Multilayer RF PCBs Manufacturer
Multilayer RF PCBs Manufacturer,Multilayer RF PCBs are specialized circuit boards designed for high-frequency applications, featuring multiple layers of conductive material and insulating substrate. They enable the integration of complex RF components while maintaining optimal signal integrity and minimizing electromagnetic interference. These PCBs are crucial in wireless communication systems, radar, satellite communication, and other RF applications, offering advantages such as higher component density, reduced size, パフォーマンスの向上, and enhanced reliability. With meticulous design and manufacturing processes, Multilayer RF PCBs ensure efficient transmission and reception of RF signals in a wide range of electronic devices and systems.
What are Multilayer RF PCBs?
Multilayer RF PCBs, or multilayer radio frequency printed circuit boards, are specialized circuit boards designed to handle high-frequency signals typically used in wireless communication systems, レーダーシステム, satellite communication, and other RF applications. Unlike traditional PCBs, which consist of only one or two layers, multilayer RF PCBs have multiple layers stacked together with alternating layers of conductive material (usually copper) and insulating material (usually epoxy resin with glass fiber reinforcement).
These PCBs are designed with careful consideration of signal integrity, インピーダンス制御, および電磁干渉 (EMIの) management to ensure optimal performance of RF circuits. They often incorporate features such as controlled impedance transmission lines, グランドプレーン, and shielding layers to minimize signal loss, reflections, and crosstalk.
The number of layers in multilayer RF PCBs can vary depending on the complexity of the circuit and the specific requirements of the application. Common configurations range from four to more than ten layers.
Designing multilayer RF PCBs requires specialized expertise in RF engineering, high-frequency electronics, and PCB layout techniques. Advanced simulation and modeling tools are often used to analyze and optimize the performance of these PCBs before fabrication.
全, multilayer RF PCBs play a crucial role in the development of high-performance RF systems by providing a reliable and efficient platform for integrating complex RF circuits while maintaining signal integrity and minimizing interference.
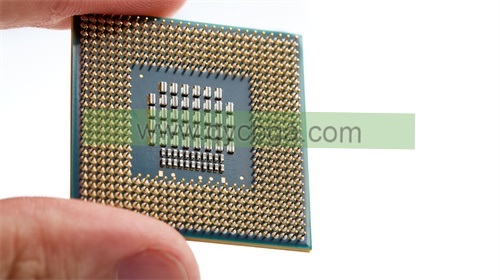
Multilayer RF PCBs Manufacturer
What are Multilayer RF PCB Design Guidelines?
設計 multilayer RF PCBs requires careful consideration of various factors to ensure optimal performance of high-frequency circuits. Here are some key design guidelines:
- レイヤースタックアップ: Choose an appropriate layer stackup with controlled impedance layers for signal traces and dedicated ground planes for RF components. Ground planes should be continuous and uninterrupted to provide low impedance return paths for RF signals and minimize EMI.
- Impedance Control: Maintain consistent trace widths, spacing, and dielectric thickness to control characteristic impedance. Use impedance calculators or simulation tools to determine appropriate dimensions for transmission lines to match the impedance of RF components and minimize signal reflections.
- シグナルインテグリティ: Minimize signal loss, reflections, and crosstalk by maintaining controlled impedance, reducing discontinuities such as vias and bends in transmission lines, and optimizing routing to minimize parallel traces and coupling between traces.
- Grounding: Implement a solid ground plane on each layer of the PCB to provide a low-impedance return path for RF signals and reduce ground loops. Connect all ground planes together with vias to create a solid ground reference across all layers.
- Decoupling Capacitors: Place decoupling capacitors strategically near RF components to provide clean power and minimize noise. Use low-inductance ceramic capacitors with short traces to connect them to power and ground planes.
- RF Components Placement: Carefully place RF components on the PCB to minimize trace lengths, reduce parasitic capacitance and inductance, and optimize signal paths. Place sensitive RF components away from sources of electromagnetic interference (EMIの) such as switching regulators or high-speed digital signals.
- Routing: Route RF traces as short and direct as possible to minimize signal loss and impedance mismatch. Use wide traces for high-current paths and keep traces separated to minimize coupling. Avoid 90-degree bends and use gradual curves instead to reduce signal reflections.
- Isolation and Shielding:Use shielding techniques such as RF enclosures, shielding cans, or RF absorbing materials to isolate sensitive RF circuits from external interference and reduce emissions. Shielding should be grounded to provide effective EMI protection.
- High-Frequency Materials: Select PCB materials with low dielectric loss and low signal attenuation at high frequencies. High-frequency laminates with low loss tangent and stable dielectric constant are preferred for multilayer RF PCBs.
- シミュレーションとテスト: Validate the design through simulation using electromagnetic simulation software to analyze signal integrity, インピーダンス整合, and EMI. Perform prototype testing with RF equipment to verify performance and make adjustments if necessary.
これらのガイドラインに従う, designers can create multilayer RF PCBs that meet the stringent requirements of high-frequency applications while ensuring reliable performance and minimal interference.
What is the Multilayer RF PCB Fabrication Process?
の製造プロセス multilayer RF PCBs involves several steps to create the complex stackup of conductive and insulating layers needed for high-frequency applications. Here’s an overview of the typical fabrication process:
- デザインとレイアウト: The process begins with the design and layout of the PCB using specialized PCB design software. Designers create the multilayer stackup, define the placement of components, and route high-frequency traces while adhering to design guidelines for impedance control, シグナルインテグリティ, and RF performance.
- 材料の選択: Select high-quality PCB materials suitable for RF applications. Common materials include specialized high-frequency laminates with low dielectric loss and stable electrical properties across a range of frequencies. The choice of material depends on factors such as frequency range, signal speed, and thermal requirements.
- レイヤースタックアップ:Based on the design specifications, the PCB manufacturer creates the layer stackup by laminating alternating layers of conductive copper foil and insulating substrate material (prepreg). The stackup typically includes multiple signal layers, グランドプレーン, and power planes interconnected through vias.
- Inner Layer Processing: The inner layers of the PCB stackup undergo several processes, including etching, 錬成, とメッキ. Copper is selectively etched away from the inner layers to create the desired circuit patterns, vias are drilled to establish electrical connections between layers, and copper is plated onto the walls of the vias to ensure conductivity.
- Prepreg and Core Lamination: After processing the inner layers, the prepreg layers (insulating material impregnated with epoxy resin) and core layers (copper-clad laminates) are laminated together under heat and pressure to form a solid multilayer PCB panel.
- 錬成: Holes are drilled through the entire stackup at specified locations for component mounting and interlayer connections. Advanced drilling techniques such as laser drilling may be used for high-precision vias in RF PCBs.
- Through-Hole Plating: Through-holes and vias are plated with conductive material (通常、銅) to establish electrical connections between layers. Plating ensures low-resistance interconnections and provides mechanical support for component attachment.
- Outer Layer Processing: Outer layer processing involves applying a layer of photoresist to the surface of the PCB panel, exposing it to UV light through a photomask to define the circuit patterns, and etching away the unwanted copper to reveal the final traces and pads.
- 表面仕上げ: The exposed copper surfaces are coated with a surface finish to protect against oxidation, promote solderability, and improve electrical performance. Common surface finishes for RF PCBs include immersion gold (エニグ), イマージョンシルバー, or immersion tin.
- 最終検査と試験: The completed PCB panels undergo rigorous inspection and testing to ensure compliance with design specifications, 寸法精度, 電気的導通, and signal integrity. Advanced testing techniques such as impedance testing and high-frequency testing may be performed to verify RF performance.
- Routing and Separation: After testing, the PCB panels are routed into individual boards and separated from the panel. Any remaining copper is trimmed, and the boards may undergo additional processes such as edge plating or edge beveling for enhanced durability and functionality.
- Final Quality Check and Packaging: The finished PCBs undergo a final quality check to ensure they meet the required specifications. They are then packaged and prepared for shipment to the customer or assembly facility.
次の手順に従います, manufacturers can produce high-quality multilayer RF PCBs with the complex layer stackup and precise circuitry needed for demanding RF applications.
How do you manufacture Multilayer RF PCBs?
Manufacturing multilayer RF PCBs involves a series of specialized processes to create the complex stackup of conductive and insulating layers required for high-frequency applications. ここでは、製造プロセスの概要をご紹介します:
- 材料の準備: The process begins with the preparation of high-quality PCB materials suitable for RF applications. This includes selecting specialized high-frequency laminates with low dielectric loss and stable electrical properties. The laminates are typically composed of layers of fiberglass-reinforced epoxy resin with copper foil bonded to one or both sides.
- レイヤースタックアップ設計: Based on the PCB design specifications, engineers determine the layer stackup configuration, レイヤー数を含む, the arrangement of signal, ground, and power planes, and the thickness of each layer. The layer stackup is designed to meet impedance requirements, minimize signal loss, and provide effective grounding for RF circuits.
- Circuit Design and Layout: PCB designers use specialized software to create the circuit layout, including the placement of components, routing of signal traces, and generation of Gerber files for manufacturing. Careful attention is paid to impedance control, シグナルインテグリティ, and RF performance throughout the design process.
- Inner Layer Processing: The inner layers of the PCB stackup undergo several processing steps. まずは, a layer of copper foil is bonded to each side of the prepreg material. 次に, the copper is etched away using a chemical process to create the desired circuit patterns. Laser drilling or mechanical drilling is then used to create vias for interlayer connections.
- Layer Alignment and Lamination: Once the inner layers are processed, they are aligned and stacked together with prepreg layers and core laminates to form the multilayer PCB stackup. The stackup is then pressed together and heated in a lamination press to bond the layers into a solid panel.
- 穴あけとメッキ: ラミネート後, holes are drilled through the entire stackup at specified locations for component mounting and interlayer connections. The holes are then plated with conductive material (通常、銅) to create vias that establish electrical connections between layers.
- Outer Layer Processing: The outer layers of the PCB panel are coated with a layer of photoresist, which is then exposed to UV light through a photomask to define the circuit patterns. The exposed areas are then etched away to reveal the final traces and pads.
- 表面仕上げ:Once the circuit patterns are defined, the exposed copper surfaces are coated with a surface finish to protect against oxidation and improve solderability. Common surface finishes for RF PCBs include immersion gold (エニグ), イマージョンシルバー, or immersion tin.
- 最終検査と試験: The completed PCB panels undergo rigorous inspection and testing to ensure they meet the required specifications for dimensions, 電気的導通, インピーダンス整合, and signal integrity. Advanced testing techniques such as impedance testing and high-frequency testing may be performed to verify RF performance.
- Routing and Separation: After testing, the PCB panels are routed into individual boards and separated from the panel. Any remaining copper is trimmed, and the boards may undergo additional processes such as edge plating or edge beveling for enhanced durability and functionality.
- Final Quality Check and Packaging: The finished PCBs undergo a final quality check to ensure they meet the required specifications. They are then packaged and prepared for shipment to the customer or assembly facility.
By following these manufacturing processes, companies can produce high-quality multilayer RF PCBs with the complex layer stackup and precise circuitry needed for demanding RF applications.
How much should Multilayer RF PCBs cost?
The cost of multilayer RF PCBs can vary significantly depending on several factors including the complexity of the design, レイヤーの数, the quality of materials used, 関連する製造プロセス, and the quantity ordered. ここでは、コストに影響を与える主な要因をいくつか紹介します:
- レイヤー数: Multilayer RF PCBs typically have more layers compared to standard PCBs to accommodate the complex circuitry required for high-frequency applications. The cost generally increases with the number of layers due to the additional materials and manufacturing processes involved.
- 材料の選択: The choice of PCB materials, particularly high-frequency laminates with low dielectric loss and stable electrical properties, コストに大きな影響を与える可能性があります. Specialized materials designed for RF applications tend to be more expensive than standard FR-4 materials.
- 設計の複雑さ: Complex designs with high component density, 厳しい公差, and intricate routing patterns may require more time and resources to manufacture, コストの上昇につながる. Designs that require impedance-controlled traces, 埋もれたビア, or blind vias can also contribute to increased manufacturing costs.
- 製造プロセス: Certain manufacturing processes such as laser drilling for high-precision vias, controlled impedance testing, and high-frequency testing may incur additional costs. Advanced surface finishes such as immersion gold (エニグ) or selective gold plating can also add to the overall cost.
- 量: Economies of scale often apply in PCB manufacturing, meaning that larger production quantities typically result in lower unit costs. Ordering larger volumes of multilayer RF PCBs can help reduce the per-unit cost.
- リード タイム: Expedited production or quick-turn services may come with additional charges. Longer lead times generally allow for more efficient production scheduling and may result in lower costs.
- サプライヤーとロケーション: PCB fabrication costs can vary between different manufacturers and regions. Offshore manufacturers may offer lower labor costs but may have longer lead times and potential quality concerns.
- 追加サービス: Additional services such as assembly, テスティング, and quality assurance may be available from PCB manufacturers for an extra cost.
これらの要因を考えると, it’s challenging to provide a specific cost without knowing the detailed requirements of the project. It’s advisable to consult with multiple PCB manufacturers, provide them with your design specifications, and request detailed quotations to get an accurate estimate of the cost for your multilayer RF PCBs.
What is Multilayer RF PCB base material?
The choice of base material for multilayer RF PCBs is critical to ensuring optimal performance in high-frequency applications. Here are some commonly used materials for multilayer RF PCBs:
- PTFE-Based Materials (ポリテトラフルオロ エチレン): PTFE-based materials, such as Rogers RO4000 series, Taconic TLY series, and Arlon AD series, are widely used in multilayer RF PCBs due to their low dielectric constant (εr) and low loss tangent (tan δ), which provide excellent electrical properties at high frequencies. These materials offer stable electrical performance over a wide range of frequencies and temperatures, making them ideal for RF and microwave applications.
- Hybrid PTFE/FR-4 Materials: Some PCB laminates combine PTFE with FR-4 (epoxy-glass) materials to achieve a balance between performance and cost. These hybrid materials offer improved electrical properties compared to standard FR-4 laminates but are more affordable than pure PTFE-based materials. Examples include Isola’s IS680, Nelco’s N7000, and Panasonic’s Megtron series.
- Ceramic-Based Materials: Ceramic-filled laminates, such as DuPont’s GreenTape™ low temperature co-fired ceramic (LTCC) 料, offer excellent high-frequency performance and thermal stability. These materials are often used in multilayer RF PCBs for their low loss, 高い熱伝導率, and compatibility with thick-film and thin-film processing techniques.
- 液晶ポリマー (LCPの):LCP-based materials, such as Rogers RT/duroid® LCP series, offer low dielectric loss, 低吸湿性, and excellent dimensional stability, making them suitable for high-frequency and high-speed applications. LCP materials are typically used in multilayer RF PCBs where flexibility, 小型化, and high performance are required.
- Aramid-Based Materials: Aramid fiber-reinforced laminates, such as Panasonic’s Megtron 6, offer high mechanical strength, 熱安定性, and excellent electrical properties for multilayer RF PCBs. These materials are often used in high-reliability applications where durability and performance are critical.
The choice of base material depends on factors such as frequency range, signal speed, 熱要件, コスト制約, and specific application needs. Designers typically select materials with the lowest dielectric loss and stable electrical properties to minimize signal loss, impedance variations, and distortion in RF circuits. かつ, manufacturers may provide datasheets and technical specifications for their materials to help designers evaluate their suitability for multilayer RF PCBs.
Which company manufactures Multilayer RF PCBs?
Several companies manufacture Multilayer RF (無線周波数) プリント基板, including Rogers Corporation, Taconic Advanced Dielectric Division, Arlon Electronic Materials, and Isola Group, とりわけ. These companies offer various specialized substrate materials for high-frequency applications and possess advanced manufacturing technologies and expertise to meet the stringent requirements of RF circuits.
As for our company, we also specialize in the production of Multilayer RF PCBs. We have advanced manufacturing equipment and a skilled technical team dedicated to the design and fabrication of high-frequency circuit boards. Here are the services and capabilities we offer:
- Professional Design Team: We have an experienced design team familiar with the principles of high-frequency circuit design and technical specifications. They can design complex multilayer RF PCBs according to customer requirements, ensuring optimized circuit performance.
- Advanced Manufacturing Equipment: Equipped with advanced PCB manufacturing equipment, including precision chemical etching machines, laser drilling machines, and lamination presses, we can precisely control the manufacturing process of circuit patterns, ensuring high-quality PCBs.
- 厳格な品質管理: We implement a rigorous quality control system, with strict inspections and monitoring at every stage from raw material procurement to production. We ensure that each Multilayer RF PCB meets customer specifications and requirements.
- Flexible Production Capacity: With flexible production capacity, we can meet customer demands for different quantities and delivery times. Whether it’s small batch customization or large-scale production, we can deliver high-quality Multilayer RF PCBs on time.
- Excellent Customer Service: We value communication and collaboration with our customers, providing comprehensive technical support and after-sales service. Our team is ready to answer customer questions, address their concerns, and ensure their satisfaction with our products and services.
まとめ, our company has the professional knowledge, technical capabilities, and production resources required for designing and manufacturing Multilayer RF PCBs. Whether in telecommunications, 航宇, 軍, or industrial sectors, we can provide high-quality Multilayer RF PCBs to meet various customer needs and applications.
は何ですか 7 優れたカスタマーサービスの品質?
Good customer service is essential for building strong relationships with customers and fostering loyalty. Here are seven qualities that characterize excellent customer service:
- 応答:Responding promptly to customer inquiries, 懸念, and requests is crucial. Whether it’s through phone, 電子メール, live chat, or social media, being accessible and addressing customer needs in a timely manner demonstrates commitment to their satisfaction.
- 共感: Showing empathy and understanding towards customers’ issues and emotions builds rapport and trust. Listening actively, acknowledging their concerns, and expressing genuine concern for their well-being can turn a negative experience into a positive one.
- Clarity: Providing clear and concise information to customers helps them understand products, services, policies, and processes better. Avoiding jargon and using simple language ensures that customers feel informed and empowered to make decisions.
- プロ 意識: Maintaining professionalism in all interactions with customers conveys competence, credibility, and trustworthiness. This includes being polite, 恭しい, and courteous, 困難な状況でも.
- 柔軟性: Being flexible and adaptable to accommodate customer needs and preferences demonstrates a willingness to go above and beyond. Offering personalized solutions, accommodating special requests, and being open to feedback contribute to a positive customer experience.
- Problem-solving skills: Effectively resolving customer issues and complaints requires strong problem-solving skills. Empowering frontline staff with the authority and resources to address problems promptly and effectively can prevent escalations and enhance customer satisfaction.
- Consistency:Providing consistent service across all touchpoints and interactions ensures a cohesive and reliable customer experience. Consistency in communication, quality of service, and adherence to commitments fosters trust and loyalty among customers.
これらの資質を具現化することで、, businesses can deliver exceptional customer service that not only meets but exceeds customer expectations, leading to increased customer satisfaction, 忠義, and advocacy.
よくあるご質問(FAQ)
What are Multilayer RF PCBs?
Multilayer RF PCBs are specialized printed circuit boards designed for high-frequency applications, such as wireless communication systems, radar, and satellite communication. They consist of multiple layers of conductive material and insulating substrate, with intricate designs to handle RF signals efficiently.
What is the significance of Multilayer RF PCBs?
Multilayer RF PCBs play a crucial role in high-frequency circuits by providing optimal signal integrity, インピーダンス制御, および電磁干渉 (EMIの) management. They enable the integration of complex RF components while minimizing signal loss and interference.
What materials are used in Multilayer RF PCBs?
Multilayer RF PCBs often use specialized high-frequency materials such as PTFE-based laminates, hybrid PTFE/FR-4 materials, ceramic-based materials, 液晶ポリマー (LCPの), and aramid-based materials. These materials offer low dielectric loss, stable electrical properties, and excellent performance at high frequencies.
What are the design considerations for Multilayer RF PCBs?
Designing Multilayer RF PCBs requires careful consideration of factors such as controlled impedance, 信号ルーティング, grounding, isolation, and shielding. Designers must optimize trace geometry, minimize signal reflections, and ensure proper grounding and shielding to maintain RF performance.
How are Multilayer RF PCBs manufactured?
The manufacturing process for Multilayer RF PCBs involves several steps, including layer stackup design, 材料の準備, inner layer processing, 積層, 錬成, 鍍金, outer layer processing, 表面仕上げ, 検査, とテスト. Specialized equipment and techniques are used to ensure high-quality PCBs.
What are the advantages of Multilayer RF PCBs?
Multilayer RF PCBs offer several advantages, including higher component density, 小型・軽量化, シグナルインテグリティの向上, lower electromagnetic interference (EMIの), and enhanced performance at high frequencies. They enable the development of compact and efficient RF systems.
What applications are Multilayer RF PCBs used in?
Multilayer RF PCBs are used in various applications, 電気通信を含む, 航宇, 防御, 自動車, 医療機器, and industrial electronics. They are essential components in RF transceivers, アンテナ, amplifiers, フィルター, and other high-frequency systems.