Thin Substrate Manufacturer
Thin Substrate Manufacturer,Thin substrates, vital in advanced technology, are ultra-thin material layers crucial for electronics, photonics, and material science applications. Ranging from mere micrometers to nanometers in thickness, they enable the creation of lightweight, compact devices with enhanced performance. Used in semiconductor manufacturing, optical components, and flexible electronics, these substrates offer advantages like improved thermal management and integration density. Their fabrication involves precise processes like thin film deposition and patterning, ensuring uniformity and quality. With diverse applications spanning from integrated circuits to biomedical devices, thin substrates are fundamental in driving innovation and technological progress.
What is a Thin Substrate?
A thin substrate is a material layer that serves as a foundational surface upon which various processes are performed, typically in the fields of electronics, photonics, and materials science. These substrates are characterized by their extremely low thickness, often in the range of a few micrometers (µm) or even nanometers (nm).
In electronics, thin substrates are crucial for the fabrication of devices such as microchips, センサー, and flexible electronics. The thinness of these substrates enables the creation of lightweight, compact, and highly integrated circuits. 例えば, in semiconductor manufacturing, silicon wafers are thinned to enhance heat dissipation and improve the performance of integrated circuits. Thin substrates also play a vital role in the production of flexible electronic devices, which can be bent or folded without damaging the circuit integrity.
In photonics, thin substrates are used to produce optical components like waveguides, lasers, and photodetectors. Their reduced thickness allows for better control over optical properties and integration into compact photonic circuits.
Material science applications of thin substrates include the development of advanced coatings, thin films, and layered composites. These substrates provide a platform for the deposition of various materials to achieve specific mechanical, 熱の, or chemical properties. For instance, in the development of photovoltaic cells, thin substrates are used to create high-efficiency solar panels with reduced material costs.
The production of thin substrates often involves advanced techniques such as chemical vapor deposition (CVD検出器), 物理蒸着 (PVDディスプレイ), and molecular beam epitaxy (MBE). These processes allow for precise control over thickness and uniformity, which are critical for ensuring the performance and reliability of the final products.
まとめ, thin substrates are foundational layers used across multiple high-tech industries to enable the production of advanced electronic, photonic, and material devices, characterized by their minimal thickness and critical role in device miniaturization and performance enhancement.
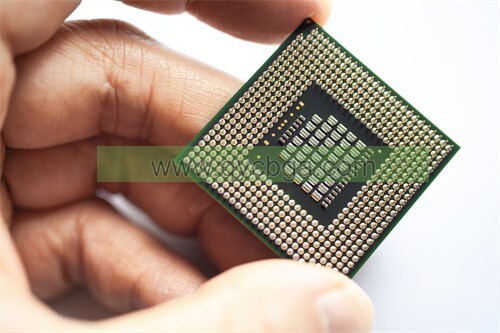
Thin Substrate Manufacturer
What are the Thin Substrate Design Guidelines?
Designing with thin substrates 最適なパフォーマンスと信頼性を確保するためには、さまざまな要素を慎重に検討する必要があります. Here are some general guidelines:
- 材料の選択: Choose a substrate material that meets the specific requirements of your application, such as mechanical strength, 熱伝導率, and electrical properties. Common materials include silicon, グラス, polymers, and specialized engineered substrates like silicon-on-insulator (SOI) or flexible substrates like polyimide.
- Thickness Optimization: Determine the appropriate thickness of the substrate based on the needs of your device or component. Thinner substrates offer advantages such as improved thermal management, 軽量化, and increased flexibility, but they may also pose challenges related to mechanical stability and handling.
- Surface Quality: Ensure that the surface of the thin substrate is free from defects, 汚染 物質, and roughness that could affect subsequent processing steps or device performance. Surface treatments such as cleaning, polishing, and planarization may be necessary to achieve the desired surface quality.
- Uniformity Control: Maintain uniform thickness and material properties across the entire substrate area to minimize variations in device performance. Use precise fabrication techniques such as deposition, エッチング, and lithography to control substrate uniformity and achieve tight tolerances.
- Structural Support: Provide adequate structural support for the thin substrate to prevent bending, warping, or cracking during handling, 加工, と操作. Use reinforcement techniques such as bonding to thicker support layers, adding mechanical structures, or integrating rigid frames to enhance substrate stability.
- サーマルマネジメント:Implement effective thermal management strategies to dissipate heat generated during device operation, especially in high-power or high-density applications. Consider incorporating thermal interface materials, ヒートシンク, or microfluidic channels to enhance heat transfer and prevent thermal damage to the substrate and surrounding components.
- Electrical Isolation: Ensure electrical isolation between different regions or layers of the thin substrate to prevent unwanted leakage currents, クロストーク, or signal interference. Use insulating materials, isolation structures, or appropriate dielectric layers to achieve electrical isolation while maintaining device functionality.
- Flexibility and Bendability: If designing flexible or bendable devices, select substrates with suitable mechanical properties and design features to accommodate bending without compromising performance or reliability. Consider factors such as bending radius, fatigue resistance, and adhesion between layers to ensure long-term durability and flexibility.
- Integration with Other Components: Plan for seamless integration of the thin substrate with other components, such as semiconductor devices, センサー, or packaging materials. Design compatible interfaces, alignment features, and bonding techniques to facilitate assembly and ensure compatibility with existing systems or fabrication processes.
- Reliability Testing: Conduct comprehensive reliability testing and characterization of thin substrate-based devices under relevant operating conditions, including mechanical stress, サーマルサイクル, humidity exposure, and electrical performance. Identify potential failure modes and design robust mitigation strategies to enhance device reliability and longevity.
これらのガイドラインに従う, designers can effectively harness the benefits of thin substrates while addressing the challenges associated with their utilization in advanced electronic, photonic, and material devices.
What is the Thin Substrate Fabrication Process?
の製造プロセス thin substrates involves several steps aimed at achieving the desired thickness, surface quality, と材料特性. Here’s a generalized overview of the fabrication process:
- 基板選択:Choose a suitable base material based on the requirements of the application. 一般的な基板材料にはシリコンが含まれます, グラス, polymers, and engineered substrates like silicon-on-insulator (SOI) or flexible materials such as polyimide.
- Cleaning and Preparation: Clean the substrate surface thoroughly to remove contaminants, residues, and particles that could affect subsequent processing steps. Use cleaning techniques such as solvent rinsing, プラズマ処理, or chemical etching to ensure a pristine substrate surface.
- Thickness Reduction: Employ techniques such as mechanical grinding, chemical mechanical polishing (CMP), or etching to reduce the thickness of the substrate to the desired level. These processes selectively remove material from the substrate surface while maintaining control over thickness uniformity and surface quality.
- Thin Film Deposition: Apply thin film layers onto the substrate surface to modify its properties or enable specific functionalities. Common deposition techniques include chemical vapor deposition (CVD検出器), 物理蒸着 (PVDディスプレイ), atomic layer deposition (ALDの), and spin coating. Thin films can be used for purposes such as passivation, insulation, メタライゼーション, or optical coatings.
- Pattern Definition: Define the desired patterns, 顔立ち, or structures on the thin substrate using lithography techniques. This involves coating the substrate with a photosensitive resist, exposing it to patterned light or electron beam, and developing the resist to transfer the pattern onto the substrate surface. 写真石版, electron beam lithography (EBL), and nanoimprint lithography are commonly used lithography methods.
- Etching and Patterning: Use etching processes such as wet chemical etching, dry etching (例えば。, プラズマエッチング), or laser ablation to selectively remove material from the substrate according to the defined patterns. Etching can be used to create features such as trenches, ビア, channels, or microstructures on the substrate surface.
- Surface Modification and Treatment: Apply surface treatments or modifications to enhance the functionality, パフォーマンス, or compatibility of the thin substrate. Treatments may include surface passivation, functionalization, oxidation, doping, or bonding with additional layers or materials.
- Quality Control and Characterization: Perform rigorous quality control and characterization of the fabricated thin substrates to ensure they meet the specified requirements and standards. Characterization techniques such as microscopy, spectroscopy, profilometry, and electrical testing are used to assess parameters such as thickness, roughness, morphology, composition, and electrical properties.
- Packaging and Integration: Package the fabricated thin substrates into final devices or components, integrating them with other elements such as semiconductor devices, センサー, or optical components. Packaging techniques may include bonding, カプセル化, コーティング, or mounting onto support structures or carriers.
- Testing and Validation: Conduct testing and validation of the fabricated thin substrate-based devices under real-world conditions to assess their performance, 確実, と機能性. Test methods may include electrical testing, サーマルサイクル, mechanical stress testing, environmental testing, and functional testing.
By following these fabrication steps and incorporating appropriate process controls and quality assurance measures, manufacturers can produce high-quality thin substrates tailored to specific applications in electronics, photonics, materials science, and beyond.
How do you manufacture a Thin Substrate?
Manufacturing a thin substrate involves a series of specialized processes tailored to achieve the desired thickness, surface quality, と材料特性. Here’s a step-by-step overview of the typical manufacturing process:
- 基板選択:Choose a suitable base material based on the requirements of the application. This could be silicon, グラス, polymers, or specialized engineered substrates like silicon-on-insulator (SOI) for electronics applications, or flexible substrates like polyimide for flexible electronics or wearable devices.
- Cleaning and Preparation: Clean the substrate surface thoroughly to remove contaminants, residues, and particles that could affect subsequent processing steps. Common cleaning techniques include solvent rinsing, ultrasonic cleaning, and plasma treatment.
- Thickness Reduction: Employ techniques to reduce the thickness of the substrate to the desired level. This can be achieved through mechanical methods such as grinding, lapping, or polishing, as well as chemical methods like etching or chemical mechanical polishing (CMP). The choice of method depends on factors such as material properties, desired thickness, and surface finish requirements.
- Surface Smoothing and Planarization: After thinning the substrate, additional steps may be necessary to smooth the surface and achieve a high degree of planarity. Techniques such as chemical mechanical polishing (CMP) or surface planarization using chemical treatments or mechanical abrasion may be employed to achieve the desired surface finish.
- Thin Film Deposition: Apply thin film layers onto the substrate surface to modify its properties or enable specific functionalities. Thin films can be deposited using techniques such as physical vapor deposition (PVDディスプレイ), 化学蒸着 (CVD検出器), atomic layer deposition (ALDの), またはスピンコーティング. These films may serve purposes such as passivation, insulation, メタライゼーション, or optical coatings.
- Lithography and Patterning: Define the desired patterns, 顔立ち, or structures on the thin substrate using lithography techniques. This involves depositing a photosensitive resist onto the substrate, exposing it to patterned light or electron beam, and developing the resist to transfer the pattern onto the substrate surface. Lithography methods may include photolithography, electron beam lithography (EBL), or nanoimprint lithography.
- Etching and Patterning: Use etching processes to selectively remove material from the substrate according to the defined patterns. Wet chemical etching, dry etching (such as plasma etching), or laser ablation may be employed to create features such as trenches, ビア, channels, or microstructures on the substrate surface.
- Surface Modification and Treatment: Apply surface treatments or modifications to enhance the functionality, パフォーマンス, or compatibility of the thin substrate. This may include surface passivation, functionalization, oxidation, doping, or bonding with additional layers or materials.
- Quality Control and Characterization: Conduct rigorous quality control and characterization of the fabricated thin substrates to ensure they meet the specified requirements and standards. This involves assessing parameters such as thickness, roughness, morphology, composition, and electrical properties using techniques such as microscopy, spectroscopy, profilometry, and electrical testing.
- Packaging and Integration:Package the fabricated thin substrates into final devices or components, integrating them with other elements such as semiconductor devices, センサー, or optical components. Packaging techniques may include bonding, カプセル化, コーティング, or mounting onto support structures or carriers.
- Testing and Validation: Perform testing and validation of the fabricated thin substrate-based devices under real-world conditions to assess their performance, 確実, と機能性. これには、電気テストが含まれる場合があります, サーマルサイクル, mechanical stress testing, environmental testing, and functional testing.
By following these manufacturing steps and employing appropriate process controls and quality assurance measures, manufacturers can produce high-quality thin substrates tailored to specific applications in electronics, photonics, materials science, and other fields.
How much should a Thin Substrate cost?
The cost of a thin substrate can vary widely depending on several factors, including the material used, the manufacturing process complexity, the desired thickness and size, surface quality requirements, そして生産量. Here are some key considerations that influence the cost:
- Material Cost: The choice of substrate material significantly impacts the overall cost. Common materials like silicon, グラス, and polymers have different cost profiles, with engineered substrates or specialty materials potentially commanding higher prices.
- 製造プロセス: The complexity and precision of the manufacturing process contribute to the cost. Processes involving advanced lithography, 薄膜蒸着, and precise etching techniques may require specialized equipment and skilled labor, 生産コストの上昇につながる.
- Thickness and Size:Thinner substrates typically require more precise and time-consuming manufacturing processes, which can increase costs. かつ, larger substrate sizes may require specialized equipment or handling procedures, adding to the overall cost.
- Surface Quality: Achieving high-quality surface finishes and uniformity may necessitate additional processing steps or tighter process controls, which can increase production costs.
- 生産量: Economies of scale play a significant role in determining the cost of thin substrates. Higher volumes of production can spread fixed costs across a larger number of units, その結果、ユニットあたりのコストが削減されます. 逆に言えば, low-volume or custom production runs may incur higher costs due to setup expenses and lower production efficiencies.
- Additional Features and Functionalities: Incorporating additional features such as patterned structures, integrated components, or specialized coatings can increase the cost of thin substrates.
- Quality Assurance and Testing: Ensuring quality control and conducting rigorous testing to meet specific requirements may add to the overall cost of production.
As a rough estimate, the cost of a thin substrate can range from a few dollars to several hundred dollars per square inch, with specialized substrates or custom requirements potentially commanding higher prices. 正確な価格設定のために, it’s essential to consult with manufacturers or suppliers who can provide quotes based on your specific needs and specifications. かつ, factors such as lead time, 包装, and shipping costs should also be considered when determining the total cost of thin substrates.
What is Thin Substrate base material?
The choice of base material for thin substrates depends on the requirements of the application and the desired properties of the final device or component. Common materials used as thin substrate base materials include:
- 珪素: Silicon is widely used in semiconductor manufacturing due to its excellent electrical properties, 機械的強度, 微細加工プロセスとの互換性. Silicon substrates are commonly employed in the production of integrated circuits, MEMSデバイス, センサー, and photonic components.
- グラス: Glass substrates offer advantages such as optical transparency, 化学的不活性, と熱安定性, making them suitable for applications in optics, displays, and microfluidics. Borosilicate glass, soda-lime glass, and quartz are commonly used as thin substrate materials in various industries.
- Polymers: Polymeric substrates provide flexibility, lightweight, そして低コスト, making them ideal for applications in flexible electronics, wearable devices, and biomedical implants. Common polymer substrates include polyimide, ポリエステル (ペット), polyethylene terephthalate (ペット), and cyclic olefin copolymer (COC).
- Engineered Substrates: Engineered substrates such as silicon-on-insulator (SOI), silicon-on-sapphire (SOS), and gallium nitride on silicon carbide (GaN-on-SiC) offer tailored properties and performance enhancements for specific applications. These substrates are often used in advanced semiconductor devices, RF and power electronics, and high-power photonics.
- Metals: Certain metals, such as stainless steel, アルミニウム, and titanium, can also serve as thin substrate base materials for applications requiring high mechanical strength, conductivity, or corrosion resistance. Metal foils and thin sheets are commonly used in flexible electronics, 包装, and structural components.
- 陶芸: セラミック基板は優れた熱伝導率を提供します, 耐薬品性, そして機械安定性, making them suitable for high-temperature applications, electronic packaging, and MEMS devices. Common ceramic materials include alumina (Al2O3), 窒化ケイ素 (シ3N4), および窒化アルミニウム (AlNの).
The selection of a base material depends on factors such as electrical properties, 熱伝導率, optical transparency, 機械的強度, chemical compatibility, とコストに関する考慮事項. かつ, substrate properties such as surface roughness, flatness, and dimensional stability are critical for achieving high-quality thin substrates in manufacturing processes.
Which company makes Thin Substrates?
Many companies manufacture thin substrates, focusing on different application areas and types of materials. In the semiconductor industry, some well-known thin substrate manufacturers include TSMC, インテル, サムスン, GLOBALFOUNDRIES, which produce silicon-based substrates for integrated circuit manufacturing. In the optics field, companies like Corning and Asahi Glass produce glass-based substrates for displays, optical fibers, and optical devices. In the flexible electronics and MEMS (Microelectromechanical Systems) fields, companies like 3M, Polyera, and Apple also produce thin substrates with specific materials.
Our company also manufactures thin substrates. We have advanced production equipment and technology, specializing in the design and manufacturing of customized thin substrates. Our engineering team has rich experience and expertise, capable of customizing thin substrates of different materials, 厚さ, and sizes according to customer requirements. The thin substrates we provide can be applied in various fields, including integrated circuits, optoelectronics, センサー, flexible electronics, biomedical, and nanotechnology.
We prioritize quality control and customer satisfaction. Our production process strictly follows international standards and is ISO certified for quality management systems. We offer flexible production solutions and customized solutions to meet the needs of different application scenarios. Whether it’s small batch production or large-scale mass production, we can provide high-quality, reliable thin substrate products at competitive prices and ensure timely delivery.
Through collaboration with us, customers can obtain high-quality thin substrate products to realize the success of their innovative projects and applications. We are committed to establishing long-term partnerships with customers, driving technological advancement, and achieving business success together.
は何ですか 7 優れたカスタマーサービスの品質?
Good customer service is essential for building positive relationships with customers and ensuring their satisfaction. Here are seven qualities that characterize good customer service:
- 応答: Good customer service involves being prompt and responsive to customer inquiries, requests, and concerns. Customers appreciate timely assistance and expect quick resolutions to their issues. Responding promptly shows that you value their time and prioritize their needs.
- 共感: 共感とは、他人の気持ちを理解し、共有する能力です, including customers. Good customer service representatives empathize with customers’ frustrations, 懸念, and emotions, demonstrating genuine care and concern for their well-being. Empathetic communication helps build trust and rapport with customers.
- コミュニケーションスキル: Effective communication is crucial for providing good customer service. クリア, コンサイス, and courteous communication helps ensure that customers understand the information provided and feel heard and valued. Good communication skills involve active listening, asking relevant questions, and providing accurate and helpful responses.
- Problem-Solving Abilities: Good customer service representatives possess strong problem-solving skills and can effectively address customers’ issues and concerns. They identify root causes, propose viable solutions, and take proactive steps to resolve problems in a timely manner. Problem-solving abilities help minimize customer frustration and build confidence in the company’s ability to deliver solutions.
- 製品知識: A good understanding of the company’s products or services is essential for providing effective customer service. カスタマーサービス担当者は、製品の機能について知識を持っている必要があります, 仕様, usage guidelines, and troubleshooting procedures. Being well-informed allows them to answer customer questions accurately and provide relevant assistance.
- プロ 意識: Good customer service is characterized by professionalism in interactions with customers. This includes maintaining a positive attitude, remaining calm and composed, 会社の方針と基準を順守します. Professionalism instills confidence in customers and reflects positively on the company’s reputation.
- Follow-Up and Feedback: Good customer service involves following up with customers to ensure that their needs have been met and their issues resolved satisfactorily. Following up demonstrates a commitment to customer satisfaction and provides an opportunity to gather feedback for continuous improvement. Seeking feedback also allows companies to identify areas for improvement and make necessary adjustments to enhance the customer experience.
これらの資質を具現化することで、, 企業は、ロイヤルティを育む優れたカスタマーサービスを提供できます, generates positive word-of-mouth, and contributes to long-term success.
よくあるご質問(FAQ) (Frequently Asked Questions)
What are the advantages of using thin substrates?
Thin substrates offer advantages such as reduced weight, enhanced flexibility, 熱管理の改善, and increased integration density. They enable the production of lightweight, compact, and high-performance devices for a wide range of applications.
What materials are used to make thin substrates?
Thin substrates can be made from a variety of materials, including silicon, グラス, polymers, engineered substrates like silicon-on-insulator (SOI), and specialized materials tailored to specific applications.
How are thin substrates manufactured?
The manufacturing process for thin substrates involves steps such as substrate selection, 清掃, thickness reduction (例えば。, grinding, polishing, エッチング), 薄膜蒸着, パターニング, surface modification, quality control, とパッケージング.
What are the applications of thin substrates?
Thin substrates find applications in diverse fields, including integrated circuits, MEMSデバイス, センサー, photonic devices, flexible electronics, biomedical devices, and optical coatings, とりわけ.
What are the challenges associated with thin substrates?
Challenges associated with thin substrates include maintaining uniform thickness and material properties, ensuring mechanical stability, 熱放散の管理, and achieving high-quality surface finishes.
How do I choose the right thin substrate for my application?
Choosing the right thin substrate involves considering factors such as material properties, thickness requirements, mechanical flexibility, 熱伝導率, 電気的特性, and compatibility with fabrication processes and environmental conditions.
Can thin substrates be customized for specific applications?
はい, thin substrates can be customized to meet the unique requirements of specific applications. This includes tailoring material compositions, 厚さ, surface treatments, and dimensional characteristics to optimize performance and functionality.
What quality assurance measures are used for thin substrates?
Quality assurance measures for thin substrates include rigorous testing and characterization to ensure compliance with specifications and standards. This may involve techniques such as microscopy, spectroscopy, profilometry, 電気試験, 信頼性試験.