Ultrathin CPU Substrates Manufacturer
Ultrathin CPU Substrates Manufacturer,Ultrathin CPU substrates represent a pivotal advancement in electronic device design, offering a compact and efficient foundation for CPU chips in various applications. These substrates, meticulously engineered from materials like silicon or specialized polymers, boast an incredibly thin profile, often measuring mere micrometers in thickness. Their thinness enables the miniaturization of electronic devices, optimizing space utilization within compact gadgets like smartphones, tablets, and wearables. Beyond space efficiency, ultrathin CPU substrates play a crucial role in enhancing thermal management, ensuring efficient heat dissipation to prevent overheating and maintain optimal performance. Moreover, these substrates facilitate high-speed electrical connectivity, enabling seamless communication between the CPU chip and other components. With their blend of compactness, thermal efficiency, and electrical performance, ultrathin CPU substrates are indispensable components driving the evolution of sleeker, more powerful, and energy-efficient electronic devices in today’s rapidly advancing technological landscape.
What is an Ultrathin CPU Substrate?
An ultrathin CPU substrate is a crucial component in modern electronic devices, particularly in microprocessors and central processing units (CPUs). Essentially, it’s a thin layer of material upon which the CPU chip is mounted and connected to other parts of the device.
Traditionally, CPU substrates were made from materials like fiberglass or ceramics, which were relatively thick and bulky. However, with the demand for smaller, more efficient electronic devices, manufacturers have turned to ultrathin substrates to save space and enhance performance.
These ultrathin substrates are typically made from advanced materials such as silicon or specialized polymers that offer both mechanical stability and electrical conductivity. They are engineered to be incredibly thin, often measuring only a fraction of a millimeter in thickness.
The primary advantage of ultrathin CPU substrates lies in their ability to enable the miniaturization of electronic devices. By reducing the thickness of the substrate, manufacturers can create thinner and lighter devices without sacrificing processing power. This is particularly important in applications such as smartphones, tablets, and ultra-thin laptops, where space is at a premium.
Additionally, ultrathin substrates can contribute to improved thermal management within electronic devices. Thinner substrates have better heat dissipation properties, allowing for more efficient cooling of the CPU and other components, which can help prevent overheating and improve overall system reliability.
Furthermore, the use of ultrathin substrates can also lead to cost savings in manufacturing, as they require fewer materials and less energy to produce compared to thicker substrates.
Overall, ultrathin CPU substrates play a vital role in advancing the capabilities of electronic devices, enabling them to become smaller, lighter, and more powerful while maintaining efficient thermal management and cost-effectiveness.
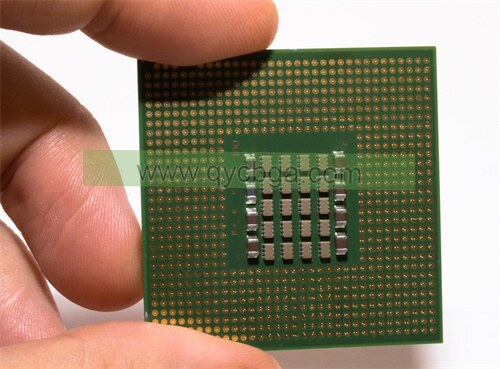
Ultrathin CPU Substrates Manufacturer
What are the Ultrathin CPU Substrate Design Guidelines?
Designing ultrathin CPU substrates requires careful consideration of several factors to ensure optimal performance, reliability, and manufacturability. Here are some key guidelines that designers typically follow:
- Material Selection: Choose materials with suitable properties for the substrate, such as high thermal conductivity, mechanical strength, and electrical conductivity. Common materials include silicon, specialized polymers, and composite materials.
- Thickness Optimization: Determine the optimal thickness of the substrate based on the specific requirements of the CPU and the overall device. Thinner substrates offer advantages in terms of space savings and thermal management but must maintain adequate mechanical integrity.
- Dielectric Properties: Ensure that the substrate material has appropriate dielectric properties to minimize signal loss and interference in the CPU’s electrical connections. Low dielectric constant materials are often preferred for high-frequency applications.
- Thermal Management: Incorporate features into the substrate design to enhance thermal conductivity and heat dissipation, such as thermal vias, metal layers, and thermal pads. Efficient thermal management is critical for preventing overheating and maintaining CPU performance.
- Signal Integrity: Implement design features to maintain signal integrity and minimize electrical noise, such as controlled impedance traces, ground planes, and signal isolation techniques. Signal integrity is essential for reliable communication between the CPU and other components.
- Manufacturability: Design the substrate with manufacturability in mind, considering factors such as material availability, fabrication processes, and cost-effectiveness. Ensure that the design can be scaled up for mass production without compromising quality.
- Mechanical Stability:Assess the mechanical stability of the substrate to withstand handling, thermal cycling, and mechanical stresses during assembly and operation. Reinforce critical areas with additional support structures or bonding techniques as needed.
- Compatibility with Assembly Processes: Ensure compatibility with assembly processes such as flip-chip bonding, wire bonding, or surface-mount technology (SMT). Design features such as solder pads and alignment marks should facilitate precise and reliable assembly.
- Reliability Testing: Conduct thorough reliability testing to evaluate the substrate’s performance under various environmental conditions, including temperature extremes, humidity, and mechanical shock. Identify and address any potential failure modes to ensure long-term reliability.
- Compliance with Standards:Ensure compliance with industry standards and regulations related to electronic components and materials, such as RoHS (Restriction of Hazardous Substances) and IPC (Association Connecting Electronics Industries) standards.
By following these design guidelines, engineers can develop ultrathin CPU substrates that meet the demanding requirements of modern electronic devices while achieving optimal performance, reliability, and manufacturability.
What is the Ultrathin CPU Substrate Fabrication Process?
The fabrication process for ultrathin CPU substrates involves several steps, each crucial for achieving the desired thinness, electrical properties, and reliability. Here’s an overview of the typical fabrication process:
- Material Selection: The process begins with the selection of suitable substrate materials such as silicon, specialized polymers, or composite materials. The choice of material depends on factors such as thermal conductivity, mechanical strength, and dielectric properties.
- Substrate Preparation:The selected material is prepared for processing by cleaning and polishing to remove any contaminants and surface imperfections. This step ensures the substrate’s surface is smooth and uniform, facilitating subsequent manufacturing steps.
- Deposition of Thin Film Layers: Thin film deposition techniques, such as chemical vapor deposition (CVD) or physical vapor deposition (PVD), are used to apply thin layers of conductive and insulating materials onto the substrate. These layers may include metal traces, dielectric materials, and barrier layers, depending on the substrate design requirements.
- Photolithography: Photolithography is employed to define the intricate patterns of conductive traces and features on the substrate. A photoresist material is applied to the substrate surface, exposed to ultraviolet (UV) light through a photomask, and then developed to selectively remove the exposed regions, leaving behind the desired patterns.
- Etching: Etching processes, such as wet chemical etching or plasma etching, are used to selectively remove material from the substrate according to the pattern defined by the photoresist. This step creates the precise features and conductive traces necessary for electrical connectivity within the CPU substrate.
- Surface Finishing: After etching, the substrate surface may undergo surface finishing processes to improve its electrical and mechanical properties. This may include treatments such as chemical mechanical polishing (CMP) or surface coating to enhance conductivity and protect against oxidation.
- Metallization: Metal layers are deposited onto the substrate surface to create conductive pathways and interconnects between the CPU chip and other components. Techniques such as sputtering or electroplating are used to deposit metal films with precise thickness and conductivity.
- Insulation and Passivation: Insulating layers and passivation coatings are applied to the substrate to isolate conductive traces and protect against environmental factors such as moisture and corrosion. These layers help ensure the long-term reliability of the CPU substrate.
- Quality Control and Testing: Throughout the fabrication process, rigorous quality control measures are implemented to ensure the dimensional accuracy, electrical performance, and reliability of the ultrathin CPU substrate. Testing may include electrical continuity tests, impedance measurements, and visual inspection under high magnification.
- Packaging and Integration: Once fabrication is complete, the ultrathin CPU substrate is packaged and integrated into the final electronic device assembly. This may involve flip-chip bonding, wire bonding, or surface-mount technology (SMT) processes to connect the CPU chip to the substrate and other components.
By following these fabrication steps with precision and attention to detail, manufacturers can produce ultrathin CPU substrates that meet the demanding requirements of modern electronic devices in terms of size, performance, and reliability.
How do you manufacture Ultrathin CPU Substrates?
Manufacturing ultrathin CPU substrates involves a series of complex processes aimed at creating thin, precise, and reliable substrates for mounting and interconnecting CPU chips and other electronic components. Here’s a detailed overview of the typical manufacturing process:
- Substrate Material Selection: The process begins with the selection of appropriate substrate materials based on factors such as thermal conductivity, mechanical strength, and electrical properties. Common materials include silicon, specialized polymers, and composite materials.
- Substrate Preparation:The selected substrate material is prepared for processing by cleaning and polishing to remove surface contaminants and imperfections. This step ensures a smooth and uniform substrate surface, essential for subsequent manufacturing steps.
- Thin Film Deposition: Thin film deposition techniques, such as chemical vapor deposition (CVD) or physical vapor deposition (PVD), are used to apply thin layers of conductive and insulating materials onto the substrate. These layers may include metal traces, dielectric materials, and barrier layers, depending on the substrate design requirements.
- Photolithography: Photolithography is employed to define the intricate patterns of conductive traces and features on the substrate. A photoresist material is applied to the substrate surface, exposed to ultraviolet (UV) light through a photomask, and then developed to selectively remove the exposed regions, leaving behind the desired patterns.
- Etching: Etching processes, such as wet chemical etching or plasma etching, are used to selectively remove material from the substrate according to the pattern defined by the photoresist. This step creates the precise features and conductive traces necessary for electrical connectivity within the CPU substrate.
- Surface Finishing: After etching, the substrate surface may undergo surface finishing processes to improve its electrical and mechanical properties. This may include treatments such as chemical mechanical polishing (CMP) or surface coating to enhance conductivity and protect against oxidation.
- Metallization: Metal layers are deposited onto the substrate surface to create conductive pathways and interconnects between the CPU chip and other components. Techniques such as sputtering or electroplating are used to deposit metal films with precise thickness and conductivity.
- Insulation and Passivation: Insulating layers and passivation coatings are applied to the substrate to isolate conductive traces and protect against environmental factors such as moisture and corrosion. These layers help ensure the long-term reliability of the CPU substrate.
- Quality Control and Testing: Throughout the manufacturing process, rigorous quality control measures are implemented to ensure the dimensional accuracy, electrical performance, and reliability of the ultrathin CPU substrate. Testing may include electrical continuity tests, impedance measurements, and visual inspection under high magnification.
- Packaging and Integration: Once manufacturing is complete, the ultrathin CPU substrate is packaged and integrated into the final electronic device assembly. This may involve flip-chip bonding, wire bonding, or surface-mount technology (SMT) processes to connect the CPU chip to the substrate and other components.
By following these manufacturing steps with precision and attention to detail, manufacturers can produce ultrathin CPU substrates that meet the demanding requirements of modern electronic devices in terms of size, performance, and reliability.
How much should an Ultrathin CPU Substrate cost?
The cost of an ultrathin CPU substrate can vary significantly depending on several factors, including the materials used, the complexity of the design, the manufacturing processes involved, and the volume of production. Here are some considerations that can affect the cost:
- Material Costs: The cost of the substrate material itself can be a significant factor. High-quality materials with specific properties, such as silicon or specialized polymers, may be more expensive than conventional substrate materials.
- Manufacturing Processes: The complexity and precision of the manufacturing processes required to fabricate ultrathin CPU substrates can impact the cost. Processes such as thin film deposition, photolithography, and etching may require specialized equipment and skilled labor, adding to the overall manufacturing cost.
- Design Complexity: The complexity of the substrate design, including the number of layers, the density of features, and the size of the substrate, can affect the cost. More intricate designs may require additional processing steps and higher precision, increasing the manufacturing cost.
- Volume of Production: Economies of scale play a significant role in determining the cost of ultrathin CPU substrates. Higher volumes of production generally result in lower per-unit costs due to efficiencies in manufacturing and material procurement.
- Quality and Reliability Requirements: Meeting stringent quality and reliability standards can add to the cost of ultrathin CPU substrates. Additional testing, inspection, and quality control measures may be necessary to ensure that the substrates meet the required specifications and performance criteria.
- Customization and Specialization:Customized or specialized substrate designs may incur higher costs due to the need for tailored manufacturing processes and materials. However, these customizations may be necessary to meet specific performance or integration requirements for certain applications.
Overall, the cost of an ultrathin CPU substrate can vary widely depending on the specific requirements of the application, the desired performance characteristics, and the production scale. It’s essential for manufacturers to balance cost considerations with the need for high quality, reliability, and performance to deliver substrates that meet the demands of modern electronic devices.
What is Ultrathin CPU Substrate base material?
The base material for ultrathin CPU substrates can vary depending on the specific requirements of the application and the desired properties of the substrate. Some common materials used as the base for ultrathin CPU substrates include:
- Silicon: Silicon is a widely used material for CPU substrates due to its excellent electrical properties, thermal conductivity, and compatibility with semiconductor manufacturing processes. Silicon substrates can be fabricated with high precision and can support complex integrated circuits.
- Specialized Polymers: Certain polymers, such as polyimide or liquid crystal polymer (LCP), are used as base materials for ultrathin CPU substrates in flexible and bendable electronics applications. These polymers offer flexibility, lightweight, and compatibility with roll-to-roll manufacturing processes.
- Glass: Glass substrates are sometimes used in specialized applications where high thermal stability and mechanical strength are required. Glass substrates can provide excellent flatness and dimensional stability, making them suitable for high-precision applications.
- Composite Materials: Composite materials, such as ceramic-filled polymers or metal matrix composites, can be used to create ultrathin CPU substrates with enhanced mechanical properties and thermal conductivity. These materials combine the advantages of different components to achieve specific performance characteristics.
- Flexible Substrates: In applications requiring flexibility or stretchability, flexible substrates made from materials such as polyimide, PET (polyethylene terephthalate), or elastomers may be used as the base material for ultrathin CPU substrates. These substrates can conform to curved surfaces and withstand mechanical deformation.
The choice of base material depends on factors such as the electrical requirements, thermal management needs, mechanical flexibility, and manufacturability of the substrate. Engineers carefully select the base material to ensure that the ultrathin CPU substrate meets the performance and reliability requirements of the intended application.
Which company makes Ultrathin CPU Substrates?
Many companies are producing ultrathin CPU substrates, with major players including Intel, TSMC, Samsung Electronics, Taiwan Semiconductor Manufacturing Company (TSMC), and Micron Technology. These companies are continuously conducting research and innovation to meet the increasing demands for performance, size, and reliability in modern electronic devices.
For our company, we are also an innovative enterprise focusing on electronic manufacturing. We have advanced manufacturing equipment and technology capable of producing high-quality ultrathin CPU substrates. Here are several advantages and capabilities of our company in producing ultrathin CPU substrates:
- Advanced Manufacturing Technology: We have advanced manufacturing equipment and technology, including thin film deposition, photolithography, etching, and other processes. Our manufacturing process is carefully designed and optimized to achieve high precision and reliability for ultrathin substrates.
- Customized Production Capability: We can customize ultrathin CPU substrates according to customer requirements, including size, materials, electrical performance, and other specifications. We work closely with customers to provide tailored solutions to meet their specific application needs.
- Quality Control and Reliability Assurance:We strictly adhere to quality management systems to ensure that each batch of products meets stringent quality standards and specifications. We conduct comprehensive quality inspections and testing to ensure the stability and reliability of ultrathin CPU substrates.
- Continuous Innovation and R&D:We focus on technological innovation and research and development investment to explore new manufacturing processes and materials to enhance product performance and competitiveness. We collaborate with industry partners and research institutions to drive the development of ultrathin CPU substrate technology.
In summary, our company has the technical capabilities and manufacturing strength to produce ultrathin CPU substrates and is committed to providing high-quality, customized solutions to customers. We will continue to innovate and improve to meet the growing demands of customers and achieve greater success in the field of electronic manufacturing.
What are the 7 qualities of good customer service?
Good customer service is characterized by several key qualities that contribute to positive interactions and relationships with customers. Here are seven essential qualities of good customer service:
- Responsive: Good customer service is responsive to customer inquiries, concerns, and requests in a timely manner. Whether it’s answering questions, resolving issues, or providing assistance, being responsive demonstrates attentiveness and a commitment to meeting customer needs promptly.
- Empathetic: Empathy is crucial in good customer service. It involves understanding and acknowledging the customer’s feelings, concerns, and perspectives. Empathetic interactions show customers that their emotions are valued and that the service provider cares about their experience.
- Knowledgeable:Good customer service representatives possess in-depth knowledge about the products or services they are supporting. They can provide accurate information, offer helpful advice, and address customer inquiries effectively. Knowledgeable staff inspire confidence and trust in customers.
- Professionalism: Professionalism in customer service encompasses attributes such as courtesy, politeness, and respectfulness. Maintaining a professional demeanor fosters a positive atmosphere and builds trust between the customer and the service provider.
- Problem-Solving Skills:Effective problem-solving skills are essential for resolving customer issues and concerns. Good customer service involves identifying problems, evaluating solutions, and implementing resolutions in a proactive and efficient manner. Service providers should be resourceful and creative in finding solutions that meet customer needs.
- Consistency:Consistency is key to providing good customer service across all interactions and touchpoints. Customers expect a consistent experience whether they are interacting with a company online, over the phone, or in person. Consistent service builds customer loyalty and fosters positive brand perception.
- Follow-Up: Following up with customers after interactions demonstrates a commitment to their satisfaction and provides an opportunity to ensure that their needs have been met. Whether it’s checking in on a previous issue, soliciting feedback, or offering additional assistance, follow-up communication reinforces the relationship between the customer and the service provider.
By embodying these qualities, organizations can deliver exceptional customer service experiences that foster loyalty, satisfaction, and positive brand advocacy.
FAQs
What is an ultrathin CPU substrate?
An ultrathin CPU substrate is a thin layer of material upon which a CPU chip is mounted and connected to other electronic components. It serves as a foundation for the CPU and facilitates electrical connectivity within the device.
What are the advantages of ultrathin CPU substrates?
Ultrathin CPU substrates offer several advantages, including space-saving design, improved thermal management, enhanced electrical performance, and potential cost savings in manufacturing.
What materials are used in ultrathin CPU substrates?
Common materials used in ultrathin CPU substrates include silicon, specialized polymers, composite materials, and glass. The choice of material depends on factors such as thermal conductivity, mechanical strength, and electrical properties.
How are ultrathin CPU substrates manufactured?
The manufacturing process for ultrathin CPU substrates involves thin film deposition, photolithography, etching, metallization, insulation, and passivation processes. These steps are performed with precision to create thin, precise, and reliable substrates.
What are the key design considerations for ultrathin CPU substrates?
Design considerations for ultrathin CPU substrates include material selection, thickness optimization, thermal management, signal integrity, manufacturability, mechanical stability, and compliance with industry standards.
What applications are ultrathin CPU substrates used in?
Ultrathin CPU substrates are used in a wide range of electronic devices, including smartphones, tablets, laptops, wearables, IoT devices, and other compact or thin-profile devices where space is limited.
How do ultrathin CPU substrates contribute to device performance?
Ultrathin CPU substrates contribute to device performance by enabling miniaturization, improving thermal management, enhancing electrical connectivity, and supporting high-speed signal transmission, ultimately leading to faster and more efficient operation.
What are the quality and reliability considerations for ultrathin CPU substrates?
Quality and reliability considerations include material quality, dimensional accuracy, electrical performance, thermal stability, mechanical durability, and compliance with industry standards to ensure long-term reliability and performance.
Can ultrathin CPU substrates be customized for specific applications?
Yes, ultrathin CPU substrates can be customized for specific applications by adjusting factors such as material composition, thickness, design features, and electrical properties to meet the unique requirements of the application.
Where can I find suppliers of ultrathin CPU substrates?
Suppliers of ultrathin CPU substrates can be found through electronic component distributors, semiconductor manufacturers, specialized substrate manufacturers, and online marketplaces catering to the electronics industry.