Mitsubishi BT Substrate Manufacturer
Mitsubishi BT Substrate Manufacturer,Mitsubishi BT Substrate stands as a pinnacle of advanced materials engineering in the realm of electronics. Crafted with precision and innovation, this substrate embodies a fusion of bismaleimide triazine (BT) resin and woven glass fabric, manifesting unparalleled thermal stability, electrical insulation, and mechanical robustness. Designed to excel in high-performance applications, Mitsubishi BT Substrates offer a steadfast foundation for semiconductor devices, telecommunications systems, automotive electronics, and aerospace technology. With a commitment to quality and reliability, Mitsubishi Electric ensures that each substrate delivers optimal performance, contributing to the longevity and efficiency of electronic assemblies. From its superior thermal management capabilities to its compatibility with lead-free soldering processes, Mitsubishi BT Substrate epitomizes excellence, empowering engineers to realize cutting-edge electronic solutions with confidence and precision.
What is a Mitsubishi BT Substrate?
A Mitsubishi BT substrate refers to a specialized material used in semiconductor manufacturing processes, particularly in the production of integrated circuits (ICs) and other electronic components. The acronym “BT” stands for “Bismaleimide Triazine,” which is a type of resin material known for its excellent electrical properties, mechanical strength, and thermal stability.
Mitsubishi BT substrates are primarily utilized in the fabrication of high-performance semiconductor devices due to their ability to provide a reliable and stable foundation for mounting electronic components. These substrates serve as the base material onto which various layers of conductive and insulating materials are deposited during the manufacturing process.
The key characteristics of Mitsubishi BT substrates include:
- High Thermal Conductivity: Mitsubishi BT substrates exhibit excellent thermal conductivity, which helps in dissipating heat generated by electronic components. This property is crucial for preventing overheating and ensuring the reliable operation of semiconductor devices, especially those designed for high-power applications.
- Low Dielectric Constant: The low dielectric constant of Mitsubishi BT substrates minimizes signal loss and distortion, making them suitable for high-frequency and high-speed electronic applications. This property is essential for maintaining signal integrity and maximizing the performance of ICs and other electronic circuits.
- Dimensional Stability: Mitsubishi BT substrates offer excellent dimensional stability, meaning they maintain their shape and size even under fluctuating temperatures and environmental conditions. This property is important for ensuring the precise alignment of components during the manufacturing process and the reliable operation of electronic devices in various operating environments.
- Chemical Resistance: Mitsubishi BT substrates are resistant to a wide range of chemicals, solvents, and environmental factors, enhancing their durability and longevity in harsh operating conditions.
- Mechanical Strength:The mechanical strength of Mitsubishi BT substrates ensures the structural integrity of electronic assemblies, reducing the risk of damage or failure due to mechanical stress or impact.
Overall, Mitsubishi BT substrates play a critical role in the production of advanced semiconductor devices, enabling manufacturers to achieve higher levels of performance, reliability, and miniaturization in electronic applications across various industries, including telecommunications, automotive, aerospace, and consumer electronics.
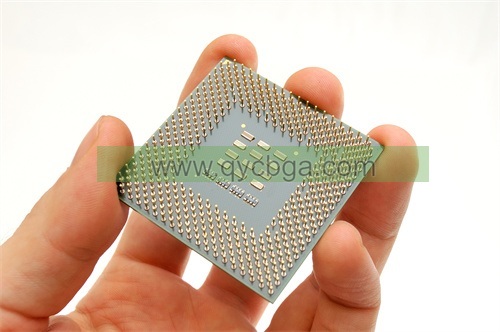
Mitsubishi BT Substrate Manufacturer
What are Mitsubishi BT Substrate Design Guidelines?
Mitsubishi BT substrate design guidelines provide recommendations and best practices for engineers and designers involved in the development of electronic components and systems using Mitsubishi BT substrates. These guidelines are aimed at optimizing the performance, reliability, and manufacturability of semiconductor devices and electronic assemblies. While specific design guidelines may vary depending on the application and requirements, some common recommendations include:
- Thermal Management: Incorporate adequate thermal management techniques to ensure efficient heat dissipation from electronic components mounted on the Mitsubishi BT substrate. This may include the use of thermal vias, heat sinks, thermal pads, or other cooling solutions to prevent overheating and maintain optimal operating temperatures.
- Signal Integrity: Pay close attention to signal integrity considerations to minimize signal loss, distortion, and electromagnetic interference (EMI). Design high-speed signal traces with controlled impedance and proper signal routing techniques to maintain signal integrity and minimize signal degradation.
- Power Distribution: Implement a robust power distribution network on the Mitsubishi BT substrate to ensure stable and reliable power supply to electronic components. This involves careful planning of power planes, decoupling capacitors, and power routing to minimize voltage drops and noise in the system.
- Mechanical Stability: Design the substrate layout and mounting arrangements to ensure mechanical stability and durability of the electronic assembly. Consider factors such as component placement, board thickness, mounting hole locations, and mechanical support structures to withstand mechanical stress, vibration, and thermal cycling.
- Material Compatibility: Select compatible materials for components, solder masks, and surface finishes to ensure proper adhesion, solderability, and reliability of the Mitsubishi BT substrate. Consider the thermal expansion coefficient (CTE) mismatch between different materials to prevent solder joint failures and mechanical reliability issues.
- Manufacturability: Design the substrate layout with manufacturability in mind, considering factors such as panelization, solder mask registration, fiducial placement, and assembly process compatibility. Optimize the design for ease of manufacturing, assembly, and testing to minimize production costs and improve yield rates.
- Environmental Considerations:Take into account environmental factors such as temperature, humidity, chemical exposure, and mechanical stressors that the electronic assembly may encounter during its lifecycle. Design the substrate and component selection to meet the required reliability standards and environmental specifications for the target application.
By following these Mitsubishi BT substrate design guidelines, engineers and designers can develop electronic systems and semiconductor devices that meet performance requirements, reliability standards, and manufacturing constraints, resulting in high-quality products with optimized functionality and longevity.
What is the Mitsubishi BT Substrate Fabrication Process?
The fabrication process for Mitsubishi BT substrates involves several steps to produce high-quality substrates suitable for use in semiconductor devices and electronic assemblies. While specific processes may vary depending on the manufacturer and the desired substrate specifications, the following are typical steps involved in the fabrication of Mitsubishi BT substrates:
- Substrate Preparation:The fabrication process begins with the preparation of the substrate material, which typically consists of layers of woven glass fabric impregnated with bismaleimide triazine (BT) resin. The glass fabric provides mechanical strength, while the BT resin offers excellent electrical properties and thermal stability. The substrate material may come in the form of sheets or panels.
- Resin Application: The substrate material is coated or impregnated with BT resin using techniques such as dip coating, roll coating, or resin infusion. The resin is evenly distributed across the substrate material to ensure uniform electrical and mechanical properties.
- Prepreg Formation: The resin-coated substrate material, also known as prepreg, undergoes a curing process to partially cure the resin and create a stable, semi-solid material. This step is essential for improving handling properties and facilitating subsequent lamination processes.
- Layer Stacking: Multiple layers of prepreg are stacked together along with conductive layers, such as copper foil, to form a multilayered structure. The conductive layers provide electrical pathways for interconnections between electronic components mounted on the substrate.
- Lamination: The stacked layers are subjected to heat and pressure in a lamination press to bond them together and consolidate the structure into a single, cohesive substrate. This process ensures strong adhesion between the layers and eliminates voids or air pockets that could affect electrical performance.
- Drilling and Routing: Holes are drilled or routed into the substrate to create vias, which provide electrical connections between different layers of the substrate. Advanced drilling techniques, such as laser drilling, may be employed to achieve precise hole sizes and locations.
- Plating and Surface Finishing: The drilled vias are plated with conductive materials, such as copper, to establish electrical continuity between layers. Surface finishing processes, such as solder mask application and surface treatment, are performed to improve solderability and protect the substrate from environmental factors.
- Final Inspection and Testing: The fabricated Mitsubishi BT substrates undergo rigorous inspection and testing to ensure compliance with quality standards and specifications. Various tests, including dimensional inspection, electrical continuity testing, and thermal cycling tests, may be conducted to validate the performance and reliability of the substrates.
By following these fabrication processes, manufacturers can produce Mitsubishi BT substrates with the desired electrical, mechanical, and thermal properties required for a wide range of semiconductor devices and electronic applications.
How do you manufacture a Mitsubishi BT Substrate?
Manufacturing a Mitsubishi BT substrate involves a series of intricate steps aimed at creating a high-quality base material for electronic components and semiconductor devices. Here’s a detailed overview of the typical manufacturing process:
- Substrate Material Preparation: The process begins with the preparation of the substrate material, which usually consists of woven glass fabric impregnated with bismaleimide triazine (BT) resin. The glass fabric provides structural support, while the BT resin offers excellent electrical properties and thermal stability. The substrate material may be supplied in the form of sheets or rolls.
- Resin Coating: The substrate material is coated or impregnated with BT resin using techniques such as dip coating, roll coating, or resin infusion. This step ensures that the resin is evenly distributed throughout the substrate material, forming a uniform layer with consistent properties.
- Partial Curing (Prepreg Formation): The resin-coated substrate material, known as prepreg, undergoes a partial curing process to stabilize the resin and create a semi-solid material. This step improves the handling characteristics of the substrate material and prepares it for further processing.
- Layer Stacking: Multiple layers of prepreg are stacked together to form a multilayered structure. Conductive layers, typically made of copper foil, are interleaved between the prepreg layers to provide electrical pathways for interconnections between components.
- Lamination:The stacked layers undergo a lamination process, where they are subjected to heat and pressure in a press. This step bonds the layers together, consolidates the structure, and eliminates voids or air pockets that could compromise the substrate’s integrity. The lamination process may involve multiple cycles to ensure thorough bonding.
- Drilling and Via Formation: After lamination, holes are drilled or routed into the substrate to create vias, which are used to establish electrical connections between different layers. Advanced drilling techniques, such as laser drilling, may be employed to achieve precise hole sizes and locations.
- Surface Preparation and Plating: The drilled vias are plated with conductive materials, such as copper, to create electrical pathways between the layers. Surface finishing processes, including the application of solder mask and surface treatment, may be performed to improve solderability and protect the substrate from environmental factors.
- Final Inspection and Testing: The manufactured Mitsubishi BT substrates undergo thorough inspection and testing to ensure they meet quality standards and specifications. Various tests, such as dimensional inspection, electrical continuity testing, and thermal cycling tests, may be conducted to verify the performance and reliability of the substrates.
By following these manufacturing steps, Mitsubishi BT substrates with the desired electrical, mechanical, and thermal properties can be produced for use in a wide range of electronic applications, including semiconductor devices, printed circuit boards (PCBs), and electronic assemblies.
How much should a Mitsubishi BT Substrate cost?
The cost of a Mitsubishi BT substrate can vary significantly depending on several factors, including the substrate’s size, thickness, complexity, material quality, manufacturing processes, and market conditions. Additionally, other considerations such as customization requirements, order volume, and supplier relationships can influence the overall cost.
Typically, Mitsubishi BT substrates are considered high-performance materials designed for demanding applications in the semiconductor industry, which may result in higher costs compared to standard substrate materials. Here are some factors that contribute to the cost of Mitsubishi BT substrates:
- Material Quality:Mitsubishi BT substrates are manufactured using high-quality materials, including bismaleimide triazine (BT) resin and woven glass fabric. The use of premium materials contributes to superior electrical properties, thermal stability, and mechanical strength, but it also increases production costs.
- Manufacturing Processes: The fabrication process for Mitsubishi BT substrates involves several intricate steps, including resin coating, lamination, drilling, plating, and surface finishing. Each of these processes requires specialized equipment, skilled labor, and quality control measures, which add to the overall manufacturing cost.
- Customization Requirements: If the Mitsubishi BT substrates need to be customized to meet specific design requirements or performance specifications, additional engineering and manufacturing efforts may be required, resulting in higher costs. Customization can include features such as unique layer configurations, controlled impedance, special surface finishes, or advanced surface treatments.
- Order Volume: The cost per unit of Mitsubishi BT substrates may vary depending on the volume of the order. Typically, larger order volumes allow manufacturers to achieve economies of scale and reduce per-unit production costs. However, smaller quantities or prototype orders may incur higher costs due to setup and handling expenses.
- Market Conditions: Market demand, supply chain dynamics, and raw material prices can impact the cost of Mitsubishi BT substrates. Fluctuations in the market may influence pricing levels, especially for materials subject to supply chain disruptions or changes in demand.
Given these factors, the cost of Mitsubishi BT substrates can range from a few dollars per square inch for standard, off-the-shelf products to significantly higher prices for custom or specialized configurations. It’s essential for buyers to consider their specific requirements, budget constraints, and quality expectations when evaluating the cost-effectiveness of Mitsubishi BT substrates for their applications. Additionally, consulting with suppliers and obtaining quotes based on the desired specifications can provide a better understanding of the potential costs involved.
What is Mitsubishi BT Substrate base material?
The base material of Mitsubishi BT substrates primarily consists of bismaleimide triazine (BT) resin impregnated into woven glass fabric layers. This composite material forms the foundation of the substrate, providing it with essential properties such as mechanical strength, thermal stability, electrical insulation, and dimensional stability.
- Bismaleimide Triazine (BT) Resin: BT resin is a high-performance thermosetting polymer known for its exceptional electrical properties, thermal stability, and resistance to various environmental factors. It serves as the matrix material that binds the substrate together and provides insulation between conductive layers. BT resin offers excellent heat resistance, making it suitable for applications where temperature fluctuations and thermal stress are common.
- Woven Glass Fabric: The woven glass fabric, also known as glass cloth, serves as the reinforcement material within the substrate. It consists of strands of glass fibers woven together to form a flexible yet sturdy fabric. The glass fabric provides mechanical support, strength, and dimensional stability to the substrate, ensuring that it can withstand the rigors of electronic assembly processes and operational conditions.
By combining BT resin with woven glass fabric, Mitsubishi BT substrates achieve a balance of mechanical robustness, thermal performance, and electrical insulation. This base material enables the substrate to support the mounting of electronic components, provide reliable electrical interconnections, dissipate heat efficiently, and maintain structural integrity under varying operating conditions. Additionally, the properties of the base material contribute to the overall reliability, performance, and longevity of electronic devices and systems employing Mitsubishi BT substrates.
Which company makes Mitsubishi BT Substrate?
Mitsubishi BT substrates are produced by Mitsubishi Electric Corporation. Mitsubishi Electric is a Japanese multinational company dedicated to developing and manufacturing various electrical and electronic products, including semiconductor devices, electronic components, industrial automation equipment, air conditioning systems, and more. As a globally renowned electronics manufacturer, Mitsubishi Electric has extensive experience and technological expertise in the semiconductor and electronics fields, and its Mitsubishi BT substrates are highly regarded in the market.
Our company can also manufacture Mitsubishi BT substrates. As an electronic manufacturing enterprise equipped with advanced production facilities and technology, we have professional R&D and production teams capable of meeting customers’ demands for high-quality substrates. We employ advanced manufacturing processes and strict quality control standards to ensure that the substrates we produce exhibit excellent electrical performance, thermal stability, and mechanical strength. Furthermore, we can customize Mitsubishi BT substrates according to customers’ requirements, offering products with various sizes, thicknesses, layer configurations, and special process requirements.
We are committed to providing customers with the highest quality products and services to meet their needs in the field of electronic manufacturing. Through continuous innovation and technological advancement, we will continue to offer customers high-performance, reliable, and cost-effective Mitsubishi BT substrates, helping them succeed in the market.
What are the 7 qualities of good customer service?
Good customer service encompasses several qualities that contribute to a positive experience for customers. Here are seven essential qualities:
- Responsiveness:A good customer service team responds promptly to customer inquiries, concerns, and requests for assistance. Quick response times demonstrate attentiveness and a commitment to addressing customer needs in a timely manner.
- Empathy: Empathy involves understanding and acknowledging the customer’s feelings, concerns, and perspectives. A good customer service representative listens actively, shows genuine empathy, and strives to put themselves in the customer’s shoes to better understand their situation.
- Clarity and Communication Skills: Effective communication is crucial in customer service. Customer service representatives should communicate clearly and concisely, using language that is easy to understand. They should also be skilled at explaining complex concepts or procedures in a simple and understandable manner.
- Problem-Solving Skills: Good customer service involves resolving customer issues and concerns effectively. Customer service representatives should be skilled problem solvers, capable of identifying root causes, exploring solutions, and taking proactive steps to address customer issues and prevent recurrence.
- Professionalism: Professionalism encompasses a range of qualities, including courtesy, respect, integrity, and reliability. Customer service representatives should conduct themselves professionally at all times, demonstrating respect for customers and maintaining a positive and helpful attitude, even in challenging situations.
- Product Knowledge: A good customer service team possesses a deep understanding of the products or services they support. Customer service representatives should be knowledgeable about product features, capabilities, pricing, and policies, enabling them to provide accurate information and guidance to customers.
- Follow-Up and Follow-Through: After resolving a customer issue or inquiry, good customer service includes follow-up to ensure customer satisfaction and address any additional concerns. Customer service representatives should follow through on commitments, such as providing updates, following up on requests, or ensuring that promised actions are completed satisfactorily.
By embodying these qualities, businesses can deliver exceptional customer service experiences that foster trust, loyalty, and satisfaction among their customers.
FAQs
What is a Mitsubishi BT substrate?
A Mitsubishi BT substrate is a type of printed circuit board (PCB) material that uses bismaleimide triazine (BT) resin. This material is known for its excellent thermal stability and electrical insulation properties, making it suitable for high-frequency and high-performance electronic applications.
What are the main applications of Mitsubishi BT substrates?
Mitsubishi BT substrates are typically used in applications requiring high thermal performance and reliability. Common uses include advanced semiconductor packaging like chip-on-board (COB) and ball grid array (BGA) packages, as well as in high-speed telecommunications, automotive electronics, aerospace, and military applications.
What are the advantages of using Mitsubishi BT substrates over traditional FR-4 substrates?
Mitsubishi BT substrates offer superior thermal stability, a lower coefficient of thermal expansion (CTE), and better dielectric properties compared to standard FR-4 substrates. These characteristics make BT substrates more suitable for high-density interconnects (HDI) and applications subjected to high thermal loads.
How does the thermal performance of Mitsubishi BT substrates compare to other materials?
BT substrates typically have a higher glass transition temperature (Tg) and a lower thermal expansion rate than many other PCB materials, which helps in maintaining structural integrity and dimensional stability at higher temperatures.
Can Mitsubishi BT substrates be used for lead-free soldering applications?
Yes, Mitsubishi BT substrates are compatible with lead-free soldering processes. Their high Tg and thermal durability make them ideal for the high temperatures required in lead-free soldering.
What thicknesses and sizes are available for Mitsubishi BT substrates?
Mitsubishi BT substrates are available in various thicknesses and sizes, which can be customized based on specific requirements of the application. Manufacturers typically provide a range from standard sizes to custom dimensions tailored for specific designs.
How do Mitsubishi BT substrates contribute to the reliability of electronic assemblies?
Due to their excellent thermal and mechanical properties, BT substrates contribute significantly to the reliability of electronic assemblies by reducing failure rates associated with thermal cycling and mechanical stress.
What are the cost implications of using Mitsubishi BT substrates?
While Mitsubishi BT substrates generally cost more than standard FR-4 materials, their enhanced performance characteristics can lead to lower overall costs in high-reliability applications due to reduced failure rates and longer product lifespans.