Minimum Clearance PCB Manufacturer
Minimum Clearance PCB Manufacturer,Minimum Clearance PCBs are printed circuit boards designed with precise spacing between conductive elements to prevent unintended electrical connections or short circuits. These PCBs adhere to strict clearance requirements, ensuring safe operation in various applications, including high-voltage environments and sensitive electronic devices. By maintaining minimum distances between traces, パッド, and components, Minimum Clearance PCBs minimize the risk of electrical hazards, signal interference, and malfunctioning. These boards are essential for ensuring reliability, safety, and compliance with industry standards in electronic design and manufacturing.
What is a Minimum Clearance PCB?
A Minimum Clearance PCB, also known as a clearance requirement or spacing rule, refers to the minimum allowable distance between conductive elements on a printed circuit board (プリント基板). This specification is crucial for preventing unintended electrical connections or short circuits that could lead to malfunctions or damage in electronic devices.
When designing a PCB, engineers must consider various factors like voltage, current, and environmental conditions to determine the appropriate clearance requirements. These requirements ensure that the PCB can safely operate without interference or risk of electrical hazards.
Expanding upon the concept, a Minimum Clearance PCB with a requirement of, 例えば, 300 micrometers, mandates that no conductive traces, パッド, or components should be closer to each other than this specified distance. This distance is typically measured between the edges of adjacent conductive elements, such as traces, パッド, or component leads.
Maintaining proper clearance distances is crucial in high-voltage applications or environments with high electromagnetic interference (EMIの) to prevent arcing, sparking, or signal interference. Failure to adhere to clearance requirements can lead to electrical failures, safety hazards, or regulatory non-compliance.
Engineers employ various design techniques and software tools to ensure that PCB layouts comply with minimum clearance requirements while optimizing space utilization and electrical performance. These techniques may include trace routing algorithms, design rule checks (コンゴ民主共和国), and simulations to validate the integrity of the design before fabrication.
まとめ, a Minimum Clearance PCB specifies the minimum allowed distance between conductive elements on a printed circuit board to ensure electrical safety, 確実, and compliance with design standards and regulations.
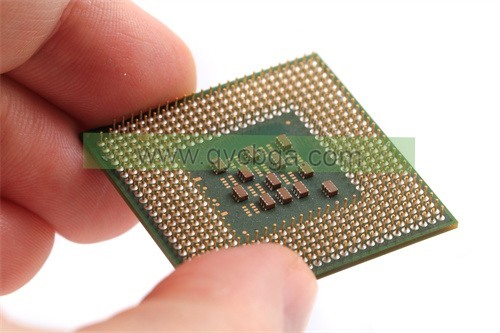
Minimum Clearance PCB Manufacturer
What are the Minimum Clearance PCB Design Guidelines?
Minimum Clearance PCB design guidelines are crucial for ensuring the integrity, 確実, and safety of electronic devices. Here are some key guidelines:
- Define Clearances:Clearly define minimum clearance requirements based on the specific application, 電圧レベル, and environmental conditions. This includes minimum clearances between traces, between traces and pads, between traces and board edges, and between components.
- Follow Manufacturer Guidelines:Adhere to clearance guidelines provided by component manufacturers, especially for components with specific high-voltage or high-frequency requirements.
- Consider Environmental Factors:Account for environmental factors such as temperature variations, 湿度, 振動, and contamination when determining clearance requirements.
- Use Design Rule Checks (コンゴ民主共和国):Utilize PCB design software with DRC capabilities to automatically check for clearance violations and ensure compliance with specified design rules.
- Keep Traces Parallel:Maintain parallelism between adjacent traces to minimize capacitive coupling and electromagnetic interference (EMIの), which can be especially critical in high-frequency applications.
- Avoid Sharp Corners:Round or chamfer sharp corners to prevent electric field concentration, which can lead to arcing or breakdown in high-voltage applications.
- Separate High and Low Voltage: Keep high-voltage and low-voltage traces, コンポーネント, and signal paths physically separated to prevent cross-talk and reduce the risk of electrical hazards.
- Consider Creepage and Clearance:In high-voltage applications, consider both creepage (the distance along the surface of the PCB) and clearance (the shortest distance through air) to prevent arcing and ensure safety.
- Optimize Layout:Optimize PCB layout to minimize trace lengths, reduce the number of vias, and maintain consistent trace widths to improve signal integrity and reduce manufacturing costs.
- Thermal Considerations:Ensure proper clearance around high-power components and traces to facilitate heat dissipation and prevent thermal issues that could affect performance or reliability.
- Documentation:Document clearance requirements clearly in the PCB design documentation, including assembly drawings, 製造図面, and design specifications, to ensure proper communication with manufacturers and assembly teams.
これらのガイドラインに従う, PCB designers can create layouts that meet safety standards, minimize signal interference, and optimize the performance and reliability of electronic devices.
What is the Minimum Clearance PCB Fabrication Process?
The fabrication process for a Minimum Clearance PCB involves several steps to ensure that the specified clearance requirements are met accurately. Here’s an overview of the typical process:
- Design Phase:During the PCB design phase, engineers specify the minimum clearance requirements based on the application, 電圧レベル, and environmental conditions. They use PCB design software to lay out the circuitry and ensure that all traces, パッド, and components adhere to the clearance guidelines.
- Design Review:Before proceeding to fabrication, the PCB design undergoes a thorough review process to check for any clearance violations or other design errors. Design rule checks (コンゴ民主共和国) are performed using PCB design software to verify that all design rules, including clearance requirements, are met.
- Gerber File Generation:Once the design is finalized, the PCB layout is converted into Gerber files, which contain the necessary information for manufacturing the PCB. These files include detailed instructions for the fabrication process, including trace widths, パッドサイズ, そして, importantly, clearance distances.
- パネライゼーション:In many cases, multiple PCBs are fabricated together on a larger panel to optimize production efficiency. During panelization, the Gerber files are arranged on a panel layout, ensuring proper spacing between individual PCBs to prevent interference during fabrication.
- Photoresist Application:The fabrication process typically begins with the preparation of the copper-clad substrate. A layer of photoresist material is applied to the substrate, which will later be used to transfer the PCB design onto the copper surface.
- Exposure and Development:The Gerber files are used to create photo masks, which are then used to expose the photoresist layer to UV light. The exposed areas of the photoresist harden, while the unexposed areas remain soluble. 露光後, the board is developed to remove the unexposed photoresist, revealing the copper underneath.
- エッチング: The PCB is then submerged in an etchant solution, which selectively removes the exposed copper, 必要な銅トレースとパッドを残します. The etching process is carefully controlled to ensure that the minimum clearance requirements are maintained throughout the board.
- Drilling:After etching, the PCB undergoes drilling to create holes for component mounting and vias. The drilling process must be precise to avoid any violations of the clearance requirements around the drilled holes.
- 表面仕上げ:Once drilling is complete, the PCB may undergo surface finishing processes such as HASL (hot air solder leveling), エニグ (無電解ニッケル浸漬金), or immersion tin to protect the exposed copper surfaces and facilitate soldering.
- Final Inspection:Before the PCBs are separated from the panel and sent for assembly, they undergo a final inspection to verify that all clearance requirements have been met and that the boards are free from defects.
By following these steps and paying close attention to the clearance requirements at each stage of the fabrication process, manufacturers can ensure that the resulting PCBs meet the specified design criteria and perform reliably in their intended applications.
How do you manufacture a Minimum Clearance PCB?
Manufacturing a Minimum Clearance PCB involves several steps to ensure that the specified clearance requirements are met accurately. Here’s a detailed outline of the manufacturing process:
- Design Phase: Engineers specify the minimum clearance requirements during the PCB design phase based on the application, 電圧レベル, and environmental conditions. Using PCB design software, they layout the circuitry ensuring that all traces, パッド, and components adhere to the clearance guidelines.
- Design Review:Before fabrication, the PCB design undergoes a comprehensive review to check for clearance violations or other errors. Design rule checks (コンゴ民主共和国) are performed using PCB design software to verify that all design rules, including clearance requirements, are met.
- Gerber File Generation:Once the design is finalized, the PCB layout is converted into Gerber files. These files contain instructions for manufacturing the PCB, including trace widths, パッドサイズ, and clearance distances.
- パネライゼーション:Multiple PCBs may be fabricated together on a larger panel to optimize production efficiency. During panelization, the Gerber files are arranged on a panel layout, ensuring proper spacing between individual PCBs to prevent interference during fabrication.
- 基質調製:The fabrication process starts with the preparation of the copper-clad substrate. A layer of photoresist material is applied to the substrate, which will be used to transfer the PCB design onto the copper surface.
- Exposure and Development: The Gerber files are used to create photo masks, which expose the photoresist layer to UV light. The exposed areas harden, while the unexposed areas remain soluble. 露光後, the board is developed to remove the unexposed photoresist, revealing the copper underneath.
- エッチング:The PCB is submerged in an etchant solution, which selectively removes the exposed copper, 必要な銅トレースとパッドを残します. The etching process is controlled to ensure that the minimum clearance requirements are maintained throughout the board.
- Drilling:After etching, the PCB undergoes drilling to create holes for component mounting and vias. Drilling must be precise to avoid violations of the clearance requirements around the holes.
- 表面仕上げ:The PCB may undergo surface finishing processes such as HASL, エニグ, or immersion tin to protect the exposed copper surfaces and facilitate soldering.
- Final Inspection:Before separating the PCBs from the panel and sending them for assembly, they undergo a final inspection. This verifies that all clearance requirements have been met and that the boards are free from defects.
By following these steps and closely monitoring clearance requirements throughout the manufacturing process, manufacturers can ensure that the resulting PCBs meet the specified design criteria and perform reliably in their intended applications.
How much should a Minimum Clearance PCB cost?
The cost of manufacturing a Minimum Clearance PCB can vary significantly based on several factors:
- Board Size:Larger PCBs generally cost more to manufacture due to increased material costs and longer production times.
- Complexity:The complexity of the PCB design, レイヤー数を含む, density of components, and intricacy of the traces, 製造コストに影響を与える可能性があります. Designs with tight clearance requirements may require more precise fabrication techniques, which can add to the cost.
- 材料の選択:基板材料の選択 (例えば。, FR-4, flexible, or rigid-flex PCBs) and surface finish options can affect the cost. Some materials may be more expensive but offer specific benefits such as higher temperature resistance or better electrical properties.
- Manufacturing Technology:高度な製造技術, such as HDI (高密度インターコネクト) or microvia drilling, may be necessary to achieve tight clearance requirements. These technologies typically incur higher fabrication costs.
- Volume:The quantity of PCBs being manufactured can impact the unit cost. Higher volumes often result in lower per-unit costs due to economies of scale.
- Turnaround Time:Expedited production services or shorter lead times may come at an additional cost.
- Quality Assurance:Manufacturers may offer additional quality assurance measures, such as electrical testing, inspection services, or certifications (例えば。, ISO, IPC), which can increase the overall cost.
To obtain an accurate cost estimate for manufacturing a Minimum Clearance PCB, it’s essential to consult with PCB manufacturers or suppliers. They can provide quotes based on your specific design requirements, quantities, and desired turnaround times. かつ, online PCB fabrication services often offer instant quotes based on uploaded design files, allowing you to quickly estimate costs for different design parameters.
What is Minimum Clearance PCB base material?
The choice of base material for a Minimum Clearance PCB depends on various factors such as the application, 動作条件, and manufacturing requirements. しかし, certain materials are commonly used due to their electrical properties, 熱性能, と製造可能性. Here are some typical base materials for Minimum Clearance PCBs:
- FR-4 (Fire Retardant 4): FR-4 is the most widely used substrate material for PCBs due to its affordability, 良好な電気絶縁特性, 製造の容易さ. It consists of a woven fiberglass cloth impregnated with an epoxy resin binder. FR-4 is suitable for many applications, 家電製品を含む, 電気通信, and industrial controls.
- High-Temperature FR-4:For applications requiring elevated temperature performance, high-temperature FR-4 variants with enhanced thermal stability and mechanical strength are available. These materials can withstand higher operating temperatures without compromising electrical performance.
- ポリイミド (円周率):Polyimide substrates offer excellent thermal stability, 柔軟性, and resistance to chemicals and radiation. They are commonly used in flexible PCBs and rigid-flex PCBs where flexibility is required, 航空宇宙など, 医療機器, およびウェアラブル電子機器.
- PTFE製 (ポリテトラフルオロ エチレン):PTFE-based materials, such as Teflon, offer exceptional electrical properties, low dielectric loss, and high thermal stability. They are often used in high-frequency and high-speed applications, including RF/microwave circuits and antennas.
- メタルコア (MCPCB):Metal core PCBs feature a metal substrate (usually aluminum or copper) for improved thermal conductivity and heat dissipation. They are suitable for high-power LED lighting, 自動車用電子機器, and power electronics applications where heat management is critical.
- セラミック:Ceramic substrates provide excellent thermal conductivity, 機械的強度, と寸法安定性. They are commonly used in high-power and high-frequency applications, such as power amplifiers, RF transmitters, and microwave circuits.
- Rogers Materials:Rogers Corporation manufactures a range of high-performance PCB substrates tailored for specific applications, including high-frequency, microwave, and RF/microwave circuits. These materials offer low dielectric loss, stable electrical properties, and tight dimensional tolerances.
The selection of the base material depends on factors such as signal integrity requirements, 熱管理のニーズ, コストに関する考慮事項, and manufacturability constraints. Designers should carefully evaluate these factors to choose the most suitable material for their Minimum Clearance PCB design.
Which company makes Minimum Clearance PCBs?
There are many companies specializing in the manufacture of Minimum Clearance PCBs, usually professional PCB manufacturers or electronic manufacturing service providers. Some well-known companies include Foxconn, JLCPCB, and Eurocircuits. These companies typically have advanced manufacturing equipment, extensive experience, and professional technical teams to meet the PCB manufacturing needs of various electronic products.
Our company is also a professional PCB manufacturer with many years of manufacturing experience and advanced production equipment. We focus on quality, 確実, and customer satisfaction, committed to providing high-quality Minimum Clearance PCB solutions to our customers.
Our manufacturing capabilities include:
- High Precision Manufacturing:We have advanced PCB manufacturing equipment and precise processing technology to achieve high-precision layout and design requirements with tiny clearances.
- 厳格な品質管理:We adopt strict quality control processes, including design validation, raw material inspection, production process monitoring, and final product testing, to ensure that each PCB meets design requirements and customer expectations.
- Fast Delivery:We have efficient production processes and flexible production arrangements to quickly respond to customer needs and provide timely delivery services.
- カスタマイズ:We can customize Minimum Clearance PCBs with different specifications, sizes, and materials according to customer requirements, meeting the needs of various application scenarios.
- Professional Technical Support:We have an experienced engineering team and professional technical support to provide comprehensive technical support and consulting services to customers, helping them solve various PCB design and manufacturing issues.
Through our efforts and professional capabilities, our company can provide customers with high-quality Minimum Clearance PCB solutions and establish long-term stable cooperation relationships with them. We will continue to improve our manufacturing capabilities and service levels to create greater value and success for customers.
は何ですか 7 優れたカスタマーサービスの品質?
Good customer service is characterized by several key qualities that contribute to positive interactions and relationships between businesses and their customers. Here are seven important qualities:
- 応答:Good customer service involves being prompt and timely in addressing customer inquiries, requests, and concerns. This includes responding to emails, phone calls, and messages promptly, as well as providing timely assistance and solutions to customer issues.
- 共感:Empathy is the ability to understand and share the feelings and perspectives of customers. Good customer service representatives listen actively to customers, 自分の感情を認める, and demonstrate genuine concern for their needs and experiences.
- Clear Communication:Clear communication is essential for effective customer service. Customer service representatives should communicate information clearly and concisely, avoiding jargon and technical language, and ensuring that customers understand their options, 指示, and solutions.
- 知識能力: Good customer service requires a thorough understanding of the products, services, policies, and processes offered by the business. Customer service representatives should be knowledgeable about the company’s offerings and be able to provide accurate information and assistance to customers.
- 問題解決スキル: Effective problem-solving skills are crucial for resolving customer issues and complaints satisfactorily. Good customer service representatives are resourceful, proactive, and creative in finding solutions to customer problems, 困難な状況でも.
- プロ 意識:Professionalism involves conducting oneself with integrity, 尊敬, and courtesy when interacting with customers. Good customer service representatives maintain a positive attitude, remain calm under pressure, and treat customers with dignity and professionalism at all times.
- フォローアップ:Following up with customers after resolving their issues or completing a transaction demonstrates a commitment to customer satisfaction and relationship-building. Good customer service includes checking in with customers to ensure their needs have been met and addressing any additional concerns or feedback they may have.
これらの資質を具現化することで、, businesses can cultivate a reputation for providing exceptional customer service and build strong, loyal relationships with their customers over time.
よくあるご質問(FAQ)
What are Mixed Dielectric Rogers PCBs?
Mixed Dielectric Rogers PCBs are printed circuit boards (プリント基板) manufactured using Rogers Corporation’s high-performance materials with different dielectric constants. These PCBs are designed for applications requiring precise control of impedance and signal integrity, such as high-frequency, microwave, and RF circuits.
What are the benefits of Mixed Dielectric Rogers PCBs?
Mixed Dielectric Rogers PCBs offer several advantages, including precise impedance control, reduced signal loss, シグナルインテグリティの向上, and enhanced reliability. These PCBs are ideal for applications demanding high-frequency performance and low insertion loss.
What applications are suitable for Mixed Dielectric Rogers PCBs?
Mixed Dielectric Rogers PCBs are commonly used in various high-frequency and microwave applications, 電気通信を含む, 航宇, defense, automotive radar systems, satellite communications, and wireless networking equipment.
What types of materials are used in Mixed Dielectric Rogers PCBs?
Mixed Dielectric Rogers PCBs utilize Rogers Corporation’s high-performance laminate materials, such as RO4000® Series, RO3000® Series, and RO4400™ Series. These materials feature different dielectric constants and are optimized for specific frequency ranges and applications.
How are Mixed Dielectric Rogers PCBs manufactured?
Mixed Dielectric Rogers PCBs are manufactured using standard PCB fabrication processes, 基質調製を含む, layer stacking, copper etching, 錬成, 鍍金, ソルダーマスクアプリケーション, および表面仕上げ. Specialized processes may be employed to ensure precise control of impedance and signal integrity.
What design considerations are important for Mixed Dielectric Rogers PCBs?
Designers should consider factors such as layer stackup configuration, trace impedance calculations, transmission line design, ビア配置, and material selection to optimize the performance of Mixed Dielectric Rogers PCBs. Working closely with experienced PCB designers and manufacturers is recommended to ensure successful implementation.
Are Mixed Dielectric Rogers PCBs cost-effective?
The cost of Mixed Dielectric Rogers PCBs may be higher compared to standard FR-4 PCBs due to the specialized materials and manufacturing processes involved. しかし, the performance benefits and reliability of Mixed Dielectric Rogers PCBs often justify the investment for applications requiring high-frequency performance and signal integrity.
Where can I obtain Mixed Dielectric Rogers PCBs?
Mixed Dielectric Rogers PCBs can be obtained from experienced PCB manufacturers specializing in high-frequency and RF/microwave applications. It’s important to choose a reputable manufacturer with expertise in working with Rogers Corporation’s materials and meeting the specific requirements of your application.