Military Circuit Board Manufacturer
Military Circuit Board Manufacturer,Military Circuit Boards (MCBs) are the backbone of modern military technology, providing the critical electronic infrastructure for a wide range of defense systems. Designed and manufactured to meet the stringent standards and demands of military applications, MCBs are built to withstand extreme conditions and deliver high reliability and performance in mission-critical environments. These specialized circuit boards incorporate ruggedized materials, advanced manufacturing techniques, and stringent quality control measures to ensure optimal functionality in harsh operating conditions such as temperature variations, shock, 진동, 및 전자기 간섭. MCBs play a vital role in military communication systems, 레이더 시스템, 항행 장비, weapons systems, electronic warfare devices, and more. Their robust design, secure features, and adherence to military standards make them essential components in safeguarding national security and enabling the success of military operations around the world.
What is a Military Circuit Board (MCB)?
A Military Circuit Board (MCB) is a specialized type of circuit board designed to meet the rigorous demands and standards of military applications. These circuit boards are built to withstand extreme conditions such as temperature variations, shock, 진동, 및 전자기 간섭 (이엠아이).
MCBs often utilize ruggedized materials and construction techniques to ensure reliability in harsh environments. They may also incorporate features such as conformal coating, which provides protection against moisture, dust, and other contaminants.
또한, military circuit boards may have specific security features to prevent tampering or unauthorized access to sensitive information. They play a crucial role in various military systems, including communication devices, 레이더 시스템, weapons systems, and electronic warfare equipment.
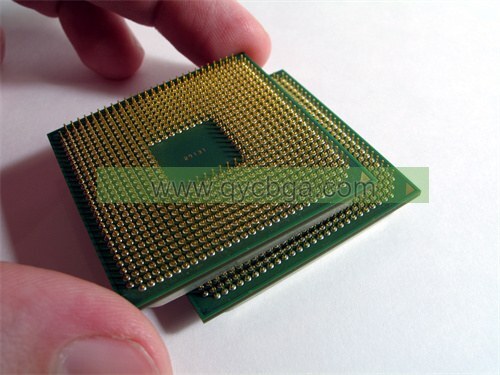
Military Circuit Board Manufacturer
What are the Military Circuit Board Design Guidelines?
Military circuit board design guidelines encompass a range of considerations to ensure that the circuit boards meet the stringent requirements of military applications. Some key guidelines include:
Qwq1. Ruggedization: The circuit board should be designed to withstand harsh environmental conditions, including temperature extremes, shock, 진동, humidity, and exposure to contaminants such as dust and moisture.
- Reliability: Military circuit boards must be highly reliable to ensure continuous operation in critical situations. This includes selecting high-quality components, employing robust manufacturing processes, and conducting thorough testing and validation procedures.
- EMI/EMC Compliance: Electromagnetic interference (이엠아이) and electromagnetic compatibility (EMC) are critical considerations in military applications where interference can disrupt communication or compromise sensitive equipment. Circuit board designs should incorporate measures to mitigate EMI and ensure compliance with relevant standards.
- Power Efficiency: Military systems often operate in remote or resource-constrained environments, so power efficiency is crucial to extend battery life and reduce logistical burdens. Designers should optimize power consumption through efficient circuitry design and the selection of low-power components.
- Security: Military circuit boards may incorporate security features to protect against unauthorized access, tampering, or data breaches. This can include encryption capabilities, secure authentication mechanisms, and physical security measures.
- Conformal Coating: Applying conformal coating to the circuit board helps protect it from moisture, dust, chemicals, and other contaminants, enhancing reliability and longevity, particularly in rugged environments.
- Component Selection: Choosing components with extended temperature ranges, high reliability ratings, and long-term availability is essential for ensuring the longevity and reliability of military circuit boards.
- Design for Manufacturability (DFM): Designing the circuit board with manufacturability in mind can streamline the production process and reduce costs. This includes optimizing component placement, minimizing complex routing, and adhering to industry-standard design practices.
- Testing and Qualification: Rigorous testing and qualification processes are necessary to verify the performance, 신뢰도, and compliance of military circuit boards with relevant standards and specifications.
By adhering to these guidelines, designers can create military circuit boards that meet the demanding requirements of military applications, ensuring reliability, durability, and performance in challenging environments.
What is the Military Circuit Board Fabrication Process?
The fabrication process for military circuit boards involves several steps to ensure that the boards meet the high standards of reliability and performance required for military applications. Here is an overview of the typical process:
- 디자인: The process begins with the design of the circuit board. Designers use specialized software to create the layout of the board, including the placement of components, routing of traces, and implementation of any required features such as impedance control or high-speed signaling.
- 재료 선택: Military circuit boards often use high-quality materials that can withstand harsh environmental conditions and provide excellent performance. Common materials include FR-4 epoxy laminate for the substrate and copper for the conductive traces.
- Preparation of Substrate: The substrate material, typically a fiberglass-reinforced epoxy laminate, is prepared by cutting it to the required size and shape. Surface treatments may be applied to improve adhesion and facilitate the subsequent processes.
- Copper Cladding: A thin layer of copper foil is bonded to one or both sides of the substrate material. This copper layer serves as the conductive material for the circuit traces and pads.
- Photoresist Application: A layer of photoresist is applied to the surface of the copper-clad substrate. The photoresist is sensitive to light and will be used to transfer the circuit pattern onto the copper layer.
- Exposure and Development: The circuit pattern is transferred onto the photoresist using a process called photolithography. A mask containing the desired pattern is aligned with the substrate, and UV light is used to expose the photoresist. After exposure, the unexposed areas of the photoresist are removed through a development process, leaving behind the pattern of the circuit traces.
- 에칭: The exposed copper areas not protected by the developed photoresist are etched away using a chemical solution. This process removes the unwanted copper, leaving behind the desired circuit traces and pads.
- Strip and Clean: The remaining photoresist is stripped away, leaving the bare copper traces on the substrate. The board is then cleaned to remove any residues from the fabrication process.
- 드릴링: Holes are drilled at specified locations on the circuit board for through-hole components or vias. These holes are typically drilled using computer-controlled drilling machines.
- Plating: Copper is plated onto the walls of the drilled holes to create electrical connections between different layers of the circuit board. This process is called electroplating.
- 표면 마감: A surface finish is applied to protect the exposed copper surfaces and provide solderability for component attachment. Common surface finishes for military circuit boards include HASL (뜨거운 공기 솔더 레벨링), 수수께끼 (무전해 니켈 침지 금), 그리고 이머젼 실버.
- 최종 검사: The completed circuit boards undergo a thorough inspection to ensure that they meet the required specifications for quality, 신뢰도, and performance. This may include visual inspection, 전기 테스트, and dimensional measurements.
Once the fabrication process is complete and the circuit boards have passed inspection, they are ready for assembly with electronic components to create finished military systems or subsystems.
How do you manufacture a Military Circuit Board (MCB)?
Manufacturing a Military Circuit Board (MCB) involves a series of steps that are similar to the general circuit board fabrication process but with additional considerations for meeting military standards and requirements. Here’s an outline of the typical manufacturing process for MCBs:
- Design and Prototyping:The process begins with the design of the MCB, taking into account the specific requirements of the military application, such as ruggedness, 신뢰도, and security. Prototyping may be conducted to validate the design before proceeding to full-scale manufacturing.
- 재료 선택: High-quality materials are chosen for the MCB to ensure reliability and performance under harsh conditions. This includes selecting substrate materials such as FR-4 epoxy laminate or specialized materials with enhanced properties for military applications.
- Preparation of Substrate: The substrate material is prepared by cutting it to the required size and shape. Surface treatments may be applied to improve adhesion and facilitate subsequent processes.
- Copper Cladding: Thin layers of copper foil are bonded to one or both sides of the substrate material to serve as the conductive material for the circuit traces and pads.
- Circuit Pattern Transfer: The desired circuit pattern is transferred onto the copper-clad substrate using photolithography techniques. A layer of photoresist is applied, exposed to UV light through a mask containing the circuit pattern, and then developed to remove the unexposed photoresist, leaving behind the pattern of the circuit traces.
- 에칭: The exposed copper areas not protected by the developed photoresist are etched away using a chemical solution, leaving behind the desired circuit traces and pads on the substrate.
- 드릴링: Holes are drilled at specified locations on the circuit board for through-hole components or vias. Computer-controlled drilling machines are used to ensure precise hole placement and dimension.
- Plating: Copper is plated onto the walls of the drilled holes to create electrical connections between different layers of the circuit board. This process, known as electroplating, enhances the reliability and conductivity of the MCB.
- 표면 마감: A surface finish is applied to protect the exposed copper surfaces and provide solderability for component attachment. Common surface finishes for MCBs include HASL (뜨거운 공기 솔더 레벨링), 수수께끼 (무전해 니켈 침지 금), 그리고 이머젼 실버.
- Component Assembly: Electronic components are assembled onto the MCB using automated pick-and-place machines or manual soldering techniques, depending on the complexity of the assembly and the size of the components.
- 테스트 및 검사: The assembled MCBs undergo rigorous testing and inspection to ensure that they meet the required specifications for quality, 신뢰도, and performance. This may include functional testing, 전기 테스트, and inspection for defects.
- Conformal Coating: 경우에 따라, MCBs may be coated with a protective conformal coating to enhance resistance to moisture, dust, and other environmental factors.
- 최종 검사 및 포장: Once testing and inspection are complete, the MCBs are subjected to a final inspection to verify compliance with military standards and requirements. They are then packaged and prepared for shipment to the end user or integration into military systems.
제조 공정 전반에 걸쳐, strict quality control measures are implemented to ensure that MCBs meet the stringent standards and reliability requirements of military applications. Compliance with industry standards such as IPC-A-600 and MIL-PRF-31032 is often necessary to ensure the highest level of quality and performance.
How much should a Military Circuit Board (MCB) 비용?
The cost of a Military Circuit Board (MCB) can vary widely depending on several factors, including the complexity of the design, the materials used, the manufacturing processes involved, and the quantity ordered. Since MCBs are built to meet the stringent requirements and standards of military applications, they often involve higher quality materials, specialized manufacturing techniques, and additional testing and inspection compared to commercial-grade circuit boards.
Here are some factors that can influence the cost of an MCB:
- Complexity of Design: MCBs with complex designs, high component density, and advanced features may require more sophisticated manufacturing processes, which can increase production costs.
- 재료 선택: High-quality materials suitable for military applications, such as specialized substrates and surface finishes, may be more expensive than standard materials used in commercial circuit boards.
- 제조 공정: Specialized manufacturing processes required for MCBs, such as controlled impedance routing, sequential lamination, and additional testing and inspection steps, can contribute to higher production costs.
- Quantity Ordered: Economies of scale apply to the production of MCBs, meaning that larger quantities typically result in lower unit costs. 그렇지만, small production runs may incur higher setup costs per unit.
- Testing and Certification: MCBs for military applications often require extensive testing and certification to ensure compliance with military standards and specifications. These additional testing and qualification processes can add to the overall cost.
- Supplier Selection: The choice of PCB manufacturer or supplier can also impact the cost of MCBs. Different suppliers may offer varying levels of expertise, 질, and pricing.
Due to the wide range of factors influencing the cost of MCBs, it’s challenging to provide a specific price without detailed information about the design requirements and manufacturing specifications. 그렇지만, MCBs typically cost more than standard commercial-grade circuit boards due to their specialized nature and the higher level of quality, 신뢰도, and performance required for military applications.
What is Military Circuit Board Base Material?
The base material for Military Circuit Boards (MCBs) is carefully selected to ensure durability, 신뢰도, and performance in harsh environments typical of military applications. Several materials are commonly used as substrates for MCBs, each offering different properties and advantages. Here are some of the key materials used:
- FR-4 Epoxy: 프렌-4 (난연성 4) epoxy laminate is one of the most widely used materials for circuit board substrates, including MCBs. It offers good mechanical strength, thermal stability, and electrical insulation properties. FR-4 is a fiberglass-reinforced epoxy laminate, providing excellent dimensional stability and resistance to environmental factors.
- 구체의 (PI): Polyimide substrates, such as Kapton, are known for their high-temperature resistance, making them suitable for MCBs operating in extreme temperature environments. Polyimide films offer excellent electrical insulation properties, 융통성, and resistance to chemicals and radiation.
- Rogers High Frequency Laminates: Rogers Corporation manufactures specialized high-frequency laminates designed for RF/microwave applications, including military communication systems and radar. These laminates offer low dielectric loss, controlled impedance, and excellent signal integrity at high frequencies.
- 메탈 코어: Metal core substrates, 알루미늄 구리와 같은, are used for MCBs requiring enhanced thermal conductivity and heat dissipation capabilities. Metal core boards are often used in power electronics applications and LED lighting systems deployed in military vehicles or aircraft.
- 질그릇의: Ceramic substrates offer high thermal conductivity, excellent dimensional stability, and resistance to extreme temperatures and harsh environments. Ceramic MCBs are commonly used in high-power applications, such as power amplifiers and radio frequency (RF) modules.
- Teflon (PTFE): Polytetrafluoroethylene (PTFE), commonly known by the brand name Teflon, is used in specialty MCBs requiring high-frequency performance, low dielectric loss, and stability over a wide temperature range. PTFE-based laminates offer exceptional electrical properties and are often used in military radar systems and satellite communication equipment.
The choice of base material for MCBs depends on the specific requirements of the application, including operating conditions, frequency range, thermal management needs, and cost considerations. Military circuit board designers carefully evaluate these factors to select the most suitable substrate material to meet the performance and reliability requirements of the intended military application.
Which company manufactures Military Circuit Boards?
Many companies manufacture military circuit boards, and some well-known manufacturers include Northrop Grumman, Lockheed Martin, Raytheon, and others. These companies specialize in military technology and systems, offering a variety of military circuit boards to meet different military needs, including communication, radar, navigation, weapons systems, and more.
As for our company, we are also a professional circuit board manufacturer with advanced technology and equipment capable of producing high-quality military circuit boards. We prioritize quality control and strictly adhere to international standards and military specifications to ensure that our products meet the stringent requirements of military applications. Our manufacturing process covers various aspects from design to production, including material selection, process flow, 테스트, and quality inspection, to ensure that the military circuit boards we produce have excellent reliability, stability, and performance.
We have an experienced team of engineers who can customize circuit board designs according to the specific requirements of customers, providing comprehensive technical support and services. Whether it’s small-batch production or large-scale orders, we can flexibly meet customer needs and ensure timely delivery.
요약하면 다음과 같습니다, as a professional circuit board manufacturer, our company has the technology, equipment, and experience required to produce military circuit boards, providing high-quality, reliable products to meet customer needs in the military application field.
무엇입니까 7 좋은 고객 서비스의 품질?
Good customer service is characterized by several key qualities that contribute to positive interactions and experiences for customers. Here are seven essential qualities:
- 응답성: Good customer service involves being prompt and responsive to customer inquiries, requests, and concerns. Responding to customers in a timely manner demonstrates attentiveness and a commitment to addressing their needs promptly.
- 공감: Empathy is the ability to understand and share the feelings of others. Good customer service representatives listen actively to customers, show understanding of their concerns, and strive to put themselves in the customer’s shoes to provide appropriate assistance and support.
- Clear Communication:Effective communication is essential for providing good customer service. Customer service representatives should communicate clearly, using language that is easy to understand, and provide information in a concise and informative manner. Clear communication helps prevent misunderstandings and ensures that customers receive the assistance they need.
- Knowledgeability: Good customer service representatives possess a deep understanding of the products or services offered by the company. They are knowledgeable about features, benefits, pricing, policies, and procedures, allowing them to answer customer questions accurately and provide helpful guidance and recommendations.
- 전문성: Professionalism encompasses various aspects of behavior, including courtesy, respect, integrity, and reliability. Good customer service representatives maintain a professional demeanor at all times, treating customers with respect, addressing their concerns with courtesy, and conducting themselves ethically and professionally.
- Problem-Solving Skills: Good customer service involves effectively resolving customer issues and concerns. Customer service representatives should be skilled problem solvers, capable of identifying the root cause of problems, exploring potential solutions, and taking appropriate action to resolve issues to the customer’s satisfaction.
- Follow-Up: Following up with customers after their interaction with customer service demonstrates a commitment to customer satisfaction and ensures that their needs have been met. Good customer service representatives may follow up to ensure that issues have been resolved satisfactorily, gather feedback on the customer experience, or provide additional assistance or support as needed.
이러한 특성을 구현함으로써, companies can deliver exceptional customer service experiences that foster customer loyalty, satisfaction, and trust.
자주 묻는 질문(FAQ)
What are Military Circuit Boards (MCBs)?
MCBs are specialized circuit boards designed and manufactured to meet the rigorous standards and requirements of military applications. They are built to withstand harsh environmental conditions, provide high reliability, and ensure optimal performance in military systems.
What makes MCBs different from commercial circuit boards?
MCBs undergo additional testing, qualification, and certification processes to ensure they meet military standards for reliability, durability, and performance. They are built using ruggedized materials and manufacturing techniques to withstand extreme conditions such as temperature variations, shock, 진동, 및 전자기 간섭.
What are the main applications of MCBs?
MCBs are used in a wide range of military systems and equipment, including communication devices, 레이더 시스템, navigation systems, weapons systems, electronic warfare equipment, and more.
What are some key features of MCBs?
MCBs often incorporate features such as conformal coating for protection against moisture and contaminants, high-temperature materials for operation in extreme environments, controlled impedance routing for signal integrity, and secure design features to prevent tampering or unauthorized access.
What standards and specifications do MCBs need to meet?
MCBs must meet various military standards and specifications, such as MIL-PRF-31032, MIL-PRF-55110, and IPC-A-600, which outline requirements for materials, 제조 공정, 테스트, and performance.
Can MCBs be customized for specific military applications?
Yes, MCBs can be customized to meet the unique requirements of different military systems and equipment. Designers can tailor the circuit board layout, materials, and features to optimize performance and reliability for specific applications.
How are MCBs tested and validated?
MCBs undergo rigorous testing and validation processes to ensure they meet military standards and specifications. 여기에는 전기 테스트가 포함될 수 있습니다., 열 순환, vibration testing, humidity testing, and more, depending on the requirements of the application.
Who manufactures MCBs?
Several companies specialize in the design and manufacture of MCBs, including both large defense contractors and specialized electronics manufacturers with expertise in military-grade components and systems.