Alumina PCB |Al2O3 PCB Manufacturer
Alumina PCB |Al2O3 PCB Manufacturer,Alumina PCBs, also known as Alumina Ceramic Printed Circuit Boards, represent a cutting-edge solution for industries demanding optimal thermal management and robust performance. Utilizing alumina ceramic as the substrate material, these PCBs boast exceptional thermal conductivity, 기계적 강도, and electrical insulation properties.
Engineered to excel in high-power electronics, RF devices, LED lighting, and other demanding applications, Alumina PCBs offer a unique advantage in dissipating heat effectively, ensuring reliability under challenging conditions. Their ability to withstand high temperatures and harsh environments makes them indispensable in aerospace, 자동차, and industrial sectors.
Designed with meticulous attention to detail, Alumina PCBs adhere to stringent quality standards, offering consistent performance and durability. With advanced manufacturing processes and precise circuitry layout, these PCBs provide an ideal platform for intricate electronic systems, facilitating optimal signal integrity and functionality.
Innovation-driven and versatile, Alumina PCBs continue to redefine the possibilities in electronic design, empowering industries to push the boundaries of performance and efficiency.
What is an Alumina PCB?
An Alumina PCB, or Alumina Ceramic Printed Circuit Board, is a type of circuit board where the substrate material is made of alumina ceramic instead of traditional materials like FR4 (a type of fiberglass-reinforced epoxy laminate). 알 루미나 (알2O3) is a ceramic material known for its excellent thermal conductivity, high mechanical strength, and good electrical insulation properties. These properties make alumina PCBs particularly suitable for applications where high thermal dissipation is required, such as power electronics, high-frequency RF devices, and LED lighting.
Alumina PCBs are typically manufactured using similar processes to traditional PCBs, including etching, 도금, and soldering. 그렇지만, due to the differences in material properties, alumina PCBs may require specialized handling and processing techniques.
전반적, alumina PCBs offer superior thermal performance compared to conventional PCBs, making them ideal for demanding applications where heat management is critical.
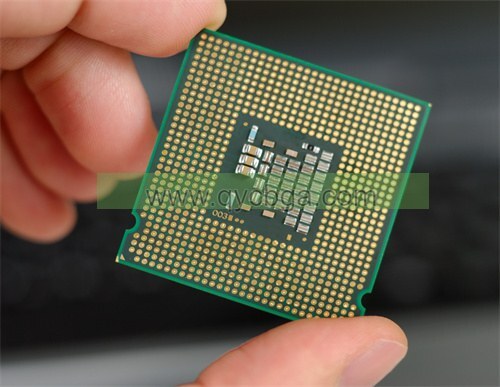
Alumina PCB |Al2O3 PCB Manufacturer
What are the Alumina PCB Design Guidelines?
Designing with alumina PCBs requires attention to specific guidelines to ensure optimal performance and reliability. Here are some key design guidelines for alumina PCBs:
- 열 관리: Alumina PCBs are prized for their excellent thermal conductivity. To maximize this property, ensure that heat-generating components are placed close to areas of high thermal conductivity on the board. Also, provide sufficient thermal vias to efficiently dissipate heat away from critical components.
- Dielectric Properties: Alumina ceramic has high dielectric strength and excellent electrical insulation properties. 그렇지만, it’s essential to consider dielectric constant variations with frequency and temperature when designing high-frequency circuits. Ensure that your design accounts for these variations to maintain signal integrity.
- Mechanical Stability: Alumina ceramic is mechanically robust, but it’s still important to design for mechanical stability. Avoid sharp corners and edges in the layout, which can create stress concentrations. 또한, provide adequate support for heavy components to prevent mechanical failure.
- 표면 마감: Choose appropriate surface finishes for your application. Common options include ENIG (무전해 니켈 침지 금) or OSP (유기 납땜성 방부제). Ensure that the chosen finish is compatible with alumina ceramic substrates and provides good solderability.
- Trace Width and Spacing:Alumina PCBs typically have similar trace width and spacing requirements as standard PCBs. Follow industry-standard guidelines for trace width, spacing, and impedance control, taking into account the specific requirements of your application.
- Component Placement: Place components strategically to minimize signal distortion and interference. Group related components together and route traces efficiently to reduce signal path lengths and impedance mismatches.
- Thermal Expansion: Alumina ceramic has a low coefficient of thermal expansion compared to other PCB materials. Consider the thermal expansion coefficient when designing for temperature variations, especially in applications with wide temperature ranges.
- Assembly Considerations: Alumina PCBs may require special handling during assembly due to their ceramic substrate. Ensure that assembly processes, such as soldering and reflow, are compatible with alumina ceramic materials to prevent damage.
- Grounding and Shielding: Proper grounding and shielding techniques are essential for maintaining signal integrity and minimizing electromagnetic interference (이엠아이). Use ground planes and shielding layers as needed to isolate sensitive signals and components.
- Testing and Validation: Thoroughly test and validate your alumina PCB design before mass production. Perform signal integrity analysis, thermal simulations, and reliability testing to ensure that the design meets performance and reliability requirements.
By following these guidelines, you can create robust and reliable designs leveraging the unique properties of alumina PCBs. 또한, consult with your PCB manufacturer for specific recommendations and considerations based on their capabilities and processes.
What is the Alumina PCB Fabrication Process?
The fabrication process for alumina PCBs is similar to that of traditional printed circuit boards but with some specific considerations due to the use of alumina ceramic as the substrate material. Here’s an overview of the typical fabrication process for alumina PCBs:
- 기판 준비: Alumina ceramic substrates are prepared by cutting them into the desired size and shape. The substrate may also undergo surface treatment processes to improve adhesion and compatibility with subsequent manufacturing steps.
- Printing: The circuit pattern is printed onto the alumina ceramic substrate using various methods such as screen printing, inkjet printing, or photolithography. This step defines the conductive traces, pads, and other features of the PCB.
- Conductor Deposition: Conductive materials, typically metals like copper, are deposited onto the substrate to form the conductive traces and pads. This can be done using techniques such as sputtering, evaporation, or electroplating.
- 에칭: The excess conductor material is removed from the substrate using chemical etching processes. This step leaves behind the desired circuit pattern on the alumina ceramic substrate.
- 비아 포메이션: Vias are drilled or punched through the substrate to establish electrical connections between different layers of the PCB. Specialized drilling techniques may be used to create vias in alumina ceramic substrates.
- Plating: After via formation, plating processes are employed to coat the vias with conductive material, typically copper, to establish electrical continuity between layers.
- 표면 마무리: Surface finishing processes are applied to the PCB to improve solderability and protect the conductive traces from oxidation. Common surface finishes include ENIG (무전해 니켈 침지 금), 증권 시세 표시기 (유기 납땜성 방부제), and HASL (뜨거운 공기 솔더 레벨링).
- Component Attachment: Electronic components are attached to the PCB using soldering techniques such as reflow soldering or wave soldering. Special care may be needed during this step to ensure compatibility with the alumina ceramic substrate.
- 테스트 및 검사: The fabricated PCB undergoes rigorous testing and inspection to ensure that it meets quality standards and performance specifications. 여기에는 전기 테스트가 포함될 수 있습니다., 육안 검사, and functionality testing.
- Final Finishing: 테스트 및 검사가 완료되면, the PCB may undergo final finishing processes such as cleaning and coating to prepare it for use in its intended application.
제작 공정 전반에 걸쳐, careful attention is paid to the unique properties of alumina ceramic substrates to ensure that the resulting PCBs meet the desired performance, 신뢰도, and quality requirements. Collaboration with experienced PCB manufacturers familiar with alumina ceramic materials is often beneficial to ensure successful fabrication.
How do you manufacture an Alumina PCB?
Manufacturing an alumina PCB involves several specialized steps due to the unique properties of alumina ceramic substrates. 다음은 일반적인 제조 공정에 대한 개요입니다:
- 기판 준비: Alumina ceramic substrates are prepared by cutting them into the desired size and shape. The substrates may undergo surface treatment processes to improve adhesion and compatibility with subsequent manufacturing steps.
- Circuit Design: The circuit layout is designed using PCB design software, taking into account the specific requirements of the application and the properties of alumina ceramic. Design considerations include thermal management, 신호 무결성, and mechanical stability.
- Mask Generation:Using the circuit design data, a photomask or stencil is generated to define the circuit pattern on the substrate. The mask contains the areas where conductive material will be deposited onto the substrate.
- Conductor Deposition: Conductive materials, typically metals like copper, are deposited onto the substrate to form the conductive traces and pads. This can be achieved through processes such as sputtering, evaporation, or screen printing.
- Pattern Transfer:The photomask or stencil is aligned and placed over the substrate, and the conductive material is deposited onto the substrate through the openings in the mask. This transfers the circuit pattern onto the substrate.
- 에칭: The excess conductor material is removed from the substrate using chemical etching processes. This step leaves behind the desired circuit pattern on the alumina ceramic substrate.
- 비아 포메이션: Vias are created to establish electrical connections between different layers of the PCB. Specialized drilling or punching techniques are used to create vias in the alumina ceramic substrate.
- Plating: After via formation, plating processes are employed to coat the vias with conductive material, typically copper, to establish electrical continuity between layers.
- 표면 마무리:Surface finishing processes are applied to the PCB to improve solderability and protect the conductive traces from oxidation. Common surface finishes include ENIG (무전해 니켈 침지 금), 증권 시세 표시기 (유기 납땜성 방부제), and HASL (뜨거운 공기 솔더 레벨링).
- Component Attachment: Electronic components are attached to the PCB using soldering techniques such as reflow soldering or wave soldering. Special care may be needed during this step to ensure compatibility with the alumina ceramic substrate.
- 테스트 및 검사: The fabricated PCB undergoes rigorous testing and inspection to ensure that it meets quality standards and performance specifications. 여기에는 전기 테스트가 포함될 수 있습니다., 육안 검사, and functionality testing.
- Final Finishing: 테스트 및 검사가 완료되면, the PCB may undergo final finishing processes such as cleaning and coating to prepare it for use in its intended application.
제조 공정 전반에 걸쳐, specialized equipment and expertise are required to handle the unique properties of alumina ceramic substrates and ensure the successful fabrication of high-quality alumina PCBs. Collaboration with experienced PCB manufacturers familiar with alumina ceramic materials is often essential for achieving optimal results.
How much should an Alumina PCB cost?
The cost of an alumina PCB can vary significantly depending on various factors such as:
- Board Size: Larger boards generally cost more due to the increased material and manufacturing costs.
- Layer Count: The number of layers in the PCB affects the complexity of the manufacturing process and therefore influences the cost.
- Material Thickness: Thicker alumina substrates may cost more than thinner ones due to the increased material usage and machining requirements.
- Copper Thickness: Thicker copper layers typically increase the cost of the PCB due to higher material and processing costs.
- 표면 마감: Different surface finishes have different costs. 예를 들어, finishes like ENIG (무전해 니켈 침지 금) tend to be more expensive than HASL (뜨거운 공기 솔더 레벨링).
- Complexity of Circuit Design:PCBs with intricate or dense circuitry may require more time and precision during manufacturing, resulting in higher costs.
- 양: Larger quantities often lead to lower per-unit costs due to economies of scale. 그렇지만, setup costs for production may affect the overall cost.
- Lead Time: Expedited manufacturing options usually come with additional costs.
- Quality Standards: Meeting specific quality standards or certifications may add to the overall cost of manufacturing.
To get an accurate cost estimate for an alumina PCB, it’s best to consult with PCB manufacturers or suppliers directly. They can provide quotes based on your specific requirements and volume needs. 또한, consider obtaining quotes from multiple manufacturers to compare pricing and services.
What is Alumina PCB base material?
The base material for alumina PCBs is alumina ceramic, also known as aluminum oxide (알2O3). Alumina ceramic is a type of ceramic material that is widely used in various industrial applications due to its excellent thermal conductivity, high mechanical strength, and good electrical insulation properties.
Alumina ceramic substrates for PCBs are typically manufactured using a process called ceramic substrate manufacturing. This process involves shaping and sintering alumina ceramic powder to form rigid and stable substrates with precise dimensions and properties suitable for PCB applications.
Alumina ceramic substrates provide several advantages for PCBs, 포함:
- High Thermal Conductivity: Alumina ceramic has excellent thermal conductivity, allowing for efficient heat dissipation from electronic components.
- Mechanical Stability: Alumina ceramic substrates are mechanically robust, providing excellent support for electronic components and resistance to mechanical stresses.
- 전기 절연: Alumina ceramic has good electrical insulation properties, which prevent short circuits and ensure reliable performance of electronic circuits.
- Chemical Resistance: Alumina ceramic is resistant to many chemicals and environmental factors, enhancing the durability and reliability of alumina PCBs.
전반적, alumina ceramic serves as an ideal base material for PCBs in applications where high thermal performance, mechanical stability, and reliability are critical requirements.
Which company makes Alumina PCB?
There are many companies that produce Alumina PCBs, including well-known companies such as CeramTec, Kyocera, and CoorsTek. These companies have advanced technology and equipment to manufacture high-quality Alumina PCBs to meet various application requirements.
As for our company, we can also produce Alumina PCBs, providing customized solutions for customers. With an experienced engineering team and advanced production equipment, we can meet various demands for Alumina PCBs.
Our production process strictly follows industry standards and quality control requirements, ensuring that each Alumina PCB has excellent performance and reliability. We collaborate with customers from design to production, offering comprehensive support and services to meet their specific application requirements.
Our advantages include:
- Customized Solutions: We can customize Alumina PCBs according to customer requirements, including size, layer count, material thickness, copper thickness, etc.
- High-Quality Materials: We use high-quality Alumina ceramic as the substrate material, ensuring excellent thermal conductivity, mechanical stability, and electrical insulation of the PCBs.
- Advanced Production Equipment: With advanced production equipment and processes, we can achieve high-precision machining and production, ensuring the quality and performance of PCBs.
- Strict Quality Control: We implement strict quality control measures, conducting rigorous inspections and tests at every stage from raw material procurement to production, ensuring that products meet customer requirements and industry standards.
- Timely Delivery: We can deliver orders on time, ensuring that customers’ production schedules proceed smoothly.
Through collaboration with us, customers can obtain high-quality customized Alumina PCBs with excellent performance and reliability for their applications. We are committed to providing customers with excellent products and services to meet their various needs and challenges.
무엇입니까 7 좋은 고객 서비스의 품질?
Good customer service is characterized by several key qualities that contribute to positive experiences for customers. Here are seven qualities of good customer service:
- 응답성:Good customer service involves promptly addressing customer inquiries, concerns, and issues. Responding to customers in a timely manner demonstrates respect for their time and shows that their needs are valued.
- 공감: Empathy involves understanding and acknowledging the customer’s perspective, feelings, and concerns. Customer service representatives who demonstrate empathy can build rapport with customers and create a supportive environment for problem resolution.
- 전문성: Professionalism in customer service entails maintaining a courteous and respectful demeanor at all times, regardless of the situation. Professional customer service representatives are knowledgeable, reliable, and maintain a positive attitude when interacting with customers.
- Communication Skills: Effective communication is essential for providing good customer service. Customer service representatives should be able to convey information clearly and concisely, listen actively to customers’ needs, and adapt their communication style to match the customer’s preferences.
- Problem-Solving Abilities: Good customer service involves the ability to effectively resolve customer issues and complaints. 고객 서비스 담당자는 수완이 풍부해야 합니다., 사전, and empowered to find solutions that meet the customer’s needs and expectations.
- Consistency: Consistency in customer service ensures that customers receive the same level of quality and attention across all interactions with a company. Consistent service delivery builds trust and loyalty with customers and reinforces the company’s reputation for reliability.
- Follow-Up: Following up with customers after their inquiries or issues have been addressed demonstrates a commitment to their satisfaction. Customer service representatives can follow up to ensure that the customer’s needs were met, gather feedback for improvement, and maintain ongoing relationships with customers.
이러한 특성을 구현함으로써, businesses can create positive experiences for customers and foster long-term relationships that drive customer satisfaction and loyalty.
자주 묻는 질문(FAQ)
What is an Alumina PCB?
An Alumina PCB, or Alumina Ceramic Printed Circuit Board, is a type of circuit board where the substrate material is made of alumina ceramic instead of traditional materials like FR4. Alumina ceramic offers excellent thermal conductivity, 기계적 강도, and electrical insulation properties.
What are the advantages of using Alumina PCBs?
Alumina PCBs offer superior thermal performance, making them suitable for applications where high heat dissipation is required. They also provide excellent mechanical stability, electrical insulation, 환경 요인에 대한 내성.
What are the typical applications of Alumina PCBs?
Alumina PCBs are commonly used in high-power electronics, RF devices, LED lighting, 항공 우주, 자동차, and other applications where thermal management is critical.
How are Alumina PCBs manufactured?
The manufacturing process for Alumina PCBs involves similar steps to traditional PCB fabrication, but with specific considerations for alumina ceramic substrates. This process includes substrate preparation, circuit design, conductor deposition, 에칭, via formation, 도금, 표면 마무리, component attachment, 테스트, and final finishing.
What are the key design guidelines for Alumina PCBs?
Designing with Alumina PCBs requires attention to thermal management, dielectric properties, mechanical stability, 표면 마무리, trace width and spacing, component placement, thermal expansion, grounding, shielding, 테스트, and validation.
How much do Alumina PCBs cost?
The cost of Alumina PCBs varies depending on factors such as board size, layer count, material thickness, copper thickness, 표면 마무리, complexity of circuit design, 양, lead time, quality standards, 및 공급 업체. It’s best to obtain quotes from PCB manufacturers based on specific requirements.
Which companies manufacture Alumina PCBs?
Some well-known companies that manufacture Alumina PCBs include CeramTec, Kyocera, CoorsTek, and various PCB manufacturers with expertise in ceramic substrates.
What are the benefits of using Alumina PCBs over traditional PCB materials?
Alumina PCBs offer superior thermal conductivity, 기계적 강도, and electrical insulation compared to traditional PCB materials like FR4. They are particularly suitable for high-power and high-frequency applications where heat dissipation is critical.