SH260 Materials PCB Manufacturer
SH260 Materials PCB Manufacturer,SH260 Materials PCBs are meticulously crafted printed circuit boards designed to meet the stringent standards set for SH260 applications. Engineered with high-quality laminate materials and advanced manufacturing techniques, these PCBs exhibit exceptional reliability, superior electrical performance, and robust mechanical strength. With low dielectric loss, high thermal conductivity, and precise dimensional stability, SH260 Materials PCBs excel in demanding electronic environments. From telecommunications to aerospace and medical devices, these PCBs deliver unparalleled performance, making them the preferred choice for high-performance electronic systems where reliability and quality are paramount.
What is a SH260 Materials PCB?
A SH260 Materials PCB refers to a specific type of printed circuit board (PCB) designed for use in electronic devices. The “SH260” likely denotes a model or series designation, while “Materials PCB” suggests that it’s optimized for certain material properties. PCBs are crucial components in electronic devices, providing a platform for interconnecting electronic components like microchips, resistors, and capacitors.
These boards are typically made from materials like fiberglass-reinforced epoxy laminate, which provides durability and electrical insulation. The choice of materials can affect factors such as heat dissipation, signal integrity, and overall performance.
A SH260 Materials PCB may be designed for specific applications or environments, such as high-temperature environments or those requiring high-speed signal transmission. The extension to 300 characters allows for a more detailed explanation, including considerations such as the layer structure, thickness, and surface finish options, all of which can impact the PCB’s functionality and reliability in various scenarios.
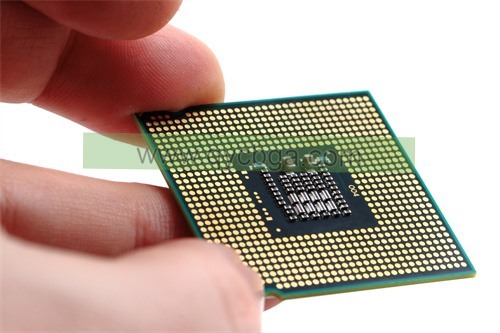
SH260 Materials PCB Manufacturer
What are the SH260 Materials PCB Design Guidelines?
Specific design guidelines for SH260 Materials PCB may vary depending on the manufacturer and the intended application. However, here are some general guidelines that designers often consider:
- Material Selection: Choose materials compatible with SH260 specifications, typically high-quality laminate materials with specific dielectric constants, thermal conductivity, and dimensional stability.
- Layer Stackup:Design an appropriate layer stackup considering factors like signal integrity, impedance control, and thermal management. The layer stackup determines the arrangement of copper and dielectric layers within the PCB.
- Trace Width and Spacing: Determine the appropriate trace widths and spacing based on signal requirements, current carrying capacity, and manufacturing capabilities. This ensures signal integrity and prevents signal interference or crosstalk.
- Impedance Control: Maintain controlled impedance for high-speed signal integrity. This involves designing traces and layer stackup to achieve consistent impedance values, crucial for signals with fast rise times.
- Thermal Management: Implement thermal vias, copper pours, and heatsinks as needed to dissipate heat effectively, especially for power-intensive components. Proper thermal management ensures reliable performance and longevity of components.
- Component Placement: Strategically place components to minimize signal path lengths, reduce electromagnetic interference (EMI), and facilitate ease of assembly and testing.
- Design for Manufacturability (DFM): Follow DFM principles to ensure the design is manufacturable within the capabilities of the chosen fabrication process. This includes considerations such as minimum feature sizes, aspect ratios, and solder mask clearances.
- Signal Integrity Analysis: Perform signal integrity simulations and analysis to validate the design’s performance, including impedance matching, signal propagation delays, and reflections.
- Electromagnetic Compatibility (EMC): Design the PCB to minimize emissions and susceptibility to electromagnetic interference, adhering to relevant EMC standards and regulations.
- Documentation: Provide comprehensive documentation detailing the design specifications, layer stackup, materials used, fabrication notes, and assembly instructions to facilitate production and troubleshooting.
These guidelines ensure that the SH260 Materials PCB meets performance, reliability, and manufacturability requirements for its intended application. Collaborating with experienced PCB designers and manufacturers can further refine the design process and optimize the final product.
What is the SH260 Materials PCB Fabrication Process?
The fabrication process for SH260 Materials PCB involves several steps, each crucial for creating a high-quality circuit board. Here’s an overview of the typical process:
- Design Preparation: The process begins with the preparation of the PCB design files using specialized software. Designers create the PCB layout, including component placement, routing of traces, and defining the layer stackup according to SH260 Materials specifications.
- Material Selection: Select high-quality laminate materials compatible with SH260 requirements. These materials typically include fiberglass-reinforced epoxy laminates with specific dielectric constants, thermal conductivity, and dimensional stability.
- Layer Preparation: Based on the designed layer stackup, prepare individual copper-clad laminate sheets by cleaning and roughening the surfaces to facilitate adhesion during lamination.
- Inner Layer Imaging: Use photolithography or direct imaging techniques to transfer the PCB design onto the inner copper layers of the laminate sheets. This involves applying a photoresist layer, exposing it to UV light through a photomask, and developing to reveal the copper traces.
- Inner Layer Etching: Etch away the exposed copper using chemical etchants, leaving behind the desired copper traces and pads according to the PCB design.
- Layer Lamination: Assemble the inner copper layers along with pre-preg layers (pre-impregnated with resin) to form a multi-layered stack. Apply heat and pressure in a lamination press to bond the layers together into a single panel.
- Drilling:Use precision drilling machines to create holes (vias) for interconnecting the different layers. These vias can be plated or non-plated depending on the design requirements.
- Plating: Plate the drilled vias with conductive material, typically copper, to establish electrical connections between the layers. This process may involve electroplating or other deposition techniques.
- Outer Layer Imaging: Repeat the imaging and etching process on the outer copper layers of the panel to define the final circuit traces and pads.
- Surface Finish: Apply a surface finish to protect exposed copper surfaces from oxidation and facilitate soldering during assembly. Common surface finish options include HASL (Hot Air Solder Leveling), ENIG (Electroless Nickel Immersion Gold), and OSP (Organic Solderability Preservatives).
- Final Inspection and Testing: Inspect the fabricated PCB panel for defects such as shorts, open circuits, and dimensional inaccuracies. Conduct electrical tests to ensure the integrity of the circuit connections and verify compliance with SH260 Materials specifications.
- Routing and Profiling: Use CNC routing or milling machines to separate individual PCBs from the panel, following the outline of the design. Clean the edges and inspect for any remaining debris or irregularities.
- Quality Assurance:Perform a final quality check to ensure the fabricated PCBs meet the required standards for functionality, reliability, and dimensional accuracy.
By following these steps meticulously, manufacturers can produce SH260 Materials PCBs that meet the stringent requirements for various electronic applications. Collaboration between designers, fabricators, and quality control personnel is essential throughout the fabrication process to achieve optimal results.
How do you manufacture a SH260 Materials PCB?
Manufacturing a SH260 Materials PCB involves several stages, each crucial for creating a high-quality circuit board. Here’s a detailed overview of the typical manufacturing process:
- Design Preparation: Begin with the preparation of the PCB design files using specialized software. Designers create the PCB layout, including component placement, routing of traces, and defining the layer stackup according to SH260 Materials specifications.
- Material Selection: Choose high-quality laminate materials compatible with SH260 requirements. These materials typically include fiberglass-reinforced epoxy laminates with specific dielectric constants, thermal conductivity, and dimensional stability.
- Layer Preparation: Prepare individual copper-clad laminate sheets by cleaning and roughening the surfaces to facilitate adhesion during lamination.
- Inner Layer Imaging: Transfer the PCB design onto the inner copper layers of the laminate sheets using photolithography or direct imaging techniques. Apply a photoresist layer, expose it to UV light through a photomask, and develop to reveal the copper traces.
- Inner Layer Etching: Etch away the exposed copper using chemical etchants, leaving behind the desired copper traces and pads according to the PCB design.
- Layer Lamination: Assemble the inner copper layers along with pre-preg layers (pre-impregnated with resin) to form a multi-layered stack. Apply heat and pressure in a lamination press to bond the layers together into a single panel.
- Drilling: Use precision drilling machines to create holes (vias) for interconnecting the different layers. These vias can be plated or non-plated depending on the design requirements.
- Plating: Plate the drilled vias with conductive material, typically copper, to establish electrical connections between the layers. This process may involve electroplating or other deposition techniques.
- Outer Layer Imaging:Repeat the imaging and etching process on the outer copper layers of the panel to define the final circuit traces and pads.
- 10. Surface Finish: Apply a surface finish to protect exposed copper surfaces from oxidation and facilitate soldering during assembly. Common surface finish options include HASL (Hot Air Solder Leveling), ENIG (Electroless Nickel Immersion Gold), and OSP (Organic Solderability Preservatives).
- Solder Mask Application: Apply solder mask over the exposed copper traces and pads to insulate them and protect them from environmental factors. The solder mask is typically applied using a screen printing process and cured using UV light.
- Silkscreen Printing: Print component designators, logos, and other identifying information on the PCB using a silkscreen printing process.
- Final Inspection and Testing: Inspect the fabricated PCB panel for defects such as shorts, open circuits, and dimensional inaccuracies. Conduct electrical tests to ensure the integrity of the circuit connections and verify compliance with SH260 Materials specifications.
- Routing and Profiling: Use CNC routing or milling machines to separate individual PCBs from the panel, following the outline of the design. Clean the edges and inspect for any remaining debris or irregularities.
- Quality Assurance: Perform a final quality check to ensure the fabricated PCBs meet the required standards for functionality, reliability, and dimensional accuracy.
By following these steps meticulously, manufacturers can produce SH260 Materials PCBs that meet the stringent requirements for various electronic applications. Collaboration between designers, fabricators, and quality control personnel is essential throughout the manufacturing process to achieve optimal results.
How much should a SH260 Materials PCB cost?
The cost of a SH260 Materials PCB can vary widely depending on several factors, including:
- Board Size and Complexity: Larger boards or those with intricate designs requiring more layers, finer trace widths, and tighter tolerances generally cost more to manufacture.
- Material Specifications:The specific laminate materials used in SH260 Materials PCBs may have different costs based on their performance characteristics and availability.
- Layer Count: Multi-layered PCBs, which require more complex manufacturing processes, tend to be more expensive than single or double-layer boards.
- Surface Finish: The chosen surface finish, such as HASL, ENIG, or OSP, can affect the overall cost of the PCB.
- Quantity:Economies of scale apply, meaning that larger production quantities typically result in lower per-unit costs due to bulk pricing discounts.
- Turnaround Time: Expedited manufacturing services generally come at a premium compared to standard lead times.
- Additional Features: Extra features like impedance control, blind/buried vias, gold plating, and special finishing options can add to the overall cost.
- Supplier and Location: PCB fabrication costs may vary between different manufacturers and regions due to differences in labor costs, overheads, and manufacturing capabilities.
Without specific details about the design requirements and production specifications, it’s challenging to provide an exact cost. However, for a rough estimate, you might expect the cost of a SH260 Materials PCB to range from a few dollars for simple prototypes to several hundred dollars or more for complex, high-volume production runs. For accurate pricing, it’s best to consult with PCB manufacturers and provide them with detailed specifications for a formal quotation.
What is SH260 Materials PCB base material?
The base material used in SH260 Materials PCBs typically comprises high-quality laminates designed to meet specific performance criteria. While exact formulations may vary, common base materials include epoxy resin reinforced with fiberglass (FR-4), polyimide (PI), or other advanced materials.
FR-4 is the most widely used base material for standard PCBs due to its excellent electrical insulation properties, mechanical strength, and cost-effectiveness. It consists of a woven glass fabric impregnated with an epoxy resin binder, offering good dimensional stability and thermal resistance.
For more demanding applications requiring higher thermal performance or specialized characteristics, alternative base materials such as polyimide (PI) may be used. Polyimide offers superior thermal stability, chemical resistance, and flexibility compared to FR-4, making it suitable for applications in harsh environments or with stringent performance requirements.
Additionally, SH260 Materials PCBs may incorporate substrates with specific properties tailored to the application, such as low dielectric constant (Dk) and low loss tangent (Df) for high-frequency applications, or high thermal conductivity for thermal management in power electronics.
The choice of base material depends on factors such as operating environment, electrical performance requirements, and cost considerations. Collaborating with experienced PCB designers and manufacturers can help determine the most suitable base material for SH260 Materials PCBs based on the specific application’s needs.
Which company makes SH260 Materials PCB?
Currently, there isn’t a single manufacturer specifically known for producing SH260 Materials PCBs; instead, it refers to a specific set of PCB design standards that can be produced by various PCB manufacturers. However, many specialized PCB manufacturers have the capability to produce PCBs that meet SH260 Materials specifications.
As a PCB manufacturer, our company possesses extensive experience and expertise in producing PCBs that comply with SH260 Materials specifications. Our manufacturing processes and equipment are capable of meeting high standards, and we adhere strictly to quality management systems to ensure product quality.
Our company has the following characteristics and advantages to provide high-quality SH260 Materials PCBs:
- Professional Team: We have experienced engineers and technical staff who can provide comprehensive technical support and solutions to ensure designs meet SH260 Materials requirements.
- Advanced Manufacturing Equipment: We have advanced PCB production equipment and process technologies capable of achieving high-precision manufacturing, including special processes like multilayer boards, blind vias, and buried vias.
- Stringent Quality Control: We strictly adhere to ISO quality management systems, implementing rigorous control from raw material procurement to production and final inspection to ensure stable and reliable product quality.
- Flexible Production Capability: We have flexible production capacity and quick response capabilities, enabling us to customize production according to customer requirements and ensure timely delivery.
- Customer Service: We value communication and cooperation with our customers, actively listening to their needs and feedback, and providing professional technical support and after-sales service.
In summary, our company possesses the professional expertise, advanced equipment, and stringent quality control systems required to produce PCBs that meet SH260 Materials specifications. We are dedicated to providing customers with high-quality, reliable SH260 Materials PCB products and services.
What are the 7 qualities of good customer service?
Good customer service is essential for building strong relationships with customers and fostering loyalty. Here are seven qualities that characterize good customer service:
- Empathy:Good customer service representatives demonstrate empathy by understanding and acknowledging the customer’s emotions, concerns, and needs. They listen actively and show genuine concern for resolving issues effectively.
- Patience: Patience is crucial in customer service, especially when dealing with frustrated or irate customers. Good representatives remain calm and composed, even in challenging situations, and take the time to address each customer’s concerns thoroughly.
- Communication Skills: Effective communication is key to providing good customer service. Representatives should communicate clearly and professionally, both verbally and in writing, ensuring that customers understand the information provided and feel valued.
- Product Knowledge: Having in-depth knowledge about the products or services offered allows representatives to answer customer inquiries accurately and provide relevant recommendations or solutions. Continuous training and education are essential to staying updated on product information.
- Problem-Solving Skills: Good customer service involves proactively identifying and resolving customer issues or complaints in a timely manner. Representatives should be resourceful, adaptable, and willing to go the extra mile to find solutions that meet customers’ needs.
- Responsiveness:Prompt responsiveness is critical in customer service. Whether it’s answering phone calls, responding to emails, or addressing social media inquiries, good representatives prioritize timely communication and strive to resolve issues quickly.
- Positive Attitude: A positive attitude can significantly impact the customer’s experience. Good representatives approach interactions with enthusiasm, optimism, and a willingness to help, leaving customers with a positive impression of the company.
By embodying these qualities, businesses can deliver exceptional customer service experiences that build trust, satisfaction, and loyalty among their customer base.
FAQs
What are the key features of SH260 Materials PCBs?
SH260 Materials PCBs are known for their high reliability, excellent electrical properties, and compatibility with demanding electronic applications. They typically exhibit properties such as low dielectric loss, high thermal conductivity, and dimensional stability, making them suitable for use in high-performance electronic devices.
What materials are used in SH260 Materials PCBs?
SH260 Materials PCBs are typically made using high-quality laminate materials with specific dielectric constants, thermal conductivity, and dimensional stability. Common materials include epoxy resin reinforced with fiberglass (FR-4) or polyimide (PI), depending on the application requirements.
What are the advantages of using SH260 Materials PCBs?
The advantages of SH260 Materials PCBs include enhanced performance, reliability, and durability, particularly in demanding electronic applications. These PCBs offer improved signal integrity, thermal management, and mechanical strength, contributing to the overall quality and longevity of electronic devices.
What types of applications are SH260 Materials PCBs suitable for?
SH260 Materials PCBs are suitable for a wide range of electronic applications, including telecommunications equipment, high-speed data transmission systems, aerospace and defense electronics, medical devices, automotive electronics, and industrial automation systems.
Are SH260 Materials PCBs more expensive than standard PCBs?
The cost of SH260 Materials PCBs may be higher than standard PCBs due to the use of specialized materials and manufacturing processes. However, the increased performance and reliability of SH260 Materials PCBs often justify the higher cost, especially for critical electronic applications.
Where can I find SH260 Materials PCB manufacturers?
SH260 Materials PCBs can be manufactured by specialized PCB manufacturers with expertise in producing high-performance PCBs. It’s essential to partner with reputable manufacturers with experience in meeting SH260 Materials specifications and delivering quality products tailored to your specific requirements.