailed PCB design using CAD software, ensuring that all design guidelines (e.g., trace width, impedance control) are followed. Export the design files in standard formats like Gerber or ODB++.
- Seleção de materiais: Choose appropriate substrate materials, typically low-loss dielectrics such as PTFE or other high-frequency materials, which minimize signal attenuation and maintain performance.
- Laser Drilling: Use laser drilling to create microvias or through-holes in the substrate. This method allows for precise and clean holes necessary for high-frequency applications.
- Copper Deposition: Apply a thin layer of copper to the substrate using processes like electroplating or vacuum deposition. This layer will form the conductive pathways.
- Photoresist Application: Coat the substrate with photoresist, a light-sensitive material. This layer will help define the circuit patterns during exposure.
- Exposure and Development: Expose the photoresist to UV light through a photomask that outlines the desired circuit pattern. After exposure, develop the photoresist to reveal the copper areas to be etched away.
- Etching: Perform chemical etching to remove unwanted copper, leaving only the desired circuit traces. This step must be precise to ensure integrity in high-frequency applications.
- Surface Finishing: Apply surface finishes such as ENIG (Ouro de imersão em níquel eletrolítico) or OSP (Organic Solderability Preservative) to enhance solderability and protect copper traces from oxidation.
- Testing and Inspection: Conduct electrical testing and visual inspections to identify any defects or irregularities. This step may involve automated optical inspection (AOI) or electrical continuity testing.
- Assembléia: Once tested, the PCBs can be assembled with components through techniques such as surface mount technology (SMT) or through-hole soldering, depending on design specifications.
- Final Testing: Perform additional testing on the fully assembled PCB to ensure it meets all operational and performance specifications, particularly for high-frequency behavior.
This fabrication process ensures that HF Radar PCBs are produced with high accuracy and reliability, essential for their performance in radar applications.
How do you manufacture an HF Radar PCB?
Manufacturing an HF Radar PCB involves a series of precise steps to ensure optimal performance and reliability. Here’s a structured overview:
- Fase de projeto: Use CAD software to create the PCB layout, adhering to design guidelines for high-frequency applications. Ensure proper impedance control, trace width, and spacing.
- Seleção de materiais: Choose suitable low-loss dielectric materials, such as PTFE or ceramic substrates, which minimize signal attenuation.
- Perfuração: Employ laser drilling to create microvias or through-holes. This method offers high precision, essential for high-frequency signal paths.
- Copper Layering: Apply a thin layer of copper on the substrate using processes like electroplating. This layer will form the conductive traces.
- Photoresist Application: Coat the substrate with photoresist, a light-sensitive material that helps define circuit patterns during exposure.
- Exposure and Development: Expose the photoresist to UV light through a photomask that outlines the circuit design. Develop the photoresist to reveal areas of copper to be retained.
- Etching Process: Use chemical etching to remove excess copper, leaving behind the desired circuit traces. Precision is crucial to maintain high-frequency performance.
- Acabamento de superfície: Apply surface finishes, such as ENIG or OSP, to enhance solderability and protect copper from oxidation.
- Inspection and Testing: Conduct visual inspections and electrical testing, including automated optical inspection (AOI) and continuity testing, to ensure circuit integrity.
- Component Assembly: Assemble the PCB with components using surface mount technology (SMT) or through-hole methods, depending on the design.
- Final Testing: Perform additional tests on the fully assembled PCB to validate its functionality and performance, focusing on high-frequency characteristics.
By following these steps, manufacturers can produce HF Radar PCBs that meet the stringent demands of radar applications, ensuring reliable operation and performance.
How much should an HF Radar PCB cost?
The cost of an HF Radar PCB can vary significantly based on several factors, incluindo:
- Material Costs:High-frequency materials like PTFE or ceramics are generally more expensive than standard FR4.
- Complexidade: More complex designs with intricate layouts, multiple layers, or specialized features (like microvias) will increase costs.
- Size: Larger PCBs typically cost more due to increased material usage and manufacturing time.
- Volume: Production volumes can impact unit pricing. Higher quantities often result in lower per-unit costs.
- Surface Finishes: Advanced finishes like ENIG or selective plating add to the overall cost.
- Testing and Inspection: Additional costs may be incurred for rigorous testing and quality assurance processes.
As a rough estimate, small quantities of HF Radar PCBs might range from $100 Para $500 each, while larger production runs could lower the cost to between $20 and $100 per unit, depending on the specifics. For an accurate quote, it’s best to consult with PCB manufacturers who can provide tailored pricing based on your design requirements.
What is HF Radar PCB base material?
HF Radar PCBs typically use specialized base materials designed for high-frequency performance. The most common materials include:
- PTFE (Polytetrafluoroethylene): Known for its low dielectric constant and low loss tangent, PTFE is highly effective at minimizing signal attenuation and maintaining performance at high frequencies.
- Ceramic Materials: These materials offer excellent thermal stability and low loss characteristics. They are often used in high-performance applications requiring high reliability.
- FR-4 (with modifications): While standard FR-4 is not ideal for high-frequency applications, modified versions with lower loss characteristics can be used for certain HF applications, though they generally do not perform as well as PTFE or ceramics.
- FEP (Fluorinated Ethylene Propylene): Similar to PTFE, FEP is another fluoropolymer that offers good dielectric properties and is sometimes used in HF applications.
- LCP (Liquid Crystal Polymer):LCPs are used for their low dielectric loss and dimensional stability, making them suitable for high-frequency PCBs.
These materials are chosen based on their electrical properties, mechanical strength, thermal stability, and compatibility with the manufacturing processes required for HF Radar applications.
Which company makes HF Radar PCBs?
Many companies specialize in manufacturing HF Radar PCBs, possessing extensive experience and expertise in high-frequency PCB design and production. Here are some well-known manufacturers of HF Radar PCBs:
- Shin-Etsu Chemical:This company offers high-performance polytetrafluoroethylene (PTFE) substrates widely used in HF Radar PCBs.
- Mitsubishi Electric: Known for its high-quality circuit boards, particularly in aerospace and military applications that require high-frequency circuits.
- International PCB (IPC): This company focuses on providing high-frequency PCB solutions for military and communication sectors, with years of industry experience.
- Hitech PCB: Specializing in the design and manufacturing of high-frequency PCBs, serving various high-tech applications, including radar systems.
- ACE PCB: Focused on high-frequency and high-speed PCBs, offering customized solutions to meet customer needs.
In the production of HF Radar PCBs, the selection of appropriate substrates is crucial. These materials must possess low loss, low dielectric constant, and good thermal stability. Common materials include PTFE, ceramics, and LCP.
Our company also has the capability to produce HF Radar PCBs. We utilize advanced manufacturing equipment and technologies to ensure high precision and reliability. Our design team has rich experience and can provide customized solutions based on specific customer requirements. In terms of material selection, we use high-performance PTFE and ceramic substrates to ensure signal integrity and stability in radar systems operating at high frequencies.
Adicionalmente, we emphasize quality control throughout the production process, ensuring that every step—from design to finished product—meets strict standards and customer expectations. Our clients span military, aerospace, meteorological monitoring, and civilian sectors, earning a solid reputation for outstanding product quality and timely customer service.
If you need design or manufacturing of HF Radar PCBs, please feel free to contact us. We are committed to providing you with professional services and support.
Quais são os 7 Qualidades de um bom atendimento ao cliente?
The seven qualities of good customer service are:
- Responsividade: Quickly addressing customer inquiries and concerns shows that you value their time and needs.
- Empatia: Understanding and relating to customers’ feelings and situations helps build rapport and trust.
- Knowledge: Having a deep understanding of products or services allows representatives to provide accurate information and solutions.
- Politeness: Courteous and respectful communication enhances the overall customer experience and reflects well on the brand.
- Habilidades de resolução de problemas: Effectively resolving issues and offering solutions demonstrates commitment to customer satisfaction.
- Comunicação clara: Conveying information clearly and concisely helps avoid misunderstandings and ensures customers feel informed.
- 7. Follow-Up: Checking in with customers after an interaction shows care and helps address any lingering concerns, reinforcing a positive relationship.
Perguntas frequentes
What materials are used for HF Radar PCBs?
Common materials include PTFE (polytetrafluoroethylene), ceramic substrates, and modified FR-4. These materials are chosen for their low dielectric loss and stability at high frequencies.
What is the typical manufacturing process for HF Radar PCBs?
The manufacturing process includes design preparation, Seleção de material, drilling, copper layering, photoresist application, exposure and development, etching, acabamento superficial, inspection, and final assembly.
How do I choose the right manufacturer for HF Radar PCBs?
Look for manufacturers with experience in high-frequency applications, advanced manufacturing capabilities, quality certifications, and a proven track record of delivering reliable products.
What are the challenges in designing HF Radar PCBs?
Challenges include maintaining impedance control, minimizing signal loss, ensuring thermal stability, and achieving precise manufacturing tolerances.
How do I determine the cost of HF Radar PCBs?
Costs vary based on factors like material choice, design complexity, size, production volume, and surface finishes. It’s best to obtain quotes from manufacturers based on specific project requirements.
What testing is done on HF Radar PCBs?
Testing typically includes electrical continuity checks, automated optical inspection (AOI), signal integrity testing, and sometimes thermal performance evaluations.
Can HF Radar PCBs be customized?
Yes, many manufacturers offer customization options based on specific application requirements, including size, layer count, and component layout.
What is the typical lead time for HF Radar PCB production?
Lead times can vary widely based on complexity and volume, but they generally range from a few weeks to several months for custom designs.