N4000-13 Series Materials PCB Manufacturer
N4000-13 Series Materials PCB Manufacturer,N4000-13 Series Materials PCB are high-performance laminates designed for demanding electronic applications. Known for their excellent thermal and mechanical properties, these materials provide superior reliability and stability under extreme conditions. They feature low dielectric loss, high thermal conductivity, and excellent dimensional stability, making them ideal for high-frequency and high-speed digital applications. The N4000-13 series is particularly suited for use in telecommunications, networking equipment, and advanced computing systems. With enhanced moisture resistance and thermal performance, these materials ensure the longevity and efficiency of electronic devices, meeting the rigorous standards of modern electronics manufacturing.
What is an N4000-13 Series Materials PCB?
The N4000-13 Series Materials PCB refers to a specific type of high-performance laminate designed for use in electronic applications, particularly in PCB (Printed Circuit Board) manufacturing. This series is known for its advanced thermal and electrical properties, making it suitable for demanding environments where reliability and performance are crucial.
These materials typically feature low dielectric constant and low dissipation factor, ensuring efficient signal transmission and minimal signal loss. They are often used in high-frequency applications, such as RF (Radio Frequency) circuits and microwave circuits, where signal integrity is paramount.
Manufactured using state-of-the-art processes, N4000-13 Series Materials PCBs offer excellent dimensional stability and mechanical strength, making them ideal for complex designs that require precision and durability. They are compatible with various fabrication techniques, including multilayer PCB construction, ensuring flexibility in design while maintaining consistent electrical performance across the board.
In summary, the N4000-13 Series Materials PCB represents a cutting-edge solution in PCB technology, tailored for applications demanding high reliability, thermal management, and electrical performance.
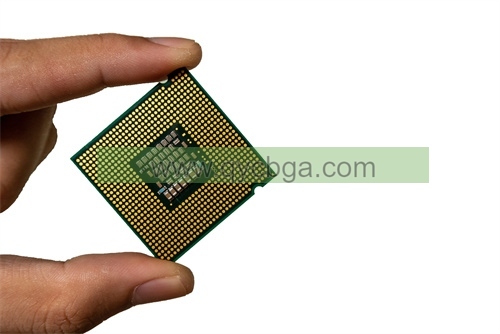
N4000-13 Series Materials PCB Manufacturer
What are the N4000-13 Series Materials PCB Design Guidelines?
The N4000-13 Series Materials PCB design guidelines focus on maximizing the performance and reliability of PCBs using these specific laminates. Here are some key aspects typically covered in such guidelines:
- Material Properties: Understand the electrical and thermal properties of N4000-13 Series Materials, including dielectric constant (εr), dissipation factor (Df), thermal conductivity, and coefficient of thermal expansion (CTE). Design with these properties in mind to optimize signal integrity and thermal management.
- Layer Stackup: Define the PCB layer stackup considering the desired impedance control, signal routing requirements, and thermal considerations. Utilize the material’s properties to achieve controlled impedance for high-frequency signals and manage heat dissipation effectively.
- Trace Width and Spacing: Determine appropriate trace widths and spacing based on the dielectric properties of N4000-13 Series Materials to maintain signal integrity and prevent signal crosstalk or interference.
- Via Design: Optimize via structures including pad size, via types (plated through-hole, microvias), and placement to minimize signal loss, maintain electrical continuity, and support high-density interconnect (HDI) designs if needed.
- Thermal Management: Incorporate adequate thermal vias, copper planes, and heat sinks as necessary to manage heat dissipation effectively, leveraging the high thermal conductivity of N4000-13 Series Materials.
- Mechanical Considerations: Ensure PCB designs meet mechanical strength requirements by considering material stiffness, flexural strength, and dimensional stability under varying environmental conditions.
- Manufacturing Compatibility: Design PCBs that are manufacturable within the capabilities of N4000-13 Series Materials, considering fabrication processes such as etching, drilling, and lamination.
- Testing and Validation: Plan for testing and validation processes to verify electrical performance, impedance matching, thermal behavior, and reliability of the PCB designs using N4000-13 Series Materials.
By following these guidelines, designers can harness the full potential of N4000-13 Series Materials PCBs, ensuring optimal performance, reliability, and manufacturability in high-frequency and high-reliability applications.
What is the N4000-13 Series Materials PCB Fabrication Process?
The fabrication process for N4000-13 Series Materials PCBs involves several key steps to ensure the material’s properties are utilized effectively while maintaining high quality and reliability. Here’s an overview of the typical fabrication process:
- Material Selection: Choose N4000-13 Series Materials based on the specific requirements of the PCB design, considering factors such as dielectric constant, dissipation factor, thermal conductivity, and mechanical properties.
- Preparation: Clean and prepare the substrate materials to ensure proper adhesion and consistency in subsequent processing steps.
- Layer Stackup Design: Design the layer stackup according to the PCB’s functional requirements, impedance control needs, and thermal management considerations. This involves selecting the number of layers, defining signal, power, and ground planes, and planning for high-density interconnect (HDI) if necessary.
- Copper Cladding: Apply copper foil to the substrate through lamination or deposition processes. This step involves cleaning, roughening (for good adhesion), and bonding the copper foil to the substrate material.
- Circuit Patterning (Etching): Use photolithography and etching techniques to define the circuit patterns on the copper layers. This involves applying a photoresist layer, exposing it to UV light through a photomask with the desired circuit pattern, developing the resist to remove unwanted areas, and etching away the exposed copper.
- Drilling: Drill holes for vias and component mounting pads using precision drilling machines. For high-density designs, this may include microvia drilling, which requires precise control over drill depth and diameter.
- Via Formation:Create vias (plated through-holes or microvias) to establish electrical connections between different layers of the PCB. This step includes processes like via cleaning, desmearing (for microvias), and electroplating to deposit conductive material inside the vias.
- Surface Finishing:Apply surface finishes to protect exposed copper and facilitate soldering during assembly. Common surface finishes include ENIG (Electroless Nickel Immersion Gold), HASL (Hot Air Solder Leveling), OSP (Organic Solderability Preservatives), and immersion tin/silver.
- Solder Mask Application: Apply solder mask over the PCB surface, leaving openings for component pads, vias, and fiducials. The solder mask protects the copper traces from oxidation and facilitates soldering during assembly.
- Silkscreen Printing: Apply component designators, logos, and other identifiers to the PCB surface using silkscreen printing. This step helps with component placement and assembly.
- Testing and Inspection: Conduct electrical testing (e.g., continuity testing, impedance testing) and visual inspection to ensure the PCB meets design specifications and quality standards.
- Final Fabrication: Cut individual PCBs from the panel, perform final inspection, and prepare for assembly by cleaning and packaging.
Throughout the fabrication process, stringent quality control measures are essential to ensure that N4000-13 Series Materials PCBs meet performance, reliability, and consistency requirements for their intended applications. Advanced manufacturing techniques and adherence to design guidelines help optimize the PCB’s electrical performance, thermal management, and mechanical stability.
How do you manufacture an N4000-13 Series Materials PCB?
Manufacturing an N4000-13 Series Materials PCB involves a detailed process aimed at leveraging the material’s advanced properties for high-performance electronic applications. Here’s an expanded format covering each step in the manufacturing process:
- Material Selection and Preparation:Begin by selecting N4000-13 Series Materials based on specific design requirements such as high-frequency performance, thermal management needs, and mechanical strength. These materials typically exhibit low dielectric constant (εr), low dissipation factor (Df), high thermal conductivity, and good dimensional stability. Clean and prepare the substrate materials to ensure they are free from contaminants that could affect adhesion and electrical properties during fabrication.
- Layer Stackup Design:Design the layer stackup of the PCB according to the functional requirements and performance specifications. This involves determining the number of layers needed, the arrangement of signal, power, and ground planes, and planning for controlled impedance requirements. Consideration should also be given to thermal management strategies, especially if the PCB will dissipate significant heat.
- Copper Cladding:Apply copper foil to the substrate material using lamination or deposition processes. This step involves cleaning the substrate surface, roughening it to promote adhesion, and bonding the copper foil securely. The thickness and quality of the copper layer are critical for achieving optimal electrical conductivity and signal integrity in the finished PCB.
- Circuit Patterning (Etching):Use photolithography and etching techniques to define the circuit patterns on the copper layers. Begin by applying a layer of photoresist over the copper surface, exposing it to UV light through a photomask that outlines the desired circuit pattern. Develop the resist to remove areas not protected by the mask and then etch away the exposed copper using chemical processes. This step creates the conductive pathways (traces) that will carry electrical signals throughout the PCB.
- Drilling:Drill holes in the PCB for vias and component mounting pads using precision drilling machines. For designs requiring high-density interconnects, microvia drilling may be used to create very small holes with precise dimensions. Control over drill depth and diameter is crucial to ensure proper electrical connectivity between different layers of the PCB.
- Via Formation:Create vias (plated through-holes or microvias) to establish electrical connections between different layers of the PCB. Begin by cleaning and preparing the holes, then apply a conductive material (typically copper) through processes like electroplating to ensure continuity and reliability. For microvias, additional steps such as desmearing and surface treatment may be necessary to achieve proper adhesion and conductivity.
- Surface Finishing:Apply a surface finish to protect exposed copper surfaces and facilitate soldering during component assembly. Common surface finishes include Electroless Nickel Immersion Gold (ENIG), Hot Air Solder Leveling (HASL), Organic Solderability Preservatives (OSP), and immersion tin/silver. Surface finishes play a critical role in ensuring solderability, corrosion resistance, and overall reliability of the PCB.
- Solder Mask Application:Apply solder mask over the PCB surface, leaving openings (exposed pads) for component attachment, vias, and fiducial marks. Solder mask protects copper traces from oxidation and contamination, facilitates soldering during assembly, and provides insulation between adjacent conductive traces.
- Silkscreen Printing:Print component designators, logos, and other identifiers on the PCB surface using silkscreen printing techniques. This step assists in component placement during assembly and provides visual guidance for technicians and inspectors.
- Testing and Inspection:Perform rigorous electrical testing and visual inspection throughout the manufacturing process to ensure the PCB meets design specifications and quality standards. Electrical tests may include continuity testing, impedance testing (for controlled impedance designs), and other functional tests to verify proper operation.
- Final Fabrication and Quality Assurance:Cut individual PCBs from the manufacturing panel, conduct final inspection to verify dimensional accuracy, surface quality, and overall integrity. Prepare the finished PCBs for assembly by cleaning and packaging them according to industry standards.
Manufacturing N4000-13 Series Materials PCBs requires precision, adherence to design guidelines, and careful quality control to achieve high-performance, reliability, and consistency in electronic applications. Advanced manufacturing techniques and expertise in handling specialized materials are crucial to harness the full potential of these PCBs in demanding environments such as telecommunications, aerospace, and high-speed computing.
How much should an N4000-13 Series Materials PCB cost?
The cost of an N4000-13 Series Materials PCB can vary widely based on several factors including the following:
- Board Size and Complexity: Larger boards or those with complex designs (e.g., high layer count, fine trace width and spacing) generally cost more due to increased material usage and manufacturing complexity.
- Material Specifications: The specific grade and thickness of N4000-13 Series Materials chosen can influence cost. Higher performance grades or thicker laminates may cost more per unit area.
- Layer Count:PCBs with more layers typically cost more due to increased manufacturing complexity and material usage.
- Surface Finish and Special Processes: Choice of surface finish (e.g., ENIG, HASL, OSP) and any special processes (e.g., impedance control, blind/buried vias) can affect cost.
- Quantity:Economies of scale apply, so larger production quantities generally reduce the cost per unit. Prototype or small batch runs may be more expensive per board.
- Lead Time: Expedited manufacturing timelines often incur higher costs due to prioritization and potential overtime charges.
- Supplier and Location:Costs can vary between PCB manufacturers based on their capabilities, location, and overhead costs.
To provide a rough estimate, typical prices for standard N4000-13 Series Materials PCBs in small quantities might range from $5 to $50 per square inch, depending on the factors mentioned above. Larger quantities and simpler designs could potentially lower this range, while highly complex designs or specialized requirements might exceed it.
For accurate pricing, it’s advisable to request quotes from PCB manufacturers based on your specific design requirements and production volume. This allows for a tailored assessment considering all relevant factors impacting cost.
What is N4000-13 Series Materials PCB base material?
The N4000-13 Series Materials PCB base material refers to a specific type of high-performance laminate used as the substrate for manufacturing printed circuit boards (PCBs). These materials are characterized by their advanced properties designed to meet the demanding requirements of modern electronic applications, especially those involving high-frequency signals and thermal management.
Specifically, the base material of N4000-13 Series PCBs typically includes:
- Substrate Material: The substrate is composed of a specialized dielectric material with a low dielectric constant (εr) and a low dissipation factor (Df). This helps in minimizing signal loss and maintaining signal integrity, crucial for high-frequency applications.
- Copper Foil: Copper foil is bonded to the substrate material to form the conductive layers of the PCB. The copper foil used in N4000-13 Series Materials PCBs is chosen for its high electrical conductivity and ability to support fine traces and high-density interconnect designs.
- Laminate Structure: The laminate structure may include multiple layers of the substrate material and copper foil, depending on the PCB design requirements. This layered construction enables the creation of complex circuit patterns and facilitates controlled impedance designs.
- Surface Finish: The surface finish applied to the copper layers helps protect them from oxidation and ensures good solderability during component assembly. Common surface finishes include ENIG (Electroless Nickel Immersion Gold), HASL (Hot Air Solder Leveling), and OSP (Organic Solderability Preservatives).
Overall, the base material of N4000-13 Series PCBs is engineered to provide excellent electrical performance, thermal management capabilities, and mechanical stability. These properties make them suitable for use in telecommunications equipment, aerospace systems, high-speed computing devices, and other applications requiring reliable PCBs capable of operating in demanding environments.
Which company makes N4000-13 Series Materials PCB?
N4000-13 Series Materials PCBs are typically produced by specialized manufacturers known for their high-performance circuit board materials, enjoying a strong reputation in the electronics industry. These companies often boast advanced manufacturing equipment and stringent quality control standards to ensure their products meet the demands of high-frequency and high-reliability applications.
These PCB materials are commonly used in designs requiring low dielectric constant and low dissipation factor, ensuring stable signal transmission and minimal signal loss. The production process for N4000-13 Series Materials PCBs includes material selection, stackup design, copper foil application, circuit patterning, hole drilling, surface treatment, solder mask application, silkscreen printing, testing, and quality validation. This comprehensive process ensures reliability and performance in diverse operational environments.
Regarding production capabilities, our company also manufactures and supplies N4000-13 Series Materials PCBs. We possess advanced production equipment and a skilled workforce capable of delivering high-quality, customized solutions tailored to customer specifications. We prioritize product quality, performance, and customer satisfaction, continuously improving our production capabilities and service levels through innovation and technological advancement.
For specific inquiries about N4000-13 Series Materials PCBs or further details about our manufacturing capabilities, please feel free to contact us. We are committed to providing professional technical support and services to meet various PCB requirements effectively.
What are the 7 qualities of good customer service?
The 7 qualities of good customer service are essential for ensuring positive customer experiences and building strong relationships. They include:
- Responsiveness: Promptly addressing customer inquiries, concerns, and requests demonstrates attentiveness and respect for their time.
- Empathy: Understanding and empathizing with the customer’s situation shows that you care about their needs and concerns.
- Patience: Remaining calm and patient, especially during challenging interactions, helps to maintain professionalism and foster positive outcomes.
- Clear Communication: Communicating clearly and effectively ensures that information is understood and reduces misunderstandings.
- Product Knowledge: Having a deep understanding of the products or services offered enables you to provide accurate information and advice to customers.
- Problem-Solving Skills:Being proactive and resourceful in resolving customer issues demonstrates commitment to finding solutions and ensuring satisfaction.
- 7. Personalization: Tailoring interactions to the specific needs and preferences of each customer helps to create a personalized and memorable experience.
By embodying these qualities, businesses can enhance customer satisfaction, loyalty, and advocacy, contributing to long-term success and growth.
FAQs
What are N4000-13 Series Materials PCBs used for?
N4000-13 Series Materials PCBs are used in high-frequency applications where low dielectric constant and low dissipation factor are critical. They are suitable for telecommunications equipment, aerospace systems, high-speed computing devices, and other electronic applications requiring reliable performance.
What are the key properties of N4000-13 Series Materials PCBs?
Key properties include low dielectric constant (εr), low dissipation factor (Df), high thermal conductivity, and excellent dimensional stability. These properties ensure minimal signal loss, efficient heat dissipation, and reliability in varied environmental conditions.
How do N4000-13 Series Materials compare to other PCB materials?
N4000-13 Series Materials are designed to provide superior performance in high-frequency applications compared to standard PCB materials. They offer enhanced electrical and thermal properties suitable for demanding electronic designs.
What are the manufacturing considerations for N4000-13 Series Materials PCBs?
Manufacturing considerations include precise material handling to maintain properties, careful design of layer stackups for impedance control, and specialized processes for drilling microvias and applying surface finishes suitable for high-frequency signals.
Which industries benefit most from N4000-13 Series Materials PCBs?
Industries such as telecommunications, aerospace, automotive (for radar and communication systems), and high-speed computing benefit from N4000-13 Series Materials PCBs due to their reliability, performance, and ability to meet stringent technical requirements.
What are the cost considerations for N4000-13 Series Materials PCBs?
The cost of N4000-13 Series Materials PCBs can vary based on factors such as board size, complexity, material grade, surface finish, and production volume. Generally, they are priced higher than standard PCB materials due to their specialized properties and manufacturing requirements.
Where can I source N4000-13 Series Materials PCBs?
N4000-13 Series Materials PCBs are typically sourced from specialized PCB manufacturers with expertise in high-frequency materials. It’s important to choose a manufacturer with a proven track record in producing high-quality, reliable PCBs for your specific application needs.