Minimum Spacing PCB Manufacturer
Minimum Spacing PCB Manufacturer,Minimum Spacing PCBs are printed circuit boards designed with precise clearance between conductive traces, components, and features. These boards are engineered to meet stringent design requirements while ensuring electrical integrity and reliability. The minimized spacing between elements helps prevent electrical interference, signal degradation, and potential short circuits, particularly crucial in high-frequency and high-density electronic applications.
Manufacturing Minimum Spacing PCBs involves advanced fabrication processes and precise manufacturing techniques. Material selection plays a vital role, with options like FR-4, high-temperature variants, polyimide, and specialized substrates tailored to specific application needs.
Designers meticulously plan the layout, utilizing CAD software and adhering to design guidelines to achieve the desired spacing. This includes optimizing signal paths, routing traces efficiently, and avoiding sharp corners to maintain signal integrity.
Overall, Minimum Spacing PCBs are essential for applications demanding reliability, performance, and compactness. Their careful design and manufacturing ensure they meet the rigorous demands of modern electronic devices while providing robust functionality and longevity.
What is a Minimum Spacing PCB?
A Minimum Spacing PCB, or Minimum Spacing Printed Circuit Board, refers to the minimum distance required between conductive traces, components, or other features on a printed circuit board (PCB). This distance is crucial to prevent electrical interference, short circuits, and other forms of signal degradation or malfunction.
In electronic design, PCB layout plays a critical role in determining the performance, reliability, and manufacturability of electronic devices. The spacing between components and traces on a PCB is carefully calculated based on various factors, including electrical characteristics, thermal considerations, and manufacturing constraints.
The minimum spacing requirements are determined by factors such as the voltage levels present on the PCB, the materials used, environmental conditions, and regulatory standards. High-voltage circuits typically require larger spacing to prevent arcing and electrical breakdown, while low-voltage circuits may allow for smaller spacing.
Various industry standards and design guidelines, such as those provided by the Institute of Electrical and Electronics Engineers (IEEE), the International Electrotechnical Commission (IEC), and the IPC (Association Connecting Electronics Industries), offer recommendations and requirements for minimum spacing based on different applications and considerations.
When designing a PCB, engineers use computer-aided design (CAD) software to lay out components and traces while adhering to minimum spacing requirements. These tools often include design rule checks (DRC) to ensure that spacing constraints are met and to flag potential issues during the design process.
Failure to adhere to minimum spacing requirements can result in various problems, including electrical shorts, signal cross-talk, electromagnetic interference (EMI), and reduced reliability. In extreme cases, it can lead to catastrophic failures, damage to components, and safety hazards.
Therefore, designers must carefully consider minimum spacing requirements throughout the PCB design process to ensure the integrity and functionality of the final product. This involves balancing the need for compact, efficient layouts with the necessity of maintaining adequate spacing to meet electrical and safety requirements. Additionally, thorough testing and validation procedures are typically employed to verify that the finished PCB meets all necessary specifications and standards.
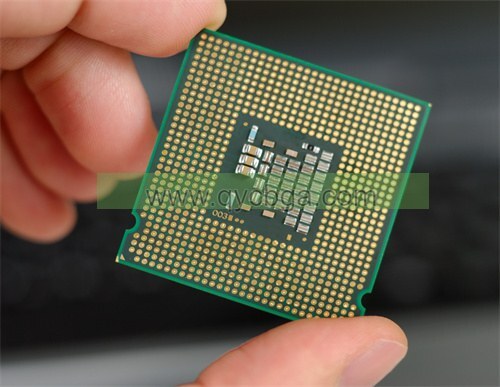
Minimum Spacing PCB Manufacturer
What are the Minimum Spacing PCB Design Guidelines?
Minimum spacing PCB design guidelines refer to the recommendations and requirements for the distances between various elements on a printed circuit board (PCB). These guidelines are essential for ensuring electrical performance, reliability, and compliance with safety standards. Here are some common minimum spacing PCB design guidelines:
- Trace-to-Trace Spacing:This guideline defines the minimum distance required between adjacent traces on the PCB. It helps prevent electrical interference, cross-talk, and short circuits. The spacing may vary depending on factors such as signal voltage, frequency, and environmental conditions.
- Trace-to-Component Spacing:Similar to trace-to-trace spacing, this guideline specifies the minimum distance between traces and individual components such as resistors, capacitors, and integrated circuits (ICs). It ensures that components do not interfere with neighboring traces and vice versa.
- Trace-to-Plane Spacing:In PCBs with power or ground planes, designers must maintain adequate spacing between traces and these planes to prevent electrical coupling, signal distortion, and EMI. The spacing requirements may differ based on the voltage levels and frequencies of signals.
- Component-to-Component Spacing:This guideline defines the minimum distance between adjacent components on the PCB. It ensures proper airflow for cooling, accessibility for maintenance, and prevents mechanical interference during assembly and operation.
- Edge-to-Trace Spacing:PCB traces near the board’s edge must have sufficient clearance to prevent issues such as solder bridging, short circuits, and damage during handling. The spacing requirement depends on the manufacturing process and assembly considerations.
- Copper-to-Board Edge Spacing:Similar to edge-to-trace spacing, this guideline specifies the minimum distance between copper features (such as traces or copper pours) and the board edge. It prevents issues during PCB manufacturing and assembly, such as copper etching variations and mechanical stress.
- Isolation Spacing for High Voltage:In circuits with high voltage components or signals, designers must adhere to specific isolation spacing guidelines to prevent arcing, electrical breakdown, and safety hazards. These guidelines are often defined by regulatory standards and safety codes.
- Creepage and Clearance Distance:For safety-critical applications and high-voltage circuits, designers must consider creepage and clearance distances. Creepage refers to the shortest path along the surface of a PCB between two conductive elements, while clearance is the shortest distance through air between them. These distances are critical for preventing electrical arcing and ensuring safety compliance.
- Compliance with Industry Standards:Designers should refer to industry standards and guidelines provided by organizations such as the IPC (Association Connecting Electronics Industries), IEEE (Institute of Electrical and Electronics Engineers), and IEC (International Electrotechnical Commission) for specific minimum spacing requirements and best practices.
By adhering to these minimum spacing PCB design guidelines, designers can optimize the performance, reliability, and safety of electronic devices while ensuring compliance with industry standards and regulatory requirements. Additionally, computer-aided design (CAD) tools with design rule checks (DRC) functionality help automate the verification of spacing constraints during the PCB design process.
What is the Minimum Spacing PCB Fabrication Process?
The minimum spacing PCB fabrication process involves the manufacturing steps necessary to ensure that the required spacing between various elements on a printed circuit board (PCB) is maintained according to design specifications and industry standards. Here’s an overview of the key steps involved in the minimum spacing PCB fabrication process:
- Design Verification:Before fabrication begins, the PCB design undergoes thorough verification to ensure that all spacing requirements specified in the design guidelines are met. Design rule checks (DRC) are performed using computer-aided design (CAD) software to detect any spacing violations or design errors.
- Material Selection:The choice of materials for the PCB substrate and copper layers is crucial in maintaining minimum spacing requirements. High-quality materials with precise thickness and dielectric properties are selected to ensure proper insulation and electrical performance.
- Layer Preparation:The fabrication process typically starts with the preparation of the PCB substrate and copper layers. Depending on the design requirements, multiple layers of copper may be laminated onto the substrate to create a multilayer PCB structure.
- Photoresist Application:A layer of photoresist material is applied to the surface of the copper layers. This photoresist layer will be patterned to define the locations of the conductive traces and features on the PCB.
- Exposure and Development:The PCB design is transferred onto the photoresist layer using a photomask and exposure to ultraviolet (UV) light. After exposure, the unexposed areas of the photoresist are developed, leaving behind the patterned resist mask.
- Etching:The exposed copper areas not protected by the photoresist mask are etched away using chemical etchants. This process defines the conductive traces and features on the PCB while maintaining the minimum spacing between them.
- Resist Stripping:After etching, the remaining photoresist mask is stripped away, leaving behind the desired copper traces and features on the PCB substrate.
- Surface Finish:Surface finish processes such as electroplating or immersion coating may be applied to the exposed copper surfaces to improve solderability, corrosion resistance, and overall reliability of the PCB.
- Final Inspection:The fabricated PCB undergoes thorough inspection to ensure that all spacing requirements, dimensional tolerances, and quality standards are met. Automated optical inspection (AOI) and other testing methods may be employed to detect any defects or deviations from the design specifications.
- Quality Assurance:Throughout the fabrication process, strict quality control measures are implemented to monitor the quality and consistency of the PCBs. This includes in-process inspections, testing of materials, and adherence to industry standards and regulations.
By following these steps and employing stringent quality control measures, PCB manufacturers can ensure that the minimum spacing requirements specified in the design are maintained throughout the fabrication process. This results in PCBs that meet the electrical performance, reliability, and safety requirements for their intended applications.
How do you manufacture a Minimum Spacing PCB?
Manufacturing a minimum spacing PCB involves several steps to ensure that the required distances between various elements on the printed circuit board (PCB) are maintained according to design specifications and industry standards. Here’s a detailed overview of the manufacturing process:
- Design Preparation: The PCB design is created using computer-aided design (CAD) software, considering the required minimum spacing between traces, components, and other features. Designers use design rule checks (DRC) to verify that the design meets spacing requirements and other design rules.
- Material Selection: High-quality materials are selected for the PCB substrate and copper layers. The substrate material provides mechanical support, while the copper layers serve as conductive paths for electrical signals. Materials with precise thickness and dielectric properties are chosen to ensure proper insulation and electrical performance.
- Layer Preparation:The PCB fabrication process begins with the preparation of the substrate and copper layers. Depending on the design requirements, multiple layers of copper may be laminated onto the substrate to create a multilayer PCB structure.
- Photoresist Application:A layer of photoresist material is applied to the surface of the copper layers. This photoresist layer will be patterned to define the locations of the conductive traces and features on the PCB.
- Exposure and Development:The PCB design is transferred onto the photoresist layer using a photomask and exposure to ultraviolet (UV) light. After exposure, the unexposed areas of the photoresist are developed, leaving behind the patterned resist mask.
- Etching:The exposed copper areas not protected by the photoresist mask are etched away using chemical etchants. This process defines the conductive traces and features on the PCB while maintaining the minimum spacing between them.
- Resist Stripping:After etching, the remaining photoresist mask is stripped away, leaving behind the desired copper traces and features on the PCB substrate.
- Drilling:Holes are drilled in the PCB for through-hole components or vias to connect different layers in multilayer PCBs. The drilling process must maintain adequate spacing between holes and other features on the PCB.
- Surface Finish: Surface finish processes such as electroplating or immersion coating may be applied to the exposed copper surfaces to improve solderability, corrosion resistance, and overall reliability of the PCB.
- Solder Mask Application:A solder mask layer is applied to the surface of the PCB to protect the copper traces from environmental factors and prevent solder bridges during assembly. Openings are left in the solder mask to expose the solder pads for component mounting.
- Silkscreen Printing:Component designators, logos, and other markings are applied to the PCB surface using silkscreen printing.
- Final Inspection:The fabricated PCB undergoes thorough inspection to ensure that all spacing requirements, dimensional tolerances, and quality standards are met. Automated optical inspection (AOI) and other testing methods may be employed to detect any defects or deviations from the design specifications.
By following these steps and employing strict quality control measures, PCB manufacturers can produce minimum spacing PCBs that meet the electrical performance, reliability, and safety requirements for their intended applications.
How much should a Minimum Spacing PCB cost?
The cost of manufacturing a minimum spacing PCB can vary widely depending on several factors, including the complexity of the design, the number of layers, the choice of materials, the manufacturing process used, and the quantity ordered. However, I can provide a general estimate to give you an idea of the potential costs involved.
For a basic single-layer PCB with minimum spacing requirements, the cost can range from $10 to $50 per square inch for low-volume production runs. This cost typically includes materials, fabrication, and basic quality control measures.
For more complex designs or multilayer PCBs with tighter spacing requirements, the cost can increase significantly. Multilayer PCBs often require additional processes such as lamination, drilling, and plating, which can add to the overall cost. Additionally, if specialized materials or manufacturing techniques are required to meet specific spacing requirements, this can also impact the cost.
In high-volume production runs, the cost per square inch typically decreases due to economies of scale. However, the initial setup costs, such as tooling and equipment, may still represent a significant portion of the total cost.
It’s essential to obtain quotes from multiple PCB manufacturers to compare costs and ensure that you’re getting the best value for your specific requirements. Factors such as lead time, quality standards, and customer support should also be considered when selecting a manufacturer.
Keep in mind that the cost of a minimum spacing PCB is just one aspect to consider. It’s essential to prioritize quality, reliability, and adherence to design specifications to ensure the success of your electronic product.
What is Minimum Spacing PCB base material?
The choice of base material for a minimum spacing PCB depends on various factors, including the specific application, electrical performance requirements, thermal properties, and manufacturing considerations. However, some common base materials used in minimum spacing PCBs include:
- FR-4 (Flame Retardant 4):FR-4 is the most widely used substrate material for PCBs due to its cost-effectiveness, mechanical strength, and good electrical insulation properties. It consists of a woven fiberglass cloth impregnated with an epoxy resin binder. FR-4 is suitable for many applications requiring minimum spacing requirements.
- High-Temperature FR-4: For applications involving high operating temperatures, such as automotive electronics or aerospace systems, high-temperature FR-4 variants are available. These materials offer improved thermal stability and can withstand elevated temperatures without significant degradation.
- Polyimide (PI):Polyimide substrates, often referred to by the brand name Kapton, are known for their excellent thermal and chemical resistance. They are commonly used in flexible PCBs (FPCBs) and applications where space constraints or flexibility are important factors. Polyimide substrates can also meet minimum spacing requirements.
- Rogers Corporation Materials:Rogers Corporation manufactures a range of high-performance PCB substrate materials, including RO4000 series and RO3000 series laminates. These materials offer excellent electrical properties, low dielectric loss, and stable performance over a wide range of frequencies, making them suitable for high-frequency and high-speed applications with tight spacing requirements.
- Isola Materials:Isola is another prominent manufacturer of PCB substrate materials, offering a variety of laminates designed for different applications and performance requirements. Materials such as IS400, IS410, and IS620 are commonly used in applications requiring minimum spacing and high reliability.
- Metal-Core PCBs:For applications requiring efficient heat dissipation, metal-core PCBs (MCPCBs) are used. These PCBs have a metal core (typically aluminum or copper) that provides superior thermal conductivity compared to traditional substrates. MCPCBs can meet minimum spacing requirements while effectively dissipating heat from high-power components.
- Ceramic Substrates:Ceramic materials such as alumina (Al2O3) and aluminum nitride (AlN) offer excellent thermal conductivity and stability, making them suitable for high-power and high-frequency applications. Ceramic substrates can meet stringent spacing requirements and provide reliable performance in demanding environments.
When selecting a base material for a minimum spacing PCB, designers must consider factors such as dielectric constant, thermal conductivity, coefficient of thermal expansion (CTE), cost, and manufacturability. Collaboration with a reputable PCB manufacturer or material supplier can help ensure that the chosen substrate material meets the specific requirements of the application.
Which company makes Minimum Spacing PCBs?
Many well-known PCB manufacturers worldwide are capable of producing Minimum Spacing PCBs. These companies possess advanced production equipment, skilled technical teams, and extensive experience to meet the demand for high-density, high-performance circuit boards. Some notable PCB manufacturers include Foxconn Technology Group, OKI Electric, LCSC, JLCPCB, and Ventec Electronics.
As for our company, we also have the capability to produce Minimum Spacing PCBs. As a professional PCB manufacturer, we are committed to providing high-quality, reliable circuit boards to meet various customer needs. Here are some of our capabilities and advantages in producing Minimum Spacing PCBs:
- Advanced Manufacturing Equipment:We have advanced production equipment and technology, including precision lithography equipment, chemical etching lines, automated drilling equipment, etc., to achieve precise line layout and minimum spacing requirements.
- Professional Technical Team:We have a team of highly skilled professionals with extensive experience in PCB design and manufacturing. They can customize designs according to customer requirements and provide professional advice and technical support.
- Strict Quality Control:We strictly adhere to quality management systems, controlling every aspect from raw material procurement to production processing and final inspection, ensuring stable and reliable product quality.
- Flexible Production Capacity:We have flexible production capabilities to meet different batch requirements from customers, from samples to mass production.
- Fast Delivery:We are committed to providing fast and efficient services to customers, ensuring timely completion of orders and delivery of products.
In summary, our company has the capability to produce Minimum Spacing PCBs and can provide high-quality, reliable products and excellent services. We welcome customers from all walks of life to inquire and cooperate with us.
What are the 7 qualities of good customer service?
Good customer service is essential for building strong relationships with customers and ensuring their satisfaction. Here are seven qualities that characterize good customer service:
- Responsiveness:Good customer service involves being prompt and responsive to customer inquiries, concerns, and requests. Whether it’s answering phone calls, replying to emails, or addressing issues in person, responding in a timely manner shows customers that their needs are valued.
- Empathy:Empathy is the ability to understand and share the feelings of others. Good customer service representatives empathize with customers’ frustrations, concerns, and needs, demonstrating genuine care and concern for their well-being.
- Clear Communication:Effective communication is essential for providing good customer service. Customer service representatives should communicate clearly, using language that is easy to understand and free of jargon. They should listen actively to customers, ask clarifying questions, and provide accurate information and solutions.
- Problem-Solving Skills:Good customer service involves being proactive in addressing customer issues and finding solutions to their problems. Customer service representatives should be resourceful, creative, and persistent in resolving issues, even when faced with challenges.
- Professionalism:Professionalism is key to delivering good customer service. This includes maintaining a positive attitude, remaining calm under pressure, and treating customers with respect and courtesy at all times. Customer service representatives should also adhere to company policies and procedures while addressing customer needs.
- Attention to Detail:Paying attention to detail is important for ensuring accuracy and quality in customer service interactions. Whether it’s processing orders, recording information, or following up on customer requests, being thorough and meticulous helps prevent errors and build trust with customers.
- Follow-Up:Good customer service doesn’t end with resolving an immediate issue; it also involves following up to ensure customer satisfaction and loyalty. Customer service representatives should check in with customers after resolving their concerns, gather feedback, and offer additional assistance if needed.
By embodying these qualities, businesses can deliver exceptional customer service experiences that foster loyalty, positive word-of-mouth, and long-term success.
FAQs
What is a Minimum Spacing PCB?
A Minimum Spacing PCB refers to a printed circuit board (PCB) where the distance between conductive traces, components, or features is minimized to meet design requirements while maintaining electrical integrity and reliability.
Why is Minimum Spacing important in PCB design?
Minimum spacing is crucial in PCB design to prevent electrical interference, short circuits, and other issues that can arise from insufficient clearance between traces or components. It helps ensure the electrical performance and reliability of the PCB.
What factors determine Minimum Spacing requirements in PCB design?
Minimum Spacing requirements in PCB design are determined by factors such as voltage levels, signal frequencies, environmental conditions, manufacturing processes, and regulatory standards.
How are Minimum Spacing requirements specified in PCB design?
Minimum Spacing requirements are typically specified in the PCB design guidelines or design rules. Designers use computer-aided design (CAD) software to define the minimum clearance or spacing between different elements on the PCB.
What are the consequences of not meeting Minimum Spacing requirements in PCB design?
Failure to meet Minimum Spacing requirements in PCB design can lead to electrical shorts, signal cross-talk, electromagnetic interference (EMI), reduced reliability, and potential safety hazards. It can also result in manufacturing issues and higher failure rates.
How are Minimum Spacing PCBs manufactured?
Manufacturing Minimum Spacing PCBs involves using advanced fabrication processes and precise manufacturing techniques to achieve the required spacing between traces, components, and features on the PCB. This includes careful material selection, precise etching, drilling, and finishing processes.
What materials are used for Minimum Spacing PCBs?
Common materials used for Minimum Spacing PCBs include FR-4 (Flame Retardant 4), high-temperature FR-4 variants, polyimide (PI), Rogers Corporation materials, Isola materials, metal-core substrates, and ceramic substrates, depending on the application requirements.
What are some design tips for achieving Minimum Spacing in PCB layout?
Designers can achieve Minimum Spacing in PCB layout by carefully planning the placement of traces and components, using routing techniques such as orthogonal routing and avoiding sharp corners, optimizing signal paths, and adhering to design rules and guidelines provided by industry standards.