What is SOP Package Substrate?
SOP Package Substrate Manufacturer,SOP (Small Outline Package) package substrate is a compact and streamlined packaging solution widely used in electronic devices where space efficiency is critical. Designed with a small footprint and thin profile, SOP substrates enable high-density mounting on circuit boards, making them ideal for portable electronics such as smartphones, tablets, and laptops. These substrates often feature fine pitch interconnects and are made from durable materials such as advanced polymers or ceramics to provide reliable electrical insulation and mechanical strength. The design of SOP package substrates focuses on minimizing package size while maximizing performance, offering enhanced thermal management and reduced signal loss for high-speed applications. This makes SOP an essential choice for designers aiming to optimize functionality in increasingly compact electronic devices.
SOP (Small Outline Package) is a type of integrated circuit (IC) package that is commonly used for surface-mount devices. It’s a compact and space-saving package designed to be mounted directly onto the surface of a printed circuit board (PCB). SOP packages typically have gull-wing or J-lead leads that extend from the sides of the package, allowing for easy soldering onto the PCB.
The substrate of an SOP package refers to the material upon which the integrated circuit is mounted and interconnected. The substrate serves as a foundation for the IC and provides electrical connections between the IC and the external circuitry on the PCB. The substrate material is usually a type of insulating material, such as ceramic or fiberglass, which provides mechanical support and electrical isolation for the IC.
In summary, the SOP package substrate is the material on which the integrated circuit is mounted within an SOP package, providing structural support and electrical connections for the IC within the package.
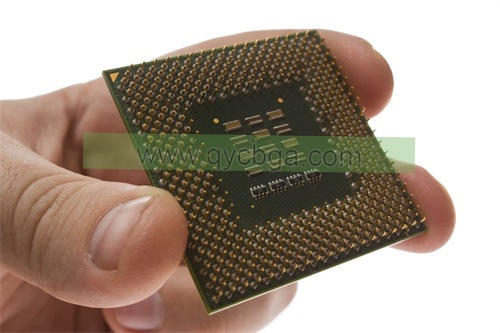
SOP Package Substrate Manufacturer
SOP Package Substrate design Reference Guide.
The design of the SOP (Small Outline Package) substrate is crucial for ensuring the reliable performance and manufacturability of integrated circuits (ICs) mounted within these packages. A comprehensive reference guide for SOP package substrate design typically covers various aspects to consider, including:
- Substrate Material Selection: Discussing the different types of substrate materials available for SOP packages, such as ceramic, fiberglass, or laminate materials. Each material has its own set of characteristics, including thermal conductivity, mechanical strength, and cost, which need to be considered based on the specific requirements of the IC and the application.
- Electrical Design Considerations: Providing guidelines for designing the electrical connections (traces) within the substrate to ensure optimal signal integrity, power distribution, and thermal management. This includes considerations for impedance control, power plane distribution, and minimizing parasitic effects such as signal crosstalk and ground bounce.
- Thermal Management: Addressing techniques for managing heat dissipation within the SOP package substrate to prevent overheating of the IC and ensure long-term reliability. This may involve the design of thermal vias, heat spreaders, and thermal pads to efficiently transfer heat away from the IC to the surrounding environment.
- Mechanical Design Guidelines: Offering recommendations for designing the mechanical aspects of the substrate, including the layout of mounting holes, component clearances, and overall package dimensions. This ensures compatibility with standard assembly processes and mechanical reliability during operation.
- Manufacturability Considerations: Discussing design considerations to facilitate the manufacturing process of SOP package substrates, such as panelization, solder mask design, and fiducial marker placement for automated assembly equipment.
- Signal Integrity and EMI Mitigation: Providing guidelines for minimizing signal distortion and electromagnetic interference (EMI) within the SOP package substrate through proper layout and grounding techniques. This includes considerations for signal routing, decoupling capacitor placement, and shielding strategies.
- Reliability and Testing: Addressing reliability concerns related to the SOP package substrate design, such as solder joint integrity, mechanical stress, and environmental factors. Guidelines for reliability testing and qualification of the substrate design may also be included.
By following the recommendations outlined in a comprehensive SOP package substrate design reference guide, designers can optimize the performance, reliability, and manufacturability of ICs mounted within SOP packages for various applications.
What are the materials used in SOP Package Substrate?
The materials used in SOP (Small Outline Package) substrates can vary depending on factors such as cost, performance requirements, and manufacturing processes. Some common materials used in SOP package substrates include:
- Ceramic: Ceramic substrates offer excellent thermal conductivity and mechanical strength, making them suitable for high-power applications where heat dissipation is critical. Alumina (Al2O3) and aluminum nitride (AlN) are commonly used ceramic materials for SOP substrates.
- Fiberglass: Fiberglass substrates, also known as FR4 (Flame Retardant 4), are composed of a fiberglass-reinforced epoxy laminate. FR4 substrates are cost-effective and widely used in consumer electronics and low- to mid-range applications.
- Laminate: Laminate substrates consist of multiple layers of insulating material, such as epoxy resin or polyimide, reinforced with fiberglass or other reinforcement materials. Laminate substrates offer good electrical insulation and mechanical properties and are commonly used in SOP packages for various applications.
- Polyimide: Polyimide substrates offer excellent thermal stability, flexibility, and resistance to chemicals and moisture. They are often used in flexible circuits and applications requiring high temperature resistance.
- Metal Core: Metal core substrates feature a layer of metal, such as aluminum or copper, sandwiched between layers of insulating material. Metal core substrates provide superior thermal conductivity and are suitable for high-power LED and power electronics applications.
- Copper: Copper substrates offer high thermal conductivity and are commonly used in high-power semiconductor devices and RF (radio frequency) applications where heat dissipation is critical.
These are some of the main materials used in SOP package substrates, each offering unique properties suited to different application requirements. Designers select the substrate material based on factors such as thermal performance, electrical properties, cost, and manufacturing feasibility.
How is SOP Package Substrate manufactured?
The manufacturing process for SOP (Small Outline Package) substrates involves several steps to create a durable and functional substrate for mounting integrated circuits (ICs). Below is a general outline of the manufacturing process:
- Substrate Material Preparation: The process begins with preparing the substrate material, which could be ceramic, fiberglass (FR4), laminate, metal core, or another suitable material. The material is typically supplied in sheets or panels of the desired thickness.
- Substrate Fabrication: The substrate material undergoes fabrication processes to create the desired shape and dimensions for the SOP package. This may involve cutting, drilling, and routing the material to form individual substrate units or panels.
- Surface Preparation: The surface of the substrate material is prepared for subsequent processing steps, such as cleaning to remove contaminants and applying surface treatments or coatings to improve adhesion and solderability.
- Circuit Pattern Formation: In this step, the circuit pattern for interconnecting the ICs and other components is formed on the substrate material. This can be achieved through various techniques such as screen printing, photolithography, or etching processes, depending on the substrate material and design requirements.
- Metallization: Metal layers are deposited onto the substrate surface to create the conductive traces and pads for electrical connections. Common metals used for metallization include copper, aluminum, and gold. The metal deposition process can involve techniques such as sputtering, electroplating, or chemical vapor deposition (CVD).
- Dielectric Layer Deposition: Insulating layers are deposited or laminated onto the substrate to insulate the conductive traces and provide electrical isolation between layers. These dielectric layers may consist of materials such as epoxy resin, polyimide, or other suitable insulating materials.
- Via Formation: Vias are created in the substrate to allow electrical connections between different layers or to provide thermal pathways for heat dissipation. Vias can be formed using drilling, laser ablation, or other techniques, followed by metallization to establish electrical continuity.
- Surface Finish: The substrate surface is finished to facilitate soldering of ICs and other components during assembly. Common surface finishes include solder mask application, which protects the substrate and defines soldering areas, and surface plating techniques such as electroless nickel immersion gold (ENIG) or hot air solder leveling (HASL).
- Quality Control and Testing: Throughout the manufacturing process, quality control measures are implemented to ensure the substrate meets specified tolerances and performance criteria. Testing may include visual inspection, electrical testing, and reliability testing to verify the integrity and functionality of the substrates.
- Packaging and Shipping: Once manufactured and tested, the SOP package substrates are packaged and prepared for shipping to assembly facilities where ICs and other components will be mounted onto them to complete the electronic assemblies.
Overall, the manufacturing process for SOP package substrates involves a combination of material preparation, fabrication, metallization, and quality control steps to produce high-quality substrates suitable for use in various electronic applications.
The Application area of SOP Package Substrate
SOP (Small Outline Package) substrates find applications across a wide range of industries and electronic devices due to their compact size, surface-mount capability, and versatility. Some common application areas of SOP package substrates include:
- Consumer Electronics: SOP package substrates are extensively used in consumer electronics devices such as smartphones, tablets, laptops, digital cameras, and wearable devices. They provide a compact and lightweight solution for mounting integrated circuits (ICs) and other electronic components in these portable devices.
- Telecommunications: SOP substrates are used in telecommunications equipment including routers, switches, modems, and base stations. They facilitate the assembly of high-density electronic circuits with reliable electrical connections, making them suitable for telecommunications infrastructure and networking applications.
- Automotive Electronics: In automotive electronics, SOP package substrates are employed in various applications such as engine control units (ECUs), airbag systems, infotainment systems, and advanced driver assistance systems (ADAS). They offer robust construction and thermal performance required for harsh automotive environments.
- Industrial Automation: SOP package substrates are utilized in industrial automation equipment, control systems, robotics, and machinery. They enable the integration of complex electronic circuits with efficient heat dissipation and reliable performance in demanding industrial environments.
- Medical Devices: SOP substrates are used in medical devices and equipment such as patient monitoring systems, diagnostic devices, imaging equipment, and medical implants. They provide compact and reliable solutions for mounting sensitive electronic components in medical applications.
- Aerospace and Defense: In aerospace and defense applications, SOP package substrates are employed in avionics systems, navigation equipment, radar systems, communications devices, and missile guidance systems. They offer rugged construction, high reliability, and resistance to extreme environmental conditions.
- Renewable Energy: SOP substrates are used in renewable energy systems such as solar inverters, wind turbine controllers, and battery management systems. They enable the efficient integration of power electronics and control circuits for renewable energy generation and storage.
- Consumer Appliances: SOP package substrates find applications in various household appliances including refrigerators, washing machines, dishwashers, microwave ovens, and air conditioners. They provide compact and cost-effective solutions for controlling and monitoring electronic functions in appliances.
Overall, SOP package substrates play a crucial role in enabling the miniaturization, performance, and reliability of electronic devices across a diverse range of industries and applications.
What are the advantages of SOP Package Substrate?
SOP (Small Outline Package) substrates offer several advantages that make them desirable for a wide range of electronic applications. Some of the key advantages include:
- Compact Size: SOP packages are designed to be small and compact, making them suitable for space-constrained applications where size is a critical factor. Their small form factor allows for high-density mounting of integrated circuits (ICs) and other components on printed circuit boards (PCBs), enabling miniaturization of electronic devices.
- Surface-Mount Capability: SOP packages are surface-mountable, meaning they can be directly mounted onto the surface of PCBs without the need for through-holes. This surface-mount capability simplifies the assembly process, reduces manufacturing costs, and enables automated assembly techniques such as pick-and-place machines.
- High Density Integration: SOP substrates support high-density integration of electronic components, including ICs, resistors, capacitors, and other discrete components. They provide multiple leads or pads for connecting these components, allowing for complex electronic circuits to be implemented in a compact space.
- Good Electrical Performance: SOP substrates offer good electrical performance, including low signal distortion, impedance control, and reliable electrical connections. The design of SOP packages allows for optimized signal routing and power distribution, contributing to the overall performance and functionality of electronic systems.
- Thermal Management: SOP packages typically feature thermal vias or thermal pads that help dissipate heat generated by ICs during operation. This efficient thermal management ensures reliable performance and prevents overheating of the components, particularly in high-power applications.
- Mechanical Durability: SOP substrates are designed to withstand mechanical stresses and environmental factors encountered during operation, such as shock, vibration, and temperature fluctuations. The robust construction of SOP packages enhances their mechanical durability and reliability in various application environments.
- Cost-Effectiveness: SOP packages are often cost-effective compared to other packaging technologies, such as leaded packages or ceramic packages. Their simple design, standardized manufacturing processes, and mass production capabilities contribute to their cost-effectiveness, making them an attractive option for a wide range of electronic devices.
- Compatibility: SOP packages are compatible with standard surface-mount assembly processes and equipment, making them easy to integrate into existing manufacturing workflows. They are also compatible with automated testing and inspection methods, ensuring efficient production and quality control.
Overall, the advantages of SOP package substrates, including their compact size, surface-mount capability, high-density integration, thermal management, mechanical durability, and cost-effectiveness, make them a preferred choice for many electronic applications across various industries.
How Much Does SOP Package Substrate Cost?
The cost of SOP (Small Outline Package) substrates can vary widely depending on several factors, including the substrate material, size, complexity, quantity, and manufacturing processes involved. Here are some factors that influence the cost of SOP package substrates:
- Substrate Material: The choice of substrate material can significantly impact the cost. For example, ceramic substrates tend to be more expensive than fiberglass (FR4) or laminate substrates due to their superior thermal properties and manufacturing complexity.
- Size and Complexity: Larger and more complex SOP substrates with intricate circuit patterns, multiple layers, and fine-pitch features may require additional manufacturing steps and materials, leading to higher costs.
- Quantity: Economies of scale play a significant role in determining the cost of SOP substrates. Larger production quantities typically result in lower unit costs due to bulk purchasing of materials and increased manufacturing efficiency.
- Manufacturing Processes: The specific manufacturing processes involved in producing SOP substrates, such as circuit pattern formation, metallization, via drilling, surface finishing, and quality control, can impact the overall cost. Sophisticated manufacturing techniques may incur higher costs compared to simpler processes.
- Customization: Customized SOP substrates designed to meet specific performance requirements or application needs may incur additional development and setup costs, resulting in higher overall costs compared to standard off-the-shelf substrates.
- Supplier and Location: The choice of substrate supplier and manufacturing location can also affect the cost. Different suppliers may offer varying pricing structures, quality levels, and lead times for SOP substrates.
- Market Conditions: Fluctuations in raw material prices, labor costs, and market demand can influence the overall cost of SOP substrates. Supply chain disruptions or shortages of key materials may also impact pricing.
Due to the many variables involved, it’s challenging to provide a specific cost for SOP package substrates without knowing the specific requirements of the application and the manufacturing details. Typically, customers can request quotes from substrate suppliers or contract manufacturers based on their exact specifications to determine the cost of SOP substrates for their project.
FAQs about SOP Package Substrate
What is an SOP package substrate?
An SOP package substrate is a type of integrated circuit packaging used to mount and interconnect electronic components, typically smaller and lower-profile than traditional packages. SOP packages are commonly used for small and medium-sized ICs.
What are the advantages of SOP package substrates?
SOP package substrates offer advantages such as compact size, lightweight design, low profile, compatibility with surface mount technology (SMT), and cost-effectiveness for small and medium-sized electronic components.
What materials are used in SOP package substrates?
Similar to other types of package substrates, materials used in SOP package substrates include substrate core materials (e.g., FR-4), copper foil for conductive traces, dielectric material for insulation, solder mask for protection, and surface finish materials such as immersion tin or gold.
How are SOP package substrates manufactured?
The manufacturing process of SOP package substrates involves similar steps to other package substrates, including substrate fabrication, layer buildup, circuit formation, surface finishing, and quality control. However, SOP packages typically have simpler designs compared to larger packages.
What are the applications of SOP package substrates?
SOP package substrates are commonly used in various electronic devices where space is limited or where smaller form factors are desired. They are found in applications such as consumer electronics, telecommunications, computing and networking, automotive electronics, and industrial electronics.
How much do SOP package substrates cost?
The cost of SOP package substrates can vary depending on factors such as size, complexity, material selection, manufacturing processes, volume, supplier, and location. Pricing information can be obtained from substrate manufacturers or suppliers.
Where can I find more information about SOP package substrates?
More information about SOP package substrates can be found through datasheets, application notes, technical articles, industry publications, and consultation with substrate manufacturers or suppliers. Additionally, online resources and forums may provide insights and discussions related to SOP package substrates.