Ceramic Substrates For LED PCB Manufacturer
Ceramic Substrates For LED PCB Manufacturer,Ceramic substrates for LED PCBs are specialized platforms designed to optimize the performance and reliability of LED lighting systems. Made from high-quality ceramic materials such as aluminum oxide (알2O3) or aluminum nitride (알엔), these substrates offer exceptional thermal conductivity and electrical insulation properties. By efficiently dissipating heat generated by LEDs, ceramic substrates help maintain optimal operating temperatures, enhancing LED performance and longevity. Their excellent dimensional stability ensures precise placement of LED components, while high electrical insulation prevents short circuits, ensuring safety and reliability. Customizable in terms of size, shape, and surface features, ceramic substrates can be tailored to meet the specific requirements of various LED applications, from automotive lighting to industrial and residential lighting solutions. With their superior thermal management capabilities and durability, ceramic substrates play a vital role in advancing the efficiency and reliability of LED lighting technology.
What are Ceramic Substrates for LED PCBs?
Ceramic substrates for LED PCBs are specialized platforms designed to support and enhance the performance of LED (Light Emitting Diode) components. These substrates are made from ceramic materials such as aluminum oxide (알2O3) or aluminum nitride (알엔), which offer excellent thermal conductivity and electrical insulation properties.
LEDs generate heat during operation, which can degrade their performance and lifespan if not efficiently dissipated. Ceramic substrates provide superior thermal management compared to traditional materials like FR4, allowing LEDs to operate at higher power levels while maintaining reliability.
또한, ceramic substrates offer excellent dimensional stability, ensuring precise placement of LED components and maintaining consistent performance over time. They also provide high electrical insulation, preventing short circuits and ensuring safety in LED applications.
The design and manufacturing process of ceramic substrates can vary depending on specific application requirements, including LED type, power output, and environmental conditions. Advanced techniques such as thin-film deposition and laser processing may be employed to create intricate patterns and features on the substrate surface, optimizing LED performance further.
전반적, ceramic substrates play a crucial role in maximizing the efficiency, 신뢰도, and longevity of LED-based lighting systems, making them essential components in various industries ranging from automotive to aerospace, and from consumer electronics to industrial lighting.
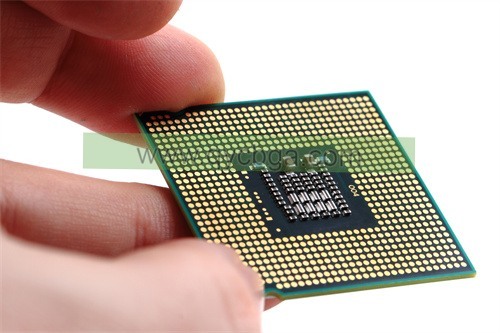
Ceramic Substrates For LED PCB Manufacturer
What are the Design Guidelines for Ceramic Substrates for LED PCBs?
Designing 세라믹 기판 for LED PCBs involves careful consideration of several key factors to ensure optimal performance and reliability. Here are some design guidelines to follow:
- 열 관리: Ensure efficient heat dissipation by incorporating thermal vias, 써멀 패드, or metal core layers to transfer heat away from the LED components and dissipate it effectively. Consider the thermal conductivity of the ceramic material and its thickness to meet thermal requirements.
- 전기 절연: Ceramic substrates should provide high electrical insulation to prevent short circuits and ensure safety. Design for appropriate spacing between conductive traces and components, and choose ceramic materials with high dielectric strength.
- 치수 안정성: Ceramic substrates should maintain dimensional stability under thermal cycling and mechanical stress. Consider the coefficient of thermal expansion (증권 시세 표시기) of the ceramic material and its compatibility with other materials in the assembly to prevent warping or delamination.
- LED Placement and Layout: Position LED components strategically to optimize light distribution and minimize thermal gradients. Use simulation tools to analyze LED placement and layout for uniform illumination and efficient heat dissipation.
- Solderability and Compatibility: Ensure that the ceramic substrate is compatible with soldering processes and materials used for attaching LED components. Choose solder mask materials and surface finishes suitable for ceramic substrates to achieve reliable solder joints.
- Environmental Considerations: Consider the operating environment of the LED PCB, including temperature extremes, humidity, and exposure to chemicals or contaminants. Select ceramic materials with appropriate resistance to environmental factors to ensure long-term reliability.
- 제조 가능성: Design for manufacturability by considering the capabilities and limitations of ceramic substrate fabrication processes, such as laser machining, 금속, and thin-film deposition. Optimize design features for cost-effective production and assembly.
- Testing and Quality Assurance: Implement testing procedures to verify the performance and reliability of ceramic substrates for LED PCBs. Conduct thermal, electrical, and mechanical testing to validate design specifications and ensure consistent quality.
By adhering to these design guidelines, engineers can develop ceramic substrates that meet the stringent requirements of LED lighting applications, delivering superior performance, 신뢰도, and longevity.
What is the Fabrication Process for Ceramic Substrates for LED PCBs?
The fabrication process for 세라믹 기판 for LED PCBs involves several steps to create a durable and reliable platform for mounting LED components. Here’s an overview of the typical fabrication process:
- 재료 선택: Choose the appropriate ceramic material based on thermal conductivity, electrical insulation properties, and compatibility with LED application requirements. Common choices include aluminum oxide (알2O3) 및 질화알루미늄 (알엔).
- 기판 준비: Start with ceramic sheets or panels and prepare them for processing. This may involve cutting the ceramic material to the desired size and shape using techniques such as laser cutting or mechanical cutting.
- 표면 처리: Clean the ceramic substrate surface to remove any contaminants or impurities that could affect subsequent processing steps. Surface treatment methods may include chemical etching or plasma cleaning to improve adhesion and solderability.
- 금속: Apply metal layers to the ceramic substrate surface to create conductive traces and pads for mounting LED components. Metallization can be achieved through various techniques such as screen printing, sputtering, or thick-film deposition.
- Pattern Definition: Define the circuit pattern and layout on the ceramic substrate using photolithography or screen printing techniques. Photomasks or stencils are used to transfer the desired pattern onto the substrate surface, creating precise features for LED placement and interconnects.
- 에칭: Remove unwanted metal layers from the ceramic substrate surface using chemical etching or plasma etching processes. Etching selectively removes metal material, leaving behind the desired circuit pattern and interconnects.
- 유전층 증착: Deposit dielectric layers on the substrate surface to insulate conductive traces and protect against short circuits. Dielectric materials such as glass or ceramic-based films are applied using techniques like spin coating, chemical vapor deposition (증권 시세 표시기), or physical vapor deposition (PVD).
- 비아 포메이션: Create vias or holes in the ceramic substrate to facilitate electrical connections between different layers or components. Vias may be formed using drilling, 레이저 절제, or chemical etching techniques, followed by metalization to establish electrical continuity.
- 표면 마감: Apply a surface finish to the ceramic substrate to improve solderability and protect against oxidation. Common surface finishes include immersion tin, immersion silver, or gold plating, which provide a flat, solderable surface for mounting LED components.
- Quality Control: Perform thorough inspection and testing of the fabricated ceramic substrates to ensure they meet design specifications and quality standards. This may involve dimensional measurements, electrical continuity testing, and visual inspection for defects.
By following these fabrication steps, manufacturers can produce ceramic substrates tailored to the specific requirements of LED PCBs, offering superior thermal management, electrical insulation, and reliability for a wide range of lighting applications.
How are Ceramic Substrates for LED PCBs Manufactured?
Manufacturing ceramic substrates for LED PCBs involves a series of processes to create a durable and functional platform for mounting LED components. 다음은 일반적인 제조 공정에 대한 개요입니다:
- Material Preparation: The manufacturing process begins with the selection of ceramic materials such as aluminum oxide (알2O3) or aluminum nitride (알엔). These materials are typically sourced in the form of sheets or panels. The ceramic material may undergo additional preparation steps such as milling or grinding to achieve the desired thickness and surface smoothness.
- Sheet Cutting: The ceramic sheets or panels are cut to the required size and shape using techniques such as laser cutting, water jet cutting, or mechanical cutting. Precision cutting ensures uniformity and consistency in the dimensions of the ceramic substrates.
- Surface Cleaning: The surfaces of the ceramic substrates are thoroughly cleaned to remove any contaminants, oils, or residues that could affect subsequent processing steps. Cleaning methods may include solvent cleaning, ultrasonic cleaning, or plasma cleaning.
- 금속: Metal layers are applied to the ceramic substrate surfaces to create conductive traces and pads for mounting LED components. Metallization can be achieved through techniques such as screen printing, sputtering, or thick-film deposition. The metal layers may consist of materials such as copper, silver, or gold.
- Pattern Definition: The circuit pattern and layout are defined on the ceramic substrate surfaces using photolithography or screen printing techniques. Photomasks or stencils are used to transfer the desired pattern onto the substrate surface, creating precise features for LED placement and interconnects.
- 에칭:Unwanted metal layers are selectively removed from the ceramic substrate surfaces using chemical etching or plasma etching processes. Etching removes metal material from areas not protected by the pattern, leaving behind the desired circuit pattern and interconnects.
- 유전층 증착: Dielectric layers are deposited onto the substrate surfaces to insulate conductive traces and protect against short circuits. Dielectric materials such as glass or ceramic-based films are applied using techniques like spin coating, chemical vapor deposition (증권 시세 표시기), or physical vapor deposition (PVD).
- 비아 포메이션:Vias or holes are created in the ceramic substrates to facilitate electrical connections between different layers or components. Vias may be formed using drilling, 레이저 절제, or chemical etching techniques, followed by metalization to establish electrical continuity.
- 표면 마감: A surface finish is applied to the ceramic substrates to improve solderability and protect against oxidation. Common surface finishes include immersion tin, immersion silver, or gold plating, providing a flat, solderable surface for mounting LED components.
- Quality Control: The manufactured ceramic substrates undergo rigorous inspection and testing to ensure they meet design specifications and quality standards. This may include dimensional measurements, electrical continuity testing, and visual inspection for defects.
By following these manufacturing processes, producers can create ceramic substrates tailored to the specific requirements of LED PCBs, offering superior thermal management, electrical insulation, and reliability for various lighting applications.
How much should Ceramic Substrates for LED PCBs cost?
The cost of ceramic substrates for LED PCBs can vary widely depending on several factors, including the material used, size and thickness of the substrate, complexity of the design, manufacturing processes involved, and order quantity. Here are some considerations that can impact the cost:
- 재료비: Ceramic materials like aluminum oxide (알2O3) or aluminum nitride (알엔) can vary in price depending on factors such as purity, grade, and availability. Higher purity materials or specialized formulations may command a higher cost.
- 제조 공정: The complexity of the manufacturing processes involved in producing ceramic substrates, such as metallization, 에칭, and dielectric layer deposition, can influence costs. Additional processes like laser cutting or surface finishing may also add to the overall cost.
- Design Complexity: More intricate designs with finer features, tighter tolerances, or multiple layers may require additional processing steps and specialized equipment, leading to higher manufacturing costs.
- Order Quantity: Economies of scale often apply in manufacturing, meaning larger order quantities typically result in lower per-unit costs. Bulk orders may be eligible for volume discounts, reducing the overall cost per substrate.
- Quality and Reliability Requirements: Meeting stringent quality and reliability standards may necessitate additional testing and inspection procedures, as well as the use of higher-quality materials and manufacturing processes, which can impact costs.
- 사용자 정의 및 특별 요구 사항: Customized features, special surface finishes, or unique requirements specified by the customer may incur additional costs compared to standard off-the-shelf substrates.
Given these factors, it’s challenging to provide a specific cost estimate without knowing the exact specifications and requirements of the ceramic substrates for LED PCBs. Prices can range from a few dollars to several tens of dollars per substrate, with bulk orders typically offering lower unit costs. Companies specializing in the manufacture of ceramic substrates can provide detailed quotes based on specific project requirements.
What is the Base Material for Ceramic Substrates for LED PCBs?
The base material for ceramic substrates used in LED PCBs typically consists of ceramic compounds chosen for their excellent thermal conductivity, electrical insulation properties, and mechanical strength. Two common ceramic materials used as base substrates for LED PCBs are:
- Aluminum Oxide (알2O3): Also known as alumina, aluminum oxide is a widely used ceramic material in LED PCBs. It offers good thermal conductivity, electrical insulation, and mechanical stability. Alumina substrates are relatively cost-effective and suitable for various LED applications.
- Aluminum Nitride (알엔): Aluminum nitride is another popular choice for ceramic substrates in LED PCBs. It exhibits even higher thermal conductivity than alumina, making it particularly suitable for applications requiring efficient heat dissipation. AlN substrates also offer excellent electrical insulation and reliability.
Both aluminum oxide and aluminum nitride substrates can be manufactured in various thicknesses and sizes to accommodate different LED PCB designs and requirements. These ceramic materials provide a stable and reliable platform for mounting LED components while ensuring efficient thermal management and electrical isolation.
Which Company Manufactures Ceramic Substrates for LED PCBs?
There are many companies specialized in the manufacturing of ceramic substrates for LED PCBs, some well-known ones include Kyocera, Ceramtec, CoorsTek, Maruwa, and others. These companies have extensive experience and technological expertise in the LED lighting and electronics industries, offering various specifications and types of ceramic substrates to meet specific customer needs.
In our company, we are also one of the professional manufacturers of ceramic substrates for LED PCBs. We have advanced production equipment and a skilled technical team dedicated to providing high-quality, high-performance ceramic substrate solutions.
Our ceramic substrate manufacturing process employs advanced techniques and rigorous quality control measures to ensure products meet industry standards and customer requirements. Our production capabilities cover various ceramic materials, including aluminum oxide (알2O3), aluminum nitride (알엔), among others, catering to different application scenarios.
Features and advantages of our ceramic substrate products include:
High Thermal Conductivity: Our ceramic substrates offer excellent thermal conductivity, effectively dissipating the heat generated by LEDs, thus enhancing LED performance and lifespan.
Excellent Electrical Insulation: Ceramic materials possess outstanding electrical insulation properties, ensuring stability and safety in electrical aspects of LED PCBs.
Stable Dimensions and Shapes: Our ceramic substrates exhibit excellent dimensional stability and shape accuracy, suitable for precise LED assembly and layout.
사용자화: We can customize ceramic substrates according to customer-specific requirements, including size, shape, thickness, and surface treatment, to meet various project needs.
High Quality and Reliability: We adhere to strict quality control standards and testing procedures, ensuring each ceramic substrate meets specification requirements and delivers reliable performance.
As a manufacturer of ceramic substrates for LED PCBs, we are committed to providing customers with high-performance, high-quality products and collaborating with them to drive advancements in the LED lighting and electronics industries. We are dedicated to listening to customer needs, offering tailored solutions, and building long-term partnerships with them.
무엇입니까 7 Qualities of Good Customer Service?
Seven qualities of good customer service include:
- 공감: Understanding and empathizing with the customer’s needs, concerns, and emotions fosters a positive connection and demonstrates genuine care for their experience.
- Effective Communication: Clear and concise communication is essential for conveying information, providing assistance, and resolving issues promptly. Active listening and responsiveness are also crucial components of effective communication.
- 전문성: Maintaining professionalism in all interactions with customers instills confidence and trust. This includes being courteous, respectful, and maintaining a positive attitude, 어려운 상황에서도.
- Product Knowledge:Having a thorough understanding of the products or services being offered enables customer service representatives to answer questions accurately, provide helpful recommendations, and address concerns effectively.
- Problem-Solving Skills:The ability to identify and resolve customer issues efficiently is vital for delivering satisfactory outcomes. 고객 서비스 담당자는 수완이 풍부해야 합니다., 사전, and capable of finding solutions tailored to each customer’s needs.
- Reliability: Consistency and reliability in delivering service create a sense of trust and reliability. Meeting or exceeding customer expectations consistently builds loyalty and enhances the overall customer experience.
- Flexibility and Adaptability: Being flexible and adaptable to changing circumstances allows customer service representatives to accommodate varying customer needs and preferences. Adjusting communication styles, problem-solving approaches, and service delivery methods as needed demonstrates a commitment to customer satisfaction.
자주 묻는 질문(FAQ)
What are ceramic substrates for LED PCBs?
Ceramic substrates for LED PCBs are specialized platforms made from ceramic materials such as aluminum oxide (알2O3) or aluminum nitride (알엔). They provide a stable and reliable foundation for mounting LED components in lighting applications.
What are the advantages of using ceramic substrates for LED PCBs?
Ceramic substrates offer several advantages, including excellent thermal conductivity for efficient heat dissipation, 높은 전기 절연 특성, dimensional stability, and reliability in harsh environments.
How do ceramic substrates enhance LED performance?
By efficiently dissipating heat generated by LEDs, ceramic substrates help maintain optimal operating temperatures, which can improve LED performance, longevity, and reliability. They also provide electrical isolation to prevent short circuits and enhance overall system efficiency.
What types of ceramic materials are used for LED PCB substrates?
Common ceramic materials used for LED PCB substrates include aluminum oxide (알2O3) 및 질화알루미늄 (알엔) due to their favorable thermal and electrical properties. Other specialized ceramics may also be used depending on specific application requirements.
Can ceramic substrates be customized for specific LED applications?
Yes, ceramic substrates can be customized in terms of size, shape, thickness, and surface features to meet the unique requirements of different LED applications. Customization allows for optimized thermal management, electrical performance, and mechanical integration.
Are ceramic substrates cost-effective compared to other materials?
While ceramic substrates may have higher initial costs compared to traditional materials like FR4, they offer superior thermal management and reliability, which can result in long-term cost savings by extending LED lifespan and reducing maintenance requirements.
What factors should be considered when selecting ceramic substrates for LED PCBs?
When selecting ceramic substrates, factors such as thermal conductivity, electrical insulation, 기계적 강도, dimensional stability, compatibility with assembly processes, and environmental durability should be taken into account to ensure optimal performance and reliability.