味の素(ABFの) パッケージ基板メーカー
味の素(ABFの) パッケージ基板メーカー,味の素 (ABFの) Package Substrate is an advanced packaging substrate material developed by Ajinomoto Co., Inc. It is primarily used in semiconductor packaging, particularly for high-performance and high-density integrated circuits. The ABF substrate is renowned for its excellent electrical properties and thermal stability, effectively reducing signal transmission delays and electromagnetic interference. Its unique low thermal expansion coefficient and high mechanical strength make it an ideal choice for high-reliability electronic devices. In the modern electronics industry, ABF substrates are widely used in servers, storage devices, ネットワーク機器, および家庭用電化製品, serving as a key material for enhancing the performance and reliability of electronic products.
What is Ajinomoto (ABFの) パッケージ基板?
味の素ビルドアップフィルム (ABFの) package substrate is a critical component in the construction of advanced semiconductor devices. It’s a type of high-density interconnect (HDIの) 半導体パッケージに使用される基板. ABF substrates provide a platform for mounting and connecting semiconductor chips, facilitating the flow of electrical signals within the device.
These substrates are made using thin layers of polymer films coated with a conductive material, typically copper, to create intricate circuit patterns. The use of ABF substrates allows for the creation of densely packed circuits with fine pitch features, enabling the integration of more components in a smaller footprint.
ABF substrates offer several advantages over traditional substrates, such as better signal integrity, 低消費電力, and improved thermal performance. They are also highly reliable, with excellent mechanical properties that withstand the stresses of semiconductor manufacturing processes and device operation.
まとめ, 味の素ビルドアップフィルム (ABFの) package substrates are essential components in the fabrication of advanced semiconductor devices, providing a foundation for high-performance and compact electronic systems.
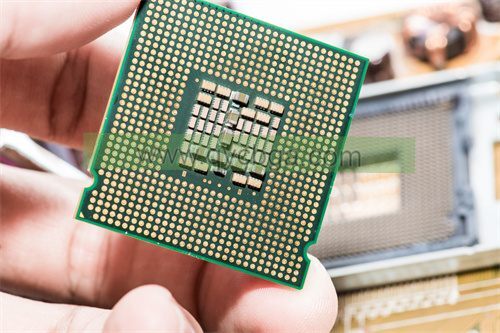
味の素(ABFの) パッケージ基板メーカー
What are Ajinomoto (ABFの) Package Substrate Design Guidelines?
Designing with 味の素ビルドアップフィルム (ABFの) パッケージ基板 involves adhering to specific guidelines to ensure optimal performance and reliability. While the exact guidelines may vary depending on the specific application and manufacturing processes, some common design principles include:
- レイヤースタックアップ設計: ABF substrates consist of multiple layers of polymer films and conductive traces. Designers need to carefully plan the layer stackup to achieve the desired electrical and mechanical properties. This includes determining the number of signal, 力, と地表層, as well as the thickness and material properties of each layer.
- シグナルインテグリティに関する考慮事項: High-speed signal integrity is critical in modern electronic devices. Designers must minimize signal degradation due to impedance mismatches, クロストーク, and transmission line effects. This may involve careful routing of signal traces, controlled impedance design, and placement of decoupling capacitors.
- サーマルマネジメント: Efficient heat dissipation is essential to prevent overheating and ensure the reliability of semiconductor devices. Designers should incorporate thermal vias, サーマルパッド, and other thermal management techniques to facilitate heat transfer away from critical components.
- コンポーネントの配置: Proper placement of components on the substrate can significantly impact electrical performance and manufacturability. Designers should consider factors such as signal routing, thermal coupling, and accessibility for assembly and testing.
- Manufacturability and Yield: Designs should be optimized for manufacturability to ensure high yield and low production costs. This may involve minimizing the use of complex features, such as blind vias and microvias, and adhering to design rules specified by the substrate manufacturer.
- 信頼性と耐久性: Electronic devices must withstand various environmental stresses, 温度サイクルを含む, 機械的衝撃, and moisture exposure. Designers should design for reliability by selecting appropriate materials, avoiding sharp corners and stress concentrations, and performing thorough simulation and testing.
- Compliance with Standards: Depending on the application, designers may need to ensure compliance with industry standards and regulations, such as JEDEC specifications for semiconductor packaging or IPC guidelines for PCB design.
By following these design guidelines, engineers can create robust and high-performance electronic devices using Ajinomoto Build-up Film (ABFの) パッケージ基板. Collaboration with substrate manufacturers and simulation tools can also help validate designs and optimize performance.
What is the Ajinomoto (ABFの) Package Substrate Fabrication Process?
の製造プロセス 味の素ビルドアップフィルム (ABFの) パッケージ基板 involves several steps to create the intricate circuit patterns and structures required for semiconductor packaging. While specific details may vary depending on the manufacturer and the desired substrate specifications, a typical fabrication process includes the following stages:
- Preparation of Base Material:The fabrication process begins with the preparation of the base material, typically a thin polymer film. The polymer film serves as the substrate upon which the circuit patterns will be formed. It is essential to ensure that the base material has the necessary properties, such as dimensional stability and thermal resistance, to withstand subsequent processing steps.
- Surface Treatment: The surface of the base material is treated to improve adhesion and promote the deposition of conductive materials in later steps. Surface treatments may include plasma cleaning, chemical etching, or the application of adhesion-promoting layers.
- 回路パターニング:Circuit patterns are formed on the base material using photolithography or similar patterning techniques. A photoresist material is applied to the surface of the base material, exposed to ultraviolet light through a photomask containing the desired circuit pattern, and developed to remove the unexposed regions. The exposed areas of the base material are then subjected to etching to remove the underlying material and define the conductive traces and vias.
- Conductive Material Deposition: パターニング後, conductive materials such as copper are deposited onto the substrate surface to form the circuit traces and vias. This may be achieved through techniques such as sputtering, 電気 めっき, または化学蒸着 (CVD検出器). Multiple layers of conductive materials may be deposited to create complex multilayered structures.
- Dielectric Layer Formation: Dielectric layers are deposited between the conductive layers to insulate them and provide electrical isolation. The dielectric material may be applied using spin coating, 化学蒸着 (CVD検出器), or other deposition techniques. After deposition, the dielectric material is cured to achieve the desired mechanical and electrical properties.
- ビアフォーメーション: Vias are openings in the dielectric layers that allow for electrical connections between different conductive layers. Vias are formed by drilling or laser ablation, followed by the deposition of conductive material to line the vias and establish electrical continuity between adjacent layers.
- 表面仕上げ:The substrate surface may undergo additional treatments to improve solderability, corrosion resistance, and wire bonding capabilities. Surface finishing techniques may include applying solder mask layers, surface metallization, or immersion plating.
- テストと検査: After fabrication, the substrates undergo rigorous testing and inspection to ensure they meet the required specifications for electrical performance, 寸法精度, と信頼性. Testing may include continuity testing, impedance measurements, 欠陥の目視検査.
By following these fabrication steps, manufacturers can produce Ajinomoto Build-up Film (ABFの) package substrates with the precise circuit patterns and electrical properties required for advanced semiconductor packaging applications.
How do you manufacture Ajinomoto (ABFの) パッケージ基板?
Manufacturing Ajinomoto Build-up Film (ABFの) package substrates involves a series of intricate processes to create the necessary circuitry and structural features required for semiconductor packaging. ここでは、製造プロセスの一般的な概要を示します:
- 基質調製: The manufacturing process begins with the preparation of the base material, typically a thin polymer film. This film serves as the foundation upon which the circuit patterns will be formed. The substrate material is chosen based on factors such as thermal stability, 寸法精度, and dielectric properties.
- Surface Treatment: The surface of the substrate material undergoes various treatments to enhance adhesion and facilitate the deposition of conductive and dielectric materials in subsequent steps. Surface treatments may include plasma cleaning, chemical etching, and the application of adhesion-promoting layers.
- 回路パターニング: Circuit patterns are formed on the substrate material using photolithography or similar patterning techniques. A photoresist material is applied to the substrate surface, exposed to ultraviolet light through a photomask containing the desired circuit pattern, and developed to remove the unexposed regions. The exposed areas of the substrate are then subjected to etching to define the conductive traces and vias.
- Conductive Material Deposition:パターニング後, conductive materials such as copper are deposited onto the substrate surface to form the circuit traces and vias. This may be achieved through techniques such as sputtering, 電気 めっき, または化学蒸着 (CVD検出器). Multiple layers of conductive materials may be deposited to create complex multilayered structures.
- Dielectric Layer Formation: Dielectric layers are deposited between the conductive layers to insulate them and provide electrical isolation. The dielectric material may be applied using spin coating, CVD検出器, or other deposition techniques. After deposition, the dielectric material is cured to achieve the desired mechanical and electrical properties.
- ビアフォーメーション: Vias are openings in the dielectric layers that allow for electrical connections between different conductive layers. Vias are formed by drilling or laser ablation, followed by the deposition of conductive material to line the vias and establish electrical continuity between adjacent layers.
- 表面仕上げ: The substrate surface undergoes additional treatments to improve solderability, corrosion resistance, and wire bonding capabilities. Surface finishing techniques may include applying solder mask layers, surface metallization, or immersion plating.
- テストと検査: After manufacturing, the substrates undergo comprehensive testing and inspection to ensure they meet the required specifications for electrical performance, 寸法精度, と信頼性. Testing may include continuity testing, impedance measurements, 欠陥の目視検査.
By carefully following these manufacturing steps, producers can create Ajinomoto Build-up Film (ABFの) package substrates with the precise circuit patterns and electrical properties needed for advanced semiconductor packaging applications.
How much should Ajinomoto (ABFの) Package Substrate cost?
The cost of Ajinomoto Build-up Film (ABFの) パッケージの基材は、いくつかの要因によって大きく異なります, 含む:
- 素材の品質: The quality of the substrate materials, such as the polymer film, conductive materials, and dielectric layers, コストに影響を与える可能性があります. Higher quality materials may command a higher price due to better performance and reliability.
- 設計の複雑さ: 基板設計の複雑さ, レイヤー数を含む, circuit density, and feature size, can influence the manufacturing cost. More complex designs may require additional processing steps and higher precision, resulting in increased costs.
- 製造台数: The volume of substrates being produced can affect the unit cost. Higher production volumes typically lead to economies of scale, allowing manufacturers to spread fixed costs across a larger number of units and reduce per-unit costs.
- カスタマイズ要件: Customized features or specifications requested by the customer may incur additional costs. These could include special surface finishes, unique material formulations, or specific dimensional tolerances tailored to the application’s requirements.
- サプライヤーとロケーション:The choice of supplier and manufacturing location can impact costs due to differences in labor rates, overhead expenses, and shipping costs. Suppliers with advanced manufacturing capabilities or located in regions with lower production costs may offer more competitive pricing.
- 市場の需要: Market demand and supply dynamics can influence pricing. In periods of high demand or supply constraints, prices may increase due to limited availability or higher manufacturing costs.
- 追加サービス: Additional services such as design assistance, テスティング, and packaging may incur extra charges, 基板の全体的なコストに加算.
Given these variables, it’s challenging to provide a specific cost for Ajinomoto Build-up Film (ABFの) package substrates without knowing the exact specifications and requirements of a particular project. 通常, customers would need to request a quote from the manufacturer or supplier based on their specific needs and volume requirements.
What is Ajinomoto (ABFの) Package Substrate base material?
味の素ビルドアップフィルム (ABFの) package substrates typically use polymer films as the base material. These polymer films serve as the foundation upon which the circuit patterns and structures are built during the fabrication process. The choice of polymer material depends on various factors such as thermal stability, 寸法精度, dielectric properties, and compatibility with the manufacturing processes involved.
Common polymer materials used as base substrates for ABF package substrates include:
- ポリイミド (円周率): Polyimide films offer excellent thermal stability, 機械的強度, and chemical resistance, making them well-suited for high-temperature applications. They are commonly used in flexible and rigid-flex PCBs due to their flexibility and reliability.
- 液晶ポリマー (LCPの): LCP films exhibit low moisture absorption, 優れた寸法安定性, and high-frequency performance, making them ideal for high-speed and high-frequency applications. They are often used in advanced electronic packaging, especially in RF and microwave devices.
- ビスマレイミドトリアジン (BTの):BT resin films offer high thermal performance, 低誘電率, and good electrical insulation properties. They are commonly used in substrates for semiconductor packaging, especially in flip-chip and ball grid array (BGAの) パッケージ.
- エポキシ樹脂: Epoxy-based films provide good adhesion, 機械的強度, and chemical resistance, making them suitable for various electronic packaging applications. They are often used in multilayer PCBs and substrate materials for semiconductor devices.
These base materials can be further modified or treated to enhance specific properties such as adhesion, surface smoothness, and thermal conductivity, depending on the requirements of the application. The choice of base material plays a crucial role in determining the overall performance, 確実, and cost-effectiveness of ABF package substrates.
Which company makes Ajinomoto (ABFの) パッケージ基板?
味の素 (ABFの) Package Substrate is produced by Ajinomoto Co., Inc., a Japanese multinational corporation. As a global company, Ajinomoto operates in various sectors including food, 化学薬品, and pharmaceuticals. Specifically, the Electronic Materials Division of Ajinomoto is responsible for manufacturing ABF package substrates to meet the needs of the semiconductor packaging industry.
Ajinomoto is renowned for its high-quality products and advanced manufacturing technologies. Its ABF package substrates utilize state-of-the-art materials and processes, offering excellent electrical performance, 確実, and versatility. Through continuous research and technological innovation, the company continually enhances product quality and performance to meet customer demands for high-performance electronic packaging solutions.
Our company, equipped with advanced manufacturing equipment and technology, is also capable of producing Ajinomoto (ABFの) Package Substrates. We have an experienced team of engineers and quality management professionals who provide comprehensive services from design to production. We prioritize product quality and customer satisfaction, committed to delivering high-quality and reliable ABF package substrate products to our customers.
Our manufacturing processes adhere strictly to industry standards and quality management systems, ensuring product stability and consistency. We also offer customized solutions tailored to meet specific customer requirements, catering to diverse application needs. With the ability to adapt flexibly to market changes and customer demands, we strive to provide the most competitive products and services to our customers.
As a responsible and innovative company, we will continue our efforts to deliver superior and reliable ABF package substrate products to the electronics industry, creating greater value and success for our customers.
は何ですか 7 優れたカスタマーサービスの品質?
Good customer service is characterized by several key qualities that contribute to positive interactions and relationships between businesses and their customers. Here are seven qualities of good customer service:
- 応答: Good customer service involves being prompt and responsive to customer inquiries, requests, and concerns. Responding to customers in a timely manner demonstrates attentiveness and a commitment to addressing their needs efficiently.
- 共感: Empathy is the ability to understand and relate to the feelings and experiences of customers. Good customer service representatives demonstrate empathy by listening actively, acknowledging customer emotions, and showing genuine concern for their issues or challenges.
- プロ 意識: Professionalism entails conducting oneself with courtesy, 尊敬, and integrity in all customer interactions. Good customer service representatives maintain a professional demeanor, communicate clearly and professionally, and handle difficult situations calmly and effectively.
- 知識能力: Good customer service requires having a thorough understanding of the products, services, and policies offered by the business. Knowledgeable representatives can provide accurate information, answer customer questions confidently, and offer relevant solutions or recommendations.
- Flexibility: Flexibility is essential for adapting to diverse customer needs and preferences. Good customer service involves being flexible and accommodating, willing to tailor solutions or make exceptions when appropriate to meet customer requirements.
- Proactivity: Proactive customer service involves anticipating customer needs and addressing issues before they escalate. Good customer service representatives take initiative to identify potential problems, offer proactive assistance or guidance, and follow up to ensure customer satisfaction.
- Consistency:Consistency is key to building trust and loyalty with customers. Good customer service should be consistent across all channels and interactions, maintaining a high level of quality and reliability over time.
これらの資質を具現化することで、, businesses can deliver exceptional customer service experiences that foster customer satisfaction, 忠義, and advocacy.
よくあるご質問(FAQ)
What is Ajinomoto (ABFの) パッケージ基板?
味の素 (ABFの) Package Substrate is a type of high-density interconnect (HDIの) 半導体パッケージに使用される基板. It provides a platform for mounting and connecting semiconductor chips, facilitating the flow of electrical signals within electronic devices.
What are the advantages of using Ajinomoto (ABFの) パッケージ基板?
ABF substrates offer several advantages, including better signal integrity, 低消費電力, improved thermal performance, そして高い信頼性. They enable the integration of more components in a smaller footprint, making them suitable for compact electronic devices.
How is Ajinomoto (ABFの) パッケージ基板製造?
The manufacturing process for ABF package substrates involves several steps, 基質調製を含む, 表面処理, 回路パターニング, conductive material deposition, dielectric layer formation, ビアフォーメーション, 表面仕上げ, and testing/inspection. Each step is carefully executed to create the necessary circuit patterns and structures required for semiconductor packaging.
What are the design guidelines for Ajinomoto (ABFの) パッケージ基板?
Designing with ABF package substrates involves adhering to specific guidelines to ensure optimal performance and reliability. Guidelines may include considerations for layer stackup design, シグナルインテグリティ, サーマルマネジメント, コンポーネントの配置, 製造可能性, 確実, and compliance with standards.
Which company manufactures Ajinomoto (ABFの) パッケージ基板?
Ajinomoto Co., Inc., a Japanese multinational corporation, manufactures Ajinomoto (ABFの) パッケージ基板. The Electronic Materials Division of Ajinomoto is responsible for producing ABF package substrates to meet the needs of the semiconductor packaging industry.
What are the typical applications of Ajinomoto (ABFの) パッケージ基板?
ABF package substrates are used in a wide range of electronic devices, スマートフォンを含む, 錠剤, ラップトップ, 家電, 自動車用電子機器, and industrial equipment. They are particularly well-suited for applications requiring high-density, high-performance semiconductor packaging.