Molded Interconnect Substrate Manufacturer
Molded Interconnect Substrate Manufacturer,成形相互接続基板 (MISの) integrates circuitry directly into a molded plastic substrate, combining mechanical and electrical functions in a single component. This innovative technology enables the creation of complex three-dimensional structures with embedded conductive traces and vias, reducing the need for traditional PCBs and connectors. MIS enhances design flexibility, reduces assembly complexity, and lowers overall manufacturing costs in various industries such as automotive, 家電, および医療機器. By integrating electronics into molded parts, MIS facilitates compact, lightweight designs while improving reliability and performance in rugged environments.
What is a Molded Interconnect Substrate (MISの)?
A Molded Interconnect Substrate (MISの) is a type of electronic packaging technology that integrates circuitry directly into a molded plastic substrate. This substrate typically consists of a thermoplastic material infused with conductive traces, which can be used to create complex three-dimensional structures.
MIS enables the integration of both electrical and mechanical functions into a single part, reducing the need for multiple components and assembly steps in electronic devices. This technology is particularly useful in applications where space, weight, and cost are critical factors, such as in mobile devices, ウェアラブル, 自動車用電子機器, および医療機器.
The manufacturing process of MIS involves several steps, including injection molding of the plastic substrate, laser structuring of conductive traces, and optionally, the integration of components such as LEDs or sensors directly onto the substrate. This integration capability not only reduces the size and weight of devices but also enhances their reliability by minimizing the number of interconnections that could potentially fail.
全, MIS represents an innovative approach to electronic packaging, offering designers flexibility in creating compact and robust electronic devices while optimizing manufacturing efficiency and lowering overall costs.
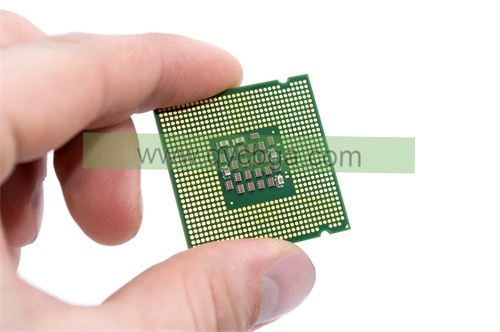
Molded Interconnect Substrate Manufacturer
What are the Molded Interconnect Substrate (MISの) デザインガイドライン?
Designing with Molded Interconnect Substrates (MISの) involves following specific guidelines to ensure the functionality, 確実, and manufacturability of the integrated electronic components. Here are some key design guidelines for MIS:
- 基板材料選定: Choose a thermoplastic material suitable for injection molding, such as liquid crystal polymer (LCPの) or thermoplastic polyurethane (TPU). The material should have good mechanical properties, 寸法安定性, and compatibility with the intended electronic components and manufacturing processes.
- Conductive Trace Design:Design the layout of conductive traces considering electrical performance, シグナルインテグリティ, と熱管理. Ensure proper spacing between traces to prevent electrical interference or short circuits.
- コンポーネントの配置: Plan the placement of electronic components considering space constraints and thermal considerations. Components should be positioned to minimize signal path lengths and ensure adequate clearance for assembly processes.
- Design for Manufacturing (ディエフエム): Follow DFM principles to optimize the mold design, ツーリング, and manufacturing process. Consider draft angles, gate locations, and parting lines to facilitate smooth injection molding and ensure uniform material distribution.
- Surface Finish and Coating: Specify appropriate surface finishes and coatings for the MIS to protect conductive traces from environmental factors such as moisture, corrosion, and mechanical wear.
- Assembly and Interconnects: Design features for mechanical attachment and electrical interconnects between the MIS and other components or circuit boards. Ensure robust solder joints or other reliable connection methods.
- テストと品質保証: Incorporate test points and provisions for in-circuit testing (ICT) or functional testing to verify electrical performance and ensure product quality.
- コンプライアンスと基準: Adhere to relevant industry standards and regulatory requirements for electrical safety, electromagnetic compatibility (EMCの), そして環境の持続可能性.
- サーマルマネジメント: Consider thermal dissipation requirements and incorporate design features such as heat sinks or thermal vias to manage heat generated by electronic components.
- Prototyping and Validation: Conduct prototype testing and validation to evaluate the design’s functionality, 確実, and manufacturability before full-scale production.
By following these design guidelines, engineers can leverage the advantages of Molded Interconnect Substrates (MISの) to create compact, 頼もしい, and cost-effective electronic devices suitable for various applications in consumer electronics, 自動車, healthcare, and beyond.
What is the Molded Interconnect Substrate (MISの) 製作プロセス?
The fabrication process of Molded Interconnect Substrates (MISの) involves several distinct steps to integrate circuitry into a molded plastic substrate. Here’s a general outline of the fabrication process:
- 基板材料選定: The process begins with selecting a suitable thermoplastic material for injection molding, such as liquid crystal polymer (LCPの), thermoplastic polyurethane (TPU), or other compatible materials. The material should have good mechanical properties, 寸法安定性, and be capable of incorporating conductive traces.
- Mold Design: A mold is designed based on the intended shape and features of the MIS. The mold design includes provisions for cavity and core features, gating, and venting to ensure uniform material flow and proper filling of the mold during injection molding.
- Injection Molding: The selected thermoplastic material is melted and injected into the mold under controlled conditions of temperature and pressure. Injection molding allows for the formation of complex three-dimensional shapes with integrated features, such as channels for conductive traces and spaces for electronic components.
- Laser Structuring: After the plastic substrate is molded, laser structuring is used to create conductive traces and interconnections within the substrate. This process involves using a laser to selectively ablate or remove the substrate material where conductive traces are desired. The laser structuring step requires precise control to ensure accurate placement and dimensions of the traces.
- メタライゼーション:Once the substrate is laser structured, a metallization process is employed to deposit a thin layer of conductive material, typically copper, onto the exposed areas where traces have been created. This metallization step ensures electrical conductivity between different circuit elements and components.
- コンポーネントの統合: Electronic components such as LEDs, センサー, or passive components may be integrated directly onto the substrate surface or within designated areas during or after the molding process. This integration can be achieved through pick-and-place assembly techniques or by embedding components within the substrate material.
- 表面仕上げ: After metallization and component integration, the MIS may undergo surface finishing processes to protect conductive traces and improve overall durability. This may include applying coatings for corrosion resistance or enhancing surface properties.
- テストと品質保証: Throughout the fabrication process, various tests are conducted to ensure the functionality and reliability of the MIS. This includes electrical testing to verify connectivity and performance, as well as inspections for dimensional accuracy and adherence to design specifications.
- Assembly and Packaging: Once fabricated and tested, the MIS can be further integrated into larger assemblies or electronic devices. This may involve additional assembly steps to connect the MIS with other components or circuit boards, followed by final packaging to protect the device from environmental factors.
全, the fabrication process of Molded Interconnect Substrates combines injection molding with advanced manufacturing techniques like laser structuring and metallization to create integrated electronic components that are compact, 頼もしい, and cost-effective for a variety of applications in industries such as consumer electronics, 自動車, および医療機器.
How do you manufacture a Molded Interconnect Substrate (MISの)?
Manufacturing a Molded Interconnect Substrate (MISの) involves a precise sequence of steps combining injection molding with specialized processes for creating conductive traces and integrating electronic components. Here’s a detailed overview of the manufacturing process:
- 材料の選択: Choose a thermoplastic material suitable for injection molding, such as liquid crystal polymer (LCPの), thermoplastic polyurethane (TPU), or other engineering plastics. The material should offer good mechanical properties, 寸法安定性, and compatibility with subsequent processing steps.
- Mold Design and Tooling: Design molds for the MIS based on the desired shape, 顔立ち, and layout of conductive traces. The mold design includes considerations for cavity dimensions, gating systems, cooling channels, and venting to ensure uniform material flow and part quality during injection molding.
- Injection Molding: The manufacturing process begins with injection molding, where the chosen thermoplastic material is heated to a molten state and injected into the mold under controlled conditions of temperature and pressure. The mold is filled to form the base substrate with integrated features, including channels and recesses for conductive traces and component placement.
- Laser Structuring: Once the substrate is molded, laser structuring is employed to create conductive traces within the substrate. A laser selectively removes material from the substrate surface where conductive paths are desired, exposing the underlying plastic for subsequent metallization.
- メタライゼーション: After laser structuring, a metallization process is used to deposit a thin layer of conductive material, typically copper, onto the exposed areas of the substrate. This metallization step ensures electrical connectivity between different circuit elements and components integrated into the MIS.
- コンポーネントの統合: Electronic components such as LEDs, センサー, or passive components can be integrated directly onto the substrate surface or within designated areas during or after the molding process. This integration may involve pick-and-place assembly techniques or embedding components within the substrate material.
- 表面仕上げ: The MIS undergoes surface finishing processes to protect conductive traces and enhance overall durability. This may include applying coatings for corrosion resistance, improving solderability, or enhancing surface properties to meet specific application requirements.
- テストと品質管理: 製造プロセス全体を通じて, rigorous testing is conducted to verify the functionality, 確実, and adherence to design specifications of the MIS. Electrical tests ensure proper connectivity and performance, while visual inspections and dimensional measurements confirm part quality.
- Assembly and Packaging: Once fabricated and tested, the MIS can be further assembled into larger electronic assemblies or devices. This may involve connecting the MIS with other components or circuit boards through soldering or other interconnection methods, followed by final packaging to protect the device from environmental factors.
- Final Inspection and Verification: Before shipping or integration into end products, a final inspection ensures that each MIS meets customer requirements and industry standards for performance, 確実, and quality.
これらの製造手順に従ってください, Molded Interconnect Substrates (MISの) are produced as integrated components that offer advantages in size reduction, 信頼性の向上, and cost efficiency for various applications in electronics, 自動車, healthcare, その他.
How much should a Molded Interconnect Substrate (MISの) 費用?
The cost of a Molded Interconnect Substrate (MISの) can vary widely depending on several factors related to design complexity, 使用材料, 製造プロセス, と生産量. Here are some considerations that influence the cost of an MIS:
- 設計の複雑さ: The complexity of the MIS design, レイヤー数を含む, size of the substrate, intricacy of the conductive traces, and integration of components, significantly impacts the cost. More complex designs may require specialized tooling and manufacturing techniques, コストの上昇につながる.
- 料: The choice of thermoplastic material for the substrate, as well as the type and thickness of metallization used for conductive traces, affects costs. High-performance materials like liquid crystal polymers (LCPの) or specialty plastics can be more expensive than standard polymers.
- 製造プロセス:The manufacturing processes involved, such as injection molding, laser structuring, メタライゼーション, and assembly of components, 全体的なコストに貢献する. Advanced techniques and precision manufacturing increase costs compared to simpler methods.
- 生産量: Economies of scale play a significant role in MIS cost. Higher production volumes generally lead to lower per-unit costs due to spreading fixed costs across more units. 逆に言えば, low-volume production runs may incur higher costs per unit.
- Tooling and Setup: Initial costs for mold design, tooling fabrication, and setup for production are significant factors in the overall cost of MIS. These costs are typically amortized over the production volume.
- Quality and Testing Requirements: Meeting stringent quality standards and testing requirements can add to the overall cost of manufacturing MIS. Testing for electrical performance, 確実, and compliance with industry standards may require additional resources and investment.
- Supplier and Geographic Factors: Costs can also vary based on the supplier’s capabilities, geographic location, および諸経費. Different regions may have different labor costs, 規制要件, and logistics considerations that influence overall pricing.
Due to these factors, it’s challenging to provide a specific cost figure for an MIS without detailed information about the design specifications, 料, 製造プロセス, and production volume. 一般的に, MIS costs can range from a few dollars per unit for simpler designs and higher volumes to tens of dollars or more per unit for complex designs or low-volume productions. 正確な価格設定のために, it’s advisable to consult with manufacturers or suppliers specializing in MIS fabrication, who can provide cost estimates based on specific project requirements.
What is Molded Interconnect Substrate (MISの) base material?
The base material used for Molded Interconnect Substrates (MISの) is typically a thermoplastic polymer that can be molded into complex shapes and integrated with conductive traces. Some common materials used as the base substrate for MIS include:
- 液晶ポリマー (LCPの): LCP is a high-performance thermoplastic known for its excellent electrical properties, 寸法安定性, and resistance to heat. It is widely used in applications requiring miniaturization and high-frequency performance.
- Thermoplastic Polyurethane (TPU): TPU is a versatile material known for its flexibility, 耐久性, そして処理の容易さ. It offers good mechanical properties and can be used in applications where impact resistance and elasticity are important.
- Polybutylene Terephthalate (PBT): PBT is a common engineering thermoplastic known for its stiffness, 寸法安定性, and chemical resistance. It is suitable for applications requiring moderate mechanical strength and reliability.
- Polyethylene Terephthalate (ペット): PET is a widely used thermoplastic known for its transparency, mechanical properties, and chemical resistance. It is suitable for applications where cost-effectiveness and good electrical insulation properties are required.
The choice of base material depends on the specific requirements of the application, including mechanical strength, thermal characteristics, 電気的特性, and compatibility with manufacturing processes such as injection molding and laser structuring. These materials are selected to enable the integration of conductive traces and the reliable operation of electronic components within the molded substrate of the MIS.
Which company makes Molded Interconnect Substrates (MISの)?
Many companies are involved in the production of Molded Interconnect Substrates (MISの), especially those focused on electronic packaging and manufacturing microelectronic devices. Companies around the world are leveraging this technology to develop smaller and more powerful electronic products.
The manufacturing of MIS involves complex processes such as injection molding, laser structuring, メタライゼーション, and integration of electronic components. Well-known companies such as Molex, LPKF, RTP Company, とりわけ, have deep expertise and technological capabilities in this field. They provide high-quality and reliable MIS solutions tailored to various application needs using advanced processes and equipment.
Our company also has the capability and experience to produce Molded Interconnect Substrates (MISの). We possess advanced injection molding equipment and laser processing technology to manufacture complex three-dimensional structures according to customer design requirements, including integrated circuit paths and spaces for electronic component installation. Our production team is highly skilled, ensuring precise control over each manufacturing step to meet the highest standards of product quality and performance.
Throughout our manufacturing process, we emphasize quality control and product testing. Each batch of products undergoes rigorous electrical performance testing, visual inspections, and dimensional measurements to ensure compliance with customer requirements and industry standards. We also offer customized surface treatments and coatings to protect circuit paths and enhance product durability and reliability based on customer specifications.
As a company dedicated to technological innovation and customer satisfaction, we are committed to providing innovative solutions that help our customers achieve competitive advantages and market success. Whether in consumer electronics, 自動車用電子機器, 医療機器, or other industries, we support our customers’ product design and manufacturing needs through Molded Interconnect Substrates (MISの) テクノロジー.
は何ですか 7 優れたカスタマーサービスの品質?
Good customer service is characterized by several key qualities that contribute to a positive customer experience and foster long-term customer loyalty. Here are seven qualities of good customer service:
- 応答: 優れたカスタマーサービスチームは、お客様からの問い合わせに迅速に対応します, 懸念, とリクエスト. This includes acknowledging messages and providing timely updates on the status of issues or orders.
- 共感: Empathy involves understanding and sharing the feelings of customers. Good customer service representatives demonstrate empathy by actively listening to customers, showing genuine concern for their needs, and striving to resolve issues from the customer’s perspective.
- Clear Communication: Effective communication is essential in customer service. This includes conveying information clearly and concisely, using language that is easily understandable to the customer, and ensuring that expectations are properly set and managed.
- 知識能力: Customer service representatives should have a good understanding of the products or services offered by the company. They should be knowledgeable enough to answer customer questions accurately and provide helpful guidance or troubleshooting assistance.
- プロ 意識: Professionalism encompasses behaviors such as courtesy, respectfulness, and maintaining a positive attitude even in challenging situations. It involves conducting oneself in a manner that reflects well on the company and promotes trust and confidence with customers.
- 問題解決スキル: Dealing with customer issues and complaints requires strong problem-solving skills. Good customer service involves actively seeking solutions to problems, taking ownership of issues, and following through to ensure resolution to the customer’s satisfaction.
- パーソナル 化: Providing personalized customer service involves treating each customer as an individual with unique preferences and needs. This can include remembering past interactions, preferences, or specific circumstances related to the customer’s experience with the company.
By consistently demonstrating these qualities, organizations can create a positive customer service experience that builds customer trust, satisfaction, and loyalty. Good customer service not only resolves immediate issues but also strengthens the overall relationship between the customer and the company.
よくあるご質問(FAQ)
What is a Molded Interconnect Substrate (MISの)?
A Molded Interconnect Substrate (MISの) is a technology that integrates circuitry directly into a molded plastic substrate. It combines the functions of a substrate and interconnects into a single part, enabling compact and efficient electronic designs.
What are the advantages of using MIS?
MIS offers several advantages, including reduced space and weight in electronic devices, 組み立てプロセスの簡素化, improved reliability by minimizing interconnections, and potential cost savings in manufacturing.
What materials are used in MIS?
Common materials used for MIS substrates include liquid crystal polymers (LCPの), thermoplastic polyurethane (TPU), and other engineering thermoplastics that are suitable for injection molding and compatible with electronic components.
What applications are suitable for MIS?
MIS technology is used in a wide range of applications such as mobile devices, ウェアラブル, 自動車用電子機器, 医療機器, とIoT (モノのインターネット) devices where space, weight, and reliability are critical factors.
What are the design guidelines for MIS?
Design guidelines for MIS include considerations for substrate material selection, conductive trace design, コンポーネントの配置, 製造可能性 (ディエフエム), サーマルマネジメント, テスティング, 業界標準への準拠.
Who manufactures MIS?
Several companies specialize in the manufacturing of Molded Interconnect Substrates (MISの), providing customized solutions based on customer specifications and application requirements.