Flip-Chip Substrate Manufacturer
Flip-Chip Substrate Manufacturer,Flip-chip substrates are advanced packaging solutions used in microelectronics to connect semiconductor devices directly to the substrate, enhancing performance and compactness. This technology involves flipping the chip so that its active side faces the substrate, allowing for shorter interconnects and improved signal integrity. Flip-chip substrates often feature high-density interconnects (HDIの) and fine-pitch bumps for precise alignment and electrical connection. They are designed to handle high-speed data transmission and minimize parasitic effects, making them ideal for applications in CPUs, GPUの, and high-performance integrated circuits. Flip-chip substrates contribute to miniaturization and efficiency in modern electronic devices.
What is an RF/Microwave PCB?
An RF/Microwave PCB (プリント回路基板) is a specialized type of circuit board designed to handle high-frequency signals typically ranging from RF (無線周波数) to microwave frequencies. These boards are crucial in applications such as telecommunications, レーダーシステム, satellite communications, and wireless networking.
Key features of RF/Microwave PCBs include:
- 材料の選択: They use materials with high dielectric constants and low loss tangents, such as PTFE (ポリテトラフルオロ エチレン) またはセラミックス, to minimize signal loss and maintain signal integrity at high frequencies.
- Trace Geometry: RF/Microwave PCBs require precise control over trace widths, lengths, and spacing to match impedance requirements and minimize signal reflections.
- コンポーネントの配置: Components are placed strategically to minimize parasitic effects and maintain signal integrity. This includes careful consideration of ground plane placement and via placement.
- Shielding: RF/Microwave circuits often require shielding to prevent electromagnetic interference (EMIの) and ensure the circuit operates correctly in its intended frequency range.
- 製造技術: Specialized manufacturing techniques such as controlled impedance routing, plated-through holes (PTH), および表面実装技術 (SMTの) are employed to meet the stringent requirements of high-frequency circuits.
- Testing and Validation: RF/Microwave PCBs undergo rigorous testing and validation procedures, including impedance testing, insertion loss measurements, and signal integrity analysis, to ensure they meet performance specifications.
全, RF/Microwave PCBs are designed with careful consideration of electrical properties, 料, and manufacturing techniques to ensure optimal performance in high-frequency applications where signal integrity and reliability are critical.
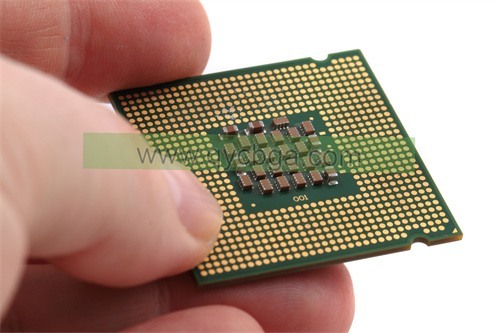
Flip-Chip Substrate Manufacturer
What are Flip-Chip Substrate Design Guidelines?
Flip-chip substrate design guidelines refer to specific principles and practices used in the design of substrates for flip-chip packaging technology. Flip-chip technology involves directly mounting semiconductor chips onto substrates or carriers, allowing for more compact and efficient electronic devices. Here are some key design guidelines for flip-chip substrates:
- Dielectric Material Selection: Choose substrate materials with appropriate dielectric properties that support high-frequency signals and minimize signal loss. 一般的な材料にはFR-4が含まれます (for lower frequencies) and higher-performance materials like BT (ビスマレイミドトリアジン) or PTFE (ポリテトラフルオロ エチレン) for higher frequencies.
- レイヤースタックアップ設計: Design the substrate’s layer stackup carefully to achieve controlled impedance matching for signal integrity. This involves placing signal layers adjacent to ground planes and ensuring controlled spacing between layers to minimize crosstalk and interference.
- Pad and Trace Design: Optimize the pad and trace dimensions to match the requirements of the flip-chip bump size and pitch. Ensure the pads are large enough to accommodate the bumps and provide sufficient electrical contact area.
- Via Design: Use blind or buried vias whenever possible to reduce signal transmission path lengths and minimize parasitic capacitance and inductance. Vias should be placed strategically to maintain signal integrity and thermal management.
- サーマルマネジメント: Incorporate thermal vias and thermal pads to efficiently dissipate heat generated by the flip-chip components. Proper thermal management helps prevent overheating and ensures reliable operation of the device.
- Alignment and Assembly: Design alignment features on the substrate to ensure accurate placement and alignment of the flip-chip components during assembly. This helps in achieving reliable electrical connections and mechanical stability.
- Substrate Material Properties: Consider material properties such as coefficient of thermal expansion (CTEの), 熱伝導率, and moisture absorption characteristics. These properties affect the reliability and performance of the flip-chip assembly over its operational lifetime.
- Testing and Validation: Implement testing and validation procedures to ensure the substrate design meets performance specifications, including electrical testing for impedance matching, シグナルインテグリティ, and reliability testing under thermal stress conditions.
これらのガイドラインに従う, designers can create flip-chip substrates that meet the stringent requirements of modern electronic devices, including high-speed communication systems, マイクロプロセッサ, and high-density integrated circuits. Each guideline plays a crucial role in ensuring the overall performance, 確実, and manufacturability of flip-chip assemblies.
What is the Flip-Chip Substrate Fabrication Process?
The flip-chip substrate fabrication process involves several key steps to create a substrate suitable for flip-chip packaging technology. Here’s an overview of the typical fabrication process:
- 基板材料選定:Choose a suitable substrate material based on the specific requirements of the flip-chip application. Common substrate materials include FR-4 (for lower frequencies), BTの (ビスマレイミドトリアジン), or PTFE (ポリテトラフルオロ エチレン) for higher frequencies. The material should have appropriate dielectric properties, 熱伝導率, と寸法安定性.
- レイヤースタックアップ設計:Design the layer stackup of the substrate based on the electrical and thermal requirements. 通常, the stackup includes signal layers, ground layers, and power planes. Signal layers are sandwiched between ground and power planes to provide controlled impedance and effective heat dissipation.
- Circuit Design and Layout:Create the circuit design and layout using computer-aided design (CAD) tools. This involves placing components, routing traces, and designing pads according to flip-chip bump pitch and size requirements. Special attention is given to impedance control, シグナルインテグリティ, and minimizing electromagnetic interference (EMIの).
- リソグラフィーとエッチング:Use photolithography and etching processes to define the circuit patterns on each layer of the substrate. フォトレジスト材料を基板に塗布します, exposed to UV light through a mask, and then developed to transfer the pattern onto the substrate surface. Etching removes unwanted copper or other conductive material to form the circuit traces.
- ビアフォーメーション:ビアを作成 (plated-through holes) to establish electrical connections between different layers of the substrate. Vias can be formed using mechanical drilling or laser drilling processes, followed by electroplating to deposit conductive material inside the vias.
- 表面仕上げ:Apply a surface finish to protect the exposed copper traces and pads from oxidation and to facilitate soldering during component assembly. Common surface finishes include solder mask (for insulation and solder dam), エニグ (無電解ニッケル浸漬金), ハスレ (熱風はんだレベリング), or OSP (Organic Solderability Preservative).
- Quality Assurance:Conduct rigorous quality assurance tests to verify the substrate’s electrical performance, 寸法精度, and reliability under various environmental conditions. Tests may include impedance testing, solderability testing, サーマルサイクル, and mechanical stress testing.
- 最終検査と梱包:Inspect the fabricated substrates for defects and ensure they meet the required specifications. Substrates are then packaged and prepared for shipment to semiconductor assembly and testing facilities (ATFs) where flip-chip components will be mounted.
次の手順に従います, manufacturers can produce flip-chip substrates that meet the high-performance and reliability demands of modern electronic devices. Each stage of the fabrication process is critical in ensuring the substrate’s functionality, electrical integrity, and compatibility with flip-chip packaging technology.
How do you manufacture a Flip-Chip Substrate?
The flip-chip substrate fabrication process involves several precise steps to create substrates that can accommodate flip-chip packaging technology effectively. Here’s an overview of the typical fabrication process:
- 材料の選択: Choose a substrate material based on the application requirements, such as FR-4 for lower frequencies or higher-performance materials like BT (ビスマレイミドトリアジン) or PTFE (ポリテトラフルオロ エチレン) for higher frequencies and better electrical performance.
- レイヤースタックアップ設計: Design the substrate’s layer stackup considering the number and arrangement of signal, 力, と地表層. This design aims to achieve controlled impedance matching and to provide a stable platform for the flip-chip bonding process.
- Circuit Design and Layout: Create the circuit design and layout using specialized CAD (Computer-Aided Design) tools. Pay attention to trace widths, spacing, and via placements to ensure signal integrity and impedance control.
- 基質調製: Begin with the preparation of the base substrate material. This involves cutting the substrate to the desired size and shape, and preparing the surfaces for subsequent processing steps.
- Copper Deposition:Apply a layer of copper to the substrate surfaces using techniques such as electroplating or sputtering. This copper layer will form the conductive traces and pads on the substrate.
- エッチング: Use photolithography and etching processes to define the copper traces and pads according to the circuit design. Photolithography involves applying a photoresist layer, exposing it to UV light through a mask that defines the circuit pattern, and then developing it to create a patterned resist. The exposed copper is then etched away using an appropriate etchant.
- ビアフォーメーション: ビアを作成 (plated-through holes) in the substrate to establish electrical connections between different layers. Vias can be formed using mechanical drilling, laser drilling, or chemical etching followed by copper plating.
- 表面仕上げ: Apply a surface finish to the copper traces and pads to ensure solderability and prevent oxidation. 一般的な表面仕上げには、無電解ニッケル浸漬金が含まれます (エニグ), 有機はんだ付け性防腐剤 (OSPの), and electroplated nickel/gold.
- ソルダーマスクアプリケーション: Apply solder mask over the substrate, leaving openings (exposed pads) for the electrical contacts. The solder mask protects the underlying copper traces from environmental exposure and helps define the areas for solder attachment during flip-chip assembly.
- 最終検査と試験:Conduct thorough inspection and testing of the fabricated substrate to ensure it meets design specifications. これには、目視検査が含まれる場合があります, electrical testing for continuity and impedance, and dimensional checks.
- Quality Assurance: Implement quality assurance processes throughout the fabrication process to ensure consistency and reliability of the flip-chip substrates.
By following these steps meticulously, manufacturers can produce flip-chip substrates that provide reliable electrical connections, optimal signal integrity, 効率的な熱放散, meeting the demands of high-performance electronic applications. Each stage in the process plays a crucial role in achieving the desired substrate quality and functionality.
How much should a Flip-Chip Substrate cost?
The cost of a flip-chip substrate can vary widely depending on several factors:
- 材料: The type and quality of substrate material used (例えば。, FR-4, BTの, PTFE製) significantly impact the cost. Higher-performance materials designed for RF/microwave applications or high-speed digital circuits generally cost more than standard FR-4.
- Complexity: 基板設計の複雑さ, レイヤー数を含む, トレースとビアの密度, and the precision required for impedance control, all influence the cost. More complex designs typically incur higher fabrication costs due to increased manufacturing complexity and longer processing times.
- Size and Quantity: The size of the substrate and the volume of production also play a role. Larger substrates or smaller production runs may cost more per unit due to economies of scale in manufacturing.
- 表面仕上げと特徴: Additional features such as specific surface finishes (例えば。, エニグ, OSPの), specialized via structures (blind vias, 埋もれたビア), and the inclusion of advanced technologies (such as embedded passives or heat dissipation structures) can increase costs.
- 製造プロセス: Different manufacturing processes (例えば。, laser drilling vs. mechanical drilling for vias) and the use of advanced equipment and techniques can affect costs.
- サプライヤーとロケーション:Costs can also vary based on the supplier’s location, expertise, and quality standards. Suppliers with advanced capabilities and certifications (例えば。, ISO standards for quality management) may charge higher prices.
To provide a rough estimate, flip-chip substrates can range in cost from a few dollars for simpler designs in standard materials to tens or even hundreds of dollars for more complex designs with high-performance materials and advanced features. It’s essential for designers and manufacturers to balance cost considerations with the performance requirements and reliability expectations of the substrate for the specific application.
What is Flip-Chip Substrate base material?
The base material used for flip-chip substrates can vary depending on the specific requirements of the application. Here are some common types of base materials used:
- FR-4 (難燃 4): FR-4 is a widely used substrate material for general-purpose electronics. It is composed of a woven fiberglass cloth impregnated with an epoxy resin. FR-4 is cost-effective and provides good mechanical strength and dimensional stability. It is suitable for lower frequency applications and standard digital circuits.
- BTの (ビスマレイミドトリアジン): BT is a high-performance substrate material known for its excellent electrical properties at high frequencies. It offers lower dielectric loss and better thermal stability compared to FR-4. BT is commonly used in applications requiring high-speed digital signals and RF/microwave circuits.
- PTFE製 (ポリテトラフルオロ エチレン): PTFE-based materials, such as Rogers RO4000 series, are highly specialized substrates known for their low dielectric constant (εr) and low loss tangent (tan δ). These properties make PTFE substrates suitable for very high-frequency applications (microwave and millimeter-wave frequencies) where signal integrity and low insertion loss are critical.
- セラミック基板:アルミナなどの窯業 (Al2O3) または窒化アルミニウム (AlNの) are used in applications requiring superior thermal management and high electrical insulation. Ceramic substrates offer excellent thermal conductivity and are suitable for high-power RF applications and semiconductor packaging where heat dissipation is crucial.
- Metal Core PCB (MCPCB): MCPCBs use a metal core (typically aluminum or copper) as the base material for enhanced thermal management. These substrates are used in LED applications and other high-power electronic devices where efficient heat dissipation is essential.
The choice of base material depends on factors such as the operating frequency, signal integrity requirements, 熱管理のニーズ, 機械的強度, とコストに関する考慮事項. Designers select the substrate material that best balances these requirements to achieve optimal performance and reliability in flip-chip applications.
Which company makes Flip-Chip Substrates?
There are many companies with rich experience and technology in the production of Flip-Chip Substrates. Globally, well-known companies such as Intel from the United States, TSMC from Taiwan, Samsung Electronics from South Korea, and Infineon from Germany have excellent performances in this field.
Flip-Chip Substrates are widely used in the electronics industry, including high-performance microprocessors, 通信機器, radio frequency devices, and high-frequency RF circuits. These companies ensure the performance and reliability of Flip-Chip Substrates through the use of advanced manufacturing processes and materials.
In our company, we also have the capability and experience to produce Flip-Chip Substrates. We possess advanced production equipment and a skilled technical team capable of customizing various types of Flip-Chip Substrates according to customer requirements. Our manufacturing process strictly adheres to international standards and employs the latest CAD design tools and CAM processing technologies to ensure product quality and precision.
Our Flip-Chip Substrates can be customized for various application needs, including but not limited to:
– High-frequency RF/microwave applications: Using low-loss materials and precise circuit layouts to ensure signal integrity and minimal insertion loss.
– High-speed digital signal transmission: Optimizing signal paths and controlling impedance to support high-speed data transmission and signal stability.
– High-power semiconductor packaging: Using excellent thermal materials and structural design to effectively manage device heat and temperature distribution.
Our manufacturing team is experienced in providing customized solutions based on customer design requirements and technical specifications. We are committed to delivering high-performance, highly reliable Flip-Chip Substrates to meet the evolving demands of the electronics market.
By choosing our company as your partner, you will gain access to professional technical support, high-quality products, and efficient production capabilities, enabling you to achieve technological innovation and competitive advantage in the market.
は何ですか 7 優れたカスタマーサービスの品質?
Good customer service is characterized by several key qualities that contribute to positive interactions and relationships between businesses and their customers. ここでは、7つの重要な資質をご紹介します:
- 応答:Customers appreciate timely responses to their inquiries, 懸念, or issues. Good customer service involves being prompt and efficient in addressing customer needs, whether through phone calls, emails, live chats, or in-person interactions.
- 共感: Empathy is crucial in understanding and acknowledging the customer’s feelings and concerns. Good customer service representatives listen actively, show empathy, and demonstrate a genuine desire to help resolve problems or answer questions.
- 辛抱:Patience is vital, especially when dealing with frustrated or upset customers. Good customer service involves remaining calm, composed, and patient while addressing customer issues or complaints, even if they require time and effort to resolve.
- 知識能力: Customers expect service representatives to have sufficient knowledge about the products or services offered. Good customer service involves training and equipping staff with the necessary information and resources to provide accurate and helpful assistance.
- プロ 意識: Professionalism in customer service means maintaining a courteous and respectful demeanor at all times. This includes using appropriate language, tone of voice, and behavior that reflects positively on the company and enhances the customer’s experience.
- 問題解決スキル: Effective customer service requires the ability to analyze problems, identify solutions, and take appropriate actions to resolve issues promptly. Good service representatives are proactive in finding solutions that meet the customer’s needs and expectations.
- パーソナル 化: Providing personalized service involves recognizing and addressing customers as individuals with unique preferences and histories. Good customer service includes tailoring interactions and solutions to meet the specific needs and preferences of each customer whenever possible.
By focusing on these qualities, businesses can build strong customer relationships, ロイヤリティを育む, and enhance their reputation for delivering exceptional customer service experiences.
よくあるご質問(FAQ)
What is a flip-chip substrate?
A flip-chip substrate is a specialized type of printed circuit board (プリント基板) or substrate used in semiconductor packaging technology. It provides a platform for mounting and interconnecting semiconductor chips using flip-chip bonding techniques.
What materials are used in flip-chip substrates?
Flip-chip substrates can be made from various materials depending on the application requirements. 一般的な材料にはFR-4が含まれます (for general-purpose applications), BTの (ビスマレイミドトリアジン) for higher frequencies, PTFE製 (ポリテトラフルオロ エチレン) for low loss at high frequencies, とセラミックス (アルミナや窒化アルミニウムなど) for high thermal conductivity.
How are flip-chip substrates manufactured?
The manufacturing process for flip-chip substrates involves several steps, including material selection, レイヤースタックアップ設計, circuit layout, copper deposition, エッチング, ビアフォーメーション, 表面仕上げアプリケーション, solder mask deposition, and final inspection/testing. Specialized equipment and processes are used to ensure precise alignment and interconnection of semiconductor chips.
How do flip-chip substrates compare to other packaging technologies?
Flip-chip substrates offer advantages over traditional wire bonding methods in terms of electrical performance, size reduction, と熱管理. They provide more reliable interconnections and support higher frequencies, making them suitable for demanding applications in modern electronics.