Omega Materials PCB Manufacturer
Omega Materials PCB Manufacturer,Omega Materials PCBs are advanced printed circuit boards manufactured using Omega materials, known for their exceptional thermal conductivity and mechanical strength. These PCBs are designed to efficiently dissipate heat, making them ideal for high-power applications such as power electronics and LED lighting. Omega Materials PCBs offer low thermal resistance, ensuring reliable performance and longevity of electronic components. They are crucial in industries requiring efficient heat management, such as automotive, industrial automation, and renewable energy systems. Omega Materials PCBs are engineered with precise manufacturing processes to maintain consistent thermal performance and electrical reliability in demanding operational environments.
What is an Omega Materials PCB?
An Omega Materials PCB refers to a type of printed circuit board (PCB) that utilizes Omega materials, which typically include high-performance substrates designed for specific applications requiring advanced electrical properties. These materials often feature superior thermal management, low loss characteristics at high frequencies, and excellent dimensional stability under varying conditions.
Omega Materials PCBs are commonly used in industries such as telecommunications, aerospace, and high-frequency electronic devices where reliable performance under demanding environmental conditions is crucial. They are known for their ability to handle high-power densities, maintain signal integrity at microwave frequencies, and provide efficient heat dissipation, which is essential for ensuring the longevity and reliability of electronic components.
Manufacturers of Omega Materials PCBs often tailor their designs to meet stringent performance requirements, including high-speed data transmission, reduced signal attenuation, and minimal cross-talk between circuit elements. This specialization makes Omega Materials PCBs a preferred choice in applications where standard PCB materials may not suffice due to their unique combination of electrical, thermal, and mechanical properties.
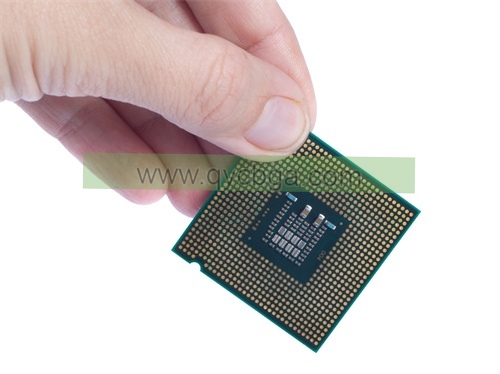
Omega Materials PCB Manufacturer
What are the Omega Materials PCB Design Guidelines?
The design guidelines for Omega Materials PCBs focus on maximizing their unique properties to ensure optimal performance and reliability. Here are some key guidelines typically considered:
- Material Selection: Choose Omega materials suitable for the specific application, considering factors like frequency range, thermal conductivity, dielectric constant, and dimensional stability.
- Layer Stackup: Design an appropriate layer stackup that minimizes signal loss, ensures controlled impedance for high-speed signals, and optimizes thermal management.
- Trace Routing: Follow guidelines for trace width, spacing, and impedance control to maintain signal integrity and minimize electromagnetic interference (EMI).
- Via Design: Optimize via structures to minimize signal distortion and ensure proper heat dissipation, especially for high-frequency and high-power applications.
- Thermal Management: Incorporate thermal vias, heatsinks, or other cooling mechanisms to manage heat effectively, enhancing reliability and longevity of components.
- Mechanical Considerations: Ensure the PCB design meets mechanical requirements for assembly, such as component placement, board size, and mounting hole locations.
- Electromagnetic Compatibility (EMC): Implement measures to reduce EMI and ensure compliance with regulatory standards, such as proper grounding, shielding, and layout considerations.
- Testing and Validation:Plan for testing methodologies to verify electrical performance, thermal behavior, and reliability under operating conditions relevant to the application.
- Documentation: Maintain comprehensive documentation of the design process, including material specifications, layer stackup details, and manufacturing instructions to facilitate quality assurance and future modifications.
By adhering to these guidelines, designers can leverage the unique properties of Omega Materials PCBs effectively, ensuring they meet performance expectations and reliability standards for their intended applications.
What is the Omega Materials PCB Fabrication Process?
The fabrication process for Omega Materials PCBs follows several key steps to ensure the materials’ unique properties are preserved and optimized for their intended applications:
- Material Selection:Choose Omega materials based on the specific requirements of the PCB design, such as high-frequency performance, thermal management, and dimensional stability.
- Preparation of Substrate: Prepare the Omega substrate by cutting it to the required dimensions and cleaning it thoroughly to remove any contaminants that could affect adhesion or conductivity.
- Layer Stackup Design: Design the layer stackup according to the PCB’s functional requirements, considering factors like signal integrity, impedance control, and thermal dissipation.
- Circuit Pattern Generation: Use CAD (Computer-Aided Design) software to generate the circuit patterns and layout according to the design specifications. This includes routing traces, placing vias, and incorporating components.
- Lamination: Apply heat and pressure to bond together multiple layers of Omega substrate and prepreg (pre-impregnated resin) to form a solid, laminated PCB structure. This step ensures proper adhesion and eliminates air voids between layers.
- Drilling: Drill holes for vias and component mounting according to the design specifications, ensuring precision and accuracy in alignment.
- Copper Deposition: Deposit copper onto the substrate surface and within the drilled holes through processes like electroplating to form conductive traces and vias.
- Etching:Use chemical etching or laser ablation techniques to remove excess copper from areas not covered by the circuit pattern, defining the final conductive traces.
- Surface Finishing: Apply surface finishes such as HASL (Hot Air Solder Leveling), ENIG (Electroless Nickel Immersion Gold), or OSP (Organic Solderability Preservatives) to protect exposed copper and ensure solderability during component assembly.
- Solder Mask Application: Apply solder mask over the PCB surface, leaving openings only where soldering is required. This protects the PCB from environmental influences and facilitates soldering during assembly.
- Silkscreen Printing: Print component designators, logos, and other identifying marks onto the PCB surface using silkscreen printing, aiding in component placement and identification.
- Testing and Inspection: Perform electrical testing, including continuity checks, impedance testing, and functional testing to verify the PCB’s performance and adherence to design specifications. Inspect the PCB for defects and ensure quality standards are met.
- Final Inspection and Packaging:Conduct a final inspection to ensure the PCB meets quality standards and specifications. Pack the PCBs appropriately for shipment or assembly.
By following these steps, manufacturers can produce Omega Materials PCBs that meet the stringent performance and reliability requirements demanded by high-frequency and high-thermal applications in industries such as telecommunications, aerospace, and electronics.
How do you manufacture an Omega Materials PCB?
Manufacturing an Omega Materials PCB involves a specialized process tailored to leverage the unique properties of Omega materials, which are crucial for high-frequency and high-thermal applications. Here’s a detailed outline of the manufacturing process:
- Material Selection: Choose Omega materials based on the specific requirements of the PCB design, such as Rogers RO4003C or similar high-performance substrates known for their excellent dielectric properties, thermal conductivity, and dimensional stability.
- Preparation of Substrate: Cut the Omega substrate into the required dimensions using precision tools. Clean the substrate thoroughly to remove any contaminants that could affect adhesion or conductivity.
- Layer Stackup Design: Design the layer stackup according to the PCB’s functional requirements using CAD (Computer-Aided Design) software. Consider factors like signal integrity, impedance control, and thermal management.
- Circuit Pattern Generation: Use CAD software to create the circuit patterns and layout according to the design specifications. This includes routing traces, placing vias, and arranging components.
- Lamination: Assemble the PCB by bonding together multiple layers of Omega substrate and prepreg (pre-impregnated resin) using heat and pressure. This step ensures proper adhesion and eliminates air voids between layers, critical for maintaining signal integrity and thermal dissipation.
- Drilling: Drill holes for vias and component mounting according to the design specifications. This step requires precision to ensure accurate alignment and hole dimensions.
- Copper Deposition: Deposit copper onto the substrate surface and within the drilled holes through electroplating or other suitable methods. This forms conductive traces and vias that connect the circuit components.
- Etching: Use chemical etching or laser ablation techniques to remove excess copper from areas not covered by the circuit pattern, defining the final conductive traces. This step is crucial for maintaining the integrity of the circuit design.
- Surface Finishing: Apply surface finishes such as HASL (Hot Air Solder Leveling), ENIG (Electroless Nickel Immersion Gold), or OSP (Organic Solderability Preservatives) to protect exposed copper and ensure solderability during component assembly.
- Solder Mask Application: Apply solder mask over the PCB surface, leaving openings only where soldering is required. This protective layer prevents solder bridges and ensures reliable electrical connections.
- Silkscreen Printing: Print component designators, logos, and other markings onto the PCB surface using silkscreen printing. This aids in component placement and identification during assembly.
- Testing and Inspection:Perform rigorous testing, including electrical tests (continuity, impedance), functional tests, and visual inspection to verify the PCB’s performance and adherence to design specifications. This step ensures high-quality and reliable PCBs.
- Final Inspection and Packaging:Conduct a final inspection to verify that the PCB meets quality standards and specifications. Pack the PCBs securely for shipment or assembly, ensuring protection during transport.
By following these manufacturing steps, manufacturers can produce Omega Materials PCBs that meet the demanding requirements of high-frequency and high-thermal applications, providing superior performance and reliability in industries such as telecommunications, aerospace, and advanced electronics.
How much should an Omega Materials PCB cost?
The cost of an Omega Materials PCB can vary widely based on several factors, including the specific type of Omega material used, the complexity of the PCB design, the quantity ordered, and additional requirements such as surface finishes and testing. Here are some key factors influencing the cost:
- Type of Omega Material: Different types of Omega materials (e.g., Rogers RO4003C, RO4350B) have varying costs based on their performance characteristics and availability.
- PCB Size and Complexity: Larger PCBs with more complex designs (e.g., high layer count, fine pitch components, controlled impedance requirements) typically cost more to manufacture due to increased material and manufacturing complexity.
- Quantity: Economies of scale apply in PCB manufacturing, where larger production quantities often lead to lower per-unit costs due to efficiencies in materials usage and manufacturing processes.
- Surface Finish:Choice of surface finish (e.g., HASL, ENIG, OSP) can impact cost, with finishes like ENIG generally costing more than HASL due to their superior performance and reliability.
- Testing and Quality Assurance: PCBs that require extensive testing (e.g., impedance testing, high-frequency testing) or strict quality assurance measures may incur additional costs.
- Lead Time: Expedited manufacturing schedules or quick-turn orders typically incur higher costs compared to standard lead times.
To provide a rough estimate, the cost of an Omega Materials PCB can range from a few dollars for simple designs and smaller quantities to tens or even hundreds of dollars for complex designs with specific performance requirements and larger production runs. For accurate pricing, it’s recommended to consult with PCB manufacturers who specialize in Omega materials and provide detailed quotations based on your specific design requirements and production volume.
What is Omega Materials PCB base material?
Omega Materials PCBs typically use high-performance substrate materials that are specifically designed to meet demanding requirements in terms of electrical performance, thermal management, and dimensional stability. Some common base materials used for Omega Materials PCBs include:
- Rogers RO4000 Series: This series includes high-frequency laminates such as RO4003C, RO4350B, RO4450F, which are known for their low dielectric constant (εr) and low loss tangent (tan δ), making them suitable for high-frequency applications.
- Isola FR408HR: A high-performance FR-4 material that offers enhanced thermal reliability and high-frequency performance compared to standard FR-4 laminates.
- Taconic TLY Series: High-frequency laminates like TLY-5, TLY-6, known for their excellent electrical properties and thermal stability.
- Arlon AD Series: High-frequency laminates such as AD250, AD255, designed for microwave and RF applications with high thermal conductivity and reliability.
- Nelco N4000 Series: High-performance laminates with low loss characteristics and good thermal stability, suitable for high-speed digital and RF/microwave applications.
These base materials are selected based on the specific requirements of the PCB design, such as signal integrity, thermal management, and mechanical properties. They are crucial for achieving the desired performance characteristics in Omega Materials PCBs used in applications such as telecommunications, aerospace, automotive electronics, and high-frequency instrumentation.
Which company makes Omega Materials PCBs?
Omega Materials PCBs are mainly produced by several well-known manufacturers specializing in high-performance substrate materials designed to meet high-frequency and high-thermal management requirements. Here’s an introduction to some major manufacturers:
- Rogers Corporation: Rogers is a global leader in high-performance substrate materials. Their RO4000 series (such as RO4003C, RO4350B) are commonly used materials for Omega Materials PCBs due to their excellent dielectric properties and low loss, making them ideal for high-frequency applications.
- Isola Group:Isola offers a wide range of high-performance FR-4 materials, including FR408HR, designed for applications requiring high thermal reliability and high-frequency performance.
- Taconic Advanced Dielectric Division: Taconic’s Advanced Dielectric Division focuses on high-frequency dielectric materials like the TLY series, known for their excellent electrical performance and thermal stability.
- Arlon Electronic Materials: Arlon provides a variety of substrates for high-frequency and microwave applications, such as the AD series, known for high thermal conductivity and reliability.
- Nelco Products: Nelco offers substrates like the N4000 series, known for low-loss characteristics and good thermal stability, suitable for high-speed digital and RF/microwave applications.
These companies provide Omega Materials PCBs globally, catering to various industries with stringent performance requirements such as telecommunications, aerospace, automotive electronics, and high-frequency instrumentation.
Additionally, our company also manufactures Omega Materials PCBs. We specialize in custom high-performance PCB solutions using advanced substrate materials from brands like Rogers, Isola, and Taconic. Equipped with state-of-the-art production equipment and an experienced engineering team, we deliver high-quality Omega Materials PCBs tailored to meet specific design requirements. Whether it’s for high-frequency signal integrity, superior thermal management, or complex multilayer designs, we provide professional manufacturing services, ensuring products meet the highest quality standards and performance requirements. Feel free to contact us for more information on how to customize Omega Materials PCBs and optimize performance for your applications.
What are the 7 qualities of good customer service?
The 7 qualities of good customer service are:
- Responsiveness: Being prompt and timely in addressing customer inquiries, requests, and issues.
- Empathy: Showing understanding and compassion towards customers’ concerns and situations.
- Patience: Remaining calm and composed, especially when dealing with challenging or upset customers.
- Clear Communication: Articulating information clearly and effectively, ensuring customers understand the information provided.
- Knowledgeability: Possessing expertise and knowledge about products, services, and policies to provide accurate information and solutions.
- Professionalism: Conducting interactions with customers in a respectful, courteous, and professional manner.
- Problem-Solving Skills: Ability to identify issues, analyze problems, and propose effective solutions to resolve customer concerns.
These qualities collectively contribute to a positive customer experience, fostering customer satisfaction, loyalty, and trust in the company’s products or services.
FAQs
What are Omega Materials PCBs?
Omega Materials PCBs refer to printed circuit boards that use high-performance substrate materials, such as Rogers RO4000 series, Isola FR408HR, and Taconic TLY series. These materials are chosen for their excellent electrical properties, thermal management capabilities, and dimensional stability, making them suitable for high-frequency and high-thermal applications.
What industries use Omega Materials PCBs?
Omega Materials PCBs are utilized in industries such as telecommunications, aerospace, automotive electronics, RF/microwave applications, and high-speed digital electronics. They are chosen for their ability to maintain signal integrity, handle high-power densities, and ensure reliability in demanding environmental conditions.
How do Omega Materials PCBs differ from standard PCBs?
Omega Materials PCBs use specialized substrate materials with enhanced properties compared to standard FR-4 PCBs. They offer lower loss tangent, higher thermal conductivity, and better mechanical stability, tailored to meet stringent performance requirements in high-frequency and high-power applications.
What factors affect the cost of Omega Materials PCBs?
Factors influencing cost include the type of Omega material used, PCB size and complexity, quantity ordered, surface finish options (e.g., ENIG, OSP), and additional testing requirements (e.g., impedance testing). Customization needs and lead times can also impact pricing.
How can I ensure the reliability of Omega Materials PCBs?
Ensuring reliability involves selecting the appropriate Omega material based on the application’s requirements, following recommended design guidelines for high-frequency PCBs, performing thorough testing (such as impedance testing), and adhering to quality manufacturing standards.
Where can I purchase Omega Materials PCBs?
Omega Materials PCBs are available from specialized PCB manufacturers and distributors who work with high-performance substrate materials. Companies like Rogers Corporation, Isola Group, Taconic Advanced Dielectric Division, and others supply these materials directly or through authorized distributors.