Rogers Antenna PCB Manufacturer
Rogers Antenna PCB Manufacturer,Rogers Antenna PCBs are specialized circuit boards crafted from Rogers Corporation’s high-performance materials, optimized for antenna applications. These PCBs feature low dielectric constant and loss tangent properties, crucial for maintaining signal integrity and minimizing interference. Rogers Antenna PCBs are designed with precision to include microstrip or stripline configurations, ensuring efficient RF signal transmission and reception. They are utilized extensively in telecommunications, aerospace, and IoT devices where reliable antenna performance is essential. Rogers Antenna PCBs contribute to compact, lightweight antenna designs that offer high gain and excellent radiation efficiency, supporting advanced wireless communication technologies across diverse industries.
What is a Rogers Antenna PCB?
A Rogers Antenna PCB refers to a printed circuit board (PCB) that utilizes materials manufactured by Rogers Corporation, a well-known supplier of high-frequency laminates and materials used in RF (radio frequency) and microwave applications. Rogers materials are valued for their excellent electrical properties, such as low dielectric constant, low loss tangent, and high thermal conductivity, which are crucial for efficient antenna design.
Antennas designed on Rogers PCBs typically exhibit better performance in terms of signal transmission, reception, and overall reliability compared to antennas on standard PCBs. These PCBs are often used in industries where RF performance is critical, such as telecommunications, aerospace, defense, and automotive sectors.
Designers prefer Rogers materials for antennas because they enable precise control over signal propagation and interference, leading to enhanced antenna efficiency and range. The choice of Rogers materials also facilitates miniaturization and integration of antennas into compact electronic devices without sacrificing performance.
Overall, a Rogers Antenna PCB represents a specialized circuit board optimized for RF applications, leveraging advanced materials to achieve superior antenna performance in various technological applications.
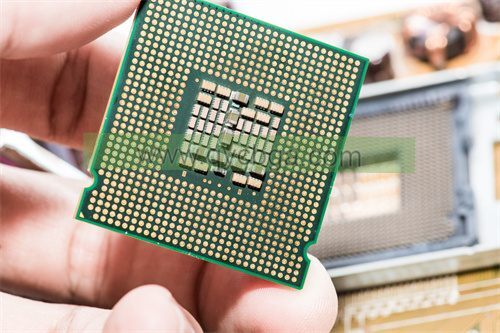
Rogers Antenna PCB Manufacturer
What are the Rogers Antenna PCB Design Guidelines?
Designing antennas on Rogers PCBs involves adhering to specific guidelines to ensure optimal performance and reliability. Here are some key Rogers antenna PCB design guidelines:
- Material Selection: Choose the appropriate Rogers material based on the frequency range, dielectric constant, and thermal properties required for the antenna design. Common materials include Rogers RO3000 series, RO4000 series, and RO5000 series, each tailored for different applications.
- Dielectric Thickness: The thickness of the Rogers laminate affects the antenna’s impedance and bandwidth. Designers should select a thickness that aligns with the desired electrical characteristics and mechanical requirements.
- Ground Plane Design: Ensure a continuous and well-defined ground plane beneath the antenna elements. The ground plane helps to maintain antenna efficiency, reduces radiation losses, and improves impedance matching.
- Antenna Placement: Place the antenna on the PCB with consideration for surrounding components and structures. Avoid placing large metal components or traces near the antenna as they can affect radiation patterns and impedance.
- Transmission Line Design: Use appropriate transmission line structures (like microstrip or coplanar waveguide) to feed the antenna elements. Maintain consistent impedance along the transmission lines to minimize reflection losses.
- Component Layout: Carefully layout the components on the PCB to minimize interference with antenna operation. Components emitting noise or electromagnetic interference should be placed away from sensitive antenna regions.
- Antenna Size and Shape: Design the antenna elements according to the desired frequency band and radiation pattern requirements. Rogers PCBs allow for precise shaping of antenna elements to achieve optimal performance.
- Stackup Considerations: Plan the PCB stackup carefully to ensure proper impedance control and signal integrity. Rogers materials typically require specific layer thicknesses and dielectric constants in the PCB stackup.
- Environmental Considerations: Anticipate the operating environment of the device and design the PCB to withstand temperature variations, humidity, and other environmental factors that could affect antenna performance.
- Testing and Validation: Perform thorough testing and validation of the antenna design on Rogers PCBs. Measure parameters such as return loss, VSWR (Voltage Standing Wave Ratio), radiation patterns, and efficiency to ensure compliance with design specifications.
By following these Rogers antenna PCB design guidelines, engineers can optimize antenna performance, achieve reliable operation, and meet the requirements of various RF and microwave applications.
What is the Rogers Antenna PCB Fabrication Process?
Fabricating a Rogers Antenna PCB involves several specialized steps to ensure the proper integration of Rogers materials and the precise construction necessary for high-frequency applications. Here’s an overview of the typical fabrication process:
- Material Selection: Choose the appropriate Rogers laminate based on the specific requirements of the antenna design, such as frequency range, dielectric constant, and thermal properties.
- Design Preparation: Develop the antenna PCB layout using CAD software. This includes defining the antenna geometry, placement of components, transmission lines, and ground planes. Ensure adherence to design guidelines for Rogers materials.
- Layer Stackup Design: Plan the layer stackup of the PCB, considering the number of layers required for the antenna design and the specific Rogers material properties needed for each layer.
- Circuit Imaging:Transfer the PCB design onto the Rogers laminate using photolithography. This involves applying a photoresist layer to the laminate, exposing it to UV light through a mask that contains the PCB pattern, and developing the exposed resist to reveal the circuit traces.
- Etching: Etch away the unwanted copper from the laminate surface using an appropriate etchant solution. This step defines the conductive pathways (traces) that form the antenna elements and transmission lines.
- Drilling: Drill holes in the PCB for component mounting and vias (interconnects between layers). The drill sizes and accuracy are critical to maintain signal integrity and mechanical stability.
- Plating: Plate the drilled holes with conductive material (typically copper) to create vias that connect different layers of the PCB. This ensures electrical continuity between layers and facilitates component interconnections.
- Surface Finish: Apply a suitable surface finish to protect the PCB from oxidation and facilitate soldering of components. Common surface finishes for Rogers PCBs include ENIG (Electroless Nickel Immersion Gold) or immersion silver.
- Solder Mask Application: Apply solder mask over the PCB surface, leaving openings for exposed pads and vias. Solder mask protects the PCB from environmental factors and prevents solder bridges during component assembly.
- Component Placement: Mount the electronic components onto the PCB using pick-and-place machines. Ensure precise placement according to the design specifications to maintain antenna performance.
- Soldering:Solder the components onto the PCB using reflow soldering techniques. Rogers materials typically require controlled soldering temperatures to prevent damage to the laminate and ensure reliable solder joints.
- Testing and Inspection: Perform electrical testing (e.g., continuity, impedance measurements) and visual inspection to verify the integrity and functionality of the Rogers antenna PCB. Test for parameters such as return loss, VSWR, and radiation patterns to ensure compliance with design requirements.
- Packaging: Depending on the application, package the finished PCB into its final form, which may involve additional enclosure or integration into a larger system.
Throughout the Rogers antenna PCB fabrication process, careful attention to material handling, process control, and quality assurance is crucial to achieve the desired RF performance and reliability. Specialized equipment and expertise in high-frequency PCB manufacturing are often required to ensure optimal results for antennas operating in demanding applications.
How do you manufacture a Rogers Antenna PCB?
Manufacturing a Rogers Antenna PCB involves a series of specialized steps to ensure high-quality construction suitable for RF and microwave applications. Here’s a detailed outline of the manufacturing process:
- Material Selection: Choose the appropriate Rogers laminate based on the specific requirements such as frequency range, dielectric constant, and thermal properties. Common series include RO3000, RO4000, and RO5000, each suited for different frequencies and performance levels.
- Design Preparation: Develop the PCB layout using CAD software tailored for high-frequency designs. Define the antenna geometry, component placement, transmission lines, and ground planes according to design specifications and Rogers material guidelines.
- Layer Stackup Design: Plan the layer stackup considering the number of layers required for the antenna design. Rogers materials often require specific dielectric thicknesses and configurations to maintain signal integrity and impedance control.
- Circuit Imaging: Transfer the PCB design onto the Rogers laminate using photolithography. Apply a photosensitive resist layer to the laminate, expose it to UV light through a mask containing the PCB pattern, and develop the resist to reveal the circuit traces.
- Etching:Etch away the exposed copper from the laminate surface using an appropriate etchant solution. This step defines the conductive pathways (traces) that form the antenna elements and transmission lines.
- Drilling: Drill holes in the PCB for component mounting and vias (interconnects between layers). Precise drilling is essential to maintain signal integrity and mechanical stability in high-frequency applications.
- Plating: Plate the drilled holes with conductive material (usually copper) to create vias that connect different layers of the PCB. This ensures electrical continuity and facilitates component interconnections across multiple layers.
- Surface Finish: Apply a suitable surface finish to protect the PCB from oxidation and facilitate soldering. Common finishes for Rogers PCBs include ENIG (Electroless Nickel Immersion Gold) or immersion silver, chosen for their compatibility with high-frequency signals.
- Solder Mask Application: Apply solder mask over the PCB surface, leaving openings for exposed pads and vias. Solder mask protects the PCB from environmental factors and prevents solder bridges during component assembly.
- Component Placement: Use automated pick-and-place machines to accurately mount electronic components onto the PCB. Place components according to the design layout to ensure optimal antenna performance and functionality.
- Soldering: Solder the components onto the PCB using controlled reflow soldering processes. Rogers materials require careful temperature management during soldering to prevent damage and ensure reliable electrical connections.
- Testing and Inspection: Conduct rigorous electrical testing and visual inspection to verify the integrity and functionality of the Rogers antenna PCB. Test for parameters such as impedance matching, signal continuity, and RF performance characteristics (e.g., return loss, VSWR).
- Quality Assurance: Implement quality checks throughout the manufacturing process to ensure adherence to design specifications and industry standards for RF and microwave PCBs.
- Packaging:Depending on the application, package the finished Rogers antenna PCB into its final form. This may involve additional enclosure or integration into larger electronic systems.
By following these manufacturing steps with precision and attention to detail, engineers and manufacturers can produce Rogers antenna PCBs that meet stringent performance requirements for telecommunications, aerospace, defense, automotive, and other high-frequency applications.
How much should a Rogers Antenna PCB cost?
The cost of a Rogers Antenna PCB can vary widely depending on several factors, including the following:
- Material Choice: Rogers materials come in various series (e.g., RO3000, RO4000, RO5000) with different performance characteristics and costs. Higher frequency and performance materials typically command higher prices.
- PCB Size and Complexity: Larger PCBs with more layers and complex designs require more materials and processing time, leading to higher costs.
- Layer Count: The number of layers in the PCB affects fabrication complexity and cost. Rogers PCBs often have multiple layers to accommodate RF and microwave designs.
- Trace Width and Spacing: RF designs often require precise control over trace width and spacing to maintain signal integrity. Tighter tolerances can increase fabrication costs.
- Surface Finish and Plating: Specialized surface finishes like ENIG (Electroless Nickel Immersion Gold) or immersion silver are common for Rogers PCBs and can affect cost.
- Quantity:Economies of scale apply in PCB manufacturing. Larger production runs typically reduce the cost per unit due to setup and tooling amortization.
- Lead Time: Urgent orders or shorter lead times may incur additional costs for expedited manufacturing.
As a rough estimate, the cost of a Rogers Antenna PCB can range from tens to hundreds of dollars per board, depending on the factors mentioned above. For a precise quote, it’s advisable to contact PCB manufacturers or suppliers specializing in Rogers materials and RF PCBs. They can provide detailed pricing based on specific design requirements, quantities, and production timelines.
What is Rogers Antenna PCB base material?
Rogers Antenna PCBs use specialized base materials manufactured by Rogers Corporation, a leading supplier of high-performance laminates for RF (radio frequency) and microwave applications. The base materials from Rogers Corporation are designed to meet the stringent requirements of high-frequency circuits, including antennas. Here are some key characteristics and types of Rogers base materials commonly used in antenna PCBs:
- RO3000 Series: This series includes laminates like RO3003, RO3006, RO3010, etc. They are characterized by low dielectric loss and stable electrical properties over a wide frequency range. RO3000 series materials are suitable for applications requiring high frequency performance and reliable signal transmission.
- RO4000 Series: Including materials such as RO4003C, RO4350B, RO4835, etc., the RO4000 series offers excellent dimensional stability, low loss, and good thermal management properties. These materials are ideal for antennas operating at microwave frequencies.
- RO5000 Series: This series comprises laminates like RO5000, RO5100, RO5250, etc. RO5000 series materials provide low dielectric constant and low loss tangent, making them suitable for high-frequency applications demanding minimal signal loss and high reliability.
- Other Specialty Materials: Rogers also offers specialty laminates tailored for specific performance requirements, such as high thermal conductivity for heat dissipation, or ultra-low dielectric constant for applications requiring precise impedance control.
These Rogers base materials are chosen for antenna PCBs due to their superior electrical properties, including low dielectric loss, stable dielectric constant, and excellent dimensional stability. They enable antennas to achieve efficient signal transmission, maintain desired impedance characteristics, and operate reliably across a wide range of frequencies. Designers select the appropriate Rogers material based on the specific application requirements, frequency bands, and environmental conditions in which the antenna will be deployed.
Which company makes Rogers Antenna PCBs?
Rogers Antenna PCBs are made from specialized substrates manufactured by Rogers Corporation, designed specifically for RF (radio frequency) and microwave applications. Rogers Corporation is a global leader in high-performance composite materials, offering various series of high-frequency substrates widely used in communications, aerospace, defense, automotive electronics, and other industries.
As a professional electronic manufacturing service provider, our company possesses the capability and experience to produce Rogers Antenna PCBs. We offer the following services:
- Professional Design Support: Our experienced engineering team provides professional support for antenna PCB design. We customize solutions according to customer requirements, whether it involves frequency range, impedance matching, or antenna shape and dimensions.
- Advanced Manufacturing Facilities: Equipped with state-of-the-art PCB manufacturing facilities and equipment, we handle complex multi-layer PCB designs and high-frequency RF circuit requirements. Our manufacturing process is meticulously controlled to ensure PCB electrical performance and mechanical stability meet design specifications.
- High-Quality Material Selection: We collaborate with reputable material suppliers to ensure the use of high-quality Rogers base materials. Depending on project requirements, we select appropriate materials from the RO3000, RO4000, or RO5000 series to ensure stability and excellent performance in high-frequency environments.
- Strict Quality Control: We implement a rigorous quality management system, conducting thorough inspections and tests at every stage from material procurement to manufacturing. Through electrical performance testing, imaging checks, and final acceptance tests, we ensure that every Rogers Antenna PCB produced meets customer requirements and international standards.
- Customized Production Capabilities: We accommodate both small and large volume production orders, supporting rapid delivery and flexible production scheduling. Whether for prototype development or mass production, we provide efficient production solutions tailored to customer needs.
With our professional capabilities and commitment, we meet customer demands for high-performance Rogers Antenna PCBs, providing reliable electronic solutions for various complex RF and microwave applications.
What are the 7 qualities of good customer service?
Good customer service is characterized by several key qualities that contribute to a positive and satisfying customer experience. Here are seven important qualities:
- Responsiveness: A good customer service team responds promptly to customer inquiries, concerns, and requests. This includes acknowledging customer communication in a timely manner and providing updates as needed.
- Empathy: Customer service representatives demonstrate empathy by understanding and acknowledging the customer’s feelings, perspectives, and challenges. They show genuine concern and strive to address issues from the customer’s point of view.
- Patience: Patience is crucial in customer service, especially when dealing with frustrated or upset customers. Patient representatives listen attentively, allow customers to express themselves fully, and work through issues without rushing.
- Clear Communication: Effective communication is essential. Customer service professionals articulate information clearly and concisely, avoiding jargon and ensuring that customers understand the information provided. They also listen actively to understand customer needs and expectations.
- Product Knowledge: Good customer service requires a deep understanding of the products or services offered. Representatives are knowledgeable about their company’s offerings, features, benefits, and troubleshooting procedures. This enables them to provide accurate information and solutions to customers.
- Problem-Solving Skills: Customer service involves resolving issues and addressing concerns effectively. Representatives use critical thinking and problem-solving skills to identify root causes, propose solutions, and follow through to ensure customer satisfaction.
- Professionalism: Professionalism encompasses various aspects such as courtesy, reliability, and maintaining a positive attitude. Customer service professionals conduct themselves with integrity, respect, and a commitment to providing excellent service.
By embodying these qualities, customer service teams can build trust, loyalty, and satisfaction among customers, ultimately contributing to the overall success and reputation of the organization.
FAQs
What are Rogers Antenna PCBs?
Rogers Antenna PCBs are printed circuit boards made using Rogers Corporation’s high-frequency laminates. These materials are optimized for RF and microwave applications, providing superior electrical properties.
Why are Rogers materials used for antenna PCBs?
Rogers materials are chosen for their low dielectric constant, low loss tangent, and high thermal conductivity, which are crucial for efficient signal transmission and reliable antenna performance in high-frequency applications.
Which Rogers materials are commonly used for antenna PCBs?
Commonly used Rogers materials include the RO3000, RO4000, and RO5000 series, each offering specific properties tailored to different frequency ranges and performance requirements.
What industries use Rogers Antenna PCBs?
Rogers Antenna PCBs are widely used in telecommunications, aerospace, defense, automotive electronics, and other industries where high-frequency signal integrity is essential.
Can you provide design support for Rogers Antenna PCBs?
Yes, our experienced engineering team offers professional design support, helping you with frequency range specifications, impedance matching, and optimal antenna geometry for your application.
What is the typical cost of a Rogers Antenna PCB?
The cost varies based on factors like material choice, PCB size, layer count, and production volume. For a precise quote, please contact us with your specific requirements.
What is the lead time for manufacturing Rogers Antenna PCBs?
Lead times depend on the complexity and quantity of the order. We offer flexible production scheduling and can provide expedited services if needed. Please contact us for detailed timelines based on your project.