Rogers RO4350B PCB Manufacturer
Rogers RO4350B PCB Manufacturer,The Rogers RO4350B PCB is a high-frequency circuit board manufactured using Rogers Corporation’s proprietary RO4350B high-frequency material. Its excellent electrical performance and stable dielectric constant make it highly favored in high-frequency applications. The RO4350B PCB exhibits outstanding signal transmission characteristics and low loss, suitable for wireless communications, radar systems, satellite communications, and other high-frequency fields. Its material composition and precision manufacturing ensure reliability and performance stability, making it an ideal choice for high-frequency circuit design.
What is a Rogers RO4350B PCB?
The Rogers RO4350B is a type of high-frequency laminate material used in PCB (Printed Circuit Board) fabrication. It’s engineered to meet the demanding requirements of RF (Radio Frequency) and microwave circuits.
RO4350B is renowned for its exceptional electrical properties, including low dielectric loss, tight dimensional stability, and consistent mechanical strength across a wide range of frequencies. These characteristics make it suitable for applications where signal integrity and reliability are paramount, such as in wireless communication systems, radar systems, and aerospace technology.
In terms of construction, RO4350B typically consists of a ceramic-filled hydrocarbon material with woven fiberglass reinforcement. This composition enables it to offer excellent thermal conductivity alongside its electrical properties, ensuring efficient heat dissipation in high-power applications.
PCBs made with RO4350B are often used in high-frequency designs where signal integrity and performance are crucial. Its stable dielectric constant over temperature, low insertion loss, and minimal signal distortion make it an ideal choice for demanding RF and microwave applications.
Overall, the Rogers RO4350B PCB stands out for its reliability, consistency, and high-performance characteristics in high-frequency circuit designs.
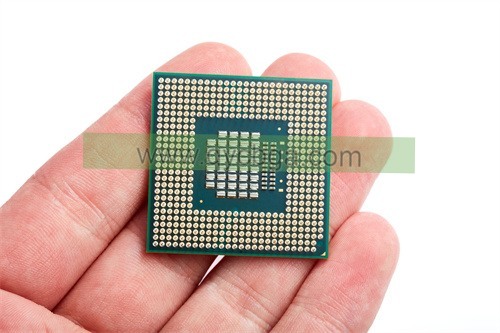
Rogers RO4350B PCB Manufacturer
What are the Rogers RO4350B PCB Design Guidelines?
Designing PCBs with Rogers RO4350B requires attention to specific guidelines to ensure optimal performance and reliability. Here are some general design guidelines:
- Material Selection: Choose the appropriate thickness and copper weight based on your design requirements. RO4350B is available in various thicknesses, typically ranging from 10 mils to 125 mils, and copper weights ranging from 0.5 oz to 2 oz.
- Impedance Control: Maintain controlled impedance for signal integrity. Use trace width, spacing, and layer stackup to achieve the desired characteristic impedance for your transmission lines. The dielectric constant (Dk) of RO4350B is around 3.48.
- Copper Plating: Ensure proper copper plating thickness for impedance matching and thermal management. Follow manufacturer recommendations for copper plating processes.
- Signal Routing: Minimize signal distortion by keeping high-speed signal traces as short and direct as possible. Avoid sharp bends and acute angles in signal traces, as they can cause signal reflections and impedance mismatches.
- Grounding: Implement a solid ground plane for noise reduction and signal integrity. Connect all ground vias to the ground plane to minimize ground loops and reduce electromagnetic interference (EMI).
- Thermal Management:Provide adequate thermal relief for components connected to copper pours to facilitate heat dissipation. Consider using thermal vias to transfer heat away from high-power components.
- Component Placement: Optimize component placement to minimize signal path lengths and reduce parasitic capacitance and inductance. Place high-speed components close to each other and minimize vias in signal paths.
- Stackup Design: Design the PCB stackup carefully to achieve the desired impedance and signal integrity. Consider factors such as layer count, dielectric thickness, and material selection to meet performance requirements.
- Manufacturability: Ensure that your design is manufacturable by following standard PCB manufacturing guidelines. Consider factors such as minimum trace width/spacing, annular ring size, and solder mask clearance.
- Testing and Validation: Perform signal integrity simulations and prototype testing to validate the design before mass production. Use tools like signal integrity analysis software and vector network analyzers to verify impedance matching and signal integrity.
By following these guidelines, you can design PCBs with Rogers RO4350B that meet the demanding requirements of high-frequency applications while ensuring reliability and performance.
What is the Rogers RO4350B PCB Fabrication Process?
The fabrication process for PCBs using Rogers RO4350B involves several steps, similar to the fabrication of standard PCBs. Here’s an overview of the process:
- Material Preparation: Start by selecting the appropriate thickness of RO4350B laminate based on your design requirements. The laminate typically comes in sheets or panels. Ensure that the material is stored and handled properly to prevent damage or contamination.
- Layer Stackup Design: Determine the layer stackup configuration based on the number of layers required for your PCB design. Consider factors such as signal integrity, impedance control, and thermal management when designing the stackup. RO4350B is often used for high-frequency designs, so the stackup may include multiple signal and ground layers.
- Copper Cladding: Apply a thin layer of copper to one or both sides of the RO4350B laminate sheets. This can be done through processes such as electroplating or lamination. The thickness of the copper layer should be chosen according to the current carrying capacity and impedance requirements of the design.
- Laser Drilling: Laser drilling is used to create holes for vias and through-holes in the PCB. This process offers precision and flexibility, especially for high-density designs. Laser drilling parameters should be optimized to prevent damage to the RO4350B material.
- Through-hole Plating: After drilling, the holes are plated with copper to establish electrical connections between layers. This process typically involves electroplating or chemical deposition to deposit a thin layer of copper inside the holes.
- Etching: Use chemical etching to remove unwanted copper from the surface of the PCB, leaving behind the desired circuit traces and patterns. Etching is usually performed using an etching solution that selectively dissolves the exposed copper.
- Solder Mask Application:Apply a solder mask over the surface of the PCB to protect the copper traces and prevent solder bridges during assembly. The solder mask is typically applied using a screen printing or spray coating process.
- Silkscreen Printing:Optionally, add component markings, reference designators, and other identifying information to the PCB using silkscreen printing. This step helps during assembly and troubleshooting.
- Surface Finish: Apply a surface finish to the exposed copper surfaces to improve solderability, prevent oxidation, and enhance durability. Common surface finishes for RO4350B PCBs include ENIG (Electroless Nickel Immersion Gold), HASL (Hot Air Solder Leveling), and immersion silver.
- Quality Inspection: Inspect the fabricated PCBs for defects, such as shorts, opens, or insufficient copper coverage. Use automated optical inspection (AOI) or visual inspection techniques to ensure the quality and integrity of the PCBs.
Once the fabrication process is complete, the PCBs are ready for assembly, where components are soldered onto the board to create the final electronic assembly.
How do you Manufacture a Rogers RO4350B PCB?
Manufacturing a Rogers RO4350B PCB involves several steps. Here’s a simplified overview:
- Design: Create the PCB layout using software like Altium Designer, Eagle, or KiCad. Ensure that the design meets the specifications required for the Rogers RO4350B material, including layer stackup, trace widths, and spacing.
- Material Selection: Choose the Rogers RO4350B laminate material for your PCB. This material has specific dielectric constant (εr) and loss tangent (tan δ) properties that make it suitable for high-frequency applications.
- Preparation of Substrate: Cut the RO4350B laminate sheets to the desired size for your PCB. Clean the substrate surface to remove any contaminants that could affect adhesion during the manufacturing process.
- Copper Cladding: Apply a thin layer of copper to one or both sides of the RO4350B substrate using techniques like lamination, electroplating, or sputtering. This copper layer will form the conductive traces and pads on the PCB.
- Photoresist Application: Apply a layer of photoresist material to the copper-clad substrate. The photoresist will be used to transfer the PCB layout onto the copper layer.
- Exposure and Development: Expose the photoresist to UV light through a mask that contains the PCB layout. The areas exposed to light will harden, while the unexposed areas will remain soluble. Develop the board to remove the unexposed photoresist, revealing the copper traces pattern.
- Etching: Submerge the board in an etchant solution (typically ferric chloride or ammonium persulfate) to remove the unwanted copper from the board, leaving behind the desired traces and pads.
- Strip Photoresist: Remove the remaining photoresist from the board using a stripping solution, leaving behind clean copper traces and pads.
- Drilling: Drill holes at specified locations for through-hole components and vias using a CNC drilling machine. Alternatively, laser drilling can be used for high-precision applications.
- Plating: Plate the drilled holes with copper to create electrical connections between layers (for multilayer PCBs) or to reinforce the holes for component mounting.
- Surface Finish: Apply a surface finish to protect the copper traces from oxidation and facilitate soldering. Common surface finishes include HASL (Hot Air Solder Leveling), ENIG (Electroless Nickel Immersion Gold), and OSP (Organic Solderability Preservatives).
- Silkscreen Printing: Optionally, apply a silkscreen layer on top of the PCB for component labeling and other markings.
- Testing: Perform electrical tests, such as continuity checks and impedance measurements, to ensure the PCB meets the design specifications.
- Assembly: Mount components onto the PCB using pick-and-place machines or by hand soldering, depending on the complexity of the assembly.
- Quality Control:Inspect the assembled PCBs for defects, such as solder bridges, missing components, or misaligned parts.
- Final Testing: Conduct functional tests on the assembled PCBs to verify proper operation before packaging and shipment.
Throughout the manufacturing process, it’s essential to adhere to industry standards and best practices to ensure the quality and reliability of the final product.
How Much Should a Rogers RO4350B PCB Cost?
The cost of a Rogers RO4350B PCB can vary significantly depending on several factors:
- Board Size: Larger PCBs require more material and production time, resulting in higher costs.
- Complexity: PCBs with intricate designs, dense component placement, and fine traces require more advanced manufacturing processes and may cost more to produce.
- Layer Count: The number of layers in the PCB affects manufacturing complexity and cost. Multilayer boards are typically more expensive than single-layer or double-layer boards.
- Material Cost: Rogers RO4350B is a specialized high-frequency laminate material, which can be more expensive than standard FR4 or other PCB substrates.
- Surface Finish: The chosen surface finish (e.g., HASL, ENIG, OSP) can impact the cost of the PCB.
- Quantities: Bulk orders typically result in lower per-unit costs due to economies of scale. However, smaller quantities may incur setup fees or higher per-unit costs.
- Lead Time: Expedited production schedules often come with additional costs compared to standard lead times.
- Additional Services: Services such as impedance control, controlled impedance testing, and quality certifications may incur extra charges.
As a rough estimate, the cost of a Rogers RO4350B PCB can range from a few dollars for simple designs to hundreds or even thousands of dollars for complex, high-frequency, or high-volume production runs. It’s best to consult with PCB manufacturers or use online quotation tools to get accurate pricing based on your specific requirements.
What is Rogers RO4350B PCB Base Material?
Rogers RO4350B is a high-frequency laminate material used for manufacturing printed circuit boards (PCBs). It is a type of ceramic-filled hydrocarbon laminate, which means it consists of a hydrocarbon resin system reinforced with woven glass fabric and ceramic filler particles.
The base material of Rogers RO4350B PCBs typically includes the following components:
- Hydrocarbon Resin System: This serves as the matrix that binds the reinforcement materials together. It provides mechanical strength, dimensional stability, and electrical insulation.
- Woven Glass Fabric:Glass fabric layers are embedded within the resin system to provide reinforcement and mechanical strength to the laminate. The glass fabric also helps maintain dimensional stability and enhances the PCB’s durability.
- Ceramic Filler Particles: Ceramic filler particles, usually composed of a ceramic material like alumina (Al2O3), are dispersed within the resin system. These filler particles help control the dielectric constant (εr) and loss tangent (tan δ) of the laminate, making it suitable for high-frequency applications.
- Copper Foil: Copper foil is bonded to one or both sides of the laminate to create conductive layers for the PCB traces and pads.
Rogers RO4350B is known for its excellent electrical performance, low loss, and stable dielectric properties over a wide frequency range, making it a preferred choice for high-frequency RF/microwave applications, such as telecommunications, aerospace, and automotive radar systems.
Which Company Makes Rogers RO4350B PCB?
The manufacture of Rogers RO4350B PCBs involves Rogers Corporation, an American high-tech company dedicated to the development and production of high-performance materials solutions. Rogers Corporation offers a range of high-frequency materials, including the RO4000 series, among which RO4350B is one.
Our company is also capable of producing Rogers RO4350B PCBs. As a professional PCB manufacturer, we possess advanced production equipment and technology, and our team has extensive experience and expertise to meet customers’ demands for high-frequency PCBs.
Our production process strictly adheres to industry standards and quality management systems, ensuring that each production step meets the highest standards. We utilize advanced materials and processes to ensure that RO4350B PCBs exhibit excellent electrical performance, stable dielectric constants, and low loss, meeting the requirements of high-frequency applications.
Furthermore, we offer customized solutions, designing and manufacturing according to customers’ specific requirements, including different layers, sizes, surface treatments, and special processes.
We are committed to providing customers with high-quality, reliable RO4350B PCBs at competitive prices and with timely delivery. Whether in small batches or large-scale production, we are able to provide satisfactory solutions to customers and establish long-term cooperative relationships.
What are the 7 Qualities of Good Customer Service?
Good customer service is characterized by several key qualities that contribute to positive interactions and experiences for customers. Here are seven qualities of good customer service:
- Responsiveness: A good customer service team is responsive and timely in addressing customer inquiries, concerns, and issues. They prioritize prompt communication and strive to provide timely solutions to customer problems.
- Empathy: Empathy involves understanding and relating to the emotions and perspectives of customers. Good customer service representatives demonstrate empathy by actively listening to customers, acknowledging their feelings, and showing genuine concern for their needs.
- Knowledgeability: Customer service staff should be knowledgeable about the products or services they support. They should possess a deep understanding of the company’s offerings, policies, and procedures, enabling them to provide accurate information and effective assistance to customers.
- Professionalism: Professionalism encompasses traits such as courtesy, politeness, and professionalism in demeanor and communication. Good customer service representatives maintain a professional attitude at all times, even in challenging or stressful situations.
- Flexibility: Flexibility involves adapting to customers’ individual needs and preferences. Good customer service teams are flexible in their approach, willing to accommodate special requests, and capable of finding creative solutions to meet customer requirements.
- Problem-Solving Skills: Good customer service representatives possess strong problem-solving skills, enabling them to effectively address customer issues and resolve conflicts. They approach challenges with a positive attitude, seeking practical solutions that satisfy customers and uphold the company’s reputation.
- Consistency: Consistency is crucial for building trust and loyalty with customers. Good customer service is consistent across all interactions and touchpoints, ensuring that customers receive the same level of service excellence every time they engage with the company.
By embodying these qualities, organizations can deliver exceptional customer service experiences that foster customer satisfaction, loyalty, and advocacy.
FAQs
What is Rogers RO4350B PCB used for?
Rogers RO4350B PCB is used in high-frequency applications such as RF and microwave circuits, telecommunications, and high-speed digital designs.
How does Rogers RO4350B compare to FR4?
RO4350B offers better high-frequency performance, lower dielectric loss, and better thermal stability compared to standard FR4 material.
Can you provide prototypes of Rogers RO4350B PCB?
Yes, we offer prototype services for Rogers RO4350B PCBs to help you validate your designs before full-scale production.
What is the lead time for Rogers RO4350B PCB manufacturing?
Lead times can vary based on the complexity of the design and order volume, but typical lead times range from 2 to 4 weeks.
Do you offer design assistance for Rogers RO4350B PCB?
Yes, our engineering team can provide design support to ensure your Rogers RO4350B PCB meets all performance requirements.
What quality control measures do you have in place for Rogers RO4350B PCBs?
We have stringent quality control measures, including electrical testing and visual inspections, to ensure the highest quality of our Rogers RO4350B PCBs.
What is the minimum order quantity for Rogers RO4350B PCBs?
We accommodate both small and large orders, with no strict minimum order quantity.