ICパッケージ基板メーカー
ICパッケージ基板メーカー,An IC package substrate is a crucial component in the semiconductor packaging process, serving as the interface between the silicon chip and the printed circuit board (プリント基板). It provides mechanical support and electrical connections through a network of conductive traces and vias. Typically made from materials like BT resin, FR-4, or advanced ceramics, these substrates offer high thermal conductivity, low thermal expansion, そして優秀な電気性能. They are designed to handle the increasing complexity and miniaturization of modern integrated circuits, ensuring efficient power distribution, シグナルインテグリティ, and heat dissipation, ultimately enhancing the reliability and performance of electronic devices.
とは IC Package Substrate?
The IC package substrate is a crucial component in electronic packaging, primarily used to connect and support integrated circuit (集積回路) フライドポテト. It provides mechanical support for the chip and facilitates electrical interconnections between the chip and external circuits. Key functions of the IC package substrate include signal transmission, 配電, サーマルマネジメント, and physical protection.
Modern IC package substrates are typically multi-layer structures made from high-performance materials such as fiberglass-reinforced epoxy resin (FR-4), ポリイミド (円周率), and ceramic materials. These materials offer excellent electrical performance and thermal stability, which are essential for applications in high-frequency and high-heat environments.
In semiconductor manufacturing, IC package substrates play a critical role, affecting overall circuit performance, product reliability, and lifespan. Advanced packaging technologies, such as Flip Chip and Ball Grid Array (BGAの), rely on high-quality substrates to achieve higher integration and smaller package sizes.
With the rapid advancement of semiconductor technology, the design and manufacturing of IC package substrates are also evolving. 例えば, substrates utilizing high-density interconnect (HDIの) technology enable finer line widths and smaller vias, supporting more complex circuit designs. かつ, embedded passive components (such as capacitors and resistors) are integrated into substrates to enhance circuit performance and save space.
The market demand for IC package substrates is growing rapidly with the rise of emerging technologies like 5G, 人工知能 (AI), and the Internet of Things (IoTの). These applications place higher performance demands on substrates, driving continuous innovation in material science and manufacturing processes. 全, IC package substrates are a fundamental cornerstone of integrated circuit technology, with their performance and reliability directly impacting the quality and competitiveness of electronic products.
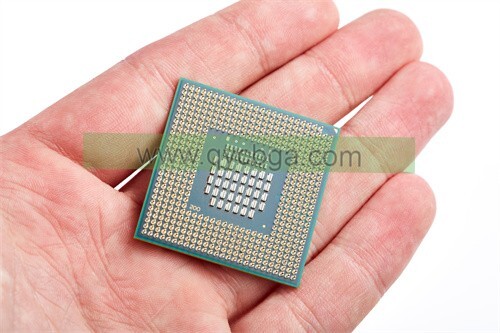
ICパッケージ基板メーカー
は何ですか IC Package Substrate デザインガイドライン?
IC package substrate design guidelines are essential principles to ensure that the package substrate effectively supports the performance and reliability of integrated circuits (ICの). Key factors to consider during the design process include:
- 材料の選択: Choosing the right materials is crucial for the electrical performance and thermal management of the substrate. Common materials include fiberglass-reinforced epoxy resin (FR-4), ポリイミド (円周率), 陶芸, and high-frequency materials. Material selection should be based on application requirements, such as high frequency, high power, or high-heat environments.
- Layer Count and Structure: The number of layers and the interlayer structure of the substrate directly impact signal transmission and power distribution. Multi-layer structures are typically used for high-density interconnect (HDIの) and complex circuit designs to minimize signal interference and enhance electrical performance.
- Trace Width and Spacing: Precise calculation of trace width and spacing is necessary to ensure signal integrity and reduce crosstalk. With advancements in technology, increasingly finer trace widths and smaller vias are being used in high-performance substrates.
- Thermal Design: Effective thermal management is crucial for the stability and longevity of ICs. The design should consider thermal channels, ヒートシンク, and thermal conductive materials to maintain appropriate temperatures during operation.
- Power Distribution Network: A well-designed power distribution network reduces power noise and improves system stability. The design should include proper layout of power and ground layers and the use of suitable decoupling capacitors to optimize power stability.
- Packaging and Soldering: Ensuring that packaging and soldering processes meet design requirements is essential to avoid physical damage and electrical failures. The design should account for pad layout and solder materials to ensure good solder quality and reliability.
- Testing and Verification: Comprehensive testing and verification after design completion are necessary to ensure substrate performance and reliability. This includes electrical testing, 熱試験, and mechanical testing to confirm that the substrate meets design specifications and application requirements.
- 製造プロセス: Consider the feasibility and cost-effectiveness of the manufacturing process, and design with sufficient tolerance to accommodate variations in the actual production process.
まとめ, IC package substrate design requires a holistic approach that considers material selection, structural layout, サーマルマネジメント, 配電, and manufacturing processes to ensure performance, 確実, そして費用対効果.
は何ですか IC Package Substrate 製作プロセス?
The fabrication process of IC package substrates involves several critical steps, each essential to ensuring the performance and reliability of the final product. Here are the main steps in the IC package substrate fabrication process:
- 材料の準備: Select and prepare appropriate substrate materials such as fiberglass-reinforced epoxy resin (FR-4), ポリイミド (円周率), またはセラミックス. Materials are typically supplied in thin sheets and need to be cut and processed according to design requirements.
- Layering and Laminating: Stack different substrate material layers according to the design. The layers are bonded together through heating and pressing using a laminating machine to ensure good adhesion and integrity between the layers.
- Pattern Transfer: Use photolithography to transfer circuit patterns onto the substrate. A photosensitive coating (フォトレジスト) is applied to the substrate, and then exposed to light through a mask to create the circuit pattern. The unexposed photoresist and excess material are removed through developing and etching processes, forming the circuit pattern on the substrate.
- 穴あけとメッキ: Drill holes in the substrate as required by the design, which will be used for electrical connections and mounting. Electroplating is then performed to deposit metal layers on the walls of the holes, creating electrical vias. This step also involves depositing conductive metal layers, 銅など.
- Deposition and Plating: Deposit a thin metal layer onto the substrate surface to enhance electrical performance and ensure good solderability. This typically involves chemical vapor deposition (CVD検出器) or electroplating processes.
- Pad and Land Fabrication: Create pads and lands on the substrate to provide electrical connections between the IC chip and the substrate. This includes depositing metal pads onto the substrate and surface treatment to improve solder quality.
- Cutting and Shaping: Cut the fabricated substrate into the required sizes and shapes. This may include cutting large panels into individual substrates or trimming the substrate to specific packaging forms.
- テストと検査: Perform electrical, メカニカル, and thermal performance tests to ensure the substrate meets design specifications and performance requirements. Testing includes functional checks, connectivity verification, and thermal management assessments.
- Surface Treatment and Coating: Apply surface treatments, such as protective coatings or solder masks, to enhance the durability and reliability of the substrate.
- Assembly and Packaging: 最終的に, solder the IC chips onto the substrate and perform final packaging. Packaging steps may include adding package bases, sealing, and testing to ensure integrity and functionality.
全, the IC package substrate fabrication process involves material preparation, pattern transfer, 錬成, 鍍金, pad fabrication, cutting, テスティング, とパッケージング. Each step must be carefully controlled to ensure the quality and performance of the final product.
どのように製造しますか IC Package Substrate?
Manufacturing IC package substrates involves a series of intricate steps to ensure high performance and reliability. ここでは、製造プロセスの概要をご紹介します:
- 材料の選択と準備: Begin by selecting suitable substrate materials such as fiberglass-reinforced epoxy resin (FR-4), ポリイミド (円周率), またはセラミックス. The materials are supplied in large sheets, which are cut into the required sizes for further processing.
- Layering and Laminating: Stack the prepared material layers according to the design specifications. These layers are then laminated together using heat and pressure to create a multi-layer substrate. This step ensures that the layers adhere properly and maintain structural integrity.
- 写真石版: Apply a photosensitive coating (フォトレジスト) 基板表面に. フォトリソグラフィーの使用, expose the photoresist to light through a mask that defines the circuit patterns. Develop the exposed photoresist to reveal the pattern, and then etch away the unwanted material to create the circuit design on the substrate.
- 穴あけとメッキ: Drill holes in the substrate where electrical connections and vias are required. Electroplating is then used to deposit metal, 銅など, onto the walls of these holes to form electrical connections. This process also involves plating the surface with a thin layer of metal for conductivity.
- 堆積: Deposit additional thin metal layers onto the substrate surface to enhance electrical performance and ensure good solderability. Techniques such as chemical vapor deposition (CVD検出器) or electroplating are commonly used for this purpose.
- Pad and Land Formation: Create metal pads and lands on the substrate where IC chips will be soldered. This involves depositing and patterning metal to form the necessary contact points for chip mounting and connection.
- Cutting and Shaping: Cut the laminated and processed substrate into specific sizes and shapes as required. This may involve dividing large panels into individual substrates or shaping them to fit particular packaging forms.
- テストと検査: Conduct various tests to ensure that the substrate meets design specifications and performance requirements. This includes electrical testing for continuity and functionality, thermal testing to check heat dissipation, and mechanical testing to ensure structural integrity.
- Surface Treatment: Apply surface treatments such as solder masks, protective coatings, or finishes to enhance the durability and reliability of the substrate. These treatments help protect the substrate from environmental factors and improve soldering quality.
- Assembly and Packaging: Solder the IC chips onto the substrate and perform final assembly and packaging. This step includes mounting the chips, sealing the package, and conducting final quality checks to ensure that the substrate is ready for use in electronic devices.
まとめ, manufacturing IC package substrates involves material preparation, layering, 写真石版, 錬成, 鍍金, 堆積, pad formation, cutting, テスティング, 表面処理, と組み立て. Each step requires precise control and quality assurance to produce high-performance and reliable substrates.
いくらにすべきか IC Package Substrate 費用?
The cost of IC package substrates can vary widely based on several factors, including materials, 設計の複雑さ, 製造数量, and additional features. Here’s a detailed breakdown of the cost factors:
- 料: The choice of substrate materials significantly impacts cost. High-performance materials such as polyimide (円周率), 陶芸, and high-frequency materials generally cost more than standard materials like fiberglass-reinforced epoxy resin (FR-4). Premium materials that offer better thermal management, シグナルインテグリティ, and durability will increase the overall cost.
- 設計の複雑さ:Substrates with complex designs, such as high-density interconnect (HDIの) or multi-layer structures, require more advanced manufacturing processes and increased labor, which can drive up costs. Substrates with fine traces, small vias, and high-precision patterns will also be more expensive.
- 製造台数: The cost per unit typically decreases with larger production volumes due to economies of scale. High-volume production can reduce the per-unit cost of substrates, while small-batch or prototype production will generally be more expensive.
- レイヤー数: Substrates with more layers, such as those used in advanced packaging technologies (例えば。, Ball Grid Array or Flip Chip), require more complex manufacturing processes and materials, これにより、コストが増加する可能性があります.
- 追加機能: Special features such as embedded passive components (コンデンサー, resistors), 高度な熱管理ソリューション, or custom surface finishes will add to the cost. The inclusion of these features often requires additional processing steps and materials.
- テストと品質管理: Comprehensive testing and quality control measures ensure substrate reliability and performance. Rigorous testing procedures can increase manufacturing costs, but they are essential for high-reliability applications.
- Lead Time and Customization: Shorter lead times and customized solutions can also impact cost. Expedited production schedules and tailored designs often come with higher price tags.
- Regional Factors: Costs can vary based on geographic location and the cost of labor and materials in different regions. 例えば, substrates manufactured in regions with high labor costs or stringent environmental regulations may be more expensive.
As a general guideline, the cost of IC package substrates can range from a few dollars to several hundred dollars per unit, 上記の要因によります. For basic FR-4 substrates, costs might be on the lower end of the spectrum, while advanced substrates with high-density interconnects or specialized materials can command higher prices. Custom quotes from manufacturers will provide the most accurate cost based on specific requirements and production volumes.
とは IC Package Substrate ベースマテリアル?
IC package substrate base material refers to the fundamental material used to construct the substrate on which integrated circuits (ICの) are mounted and electrically connected. It provides mechanical support and electrical interconnections between the IC and the external circuitry. The choice of base material is critical for the substrate’s performance, 確実, and suitability for different applications. Here’s an overview of common base materials used in IC package substrates:
- Fiberglass-Reinforced Epoxy Resin (FR-4): FR-4 is the most commonly used base material for standard IC package substrates. It consists of woven fiberglass cloth impregnated with an epoxy resin. FR-4 offers good mechanical strength, 電気絶縁性, and moderate thermal conductivity, making it suitable for a wide range of electronic applications.
- ポリイミド (円周率): ポリイミドは、その優れた熱安定性で知られる高性能ポリマーです, 耐薬品性, および電気絶縁特性. It is often used in flexible and high-temperature applications, as well as for substrates requiring superior thermal management and flexibility.
- セラミック材料: セラミック基板, such as aluminum oxide (Al2O3) または窒化アルミニウム (AlNの), are used in applications requiring high thermal conductivity and electrical insulation. Ceramics are often employed in high-power or high-frequency applications due to their excellent heat dissipation and stability under harsh conditions.
- High-Frequency Materials: For applications involving high-frequency signals, materials such as PTFE (ポリテトラフルオロ エチレン) or ceramic-filled PTFE are used. These materials have low dielectric constants and loss tangents, which are essential for maintaining signal integrity in high-frequency circuits.
- Polyethylene Terephthalate (ペット): PET is sometimes used for flexible substrates due to its good mechanical properties and flexibility. It is less commonly used in rigid IC packaging but can be found in certain flexible or hybrid packaging solutions.
- Low-Temperature Co-Fired Ceramics (LTCC): LTCC is a type of ceramic material that allows for the co-firing of multiple layers with embedded passive components. It offers high reliability and is used in advanced applications requiring high-density interconnects and integration of passive components.
- 高密度インターコネクト (HDIの) 料: HDI substrates use advanced materials and processes to create fine traces and small vias. They often incorporate materials with improved electrical and thermal properties to support high-density and high-performance applications.
The choice of base material for IC package substrates depends on several factors, including the specific application requirements, operating environment, 熱管理のニーズ, and desired electrical performance. Each material offers unique properties that make it suitable for different types of electronic devices and systems.
どの会社が作っているか IC Package Substrate?
現在は, there are many companies in the market that manufacture IC package substrates, such as Renesas Electronics, Amphenol, Hitachi Chemical, Shin-Etsu Chemical, and Toshiba. These companies have extensive experience and technology in IC package substrates, capable of producing high-performance substrates to meet various application needs.
Renesas Electronics is renowned for its innovations in integrated circuit packaging technology, with its high-density interconnect (HDIの) substrates widely used in electronic devices. Amphenol specializes in high-performance packaging solutions, with products used in communications, 自動車, and industrial electronics. Hitachi Chemical has a deep expertise in high-temperature and high-frequency substrate materials, providing reliable solutions for IC packaging. Shin-Etsu Chemical focuses on the development of high-performance substrate materials, with products excelling in high-frequency and high-power applications. Toshiba has rich experience in the design and manufacturing of packaging substrates, offering high-quality IC packaging solutions.
Our company also has the capability to manufacture IC package substrates. We use advanced substrate materials and technologies to ensure excellent performance in various application environments. Our IC package substrates have the following features:
- High-Performance Substrate Materials: We use high-quality substrate materials such as polyimide (円周率), ceramic materials, and high-frequency materials to ensure stability and reliability under high-frequency, high-power, and high-temperature conditions.
- Precision Processing Technology: We have advanced processing equipment and a skilled technical team to achieve high-precision circuit processing and laminating, ensuring high quality and excellent electrical performance.
- Multi-Layer Structure Design: We can design and manufacture complex multi-layer IC package substrates according to customer requirements, meeting the needs of various electronic devices.
- High-Quality After-Sales Service: We provide comprehensive after-sales service to ensure that customers receive timely technical support and solutions during use.
- カスタマイズサービス: We offer customized IC package substrate design and manufacturing services based on specific customer needs, ensuring that the products fully meet application requirements.
Through continuous technological innovation and strict quality control, our IC package substrates have gained wide recognition in the market and are widely used in communications, 自動車, インダストリアル, and other fields. If you have a need for IC package substrates, お問い合わせください, and we will be committed to providing you with high-quality products and services.
まとめ, 材料選択かどうか, 加工技術, またはアフターサービス, our company is capable of producing high-quality IC package substrates to meet the needs of various applications.
は何ですか 7 優れたカスタマーサービスの品質?
優れた顧客サービスは、顧客との強固な関係を築き、顧客の満足を確保するために不可欠です. ここでは、優れたカスタマーサービスの7つの重要な資質をご紹介します:
- 共感: Understanding and sharing the feelings of customers is crucial. Empathetic customer service representatives can connect with customers on a personal level, making them feel valued and understood. This helps in resolving issues effectively and building trust.
- 応答: Timely responses to customer inquiries and issues are critical. Good customer service involves being prompt and efficient in addressing concerns, answering questions, and providing solutions. Quick responses show that the company values the customer’s time and is dedicated to providing support.
- コミュニケーションスキル: Clear and effective communication is fundamental. This includes listening carefully to customers, providing accurate information, and explaining solutions in a way that is easy to understand. Good communication helps prevent misunderstandings and ensures that customers feel heard and informed.
- 辛抱: お客様との付き合い方, especially those who are frustrated or upset, 忍耐力が必要. カスタマーサービス担当者は、落ち着いて落ち着いている必要があります, providing thoughtful responses and taking the time to thoroughly address the customer’s concerns.
- Knowledgeable: A deep understanding of the products or services offered is essential for providing effective support. Knowledgeable customer service representatives can answer questions accurately, provide relevant information, and offer appropriate solutions to problems.
- Attentiveness: Paying close attention to customer needs and details is important for delivering high-quality service. Attentive service involves focusing on the customer’s specific concerns, anticipating their needs, and offering personalized assistance.
- フォローアップ: Ensuring that customer issues are fully resolved and following up to confirm satisfaction demonstrates a commitment to excellent service. Follow-up shows that the company cares about the customer’s experience and is willing to go the extra mile to ensure their needs are met.
Incorporating these qualities into customer service practices can lead to increased customer satisfaction, 忠義, and positive word-of-mouth, ultimately contributing to the success of a business.
に関するFAQ IC Package Substrate
What is an IC package substrate?
An IC package substrate is a base material used to support and connect integrated circuits (ICの) to other components and circuits. It provides mechanical support and electrical connections between the IC and the external circuitry.
What materials are used for IC package substrates?
Common materials include fiberglass-reinforced epoxy resin (FR-4), ポリイミド (円周率), 陶芸 (such as aluminum oxide), and high-frequency materials. Each material has specific properties suited to different applications.
What are the benefits of using high-performance substrates?
High-performance substrates, such as those made from polyimide or ceramics, offer superior thermal management, 電気絶縁性, と信頼性, especially in high-frequency or high-power applications.
What factors affect the cost of IC package substrates?
Cost factors include the choice of materials, 設計の複雑さ, 製造数量, and additional features. Higher complexity and performance requirements typically lead to higher costs.
How are IC package substrates manufactured?
The manufacturing process involves material preparation, layering, 写真石版, 錬成, 鍍金, 堆積, pad formation, cutting, テスティング, 表面処理, そして最終組み立て.
What is the difference between a single-layer and a multi-layer substrate?
A single-layer substrate has one layer of material, while a multi-layer substrate consists of multiple layers stacked and laminated together. Multi-layer substrates are used for more complex circuits requiring higher density interconnections.