高度なBT BGA PCBメーカー
Advanced BT BGA PCB Manufacturer.Advanced BT BGA PCBは、最先端のBluetoothアプリケーション向けに調整された洗練されたプリント回路基板です. ボールグリッドアレイの統合 (BGAの) コンポーネント, 高速データ転送で優れた性能を発揮します, 電力効率, およびワイヤレス接続. これらのPCBは、RF最適化で細心の注意を払って設計されています, 正確なアンテナ配置, 堅牢なシグナルインテグリティ. 高品質の素材と高度な技術で製造, スマートフォンなど多様な電子機器の信頼性と耐久性を確保しています, IoTデバイス, ウェアラブル, および自動車用電子機器. 高度なBT BGA PCBは、テクノロジーの最高峰を表しています, 現代のデジタル時代におけるシームレスで効率的なBluetooth通信を実現.
Advanced BT BGA PCBとは?
Advanced BT BGA PCBは、プリント回路基板を指します (プリント基板) ボールグリッドアレイに対応するように設計されています (BGAの) コンポーネント, 高度なBluetooth専用に調整 (BTの) アプリケーション. BGAは、ピンの代わりに小さなはんだボールの配列を使用してデバイスをPCBの表面に取り付けるパッケージング技術です, 密度の向上や電気的性能の向上などの利点を提供します.
Bluetoothテクノロジーの文脈で, Advanced BT BGA PCBには、高速データ転送に最適化された機能が組み込まれている可能性があります, 低消費電力, 堅牢なワイヤレス接続. これには、特殊なRFが含まれる場合があります (無線周波数) 設計, シグナルインテグリティに関する考慮事項, アンテナや電源管理回路などの他のコンポーネントとの統合.
さらに, ザ “アドバンスド” 指定は、このPCBが最新のBluetooth規格をサポートしている可能性があることを示唆しています, Bluetooth Low Energyなど (ブレ) またはBluetooth 5, より長い範囲のような拡張機能を提供する, より高いデータスループット, セキュリティの向上.
Advanced BT BGA PCBの設計には、PCBレイアウトの専門知識が必要です, RFエンジニアリング, 最適なパフォーマンスと信頼性を確保するためのBluetoothプロトコル. かつ, 業界標準とベストプラクティスへの準拠は、最新のBluetooth対応デバイスの要件を満たすために不可欠です, スマートフォンなど, IoTデバイス, ウェアラブル, および自動車用電子機器.
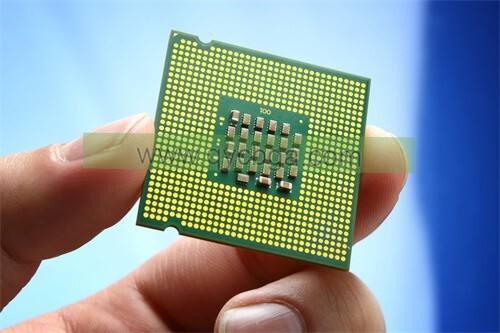
高度なBT BGA PCBメーカー
Advanced BT BGA PCB デザイン ガイドラインとは?
Aの設計dvanced BTの (Bluetooth) BGAの (ボールグリッドアレイ) プリント基板 最適なパフォーマンスと信頼性を確保するためには、さまざまな要素を慎重に検討する必要があります. ここにいくつかのガイドラインがあります:
- RF に関する考慮事項: RFに細心の注意を払う (無線周波数) デザインの原則. 適切なRFレイアウト手法, インピーダンスマッチングなど, 信号絶縁, および制御されたインピーダンストレース, シグナルインテグリティを維持し、干渉を最小限に抑えるために重要です.
- アンテナの配置: PCBレイアウトがBluetoothアンテナの配置に対応していることを確認します(s) 最適な位置で、信号強度とカバレッジを最大に. 信号の妨害や干渉を引き起こす可能性のある金属部品やその他の RF に敏感な領域の近くにアンテナを置かないでください.
- パワーインテグリティ: 配電ネットワークの実装 (PDNの) 電圧降下とノイズを最小限に抑える, 特にRF性能にとって重要な領域で. BGAコンポーネントへの安定した電源供給を維持するためには、適切なデカップリングコンデンサの配置と電源プレーンの設計が不可欠です.
- サーマルマネジメント: BGA部品は大きな熱を発生することがある, 特に高速データ転送中. サーマルビアを内蔵, ヒートシンク, 適切なPCB層のスタックアップにより、熱を効率的に放散し、性能の低下やコンポーネントの損傷につながる過熱を防ぎます.
- シグナルインテグリティ: Ensure signal integrity by minimizing signal reflections, クロストーク, および電磁干渉 (EMIの). Use techniques such as controlled impedance routing, 信号シールド, and proper ground plane design to maintain signal integrity throughout the PCB.
- 製造可能性: Consider manufacturability during PCB layout to ensure that the design can be reliably manufactured and assembled. Pay attention to BGA pad layout, solder mask openings, and assembly tolerances to prevent soldering defects and ensure proper BGA attachment.
- Compliance with Standards: Ensure that the PCB design complies with relevant industry standards and regulations, including Bluetooth SIG (Special Interest Group) 必要条件. Compliance testing may be necessary to certify the Bluetooth functionality and interoperability of the final product.
- テストの容易性: Design the PCB with test points and access for debugging and testing during development and production. Incorporate built-in self-test (BIST) features where possible to facilitate diagnostic testing and troubleshooting.
これらのガイドラインに従う, designers can create Advanced BT BGA PCBs that meet the stringent requirements of modern Bluetooth applications, ensuring high performance, 確実, 業界標準への準拠.
What is the Advanced BT BGA PCB Fabrication Process?
The fabrication process for an Advanced BT (Bluetooth) BGAの (ボールグリッドアレイ) PCB involves several steps to transform the design into a physical circuit board ready for assembly. Here’s an overview of the typical process:
- デザインの準備: The fabrication process begins with the preparation of the PCB design files. This includes the PCB layout, which specifies the placement of components, routing of traces, and other design elements. Design files are typically generated using PCB design software and saved in formats compatible with PCB fabrication equipment.
- 材料の選択: Choose the appropriate PCB substrate material based on the requirements of the design, such as dielectric constant, 熱伝導率, とコスト. Common substrate materials for BGA PCBs include FR-4 (flame retardant 4), which is a widely used epoxy-based laminate, and specialized materials optimized for RF applications.
- Preparation of Substrate: The selected substrate material is prepared by cutting it to the desired size and cleaning the surface to remove any contaminants that could affect the adhesion of copper and other layers.
- Copper Cladding: Copper foil is laminated onto the substrate to create the conductive layers of the PCB. The copper foil is bonded to the substrate using heat and pressure, and excess foil is trimmed to size.
- フォトレジスト塗布: A layer of photoresist material is applied to the surface of the copper foil. Photoresist is a light-sensitive material that will be used to create the PCB’s circuit pattern.
- 露出と開発: The PCB design pattern is transferred onto the photoresist layer using a process called photolithography. UV light is passed through a photomask containing the circuit pattern, exposing the photoresist in the desired areas. 次に、露光したフォトレジストを現像して、未露光領域を除去します, revealing the underlying copper.
- エッチング: The exposed copper is etched away using chemical solutions, leaving behind the desired circuit traces on the PCB. Etching is typically performed using acidic solutions that dissolve the copper but do not affect the substrate material.
- 錬成: Holes are drilled into the PCB to accommodate through-hole components and vias. High-precision drilling equipment is used to create holes with diameters as small as a fraction of a millimeter.
- 表面仕上げ: The exposed copper surfaces are coated with a surface finish to protect them from oxidation and facilitate soldering during assembly. Common surface finishes for BGA PCBs include HASL (熱風はんだレベリング), エニグ (無電解ニッケル浸漬金), and OSP (Organic Solderability Preservative).
- 品質管理: The fabricated PCB undergoes inspection and testing to ensure that it meets the required specifications for dimensions, tolerances, and electrical continuity. Automated optical inspection (葵) and electrical testing are commonly used to detect defects and verify the functionality of the PCB.
Once the fabrication process is complete, the Advanced BT BGA PCB is ready for assembly, where BGA components and other surface-mount devices are soldered onto the board to create the final electronic product.
How do you manufacture an Advanced BT BGA PCB?
Manufacturing an Advanced BT (Bluetooth) BGAの (ボールグリッドアレイ) PCB involves a series of steps from design validation to final assembly. Here’s a detailed outline of the manufacturing process:
- Design Validation: Before manufacturing begins, it’s crucial to validate the PCB design to ensure it meets the requirements for Bluetooth functionality, シグナルインテグリティ, と製造可能性. This may involve simulation, プロトタイピング, and testing to verify the design’s performance.
- Material Procurement: Once the design is validated, the necessary materials are procured. This includes the PCB substrate material (例えば。, FR-4), copper foil for conductive layers, ソルダーマスク, silkscreen ink, and surface finish chemicals.
- Preparation of Substrate: The selected substrate material is prepared by cutting it to the desired size and cleaning the surface to remove any contaminants. The substrate may also undergo surface treatment processes to enhance adhesion and facilitate subsequent manufacturing steps.
- Copper Cladding: Copper foil is laminated onto the substrate to form the conductive layers of the PCB. The copper foil is bonded to the substrate using heat and pressure, and excess foil is trimmed to size.
- 錬成:Holes are drilled into the PCB to accommodate through-hole components and vias. High-precision drilling equipment is used to create holes with diameters as small as needed for the BGA components.
- Inner Layer Imaging:A photoresist layer is applied to the surface of the copper foil on inner layers. The PCB design pattern is then transferred onto the photoresist layer using photolithography techniques. After exposure and development, the unwanted copper is etched away, 目的の回路トレースを残す.
- レイヤーのアライメントとボンディング: Multiple layers of the PCB are aligned and bonded together to form the multilayer stack. Alignment is critical to ensure that the vias and traces on different layers line up correctly.
- Outer Layer Imaging: Similar to inner layer imaging, a photoresist layer is applied to the surface of the outer copper layers. The PCB design pattern is transferred onto the photoresist layer using photolithography, and the unwanted copper is etched away.
- Surface Finish Application:The exposed copper surfaces are coated with a surface finish to protect them from oxidation and facilitate soldering during assembly. Common surface finishes for BGA PCBs include HASL, エニグ, and OSP.
- ソルダーマスクアプリケーション: A solder mask layer is applied to the PCB to insulate the copper traces and prevent solder bridges during assembly. Openings are created in the solder mask layer to expose the pad areas for soldering.
- Silkscreen Printing: Information such as component outlines, reference designators, and logos are printed onto the PCB using silkscreen ink for assembly and identification purposes.
- 品質管理: The manufactured PCBs undergo thorough inspection and testing to ensure they meet the required specifications for dimensions, tolerances, and electrical continuity. Automated optical inspection (葵) and electrical testing are commonly used to detect defects.
Once the PCBs pass quality control, they are ready for assembly, where BGA components and other surface-mount devices are soldered onto the board to create the final electronic product. Advanced BT BGA PCB manufacturing requires precision, attention to detail, and adherence to industry standards to ensure the reliability and performance of the finished product.
How much should an Advanced BT BGA PCB cost?
The cost of an Advanced BT (Bluetooth) BGAの (ボールグリッドアレイ) PCB can vary widely depending on factors such as complexity, 大きさ, 量, 材料仕様, と製造プロセス. しかし, I can provide a rough estimate based on typical industry standards and considerations.
- Complexity: The complexity of the PCB design, レイヤー数を含む, density of components, and routing requirements, significantly impacts the cost. More complex designs with intricate routing and high component density generally cost more to manufacture.
- Size: Larger PCBs require more material and processing time, その結果、コストが高くなります. 逆に言えば, smaller PCBs may be more cost-effective to manufacture.
- Material Specifications: The choice of materials, such as substrate type, copper thickness, そして表面の終わり, コストに影響を与える可能性があります. Specialized materials optimized for RF performance or high-speed data transfer may be more expensive than standard materials.
- 製造プロセス: Advanced manufacturing processes, such as high-precision drilling, controlled impedance routing, and specialized surface finishes, can increase the cost of PCB production.
- 量: Economies of scale typically apply in PCB manufacturing, meaning that larger production quantities often result in lower per-unit costs. しかし, prototype or small-batch production runs may incur higher costs per unit.
- サプライヤーとロケーション: PCB manufacturing costs can vary depending on the chosen supplier and their location. Suppliers with advanced capabilities and state-of-the-art equipment may charge higher prices for their services.
As a rough estimate, the cost of manufacturing an Advanced BT BGA PCB could range from a few dollars for a simple, low-complexity design in small quantities to several hundred dollars or more for a highly complex design with specialized materials and processes in larger quantities.
For a more accurate cost estimate, it’s advisable to consult with PCB manufacturers or suppliers and provide detailed specifications of the desired PCB design, including quantity, 料, and manufacturing requirements. They can provide quotes based on your specific needs and production volume.
What is the Advanced BT BGA PCB base material?
The choice of base material for an Advanced BT (Bluetooth) BGAの (ボールグリッドアレイ) PCB depends on various factors such as performance requirements, コストに関する考慮事項, および製造上の制約. しかし, a common and widely used base material for such applications is FR-4 (難燃 4).
FR-4 is a widely used epoxy-based laminate that offers several advantages suitable for Advanced BT BGA PCBs:
- 電気的性能: FR-4 provides good electrical insulation properties, 低誘電率, and stable electrical performance over a wide range of frequencies. This is important for maintaining signal integrity and minimizing interference in high-frequency applications such as Bluetooth.
- 機械的強度: FR-4 is known for its mechanical strength and dimensional stability, making it suitable for applications where the PCB may be subjected to mechanical stress or environmental factors.
- Thermal Properties: FR-4 has adequate thermal conductivity properties to dissipate heat generated by BGA components, although additional thermal management techniques may be required for advanced designs with high power dissipation.
- 費用対効果: FR-4 is relatively inexpensive compared to other specialized materials, making it a cost-effective choice for many applications.
While FR-4 is commonly used, there are also specialized materials available for specific requirements in Advanced BT BGA PCBs. 例えば, some applications may benefit from high-frequency laminate materials optimized for RF performance or materials with enhanced thermal conductivity for improved heat dissipation.
Ultimately, the choice of base material should be based on the specific requirements of the application, including performance, 費用, and manufacturability considerations. Consulting with PCB designers and manufacturers can help determine the most suitable base material for a particular Advanced BT BGA PCB design.
Which company manufactures Advanced BT BGA PCBs?
Many companies are capable of manufacturing Advanced BT BGA PCBs, including large electronics manufacturing enterprises, specialized PCB manufacturers, and custom electronic design and manufacturing service providers. Some well-known companies may include Foxconn, EU PCB, Feida Electronics, その他. These companies typically possess advanced production equipment, extensive experience, and professional teams capable of meeting various complex PCB manufacturing needs.
Our company is also a professional PCB manufacturer with the technology and resources required to produce Advanced BT BGA PCBs. Here are some advantages and capabilities of our company in manufacturing Advanced BT BGA PCBs:
- Technical Strength: We have advanced PCB manufacturing technology and equipment, including high-precision PCB production lines, automated process control systems, その他. Our technical team has rich experience and expertise to provide customized solutions for complex design requirements.
- Quality Assurance: We strictly adhere to the ISO quality management system and employ rigorous quality control processes to ensure that every PCB meets customer specifications and industry standards. We have comprehensive quality inspection equipment and processes to ensure stable and reliable product quality.
- Flexible Production Capacity:Our production capacity is flexible and diverse, capable of meeting orders of different scales and requirements. Whether it’s small batch customization or large-scale mass production, we can deliver high-quality products promptly.
- Customer Customization Services: We emphasize communication and cooperation with customers to provide customized solutions based on their requirements. Our sales and technical teams will provide full-service support to ensure that customer needs are met throughout the process.
まとめ, our company possesses the technology, resources, and experience required to manufacture Advanced BT BGA PCBs and can provide high-quality, reliable products and services. We are willing to collaborate with customers to drive development in the electronics manufacturing industry.
は何ですか 7 優れたカスタマーサービスの品質?
Good customer service is characterized by several key qualities that contribute to positive interactions and relationships with customers. Here are seven qualities of good customer service:
- 応答: 優れたカスタマーサービスには、お客様からの問い合わせに迅速に対応することが含まれます, 懸念, とリクエスト. Responding to customers in a timely manner demonstrates attentiveness and a commitment to meeting their needs efficiently.
- 共感: Empathy is essential in understanding and acknowledging the emotions and perspectives of customers. Showing empathy towards customers’ frustrations or challenges helps build rapport and fosters trust in the service provider.
- Clarity: Effective communication is crucial in providing good customer service. Clear and concise communication helps ensure that customers understand the information provided and can make informed decisions. Avoiding jargon and using simple language contributes to clarity in communication.
- プロ 意識: Professionalism involves maintaining a courteous and respectful demeanor when interacting with customers. Treating customers with professionalism regardless of the situation reinforces the company’s commitment to customer satisfaction.
- Problem-solving skills: Good customer service representatives possess strong problem-solving skills to address customer issues and resolve conflicts effectively. Being proactive in finding solutions demonstrates a commitment to resolving issues and meeting customer expectations.
- Consistency: Consistency in service delivery is key to building customer loyalty and trust. Providing consistently high-quality service across all interactions and channels reinforces the company’s reputation and fosters long-term relationships with customers.
- パーソナル 化: Tailoring the customer experience to individual preferences and needs demonstrates a customer-centric approach to service delivery. Personalization can involve remembering customer preferences, anticipating their needs, and offering relevant recommendations or solutions.
これらの資質を具現化することで、, businesses can cultivate a culture of excellent customer service and create positive experiences that lead to customer satisfaction, 忠義, and advocacy.
よくあるご質問(FAQ) (Frequently Asked Questions)
Advanced BT BGA PCBとは?
An Advanced BT BGA PCB is a printed circuit board designed to accommodate Ball Grid Array (BGAの) components specifically tailored for advanced Bluetooth applications. It incorporates features optimized for high-speed data transfer, 低消費電力, 堅牢なワイヤレス接続.
What are the advantages of using BGA components in BT PCBs?
BGA components offer advantages such as increased density, 電気的性能の向上, and better thermal characteristics compared to traditional packaging methods. They are well-suited for compact and high-performance Bluetooth applications.
What are the key design considerations for Advanced BT BGA PCBs?
Design considerations include RF (無線周波数) パフォーマンス, antenna placement, パワーインテグリティ, サーマルマネジメント, シグナルインテグリティ, 製造可能性, 規格への準拠, and testability.
What materials are commonly used for Advanced BT BGA PCBs?
Common base materials include FR-4 (難燃 4), which offers good electrical performance, 機械的強度, そして費用対効果. Specialized materials optimized for RF performance or thermal conductivity may also be used for specific applications.
How are Advanced BT BGA PCBs manufactured?
The manufacturing process involves steps such as design preparation, material procurement, substrate preparation, copper cladding, 錬成, imaging, エッチング, 表面仕上げアプリケーション, ソルダーマスクアプリケーション, silkscreen printing, と品質管理.
What are the typical costs associated with Advanced BT BGA PCBs?
Costs vary depending on factors such as complexity, 大きさ, 量, 材料仕様, と製造プロセス. A rough estimate ranges from a few dollars for simple designs to several hundred dollars or more for complex designs in larger quantities.
Which companies manufacture Advanced BT BGA PCBs?
Many companies, including electronics manufacturing enterprises, specialized PCB manufacturers, and custom electronic design and manufacturing service providers, are capable of manufacturing Advanced BT BGA PCBs.
What are the qualities of good customer service when sourcing Advanced BT BGA PCBs?
Good customer service qualities include responsiveness, empathy, clarity in communication, professionalism, problem-solving skills, consistency, and personalization in addressing customer inquiries and requirements.