Rogers Rt5880 PCB Board Manufacturer
Rogers Rt5880 PCB Board Manufacturer,Rogers RT5880 PCB boards are engineered for high-frequency applications demanding superior performance and reliability. Featuring a low dielectric constant and minimal signal loss, RT5880 boards ensure optimal signal integrity in microwave circuits, RF antennas, and radar systems. With excellent thermal stability and dimensional accuracy, these boards offer consistent performance across diverse environments. Rogers RT5880 PCBs are the go-to choice for telecommunications equipment, wireless communication devices, and other advanced electronic systems requiring precision and durability in high-frequency operation.
What is a Rogers Rt5880 PCB Board?
The Rogers RT5880 is a high-frequency laminate material used primarily in the manufacturing of printed circuit boards (PCB (폴리염화비페닐)). It is specifically engineered for applications that require excellent electrical properties, particularly at high frequencies. The Rogers RT5880 material is part of Rogers Corporation’s RT/duroid series, which are renowned for their low dielectric losses, making them ideal for microwave and millimeter-wave frequencies.
Key characteristics of the RT5880 laminate include a low dielectric constant (Dk) of approximately 2.2, which is consistent across a wide frequency range. This stable Dk ensures predictable performance of high-speed signals. Moreover, the material boasts a low dissipation factor, which minimizes energy loss during signal transmission, crucial for maintaining signal integrity in high-frequency applications.
The RT5880 is also known for its low moisture absorption. This property is critical in environments where exposure to moisture could otherwise affect the dielectric properties and lead to performance degradation. The thermal stability of RT5880 is another notable feature, with a thermal coefficient of dielectric constant at a very low rate, ensuring minimal dimensional changes in response to temperature fluctuations.
This combination of characteristics makes the Rogers RT5880 PCB board an excellent choice for demanding applications such as radar systems, satellite communications, and high-speed digital circuits where reliability and performance are paramount. Its use in these areas underscores the importance of material selection in advanced electronics design, contributing to the overall efficiency and functionality of sophisticated electronic systems.
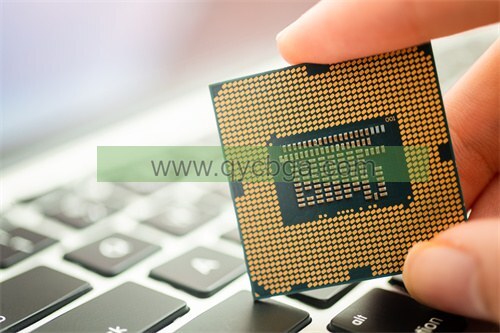
Rogers Rt5880 PCB Board Manufacturer
What are the PCB Design Guidelines for Rogers Rt5880 PCB Board?
Designing a PCB with Rogers RT5880 requires careful consideration of several key factors to ensure optimal performance at high frequencies. Here are some PCB design guidelines specific to using Rogers RT5880 material:
- Trace Width and Spacing: Maintain appropriate trace widths and spacing to minimize signal loss and impedance variations. Use controlled impedance traces to match the characteristic impedance of the transmission lines.
- 비아 디자인: Use high-quality plated-through holes (PTH) vias to maintain signal integrity. Ensure proper via placement and sizing to minimize impedance disruptions and signal reflections.
- Grounding: Implement a solid ground plane to provide a low-impedance return path for signals and to minimize electromagnetic interference (이엠아이). Avoid gaps or cuts in the ground plane beneath high-speed signal traces.
- Component Placement: Place critical components as close to each other as possible to minimize trace lengths and reduce parasitic capacitance and inductance. Group components according to their function to minimize signal path lengths.
- Decoupling Capacitors: Include decoupling capacitors strategically across the PCB to provide localized energy storage and filtering, reducing noise and voltage fluctuations.
- Stackup Design: Design a PCB stackup that optimizes signal integrity and controlled impedance. Consider the number of layers, the thickness of dielectric layers, and the arrangement of signal and ground planes.
- 열 관리: Incorporate thermal vias and thermal relief pads for components that generate heat to dissipate it efficiently. Ensure adequate airflow and heat sinking to prevent overheating of critical components.
- Copper Weight: Choose an appropriate copper weight for the PCB based on the current-carrying capacity and thermal requirements of the design. Thicker copper layers can reduce resistance and improve thermal performance.
- Material Handling: Follow proper handling and storage procedures for Rogers RT5880 material to prevent contamination or damage that could affect electrical properties.
- Testing and Verification: Perform thorough testing and verification of the PCB design, including signal integrity analysis, impedance matching, and EMI testing, to ensure compliance with design requirements and performance expectations.
By adhering to these PCB design guidelines, engineers can leverage the unique electrical properties of Rogers RT5880 material to achieve reliable high-frequency performance in their designs.
What is the Rogers Rt5880 PCB Fabrication Process?
The fabrication process for a PCB using Rogers RT5880 material follows several standard steps, with some specific considerations for high-frequency applications. Here’s an overview of the typical fabrication process:
- Material Preparation: The process begins with the preparation of Rogers RT5880 laminate material. This involves cutting the laminate sheets to the required size based on the PCB design specifications.
- 드릴링:Holes are drilled into the laminate material using precision equipment. These holes will accommodate through-hole components and vias for interconnecting different layers of the PCB.
- Layer Alignment and Bonding: If the PCB design requires multiple layers, the individual layers of copper foil and RT5880 laminate are aligned and bonded together using heat and pressure to create a single, multi-layered substrate.
- 회로 패터닝: A photoresist layer is applied to the surface of the copper foil. The PCB design is then transferred onto this photoresist layer using photolithography techniques. The areas not covered by the design are etched away using chemical etchants, 원하는 구리 흔적을 남기고.
- 비아 포메이션: Vias are created by drilling or punching holes through the substrate at specific locations where interconnection between different layers is required. These vias are then plated with conductive material to establish electrical continuity between layers.
- 표면 마감: The exposed copper surfaces of the PCB are typically coated with a surface finish to protect them from oxidation and improve solderability. 일반적인 표면 마감에는 HASL이 포함됩니다. (뜨거운 공기 솔더 레벨링), 수수께끼 (무전해 니켈 침지 금), 및 OSP (Organic Solderability Preservative).
- 솔더 마스크 적용: A solder mask is applied over the copper traces to insulate them from environmental factors and prevent unintended solder bridges during assembly. Openings are left in the solder mask to expose the areas where components will be soldered.
- 실크스크린 인쇄: Component designators, logos, and other markings are applied to the PCB surface using silkscreen printing for identification and assembly guidance.
- 테스트 및 검사: The fabricated PCB undergoes various tests and inspections to ensure it meets quality standards and design specifications. This may include electrical continuity tests, impedance measurements, and visual inspection for defects.
- Final Assembly: Once the PCB passes inspection, it is ready for final assembly. Components are mounted onto the board using automated pick-and-place machines, and soldered into place using reflow soldering or wave soldering techniques.
- Final Testing: The assembled PCB undergoes final electrical testing to verify functionality and performance before being shipped to the customer.
제작 공정 전반에 걸쳐, particular attention is paid to maintaining the dimensional stability and electrical properties of the Rogers RT5880 material, as these are crucial for achieving reliable high-frequency performance in the finished PCB.
How do you manufacture a Rogers Rt5880 PCB Board?
Manufacturing a PCB using Rogers RT5880 material involves a series of steps similar to the standard PCB fabrication process, but with special considerations for the unique properties of the RT5880 laminate. Here’s an outline of the manufacturing process:
- Material Selection and Preparation: Choose the appropriate thickness and size of Rogers RT5880 laminate sheets based on the design requirements. Ensure that the material is properly stored and handled to prevent contamination or damage.
- Design Preparation: Create or obtain the PCB design files (Gerber files) specifying the layout, dimensions, and electrical characteristics of the PCB. Considerations for high-frequency signal integrity and controlled impedance should be incorporated into the design.
- Panelization: If producing multiple PCBs on a single substrate, arrange the individual PCB designs on a panel to optimize material usage and facilitate manufacturing efficiency.
- 박판: Place the RT5880 laminate sheets and copper foil layers together in a lamination press. Apply heat and pressure to bond the layers into a solid substrate, ensuring proper alignment and registration of all layers.
- 드릴링:Precision drill the required holes for component mounting pads and vias according to the PCB design specifications. Use high-speed CNC drilling machines to achieve accuracy and consistency.
- 회로 패터닝: Apply a photoresist layer onto the copper foil surface of the laminated substrate. Expose the photoresist to UV light through a mask containing the PCB circuit pattern. Develop and etch away the unexposed photoresist and unwanted copper to create the desired copper traces.
- 비아 포메이션: Drill or punch holes through the substrate at designated locations for vias. Plate the vias with conductive material to establish electrical connections between different layers of the PCB.
- Surface Finish Application: Coat the exposed copper surfaces with a suitable surface finish to protect them from oxidation and facilitate soldering during assembly. 일반적인 표면 마감에는 HASL이 포함됩니다., 수수께끼, 및 OSP.
- 솔더 마스크 적용: Apply a solder mask over the PCB surface, leaving openings for component pads and vias. Cure the solder mask to form a protective layer over the copper traces and vias.
- 실크스크린 인쇄: Print component designators, logos, and other markings onto the PCB surface for identification and assembly guidance using a silkscreen printing process.
- 테스트 및 검사: Conduct electrical testing and visual inspection to ensure the quality and accuracy of the manufactured PCBs. Verify impedance, continuity, and dimensional accuracy according to the design specifications.
- Final Assembly: Mount electronic components onto the PCB using automated pick-and-place machines. Solder the components onto the board using reflow soldering or wave soldering techniques.
- Final Testing: Perform functional testing of the assembled PCBs to verify proper operation and adherence to performance requirements before packaging and shipment.
제조 공정 전반에 걸쳐, strict adherence to quality control measures and attention to detail are essential to produce high-quality PCBs with Rogers RT5880 material, particularly for applications requiring excellent high-frequency performance and signal integrity.
How much should a Rogers Rt5880 PCB Board cost?
The cost of a Rogers RT5880 PCB board can vary significantly depending on several factors, including the size, 복잡성, 양, and specifications of the board, as well as the fabrication and assembly processes involved. Here are some key factors that can influence the cost:
- 재료비: Rogers RT5880 laminate material is generally more expensive compared to standard FR-4 material due to its specialized properties, such as low dielectric constant and low loss tangent. The cost of the RT5880 material will depend on factors such as sheet size, thickness, and supplier pricing.
- Board Size and Complexity: Larger boards with more complex designs require more material and manufacturing time, which can increase the overall cost. Boards with densely populated components, fine pitch traces, and multiple layers may also incur higher fabrication costs.
- Layer Count: The number of layers in the PCB affects both material and manufacturing costs. Multi-layer boards require additional processes such as lamination, 드릴링, and plating, which can increase production expenses.
- Feature Complexity: Special features such as blind vias, buried vias, controlled impedance traces, and impedance matching structures can add to the manufacturing complexity and cost of the PCB.
- Surface Finish and Plating Options: Different surface finishes and plating options, such as gold plating or ENIG (무전해 니켈 침지 금), come with varying costs. Higher-quality finishes may increase the overall cost of the PCB.
- Assembly Costs: If the PCB requires component assembly, factors such as component type, assembly method (manual vs. automated), and soldering techniques will impact assembly costs.
- 양: Economies of scale typically apply, meaning that larger production quantities generally result in lower per-unit costs due to bulk purchasing of materials and efficiency gains in manufacturing.
To get an accurate cost estimate for a specific Rogers RT5880 PCB board, it’s recommended to consult with PCB manufacturers or suppliers directly. They can provide quotes based on your design specifications, desired quantities, and any additional requirements. 또한, obtaining quotes from multiple suppliers can help in comparing prices and selecting the most cost-effective option for your project.
What is the Rogers Rt5880 PCB base material?
Rogers RT/duroid® 5880 is a high-performance, low-loss laminate material used in the fabrication of printed circuit boards (PCB (폴리염화비페닐)) for high-frequency applications. Here are some key characteristics of Rogers RT/duroid® 5880 PCB base material:
- Dielectric Constant (Dk): The dielectric constant of Rogers RT/duroid® 5880 is approximately 2.20 ± 0.02 in the z-axis (through thickness) and 2.33 in the x and y axes (in-plane).
- Low Loss Tangent (Df): It exhibits a low dissipation factor, typically around 0.0009 at 10 GHz, which ensures minimal signal loss and excellent signal integrity in high-frequency circuits.
- Temperature Stability: RT/duroid® 5880 offers excellent thermal stability, making it suitable for applications operating in a wide range of temperature environments.
- Flame Retardancy: The material is inherently flame retardant, meeting UL 94V-0 requirements, which is crucial for safety in electronic applications.
- 치수 안정성: RT/duroid® 5880 has good dimensional stability, maintaining tight tolerances and consistent electrical properties across different environmental conditions.
- Substrate Construction: It consists of a ceramic-filled PTFE (polytetrafluoroethylene) composite with woven glass reinforcement, providing mechanical strength and reliability while maintaining electrical performance.
- Applications: Rogers RT/duroid® 5880 is commonly used in high-frequency applications such as microwave circuits, RF antennas, 레이더 시스템, and telecommunications equipment.
전반적, Rogers RT/duroid® 5880 is a high-quality laminate material known for its excellent electrical properties, low loss characteristics, and reliability, making it a popular choice for demanding high-frequency PCB designs.
Which company makes Rogers Rt5880 PCB Boards?
Rogers RT/duroid® 5880 PCB boards are manufactured by Rogers Corporation, a leading American company. Rogers Corporation is a global leader in high-performance materials, specializing in providing innovative material solutions to meet the needs of various electronic applications. RT/duroid® 5880 is one of their high-performance low-loss laminate materials, widely used in high-frequency circuit designs and RF microwave applications.
Our company is also capable of producing Rogers RT/duroid® 5880 PCB boards. As a professional PCB manufacturer, we have advanced production equipment and a skilled technical team capable of customizing various types of PCBs, including the Rogers material series, according to customer requirements. Our company has the following advantages:
- Customization Capability: We can customize Rogers RT/duroid® 5880 PCB boards according to customer design requirements and specifications, including different thicknesses, layers, sizes, and special process requirements.
- Quality Assurance: We strictly adhere to international standards and quality management systems to ensure that every PCB board produced meets customer requirements and undergoes rigorous quality inspection.
- Fast Delivery: With efficient production processes and flexible scheduling, we can complete orders in a short time and deliver them to customers on time.
- Technical Support: Our experienced engineering team and technical support personnel can provide customers with professional technical support and consulting services to help them solve various problems in PCB design and manufacturing processes.
- Price Advantage: We offer competitive prices for Rogers RT/duroid® 5880 PCB board manufacturing services to meet customer cost budget requirements.
Therefore, if you need customized Rogers RT/duroid® 5880 PCB boards or other types of PCBs, please feel free to contact our company. We will provide you with high-quality products and services to meet your needs and achieve mutual development.
무엇입니까 7 좋은 고객 서비스의 품질?
우수한 고객 서비스는 고객과 강력한 관계를 구축하고 충성도를 높이는 데 필수적입니다. Here are seven qualities that characterize excellent customer service:
- 응답성: A good customer service team responds promptly to customer inquiries, concerns, and requests. Whether through phone calls, emails, or live chat, being available and attentive to customer needs demonstrates responsiveness.
- 공감: Empathy involves understanding and acknowledging the customer’s perspective and emotions. Good customer service representatives listen actively, show compassion, and demonstrate genuine concern for the customer’s situation or issue.
- Knowledgeability: Customers expect customer service agents to be knowledgeable about the products or services offered. Providing accurate information, troubleshooting effectively, and offering solutions demonstrate expertise and build trust with customers.
- 전문성: Professionalism encompasses qualities such as courtesy, politeness, and respectfulness in interactions with customers. Maintaining a professional demeanor, 어려운 상황에서도, enhances the customer experience and reflects positively on the company.
- Problem-Solving Skills: Effective problem-solving skills are crucial for resolving customer issues and addressing complaints. Customer service representatives should be proactive in identifying solutions, taking ownership of problems, and following through to ensure resolution.
- Consistency: Consistency in service delivery ensures that customers receive the same level of quality and support across all interactions and touchpoints with the company. Consistency builds trust and reliability, fostering long-term relationships with customers.
- Proactive Communication: Anticipating customer needs and providing proactive communication can enhance the customer experience. Whether through updates on order status, product information, or helpful tips, proactive communication demonstrates attentiveness and adds value for customers.
이러한 특성을 구현함으로써, businesses can deliver exceptional customer service that meets or exceeds customer expectations, fosters loyalty, and contributes to overall success.
FAQs about Rogers Rt5880 PCB Boards
What are the key characteristics of RT/duroid® 5880?
RT/duroid® 5880 exhibits a low dielectric constant (Dk), low dissipation factor (Df), excellent thermal stability, dimensional stability, and flame retardancy. It is suitable for applications requiring high-frequency performance and reliability.
What applications are Rogers RT/duroid® 5880 PCB boards used for?
RT/duroid® 5880 PCB boards are commonly used in high-frequency applications such as microwave circuits, RF antennas, 레이더 시스템, telecommunications equipment, and other wireless communication devices.
What are the benefits of using Rogers RT/duroid® 5880 PCB boards?
The benefits of using RT/duroid® 5880 PCB boards include minimal signal loss, excellent signal integrity, thermal stability, dimensional stability, and reliability in high-frequency applications.
How are Rogers RT/duroid® 5880 PCB boards manufactured?
RT/duroid® 5880 PCB boards are manufactured using a process that involves laminating copper foil onto the RT/duroid® 5880 laminate material, etching the desired circuit pattern, applying surface finish, and assembling components according to the design requirements.
What are the design considerations for Rogers RT/duroid® 5880 PCB boards?
Design considerations for RT/duroid® 5880 PCB boards include controlled impedance routing, minimizing signal loss, optimizing ground plane placement, 열 관리, and ensuring compatibility with high-frequency components.
Where can I purchase Rogers RT/duroid® 5880 PCB boards?
Rogers RT/duroid® 5880 PCB boards can be purchased from authorized distributors or directly from PCB manufacturers specializing in high-frequency PCB fabrication.