多層FC-BGA基板メーカー
多層FC-BGA基板メーカー,Multilayer FC-BGA (フリップチップボールグリッドアレイ) Substrates are sophisticated circuit boards designed to support flip chip packages with multiple layers of interconnected circuitry. These substrates feature a complex stack of layers that facilitate high-density routing and effective signal distribution. With fine-pitch solder balls connecting the flip chip to the substrate, they enable efficient high-speed data transmission and reliable electrical connections. Multilayer FC-BGA substrates are used in advanced electronic devices such as processors, memory modules, and high-performance computing systems. Their intricate design supports increased functionality and performance while optimizing space and improving thermal management.
What is a Multilayer FC-BGA Substrate?
A Multilayer FC-BGA (フリップチップボールグリッドアレイ) substrate is a sophisticated component used in advanced electronic packaging. It plays a crucial role in connecting flip chip integrated circuits (ICの) to a printed circuit board (プリント基板) or a system’s motherboard.
The FC-BGA substrate features multiple layers, which are essential for managing the complex routing and interconnections required by high-performance ICs. The “multilayer” aspect refers to the multiple layers of conductive and insulating materials that make up the substrate. These layers are intricately designed to support a high-density array of solder balls, which form the electrical connection points between the flip chip and the PCB.
In a Flip Chip configuration, the IC is flipped upside down, and its connections are directly attached to the substrate. This arrangement allows for shorter interconnects and better electrical performance compared to traditional wire-bonded packages. The FC-BGA substrate ensures efficient heat dissipation and signal integrity, which are critical for high-speed and high-density applications.
The design of a Multilayer FC-BGA substrate involves careful consideration of factors such as layer thickness, material properties, and the arrangement of interconnecting vias. Advanced manufacturing techniques are used to achieve the precise alignment and reliability needed for modern electronic devices, プロセッサを含む, メモリチップ, and other high-performance components.
全, the Multilayer FC-BGA substrate is essential for meeting the demanding requirements of contemporary electronics, offering a balance of performance, 確実, と小型化.
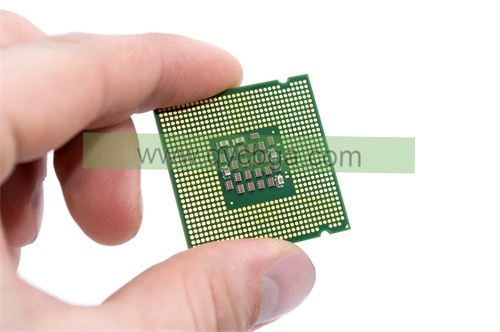
Molded Interconnect Substrate Manufacturer
は何ですか Multilayer FC-BGA Substrate デザインガイドライン?
デザイン Multilayer FC-BGA (フリップチップボールグリッドアレイ) substrate involves several critical guidelines to ensure high performance and reliability in advanced electronic packaging. Here are the key design guidelines:
- Layer Stack-up Design: Proper layer stack-up is essential for achieving the desired electrical performance. The substrate typically includes signal layers, power and ground planes, and dielectric layers. Careful design of these layers helps in managing impedance, minimizing crosstalk, and ensuring signal integrity.
- Signal Routing:High-speed signal routing requires careful planning to avoid interference and signal degradation. Use controlled impedance traces and minimize trace lengths. Differential pairs should be routed with consistent spacing and grounding to reduce electromagnetic interference (EMIの) and ensure signal integrity.
- サーマルマネジメント: Effective heat dissipation is crucial for high-performance ICs. Design the substrate with adequate thermal vias and heat spreaders to manage heat generated by the flip chip. Proper thermal design helps in maintaining component reliability and performance.
- ボールグリッドアレイ (BGAの) Layout: The placement and spacing of solder balls on the substrate are critical for reliable connections and manufacturability. Ensure that the ball grid array is aligned with the flip chip’s pads and that the solder balls are evenly spaced to avoid soldering issues.
- Via Design: Use blind and buried vias appropriately to minimize signal degradation and maintain high signal integrity. Ensure that vias are properly sized and spaced to handle current requirements and reduce inductance.
- 材料の選択: Choose materials with suitable electrical, 熱の, および機械的特性. High-frequency applications may require low-loss materials, while high-current applications need materials with good thermal conductivity.
- 製造公差: Adhere to stringent manufacturing tolerances for layer alignment, ビア配置, and pad dimensions. Precision in these aspects ensures the reliability of the substrate and the functionality of the final electronic device.
- テストと信頼性: Incorporate design features that facilitate testing and inspection of the substrate. Consider stress testing and reliability analysis to ensure that the substrate meets the required performance and durability standards.
By following these design guidelines, you can optimize the performance, 確実, and manufacturability of Multilayer FC-BGA substrates, ensuring they meet the demanding requirements of modern electronic systems.
は何ですか Multilayer FC-BGA Substrate 製作プロセス?
The fabrication process of a Multilayer FC-BGA (フリップチップボールグリッドアレイ) substrate involves several complex steps to ensure the substrate meets high-performance and reliability standards. Here’s an overview of the typical fabrication process:
- デザインとレイアウト: The process begins with detailed design and layout of the substrate. Engineers create a design that includes the number of layers, 信号ルーティング, ビア配置, およびボールグリッド配列 (BGAの) layout. This design is crucial for ensuring that the substrate meets performance, 熱の, and electrical requirements.
- 材料の準備: Raw materials, including copper foils, prepregs (pre-impregnated resin sheets), and core laminates, are prepared. These materials are selected based on their electrical, 熱の, および機械的特性.
- Core Layer Fabrication: The core layers of the substrate are created by laminating copper foil onto a core material, usually a dielectric layer. The core layers are then patterned using photolithography to define the circuitry. This involves coating the core with a photosensitive material, exposing it to UV light through a mask, and developing the pattern.
- ビアフォーメーション: ビア (vertical interconnects between layers) are drilled or laser-machined into the core layers. The vias are then plated with a conductive material, 銅など, to create electrical connections between different layers of the substrate.
- レイヤーラミネート: The individual layers, including the core layers and prepregs, are stacked and laminated together using heat and pressure. This step creates a multilayer substrate with integrated vias and signal routing.
- Blind and Buried Via Processing: If the design requires blind or buried vias (vias that do not go through the entire substrate), these are processed at this stage. Blind vias are drilled and plated up to a certain layer, while buried vias are formed between internal layers.
- Surface Patterning:The outer layers of the substrate are patterned to define the BGA pad layout and other surface features. This involves applying a photoresist layer, exposing it to UV light, and developing the pattern to create the necessary features.
- Solder Mask and Surface Finish: A solder mask layer is applied to protect the circuitry and define the areas where solder will be applied. Surface finishes, such as HASL (熱風はんだレベリング), エニグ (無電解ニッケル浸漬金), or other finishes, are applied to prepare the substrate for soldering.
- BGA Ball Placement: Solder balls are placed onto the defined pads in the BGA layout. This can be done using a variety of methods, such as solder paste printing and ball placement machines.
- 最終試験と検査: The completed substrate undergoes rigorous testing and inspection to ensure it meets the design specifications and quality standards. This includes electrical testing, thermal analysis, and visual inspection.
- 梱包と配送: テストが完了したら, the substrates are packaged and prepared for shipment to customers or assembly facilities.
Each step in the fabrication process is carefully controlled to ensure that the Multilayer FC-BGA substrate performs reliably in high-speed and high-density electronic applications.
How Do You Manufacture a Multilayer FC-BGA Substrate?
Manufacturing a Multilayer FC-BGA (フリップチップボールグリッドアレイ) substrate involves several detailed and precise steps. Here’s an overview of the process:
- 設計と仕様: The process starts with designing the substrate layout, レイヤー数を含む, 信号ルーティング, ビア配置, and BGA pad arrangement. This design is created using advanced CAD software and must meet specific electrical, 熱の, and mechanical requirements.
- 材料の選択: Choose appropriate base materials such as copper foils, prepregs (resin-impregnated fiber sheets), and core laminates. These materials must have suitable electrical, 熱の, and mechanical properties to meet the performance criteria of the FC-BGA substrate.
- Core Layer Production: Begin by preparing the core layers, which are typically made of copper foil laminated onto dielectric material. The core layers are then patterned using photolithography to define the circuitry. This involves coating the core with a photosensitive film, 紫外線にさらす (紫外線) light through a mask, and developing the pattern to reveal the circuitry.
- ビアフォーメーション: Drill or laser-cut vias into the core layers. These vias provide vertical electrical connections between different layers of the substrate. After drilling, the vias are plated with copper to ensure electrical continuity.
- 積層: Stack and laminate the prepared core layers, prepregs, and any additional dielectric layers. This process involves applying heat and pressure to bond the layers together into a cohesive multilayer substrate.
- Blind and Buried Via Processing: For designs requiring blind or buried vias, process these vias at this stage. Blind vias are drilled and plated up to a certain layer, while buried vias are formed within internal layers of the substrate.
- Surface Patterning: Pattern the outer layers to define the BGA pads and other surface features. Apply a photoresist layer, expose it to UV light through a mask, and develop the pattern to create the necessary features.
- ソルダーマスクアプリケーション: Apply a solder mask layer to protect the circuitry and define the areas where solder will be applied. This mask helps in preventing solder bridges and ensuring accurate solder placement.
- 表面仕上げ: Apply surface finishes to the pads to prepare them for soldering. Common finishes include HASL (熱風はんだレベリング), エニグ (無電解ニッケル浸漬金), or other protective coatings that enhance solderability and reliability.
- ボールグリッドアレイ (BGAの) ボールの配置: Place solder balls onto the defined BGA pads. This can be achieved using automated equipment that places solder balls precisely in the designated locations.
- 最終試験と検査:Conduct thorough testing and inspection of the substrate. This includes electrical tests to verify connectivity, thermal analysis to ensure heat dissipation, and visual inspections for defects.
- Packaging and Delivery: Once the substrates pass all tests and inspections, they are packaged carefully to prevent damage during transport and delivered to customers or assembly facilities.
Each step in the manufacturing process requires careful control and precision to ensure that the Multilayer FC-BGA substrate meets high standards of performance and reliability for advanced electronic applications.
How Much Should a Multilayer FC-BGA Substrate Cost?
The cost of a Multilayer FC-BGA (フリップチップボールグリッドアレイ) substrate can vary widely depending on several factors. Here’s an overview of the key elements that influence the pricing:
- Complexity and Design Specifications: The complexity of the substrate design significantly impacts the cost. Factors such as the number of layers, the density of the ball grid array, the type and number of vias, and the precision required for signal routing all contribute to the overall cost. More complex designs with higher performance requirements generally cost more to manufacture.
- 材料費: The choice of materials affects the cost. High-performance materials with better electrical, 熱の, および機械的特性, such as advanced dielectrics or special surface finishes, can increase the cost of the substrate.
- レイヤー数:The number of layers in the substrate influences the cost. Multilayer substrates with more layers require more processing steps and materials, which can drive up the price.
- Volume and Production Scale: The production volume plays a crucial role in determining cost. Higher production volumes often result in lower per-unit costs due to economies of scale. 逆に言えば, low-volume or prototype runs tend to be more expensive per unit.
- Manufacturing Complexity: Advanced fabrication techniques and precision manufacturing required for high-density interconnections and thermal management can increase costs. The use of advanced technologies for via formation, layer alignment, and surface finishing can also impact pricing.
- テストと品質管理: Extensive testing and quality control measures, including electrical and thermal testing, add to the cost. Ensuring the substrate meets all reliability and performance standards requires additional resources and time.
- リード タイム: Shorter lead times may result in higher costs due to expedited processing and manufacturing. Longer lead times often allow for cost optimization through better production planning and scheduling.
- Geographic Location: Manufacturing costs can vary depending on the location of the production facility. Labor costs, overheads, and material availability in different regions can affect the final price.
Ultimately, to obtain an accurate cost estimate, it’s essential to consult with manufacturers and provide detailed design specifications and production requirements. This will help in receiving a precise quote based on your specific needs.
What is the Base Material for a Multilayer FC-BGA Substrate?
The base material for a Multilayer FC-BGA (フリップチップボールグリッドアレイ) substrate is crucial for ensuring the substrate’s performance, 確実, and compatibility with high-density electronic components. The main base materials typically used include:
- 1. Core Laminates: Core laminates are the foundational layers of a Multilayer FC-BGA substrate. They consist of a dielectric material, FR-4など, prepreg (resin-impregnated fiberglass), or high-performance laminates like PTFE (polytetrafluoroethylene) or ceramic-filled composites. The core material provides mechanical support and electrical insulation between conductive layers.
- 銅箔: Copper foils are used as conductive layers in the substrate. They are laminated onto the dielectric material to form the electrical traces and pads. The thickness of the copper foil can vary based on the electrical requirements and the current-carrying capacity needed for the application.
- Prepreg: Prepregs are resin-impregnated fiberglass sheets used to bond the core layers together and provide additional dielectric insulation. They are critical for creating a stable and robust multilayer structure.
- 誘電体材料:High-frequency and high-performance applications may require specialized dielectric materials to meet specific electrical and thermal properties. These can include materials like polyimide or PTFE, which offer low dielectric constants and low loss tangents, ideal for high-speed signal transmission and thermal management.
- ソルダーマスク: A solder mask layer is applied over the surface of the substrate to protect the circuitry and define areas where solder will be applied. It prevents solder bridges and ensures accurate soldering of the BGA balls.
- 表面仕上げ: The surface finish applied to the exposed copper pads is crucial for solderability and reliability. Common finishes include HASL (熱風はんだレベリング), エニグ (無電解ニッケル浸漬金), and other protective coatings that ensure good solder joint formation and long-term durability.
- 接着剤層: Adhesive materials, such as epoxy resins, are used to bond different layers of the substrate together. These adhesives must provide strong adhesion and maintain electrical and thermal performance under various operating conditions.
The selection of these base materials depends on the specific requirements of the FC-BGA substrate, including electrical performance, サーマルマネジメント, 機械的強度, と製造可能性. Each material is chosen to meet the demanding needs of high-density, high-performance electronic applications.
Which Company Makes Multilayer FC-BGA Substrates?
Companies that manufacture Multilayer FC-BGA (フリップチップボールグリッドアレイ) substrates include several leading global electronics manufacturers and PCB producers with advanced technologies and extensive experience to meet the needs of high-performance and high-density applications. Here are some notable manufacturers:
- TSMCの (台湾セミコンダクターマニュファクチャリングカンパニー): As one of the largest semiconductor manufacturers globally, TSMC has strong capabilities in advanced packaging technologies, including Multilayer FC-BGA substrates. Their technology is widely recognized in the industry for delivering high-performance and reliable products.
- NXPセミコンダクターズ: NXP is a well-known semiconductor supplier and also produces Multilayer FC-BGA substrates. Their products are widely used in automotive, communication, and consumer electronics fields.
- Hitachi Chemical: Hitachi Chemical is a leading electronic materials supplier with extensive experience in producing Multilayer FC-BGA substrates. Their products perform excellently in high-frequency and high-speed applications.
- Fujitsu: Fujitsu provides Multilayer FC-BGA substrate solutions for various electronic products, including computers, communication devices, および家庭用電化製品.
- Xilinx: Known primarily for its FPGA products, Xilinx also manufactures high-performance Multilayer FC-BGA substrates, particularly suited for complex electronic systems and high-speed applications.
- Sino-Top: Sino-Top has significant technological expertise in high-frequency and high-speed PCBs and offers high-quality Multilayer FC-BGA substrates widely used in communications and electronic products.
Our company also manufactures Multilayer FC-BGA substrates. We possess advanced manufacturing equipment and technology, enabling us to produce high-performance substrates that meet industry standards. We offer customized services, designing and producing Multilayer FC-BGA substrates according to our clients’ specific requirements, ensuring excellent electrical performance and reliability.
We are committed to providing high-quality products and services to help our clients meet the demands of complex electronic products. Whether it’s for high-density interconnects, 高周波アプリケーション, or other special requirements, we have the capability to provide solutions. Please contact us to learn more about our production capabilities and technical support for Multilayer FC-BGA substrates.
は何ですか 7 優れたカスタマーサービスの品質?
Good customer service is crucial for building and maintaining positive relationships with customers. Here are seven key qualities of effective customer service:
- 応答: Quick and efficient responses to customer inquiries and issues are essential. Customers appreciate timely assistance and solutions, which helps in resolving problems and preventing frustration.
- 共感: Understanding and addressing customers’ needs and concerns with genuine care is important. Showing empathy helps in building trust and making customers feel valued and heard.
- コミュニケーションスキル: クリア, コンサイス, and effective communication is vital. Service representatives should be able to explain solutions, provide information, and convey messages in a manner that is easily understood by customers.
- 辛抱: Dealing with customers requires patience, especially when they are upset or confused. Service representatives should remain calm and composed, taking the time to address concerns thoroughly and without rushing.
- Knowledgeable: Having a deep understanding of the products or services offered is crucial. Representatives should be well-informed to provide accurate information, answer questions, and resolve issues effectively.
- Consistency: Providing a consistent level of service across all customer interactions is key to ensuring a reliable experience. Consistency helps in building trust and reliability, making customers feel confident in the service provided.
- 問題解決スキル: The ability to address and resolve issues effectively is a fundamental aspect of good customer service. Representatives should be resourceful and proactive in finding solutions, ensuring that customers’ problems are resolved satisfactorily.
These qualities contribute to a positive customer experience, fostering loyalty and encouraging repeat business.
FAQs about Multilayer FC-BGA Substrates
What is a Multilayer FC-BGA Substrate?
A Multilayer FC-BGA Substrate is a complex electronic component used to support and connect integrated circuits through multiple layers of materials.
How is a Multilayer FC-BGA Substrate manufactured?
It involves designing, preparing materials, laminating layers, エッチング, 錬成, 鍍金, とテスト.
What are the common applications of Multilayer FC-BGA Substrates?
They are commonly used in high-performance computing, 電気通信, および家庭用電化製品.
How can I get a quote for a Multilayer FC-BGA Substrate?
Contact our sales team with your design specifications, and we will provide a customized quote based on your requirements.
What materials are used in Multilayer FC-BGA Substrates?
The base materials include prepreg, copper-clad laminates, and other specialized materials depending on the application.
How long does it take to manufacture a Multilayer FC-BGA Substrate?
The manufacturing time varies based on complexity and volume but typically ranges from a few weeks to several months.
What is the typical cost range for a Multilayer FC-BGA Substrate?
Costs vary based on factors such as layer count, 大きさ, and complexity, so please contact us for a detailed quote.