Ajinomoto GX92R Package Substrate Manufacturer
Ajinomoto GX92R Package Substrate Manufacturer,Ajinomoto GX92R package substrates are cutting-edge components used in semiconductor packaging, renowned for their exceptional reliability and performance. Crafted from advanced materials like FR-4, ポリイミド, またはセラミック, these substrates offer superior thermal conductivity, 電気絶縁性, そして機械安定性. Engineered to meet the stringent demands of modern electronics, GX92R substrates excel in high-speed and high-power applications, ensuring optimal signal integrity and thermal management. Their customizable nature allows for tailored solutions to specific customer requirements, including circuit design, 材料の選択, と表面仕上げ. From microprocessors to memory chips and power semiconductors, GX92R substrates accommodate various semiconductor devices across diverse industries such as telecommunications, 自動車, および家庭用電化製品. Whether it’s reducing package size and weight or enhancing EMI performance, Ajinomoto GX92R package substrates stand as the epitome of innovation and reliability in semiconductor packaging.
What is the Ajinomoto GX92R Package Substrate?
Ajinomoto GX92R is a high-performance package substrate commonly used in the manufacturing of electronic products. Produced by the globally renowned chemical company Ajinomoto Fine-Techno Co., Inc., this package substrate is renowned for its quality and performance within the industry.
The Ajinomoto GX92R package substrate utilizes advanced materials and processes to ensure superior mechanical, 熱の, and electrical performance. One of its primary materials is glass fiber-reinforced epoxy resin, which offers excellent mechanical strength and thermal stability, maintaining consistent performance under various environmental conditions. かつ, Ajinomoto GX92R employs highly pure copper foil as the conductive layer, ensuring the stability and reliability of the circuit.
Ajinomoto GX92R package substrate features an extremely low coefficient of thermal expansion and excellent dimensional stability, meaning it is less prone to deformation or stress damage under temperature changes or mechanical stress, ensuring the stable operation of electronic devices. その上, the substrate exhibits excellent heat resistance, allowing it to operate for extended periods in high-temperature environments without degradation.
In electronic product manufacturing, Ajinomoto GX92R package substrate finds widespread application in high-end products such as smartphones, 錠剤, デジタルカメラ, その他. Its outstanding performance and reliability make it a preferred material for many electronic device manufacturers.
全, Ajinomoto GX92R package substrate occupies a significant position in the electronics industry due to its high performance, stability, と信頼性, providing a solid foundation for the manufacturing of various electronic devices.
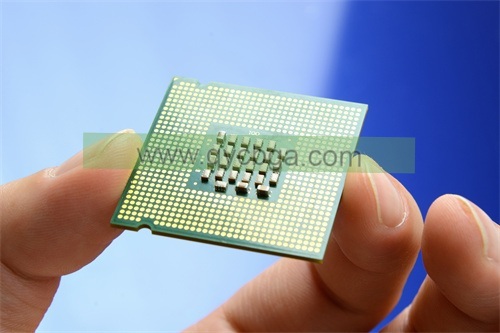
Ajinomoto GX92R package substrate Manufacturer
What are the Ajinomoto GX92R Package Substrate Design Guidelines?
The Ajinomoto GX92R package substrate design guidelines are crucial for ensuring the optimal performance and reliability of the GX92R semiconductor package. These guidelines encompass various aspects of substrate design, including material selection, layout considerations, routing strategies, and thermal management techniques. Here’s an expanded explanation:
- 材料の選択: The choice of substrate material is critical for achieving desired electrical, 熱の, および機械的特性. Guidelines may specify the use of high-performance materials such as FR-4, ポリイミド, or ceramic substrates depending on the application requirements.
- レイアウトに関する考慮事項: Proper layout design is essential to minimize signal interference, クロストーク, および電磁干渉 (EMIの). Guidelines may include recommendations for component placement, 信号ルーティング, 配電, and ground plane allocation to optimize signal integrity and minimize noise.
- Routing Strategies: Efficient routing of signal traces and power lines is crucial for minimizing signal distortion, インピーダンスの不一致, and power distribution issues. Guidelines may provide recommendations for trace width, spacing, インピーダンス整合, and signal via placement to ensure reliable signal transmission and power delivery.
- サーマルマネジメント:Effective thermal management is essential for preventing overheating and ensuring the long-term reliability of the semiconductor package. Guidelines may include recommendations for thermal vias, ヒートシンク, サーマルパッド, and thermal interface materials to dissipate heat efficiently and maintain optimal operating temperatures.
- 電気的性能: The substrate design should meet specified electrical performance criteria, such as impedance control, シグナルインテグリティ, and power delivery requirements. Guidelines may include design rules for impedance matching, 信号の終了, and power distribution network design to achieve desired electrical performance metrics.
- 信頼性に関する考慮事項: The substrate design should address reliability concerns such as mechanical stress, solder joint fatigue, and thermal cycling effects. Guidelines may include recommendations for substrate thickness, material properties, ソルダーマスク設計, and via placement to enhance the reliability and durability of the semiconductor package.
- 製造可能性: The substrate design should be manufacturable with high yield and low cost. Guidelines may include design rules for manufacturability, such as minimum feature size, ソルダーマスク登録, and pad layout to facilitate the fabrication process and ensure consistent quality.
By adhering to the Ajinomoto GX92R package substrate design guidelines, semiconductor manufacturers can optimize the performance, 確実, and manufacturability of their products, ultimately enhancing customer satisfaction and market competitiveness.
What is the Ajinomoto GX92R Package Substrate Fabrication Process?
The fabrication process for the Ajinomoto GX92R package substrate involves several steps to create a high-quality substrate that meets the requirements for electrical performance, 確実, と製造可能性. While specific details may vary depending on the manufacturing facility and technology used, here is a generalized overview of the fabrication process:
- 基板材料の準備: The process begins with preparing the substrate material, which is typically a high-performance material such as FR-4, ポリイミド, またはセラミック. The substrate material is sourced and inspected to ensure it meets the required specifications for thickness, 誘電率, 熱伝導率, および機械的特性.
- Substrate Cleaning and Surface Treatment: The substrate material undergoes a thorough cleaning process to remove any contaminants or impurities that could affect the adhesion or quality of subsequent layers. Surface treatment techniques such as plasma treatment or chemical etching may be employed to modify the surface properties and improve adhesion.
- レイヤーデポジション: The substrate undergoes a series of layer deposition processes to create the various functional layers required for the package substrate. This may include depositing conductive layers (銅など) for signal traces and power planes, dielectric layers for insulation, and protective layers (such as solder mask) to define the circuitry and protect against environmental factors.
- リソグラフィーとエッチング: Photolithography techniques are used to pattern the conductive and dielectric layers according to the design specifications. A photoresist is applied to the substrate surface, exposed to UV light through a mask, and then developed to selectively remove the unwanted material. エッチングプロセス, such as chemical etching or plasma etching, are then used to selectively remove the exposed material and define the circuitry.
- ビアフォーメーション: Vias are small holes drilled or etched through the substrate to create electrical connections between different layers of the substrate. Via formation typically involves drilling, レーザーアブレーション, or plasma etching followed by metallization to deposit conductive material (銅など) inside the vias to facilitate electrical connections.
- 表面仕上げ: Surface finish processes are applied to the substrate to protect the exposed copper traces, improve solderability, and enhance reliability. Common surface finish options include hot air solder leveling (ハスレ), 無電解ニッケル浸漬金 (エニグ), 有機はんだ付け性防腐剤 (OSPの).
- Quality Control and Testing: Throughout the fabrication process, rigorous quality control measures are implemented to ensure the substrate meets the required specifications for dimensional accuracy, layer thickness, 電気的性能, と信頼性. Various testing techniques, including visual inspection, 電気試験, 信頼性試験, may be performed to validate the quality of the substrate.
- 最終検査と梱包: Once the fabrication process is complete, the substrate undergoes final inspection to verify that all specifications have been met and that it is free from defects. The substrates are then packaged and prepared for shipment to semiconductor assembly facilities for further processing.
By following a well-defined fabrication process, manufacturers can produce Ajinomoto GX92R package substrates with consistent quality, パフォーマンス, and reliability to meet the demanding requirements of modern semiconductor packaging applications.
How do you manufacture an Ajinomoto GX92R Package Substrate?
Manufacturing an Ajinomoto GX92R package substrate involves several key steps to produce a high-quality substrate suitable for semiconductor packaging applications. ここでは、一般的な製造プロセスの概要を示します:
- 基板材料選定: The process begins with selecting the appropriate substrate material based on the specific requirements of the application. Ajinomoto GX92R package substrates can be made from materials such as FR-4 (epoxy resin), ポリイミド, またはセラミック, depending on factors such as electrical performance, 熱伝導率, とコストに関する考慮事項.
- 基質調製: The selected substrate material is prepared for processing by cutting it to the desired size and shape. The substrate may undergo surface cleaning and treatment to remove contaminants and improve adhesion for subsequent processing steps.
- Circuit Design and Layout: The circuit design for the GX92R package substrate is created based on the requirements of the semiconductor device it will accommodate. これには、コンポーネントの配置の決定が含まれます, routing of signal traces, allocation of power and ground planes, and placement of vias for interconnections.
- Photoresist Application: A layer of photoresist is applied to the substrate surface using techniques such as spin coating or screen printing. The photoresist serves as a mask for subsequent patterning steps.
- Exposure and Development: The photoresist is exposed to ultraviolet (紫外線) 所望の回路パターンを含むフォトマスクを通した光. This exposure selectively alters the chemical properties of the photoresist. The substrate is then developed to remove the unexposed photoresist, leaving behind the patterned areas.
- エッチング: Chemical etching or plasma etching is used to selectively remove the substrate material from the areas not protected by the patterned photoresist. This creates the desired circuit pattern on the substrate surface, including the conductive traces, ビア, and pads.
- メタライゼーション:Metal deposition techniques such as sputtering or electroplating are used to deposit thin layers of conductive material, typically copper, onto the patterned substrate surface. This forms the conductive traces, ビア, and pads required for electrical connections.
- 表面仕上げ: Surface finish processes are applied to the substrate to protect the exposed metal surfaces, improve solderability, and enhance reliability. Common surface finish options include hot air solder leveling (ハスレ), 無電解ニッケル浸漬金 (エニグ), 有機はんだ付け性防腐剤 (OSPの).
- 品質管理: 製造プロセス全体を通じて, rigorous quality control measures are implemented to ensure that the substrate meets the required specifications for dimensional accuracy, layer thickness, 電気的性能, と信頼性. Various inspection and testing techniques, including visual inspection, 電気試験, 信頼性試験, may be performed to validate the quality of the substrate.
- Packaging and Shipment: Once manufacturing is complete and the substrates have passed quality control checks, they are packaged and prepared for shipment to semiconductor assembly facilities for further processing and integration into electronic devices.
By following these steps with precision and attention to detail, manufacturers can produce Ajinomoto GX92R package substrates with consistent quality, パフォーマンス, and reliability to meet the demanding requirements of modern semiconductor packaging applications.
How much should an Ajinomoto GX92R Package Substrate cost?
The cost of an Ajinomoto GX92R package substrate can vary depending on several factors, 基板材料を含む, 大きさ, 設計の複雑さ, manufacturing processes involved, and quantity ordered. 一般的に, here are some factors that influence the cost:
- 基板材料: Different substrate materials have varying costs. 例えば, ceramic substrates tend to be more expensive than FR-4 or polyimide substrates due to their superior thermal and electrical properties.
- サイズと複雑さ: Larger substrates or those with complex designs requiring more intricate patterning and processing will typically cost more to manufacture.
- 製造プロセス: The specific fabrication techniques and processes used during manufacturing can affect the cost. For instance, advanced lithography and metallization processes may incur higher costs compared to standard manufacturing methods.
- Volume: 一般的に, higher volumes lead to economies of scale, その結果、ユニットあたりのコストが削減されます. Bulk orders typically receive better pricing than smaller quantities.
- 品質と信頼性の要件: Substrates manufactured to meet stringent quality and reliability standards may incur higher production costs due to additional testing, 検査, and process control measures.
- サプライヤーとロケーション: The choice of supplier and manufacturing location can also impact the cost. Suppliers with advanced facilities and expertise may charge higher prices for their services.
As a rough estimate, the cost of an Ajinomoto GX92R package substrate could range from a few dollars to several tens of dollars per unit, 上記の要因によります. For a precise cost estimate, it’s advisable to contact Ajinomoto or a certified distributor directly, providing specific details about your substrate requirements.
What is the Ajinomoto GX92R Package Substrate base material?
The Ajinomoto GX92R package substrate base material is typically composed of advanced laminates designed to meet the demanding requirements of semiconductor packaging applications. These laminates serve as the foundation or substrate upon which the circuitry and interconnections for the semiconductor device are built.
One of the commonly used base materials for Ajinomoto GX92R package substrates is FR-4 (難燃 4). FR-4 is a widely used epoxy resin-based composite material reinforced with woven glass fiber. It offers excellent electrical insulation properties, 機械的強度, と寸法安定性, making it suitable for various electronic applications, including semiconductor packaging.
FR-4 substrates typically consist of multiple layers of fiberglass cloth impregnated with epoxy resin, which are stacked and laminated together under heat and pressure. The resulting laminate has a uniform structure with consistent electrical and mechanical properties across the substrate.
In addition to FR-4, other base materials such as polyimide and ceramic may also be used for Ajinomoto GX92R package substrates, アプリケーションの特定の要件に応じて. Polyimide substrates offer high-temperature resistance and flexibility, making them suitable for applications requiring thermal stability and conformal packaging. セラミック基板, on the other hand, provide excellent thermal conductivity and mechanical strength, making them ideal for high-power and high-frequency applications.
全, the choice of base material for Ajinomoto GX92R package substrates depends on factors such as electrical performance, 熱管理の要件, 機械的安定性, とコストに関する考慮事項. By selecting the appropriate base material and optimizing the substrate design and manufacturing process, Ajinomoto ensures that GX92R package substrates meet the stringent performance and reliability standards required for modern semiconductor packaging applications.
Which company makes Ajinomoto GX92R Package Substrates?
現在は, the company that manufactures Ajinomoto GX92R package substrates is Ajinomoto Co., Inc. based in Japan. Ajinomoto is a globally renowned company in the food and chemical industries, known for its innovations in food additives. While Ajinomoto is predominantly recognized for its food business, the company also possesses extensive experience and expertise in electronic materials.
Our company can produce Ajinomoto GX92R package substrates because we have a professional team and advanced equipment in materials science, electronic engineering, and manufacturing technology. Our engineers and technicians have rich experience in precisely designing and manufacturing high-quality package substrates according to the requirements and specifications of our customers.
We have advanced production lines and technological processes that enable us to flexibly meet various manufacturing demands for package substrates. Whether it’s complex multi-layer circuit designs, precise microfabrication, or high-performance thermal management, we can provide customized solutions to meet our customers’ 必要条件.
その上, our company places a strong emphasis on quality management and customer service. We strictly adhere to international standards and industry regulations to ensure that our products meet the requirements and expectations of our customers. Our customer service team is always available to support and assist customers, ensuring that they have a satisfactory experience throughout the entire collaboration process.
まとめ, our company possesses the professional knowledge, technical capabilities, and manufacturing capacity required to produce Ajinomoto GX92R package substrates. By partnering with us, customers can confidently obtain high-quality package substrates that meet their product performance and reliability requirements.
は何ですか 7 優れたカスタマーサービスの品質?
Good customer service is characterized by several key qualities that contribute to positive interactions between businesses and their customers. Here are seven qualities of good customer service:
- 応答: 優れたカスタマーサービスには、お客様からの問い合わせに迅速に対応することが含まれます, 懸念, とリクエスト. Whether it’s through phone calls, emails, live chat, or social media, responding to customers in a timely manner shows that their needs are valued and that the business is attentive to their concerns.
- 共感: 共感とは、他人の気持ちを理解し、共有する能力です. Good customer service representatives demonstrate empathy by actively listening to customers, acknowledging their emotions, and showing genuine concern for their well-being. Empathetic interactions help build rapport and trust with customers.
- プロ 意識: Professionalism entails maintaining a courteous and respectful demeanor when interacting with customers. This includes using polite language, maintaining a positive attitude, and handling difficult situations calmly and professionally. Professional behavior instills confidence in customers and reflects positively on the business.
- 知識能力: Good customer service representatives are knowledgeable about the products or services offered by the business. They can effectively answer customer questions, provide accurate information, and offer helpful recommendations or solutions. Having a thorough understanding of the business’s offerings enhances the customer experience and builds credibility.
- Accessibility: Accessibility involves making it easy for customers to reach out for support or assistance. This may include providing multiple channels for communication, such as phone support, 電子メール, live chat, and social media. かつ, businesses should ensure that customer service representatives are readily available during operating hours to assist customers promptly.
- Flexibility: Flexibility is the ability to adapt to the unique needs and preferences of each customer. Good customer service involves being flexible in finding solutions to accommodate customer requests, addressing issues promptly, and making exceptions when necessary. Being flexible demonstrates a commitment to customer satisfaction and fosters loyalty.
- Follow-up: Following up with customers after resolving their inquiries or concerns is an important aspect of good customer service. This can involve sending a thank-you email, conducting satisfaction surveys, or checking in to ensure that the issue has been fully resolved. Following up shows that the business values customer feedback and is committed to continuously improving the customer experience.
これらの資質を具現化することで、, businesses can cultivate strong relationships with their customers, ロイヤリティを育む, and differentiate themselves in the marketplace through exceptional customer service.
よくあるご質問(FAQ)
What is Ajinomoto GX92R package substrate?
Ajinomoto GX92R package substrate is a type of substrate used in semiconductor packaging. It provides the foundation for mounting and interconnecting semiconductor devices, 集積回路など (ICの), on printed circuit boards (プリント基板).
What are the key features of Ajinomoto GX92R package substrates?
Ajinomoto GX92R package substrates are known for their high reliability, 優れた熱性能, and precise electrical characteristics. They are designed to meet the stringent requirements of modern semiconductor devices, particularly in high-speed and high-power applications.
What materials are used in Ajinomoto GX92R package substrates?
Ajinomoto GX92R package substrates are typically made from advanced laminates such as FR-4 (epoxy resin), ポリイミド, またはセラミック. These materials offer superior electrical insulation, 熱伝導率, と機械的強度, depending on the specific application requirements.
What are the advantages of using Ajinomoto GX92R package substrates?
Ajinomoto GX92R package substrates offer several advantages, including enhanced thermal management capabilities, シグナルインテグリティの向上, and reduced electromagnetic interference (EMIの). They are also designed to minimize package size and weight while maximizing performance and reliability.
What types of semiconductor devices are compatible with Ajinomoto GX92R package substrates?
Ajinomoto GX92R package substrates are suitable for a wide range of semiconductor devices, including microprocessors, メモリチップ, power semiconductors, and integrated circuits (ICの) used in various electronic applications such as telecommunications, 自動車, および家庭用電化製品.
Are Ajinomoto GX92R package substrates customizable?
はい, Ajinomoto GX92R package substrates can be customized to meet specific customer requirements and application needs. This includes customization of substrate materials, レイヤースタックアップ, circuit design, and surface finishes to optimize performance and compatibility with the semiconductor device.
Where can I purchase Ajinomoto GX92R package substrates?
Ajinomoto GX92R package substrates are typically available through authorized distributors or directly from Ajinomoto Co., Inc. Customers can contact Ajinomoto or its authorized partners to inquire about product availability, プライシング, and technical support.