Showa Denko MCL-E-700G Package Substrate Manufacturer
Showa Denko MCL-E-700G Package Substrate Manufacturer,The Showa Denko MCL-E-700G is a high-performance package substrate material designed to meet the needs of advanced semiconductor packaging. Renowned for its superior thermal and electrical properties, it supports high-speed signal transmission and high-frequency applications, making it ideal for high-density, multi-layer integrated circuit packaging technologies. The MCL-E-700G substrate utilizes special resins and reinforcement materials, providing exceptionally high mechanical stability and excellent thermal diffusion capabilities, which help enhance the overall performance and reliability of the chip. 또한, this substrate material boasts excellent chemical stability and resistance to environmental impacts, maintaining performance in various harsh conditions. 전반적, the Showa Denko MCL-E-700G offers an efficient and reliable solution suitable for the packaging requirements of various high-end electronic devices.
What is Showa Denko MCL-E-700G package substrate?
The Showa Denko MCL-E-700G package substrate is a cutting-edge technology in the realm of electronic packaging. It serves as a crucial component in the assembly and performance of various electronic devices, 집적 회로 포함 (IC (영어)) and microprocessors.
The substrate acts as a foundation upon which electronic components are mounted, providing electrical connections between them while ensuring mechanical support and thermal management. Showa Denko’s MCL-E-700G substrate is renowned for its exceptional quality and performance attributes.
This substrate is engineered using advanced materials and manufacturing techniques, making it highly reliable and efficient in demanding electronic applications. Its design features enable enhanced signal transmission, reduced power consumption, and improved heat dissipation, which are critical factors for the optimal functioning of electronic devices.
더욱이, the MCL-E-700G substrate is designed to meet the evolving requirements of modern electronics, including smaller form factors, higher integration densities, and increased functionality. Its compatibility with diverse semiconductor technologies makes it versatile for use across a wide range of applications, from consumer electronics to industrial machinery and automotive systems.
요약하면 다음과 같습니다, the Showa Denko MCL-E-700G package substrate represents a pinnacle of innovation in electronic packaging, offering superior performance, 신뢰도, and versatility to meet the demands of today’s technology-driven world.
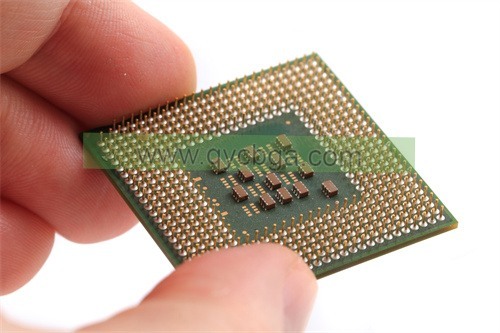
Showa Denko MCL-E-700G Package Substrate Manufacturer
What are the Showa Denko MCL-E-700G package substrate Design Guidelines?
Design guidelines for the Showa Denko MCL-E-700G package substrate typically include recommendations and specifications regarding various aspects of substrate design, such as dimensions, materials, layout, and electrical characteristics. While specific guidelines may vary depending on the application and requirements, here are some common design considerations:
- Dimensional Specifications: Guidelines for substrate dimensions including length, width, and thickness, ensuring compatibility with the intended electronic device or package.
- 재료 선택: Recommendations for substrate materials to optimize electrical performance, 열전도율, and mechanical stability. This may include specifying the type of substrate material (예), 프렌-4, 질그릇의) and its properties.
- Layer Configuration: Guidelines for the number and arrangement of substrate layers, considering factors such as signal integrity, 전력 분배, and routing complexity.
- Signal Routing and Impedance Control: Recommendations for signal routing to minimize signal degradation and ensure proper impedance matching. Guidelines may include trace width, spacing, and layer stackup configurations.
- Power Distribution Network (증권 시세 표시기):Design guidelines for the PDN to ensure adequate power delivery and voltage regulation throughout the substrate. This may include recommendations for power plane design, 디커플링 커패시터 배치, and routing.
- 열 관리: Guidelines for thermal vias, 방열판, and other thermal management features to dissipate heat generated by electronic components effectively. This helps prevent overheating and ensures reliable operation of the device.
- Component Placement and Layout: Recommendations for the placement of electronic components, such as ICs, passive components, and connectors, to minimize signal interference, routing congestion, and assembly issues.
- Design for Manufacturability (DFM): Guidelines for designing the substrate to facilitate manufacturing processes, such as PCB fabrication, 집회, 및 테스트. This may include recommendations for panelization, fiducial marker placement, and solder mask design.
- 안정성 고려 사항: Guidelines for designing the substrate to meet reliability requirements, including solder joint integrity, thermal cycling resistance, and mechanical shock/vibration tolerance.
- Compliance and Standards: 기판 설계가 관련 산업 표준 및 규정을 준수하는지 확인합니다., such as IPC standards for PCB design and RoHS compliance for materials.
These guidelines aim to optimize the performance, 신뢰도, and manufacturability of electronic devices using Showa Denko MCL-E-700G package substrates, ultimately contributing to the success of the end product in its intended application.
What is the Showa Denko MCL-E-700G package substrate Fabrication Process?
The fabrication process of the Showa Denko MCL-E-700G package substrate involves several steps that transform raw materials into a finished substrate ready for use in electronic devices. While specific details may vary depending on the manufacturing facility and technology used, here is a general overview of the fabrication process:
- 기판 재료 선택: The process begins with the selection of appropriate substrate materials, which may include laminates, 구리 포일, 그리고 절연성 물자. These materials are chosen based on the desired electrical, thermal, and mechanical properties of the final substrate.
- 기판 준비: The selected materials undergo preparation steps such as cleaning and surface treatment to ensure optimal adhesion and compatibility with subsequent manufacturing processes.
- Copper Cladding: Copper foils are laminated onto the substrate material using heat and pressure, forming the conductive layers of the substrate. The thickness and quality of the copper cladding are critical for achieving desired electrical performance.
- Laser Drilling: Laser drilling is used to create small holes, or vias, in the substrate. These vias serve as electrical connections between different layers of the substrate, allowing for the routing of signals and power throughout the device.
- Electroplating: Electroplating is employed to deposit additional layers of copper onto the substrate, including through-hole plating to ensure continuity between vias and surface plating for component attachment.
- 에칭: Chemical etching processes are used to selectively remove unwanted copper from the substrate, defining the desired trace patterns and features according to the substrate design.
- 표면 마무리: Surface finishing techniques such as immersion tin, immersion silver, or electroless nickel immersion gold (수수께끼) may be applied to the substrate to protect exposed copper surfaces, improve solderability, and enhance reliability.
- 솔더 마스크 적용: A solder mask is applied to the substrate surface, leaving openings only where solder connections are required. The solder mask protects the substrate and ensures proper soldering during component assembly.
- 실크스크린 인쇄: Information such as component reference designators, logos, and alignment marks may be printed onto the substrate surface using silkscreen printing for identification and alignment purposes.
- 테스트 및 검사: The fabricated substrate undergoes rigorous testing and inspection processes to verify its electrical connectivity, dimensional accuracy, and overall quality. Various electrical tests, visual inspections, and automated equipment may be utilized for this purpose.
- 최종 포장: Once the substrate passes inspection, it is packaged and prepared for shipment to customers or further assembly into electronic devices.
제작 공정 전반에 걸쳐, strict quality control measures are implemented to ensure that the Showa Denko MCL-E-700G package substrates meet the required specifications and performance standards for their intended applications.
How do you manufacture Showa Denko MCL-E-700G package substrate?
Manufacturing the Showa Denko MCL-E-700G package substrate involves a series of sophisticated processes that demand precision, consistency, and attention to detail. Here’s a detailed explanation of how it’s typically done:
- Material Preparation: The process begins with the selection and preparation of raw materials. Substrate materials, such as laminates and copper foils, are sourced from trusted suppliers and undergo thorough inspection for quality and conformity to specifications.
- Cleaning and Surface Treatment: The substrate materials are cleaned and treated to remove any contaminants and improve surface adhesion. Surface treatments may include processes like plasma treatment or chemical etching to enhance bonding between layers.
- Copper Cladding: Copper foils are laminated onto the substrate material using heat and pressure. This step creates the conductive layers of the substrate, and the thickness and quality of the copper cladding are carefully controlled to meet performance requirements.
- Laser Drilling: Precision laser drilling is used to create small holes, or vias, in the substrate. These vias establish electrical connections between different layers of the substrate, enabling signal routing and power distribution throughout the device.
- Electroplating: Electroplating is employed to deposit additional layers of copper onto the substrate, including through-hole plating to ensure continuity between vias and surface plating for component attachment. This step further enhances conductivity and reliability.
- 에칭: Chemical etching processes are utilized to selectively remove unwanted copper from the substrate, defining the desired trace patterns and features according to the substrate design. Etching accuracy is critical for achieving precise circuitry.
- 표면 마무리: Various surface finishing techniques, such as immersion tin, immersion silver, or electroless nickel immersion gold (수수께끼), may be applied to the substrate to protect exposed copper surfaces, improve solderability, and enhance reliability.
- 솔더 마스크 적용: A solder mask is applied to the substrate surface, leaving openings only where solder connections are required. The solder mask protects the substrate and ensures proper soldering during component assembly while also providing insulation.
- 실크스크린 인쇄: Information such as component reference designators, logos, and alignment marks may be printed onto the substrate surface using silkscreen printing for identification and alignment purposes.
- 테스트 및 검사: The fabricated substrate undergoes rigorous testing and inspection processes to verify its electrical connectivity, dimensional accuracy, and overall quality. Various electrical tests, visual inspections, and automated equipment may be utilized for this purpose.
- 최종 포장:Once the substrate passes inspection, it is packaged and prepared for shipment to customers or further assembly into electronic devices.
제조 공정 전반에 걸쳐, stringent quality control measures are implemented to ensure that the Showa Denko MCL-E-700G package substrates meet the required specifications and performance standards for their intended applications. Continuous improvement efforts are also made to optimize processes and enhance product quality.
How much should Showa Denko MCL-E-700G package substrate cost?
Determining the exact cost of the Showa Denko MCL-E-700G package substrate can be challenging as it depends on various factors such as the quantity ordered, customization requirements, market conditions, and supplier agreements. 그렇지만, I can provide insights into the factors influencing its cost and a rough estimation.
- Material Costs: The primary components of the substrate, including substrate materials, 구리 포일, and surface finishing materials, contribute significantly to the overall cost. Prices for these materials can fluctuate based on market demand, availability, and quality.
- 제조 복잡성:The complexity of the manufacturing process, 레이어 수 포함, vias, and intricate features, affects production costs. More complex designs require additional processing steps, equipment, 그리고 노동, resulting in higher manufacturing expenses.
- Volume and Scale: Economies of scale play a crucial role in determining the cost of the substrate. Larger order quantities typically result in lower per-unit costs due to efficiencies in production, material procurement, and overhead expenses.
- Customization and Specifications: Customized features, special requirements, and unique specifications requested by customers may increase the cost of the substrate. These could include specific materials, finishes, tolerances, or testing procedures tailored to the application’s needs.
- Supplier Relationships: The pricing structure may also be influenced by the relationship between the buyer and the supplier. Long-term contracts, volume commitments, and negotiated agreements can result in discounted pricing or favorable terms.
- Market Dynamics: External factors such as market demand, supply chain disruptions, currency fluctuations, and regulatory changes can impact substrate prices. Shortages of raw materials or increased demand for electronic devices may drive up costs.
Given these considerations, a rough estimate for the cost of the Showa Denko MCL-E-700G package substrate could range from several dollars to tens of dollars per square inch, depending on the factors mentioned above. 그렇지만, for precise pricing information, it’s best to consult directly with Showa Denko or their authorized distributors, as they can provide tailored quotations based on specific requirements and order quantities. 또한, volume discounts and negotiation opportunities may be available depending on the customer’s purchasing power and long-term commitments.
What is Showa Denko MCL-E-700G package substrate base material?
The base material of the Showa Denko MCL-E-700G package substrate typically consists of high-quality laminate materials designed to meet the demanding requirements of electronic packaging. While specific formulations may vary based on customer specifications and application requirements, the base material is typically composed of layers of reinforcing substrates and resin materials.
One common type of base material used in package substrates is fiberglass-reinforced epoxy laminate, often referred to as FR-4. FR-4 is a widely used substrate material known for its excellent electrical insulation properties, 기계적 강도, and dimensional stability. It consists of layers of woven glass fabric impregnated with an epoxy resin binder.
In addition to FR-4, other advanced materials such as high-temperature polyimides or ceramics may also be used as base materials for specialized applications requiring enhanced thermal performance, 신뢰도, or miniaturization.
Showa Denko may employ proprietary formulations or enhancements to the base material to tailor its properties to specific performance criteria, such as thermal conductivity, 열팽창 계수 (증권 시세 표시기), and dielectric constant. These modifications aim to optimize the substrate’s performance and reliability in various electronic applications, including high-speed digital circuits, RF/microwave devices, and power electronics.
전반적, the base material of the Showa Denko MCL-E-700G package substrate is carefully selected and engineered to provide the necessary electrical, 기계적인, and thermal properties required for reliable operation in modern electronic devices.
Which company produces Showa Denko MCL-E-700G package substrate?
The Showa Denko MCL-E-700G package substrate is produced by Showa Denko Corporation. Showa Denko is a multinational company headquartered in Japan and is one of the world’s leading manufacturers of chemicals and materials. The company has extensive experience and expertise in the field of electronic materials, offering various high-performance electronic materials and solutions, including the MCL-E-700G package substrate.
Our company also manufactures similar high-performance package substrates to meet customer needs. We have advanced production equipment and technology, as well as an experienced engineering team capable of designing and manufacturing customized substrates to customer specifications.
Our production process includes raw material procurement, manufacturing processing, quality inspection, and packaging. We use high-quality substrate materials, such as FR-4 fiberglass-reinforced epoxy resin, to ensure that the substrate has excellent electrical insulation properties, 기계적 강도, and dimensional stability. 제조 공정 전반에 걸쳐, we strictly control each step to ensure that the products meet customer specifications and quality standards.
We are committed to providing customers with high-quality, high-performance electronic materials and solutions. We can customize various types of package substrates according to customer requirements, including but not limited to the MCL-E-700G. We understand the importance of product quality and delivery lead time to our customers, so we continuously optimize our production process to meet customer needs and provide excellent service.
무엇입니까 7 좋은 고객 서비스의 품질?
Good customer service is characterized by several key qualities that contribute to positive interactions and satisfaction for customers. Here are seven qualities:
- 응답성: Good customer service involves promptly addressing customer inquiries, concerns, and requests. Responding in a timely manner demonstrates attentiveness and shows that the customer’s needs are valued.
- 공감: Empathy is the ability to understand and share the feelings of customers. Customer service representatives who demonstrate empathy can connect with customers on a personal level, validate their concerns, and provide appropriate support and solutions.
- Clear Communication: Effective communication is essential for providing good customer service. Clear and concise communication helps customers understand information, instructions, and solutions, leading to smoother interactions and resolution of issues.
- 전문성: Good customer service is conducted with professionalism, which includes maintaining a positive attitude, remaining courteous and respectful, and adhering to company policies and standards. Professionalism builds trust and confidence in the customer-service relationship.
- Problem-solving Skills: Customer service representatives should possess strong problem-solving skills to effectively address customer issues and concerns. This involves analyzing situations, identifying root causes, and implementing appropriate solutions to resolve problems and satisfy customers.
- Product Knowledge: Knowledge about products or services is crucial for providing helpful assistance and guidance to customers. Customer service representatives should be well-informed about the features, benefits, and specifications of the products or services they support, enabling them to answer questions and offer relevant recommendations.
- Follow-up and Follow-through: Good customer service extends beyond the initial interaction by following up with customers to ensure their needs have been met and their issues resolved satisfactorily. Following through on commitments and promises demonstrates reliability and reinforces trust in the company’s service.
이러한 특성을 구현함으로써, businesses can cultivate strong relationships with customers, enhance satisfaction, and foster loyalty and advocacy.
자주 묻는 질문(FAQ)
What is Showa Denko MCL-E-700G package substrate?
The Showa Denko MCL-E-700G package substrate is an advanced electronic substrate used in the assembly of various electronic devices, providing electrical connections between components while ensuring mechanical support and thermal management.
What are the key features of MCL-E-700G package substrates?
MCL-E-700G substrates typically offer high reliability, excellent electrical performance, and efficient thermal dissipation. They are designed to meet the demanding requirements of modern electronic applications.
What applications are suitable for MCL-E-700G package substrates?
MCL-E-700G substrates are suitable for a wide range of electronic applications, 집적 회로 포함 (IC (영어)), microprocessors, RF/microwave devices, power electronics, and automotive electronics.
What materials are used in MCL-E-700G package substrates?
MCL-E-700G substrates are typically constructed using high-quality laminate materials, such as FR-4 fiberglass-reinforced epoxy resin, along with copper foils, solder masks, 그리고 지상 끝.
What are the design guidelines for MCL-E-700G package substrates?
Design guidelines for MCL-E-700G substrates may include specifications regarding dimensions, materials, layer configuration, 시그널 라우팅, 열 관리, 업계 표준 준수.
How are MCL-E-700G package substrates manufactured?
The manufacturing process of MCL-E-700G substrates involves several steps, including material preparation, copper cladding, laser drilling, 전기 도금, 에칭, 표면 마무리, 솔더 마스크 적용, and testing/inspection.
Where can I purchase MCL-E-700G package substrates?
MCL-E-700G substrates are typically available through authorized distributors or directly from Showa Denko. Customers can contact Showa Denko or its authorized partners for inquiries and purchases.
What are the benefits of using MCL-E-700G package substrates?
The benefits of MCL-E-700G substrates include enhanced electrical performance, improved thermal management, 높은 신뢰성, compatibility with various semiconductor technologies, and support for advanced electronic applications.