Minimum Clearance LED Circuit Board Manufacturer
Minimum Clearance LED Circuit Board Manufacturer,Minimum Clearance LED Circuit Boards (MC-LCBs) are specialized printed circuit boards designed for LED applications. They feature precise spacing between conductive elements to prevent electrical shorts and ensure safe operation. MC-LCBs prioritize thermal management, efficiently dissipating heat generated by LEDs for optimal performance and longevity. These boards are crucial for various LED lighting systems, offering enhanced reliability and adherence to safety standards. With meticulous design and manufacturing, MC-LCBs provide the foundation for reliable and efficient LED illumination in residential, commercial, automotive, and industrial settings.
What is a Minimum Clearance LED Circuit Board?
A Minimum Clearance LED Circuit Board refers to a printed circuit board (PCB) designed with specific spacing requirements between conductive traces, components, and the board’s edge to ensure safe operation and prevent electrical shorts or arcing. This spacing, or clearance, is especially crucial in LED circuit boards where high voltages or currents may be present.
In such a design, the distance between conductive elements must be sufficient to prevent electrical breakdown, which can lead to malfunctions, fires, or even explosions in extreme cases. This clearance distance is determined by factors such as the voltage level, environmental conditions, and regulatory standards.
For instance, certain safety standards like IPC-A-600 for PCB fabrication specify minimum clearance requirements based on the voltage levels present in the circuit. LEDs, though generally low-voltage devices, can still pose risks if not properly isolated on the board.
Designing a Minimum Clearance LED Circuit Board involves careful consideration of layout, insulation, and component placement to maintain adequate spacing while optimizing the board’s performance and reliability. This ensures that the LED circuit operates safely and efficiently, meeting both functional and safety requirements.
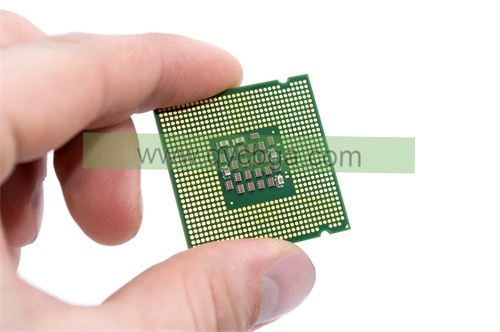
Minimum Clearance LED Circuit Board Manufacturer
What are the MC-LCB Design Guidelines?
MC-LCB (Minimum Clearance LED Circuit Board) design guidelines outline specific recommendations and requirements for designing printed circuit boards (PCBs) for LED applications while ensuring safety, reliability, and optimal performance. Here are some common guidelines:
- Minimum clearance and creepage distance:Ensure that there’s adequate space between conductive traces, components, and the board’s edge to prevent electrical arcing or short circuits. The clearance distance refers to the shortest distance between two conductors, while the creepage distance is the shortest path along the surface of the insulation between two conductors.
- Isolation of high-voltage components:If the LED circuit involves high-voltage components, such as drivers or power supplies, ensure proper isolation to prevent electric shock hazards. This may involve using isolation barriers or specific PCB layouts to maintain safe distances.
- Heat dissipation:LEDs generate heat during operation, so it’s crucial to design the PCB with adequate thermal management measures. This includes proper placement of heat sinks, vias for heat dissipation, and ensuring that components are not densely packed, which can lead to overheating.
- Component placement:Arrange components strategically to minimize signal interference, optimize signal integrity, and facilitate efficient routing of traces. Place LEDs and other heat-sensitive components away from high-temperature sources to prevent thermal stress.
- Grounding and shielding:Implement effective grounding techniques to minimize electromagnetic interference (EMI) and ensure signal integrity. Shield sensitive components from external electromagnetic fields to prevent performance degradation.
- Compliance with standards: Follow relevant industry standards and regulations, such as IPC-A-600 for PCB fabrication, UL standards for electrical safety, and any specific LED application standards. Compliance ensures that the design meets safety requirements and industry best practices.
- Testing and validation:Conduct thorough testing and validation of the PCB design to ensure that it meets performance specifications and safety standards. This may involve functional testing, electrical testing, thermal testing, and environmental testing under various operating conditions.
By adhering to these MC-LCB design guidelines, engineers can develop LED circuit boards that are not only efficient and reliable but also safe for use in various applications, ranging from consumer electronics to industrial lighting systems.
What is the MC-LCB Fabrication Process?
The fabrication process for MC-LCBs (Minimum Clearance LED Circuit Boards) involves several steps to ensure that the PCBs are manufactured to meet specific design requirements and standards. Here’s an overview of the typical fabrication process:
- Design preparation:The process begins with the preparation of the PCB design files. Engineers use PCB design software to layout the circuit, including component placement, trace routing, and adherence to MC-LCB design guidelines. Design files typically include Gerber files, drill files, and fabrication drawings.
- Substrate selection: Selecting the appropriate substrate material is crucial for MC-LCB fabrication. Common substrate materials include FR-4 (fiberglass-reinforced epoxy), metal core PCBs (MCPCBs) for enhanced thermal conductivity, and flexible substrates for applications requiring bendability.
- Substrate cleaning:Before the fabrication process begins, the substrate material undergoes thorough cleaning to remove any contaminants or residues that could affect the PCB’s performance or reliability.
- Application of copper layers:A thin layer of copper is applied to the substrate surface through processes like electroless copper deposition or lamination of copper foil. This copper layer serves as the conductive material for the circuit traces and pads.
- Photoresist application:A layer of photoresist material is applied to the copper-coated substrate. The photoresist is sensitive to ultraviolet (UV) light and serves as a mask for the subsequent etching process.
- Exposure and development:The PCB design is printed onto a film or mask, which is then aligned and exposed onto the photoresist-coated substrate using UV light. After exposure, the unexposed areas of the photoresist are dissolved away in a developing solution, leaving behind the desired circuit pattern.
- Etching:The exposed copper areas not protected by the photoresist are etched away using chemical etchants, leaving only the desired copper traces and pads on the substrate.
- Photoresist stripping:Once the etching process is complete, the remaining photoresist is removed from the substrate using a stripping solution, leaving behind the copper circuit pattern.
- Surface finish:Surface finish processes such as HASL (hot air solder leveling), ENIG (electroless nickel immersion gold), or OSP (organic solderability preservatives) are applied to the exposed copper surfaces to improve solderability and prevent oxidation.
- Final inspection:The fabricated MC-LCBs undergo a final inspection to ensure that they meet the specified design requirements, including minimum clearance distances, trace widths, and other critical parameters.
- Testing:Functional testing may be performed to verify the electrical performance of the fabricated PCBs, ensuring that they operate as intended and meet quality standards.
- Packaging and shipping:Once the MC-LCBs pass inspection and testing, they are packaged according to customer requirements and shipped to their destination for assembly into end products.
Throughout the fabrication process, strict quality control measures are implemented to ensure that MC-LCBs meet the required standards for safety, reliability, and performance in LED applications.
How do you manufacture a Minimum Clearance LED Circuit Board?
Manufacturing a Minimum Clearance LED Circuit Board (MC-LCB) involves several steps, from designing the circuit to assembling the components. Here’s an overview of the manufacturing process:
- Designing the Circuit:The process begins with designing the circuit layout using PCB design software. Engineers carefully place components, define trace routes, and ensure that minimum clearance requirements are met according to design guidelines.
- Selecting Materials:Choose the appropriate substrate material for the PCB based on factors such as thermal conductivity, flexibility, and electrical insulation properties. Common substrate materials include FR-4, aluminum, or flexible materials like polyimide.
- Preparing the Substrate:Clean the substrate material to remove any contaminants that could affect adhesion or conductivity. Then, apply a thin layer of copper to the substrate using processes like electroless plating or lamination of copper foil.
- Applying Photoresist:Coat the substrate with a layer of photoresist material. This photoresist layer will protect certain areas of the copper during the etching process.
- Exposing the Circuit Pattern:Use a film or mask containing the circuit pattern to expose the photoresist-coated substrate to UV light. The areas not blocked by the pattern will be hardened by the UV light, while the rest of the photoresist remains soluble.
- Developing the Circuit Pattern: Immerse the exposed substrate in a developing solution to dissolve the unhardened photoresist, leaving behind the circuit pattern on the substrate.
- Etching:Submerge the substrate in an etchant solution that removes the unprotected copper, leaving only the desired circuit traces and pads on the substrate.
- Stripping the Photoresist:Remove the remaining photoresist from the substrate using a stripping solution, leaving behind the clean copper traces.
- Surface Finishing:Apply a surface finish to the exposed copper surfaces to improve solderability and prevent oxidation. Common surface finishes include HASL, ENIG, or OSP.
- Component Placement:Use automated pick-and-place machines to accurately position components onto the PCB according to the circuit design.
- Soldering:Solder the components onto the PCB using reflow soldering or wave soldering techniques, depending on the type of components and assembly requirements.
- Inspection:Inspect the assembled PCBs for any defects or soldering issues using automated optical inspection (AOI) or visual inspection methods.
- Testing:Conduct electrical testing to ensure that the PCB functions correctly and meets the required performance specifications.
- Packaging:Once the PCBs pass inspection and testing, package them according to customer requirements for shipping and distribution.
Throughout the manufacturing process, quality control measures are implemented to ensure that MC-LCBs meet the necessary standards for safety, reliability, and performance in LED applications.
How much should a Minimum Clearance LED Circuit Board cost?
The cost of Minimum Clearance LED Circuit Board (MC-LCB) can vary greatly depending on several factors:
Design complexity: Circuit design complexity, including component count, layer count, and routing requirements, can significantly impact cost. More complex designs typically require more manufacturing time and resources, resulting in higher costs.
Material selection: The choice of substrate material, copper thickness, and surface treatment all affect the cost of the PCB. Higher quality materials and treatments may come with a higher price relative to standard options.
Manufacturing Quantity: Economies of scale generally apply in PCB manufacturing, meaning that larger production volumes usually result in lower unit costs. Ordering higher quantities of MC-LCB may help reduce the overall cost per board.
Production technology: Different manufacturing technologies, such as through-hole and surface mount technology (SMT), can affect the cost of PCB assembly. For high-volume production, SMT assembly tends to be more cost-effective, while for specialty components or low-volume runs, through-hole assembly may be preferred.
Additional Services: Additional services such as testing, inspection, protective coating, and packaging may incur additional costs but increase the quality and reliability of the product.
Suppliers and Locations: PCB manufacturing costs may vary based on the supplier’s pricing structure, geography, and manufacturing capabilities. Overseas manufacturers may offer lower labor costs, but may have longer lead times and potential quality risks.
As a rough estimate, the cost of manufacturing a single MC-LCB may range from a few dollars to tens of dollars, depending on the factors mentioned above. To get accurate pricing, it is best to consult with us with detailed specifications of your required MC-LCB design and production requirements.
What is the MC-LCB base material?
The base material used for Minimum Clearance LED Circuit Boards (MC-LCBs) plays a crucial role in determining the board’s performance, reliability, and cost-effectiveness. Here’s an overview of common base materials used in MC-LCB fabrication:
- FR-4 (Flame Retardant 4):FR-4 is the most widely used substrate material for PCBs, including MC-LCBs. It’s composed of woven fiberglass cloth impregnated with an epoxy resin binder. FR-4 offers excellent electrical insulation properties, mechanical strength, and dimensional stability. It’s also cost-effective and readily available, making it a popular choice for various applications.
- Metal Core PCBs (MCPCBs): MCPCBs feature a metal core, typically aluminum or copper, sandwiched between layers of dielectric material, such as FR-4 or thermally conductive prepreg. The metal core provides superior thermal conductivity, making MCPCBs ideal for LED applications where heat dissipation is critical. MCPCBs are commonly used in high-power LED lighting fixtures and automotive lighting systems.
- Flexible PCBs (Flex PCBs): Flex PCBs are made from flexible substrate materials like polyimide or polyester. They offer the advantage of being bendable and conformable to non-planar surfaces, making them suitable for applications requiring compact and lightweight designs. Flex PCBs are commonly used in wearable electronics, curved displays, and automotive interior lighting.
- High-Temperature Substrates:Some MC-LCB applications may require substrates capable of withstanding high temperatures. High-temperature materials like polyimide or ceramic substrates offer excellent thermal stability and can withstand elevated operating temperatures without degrading performance. These substrates are used in demanding applications such as aerospace, automotive, and industrial electronics.
- Specialized Substrates:In addition to the above materials, specialized substrates may be used for specific MC-LCB applications. For example, thermally conductive substrates with enhanced thermal properties are used to improve heat dissipation in high-power LED lighting systems. Ceramic substrates offer superior thermal conductivity and reliability, making them suitable for high-frequency and high-power applications.
When selecting the base material for MC-LCB fabrication, engineers consider factors such as thermal management requirements, electrical insulation properties, mechanical strength, flexibility, and cost constraints. By choosing the appropriate base material, designers can ensure that MC-LCBs meet the performance and reliability requirements of their intended applications.
Which company manufactures Minimum Clearance LED Circuit Boards?
There are many companies that manufacture Minimum Clearance LED Circuit Boards (MC-LCBs), including PCB manufacturers and electronic assembly service providers worldwide. These companies produce various types of MC-LCBs to meet the requirements of LED applications, according to customer demands and design specifications.
As our company, we also manufacture Minimum Clearance LED Circuit Boards. With advanced PCB manufacturing equipment and a skilled technical team, we are capable of designing and fabricating high-quality MC-LCBs that meet our customers’ specifications.
Our manufacturing capabilities include the following:
- Design Services:We have an experienced engineering team capable of designing Minimum Clearance LED Circuit Boards according to customer-provided specifications and requirements. Our design team ensures that the circuit layout adheres to best practices and safety standards while meeting the required minimum clearance requirements.
- Manufacturing Technology:We employ advanced PCB manufacturing technologies, including precision photolithography, chemical etching, and surface treatment processes. These technologies ensure the high precision and reliability of our PCBs while meeting the requirements of LED circuits with minimum clearance.
- Material Selection:We offer a variety of substrate material options, including FR-4, metal substrates (such as aluminum), and flexible substrates (such as polyimide), to meet the thermal management and mechanical requirements of different LED applications.
- Quality Control:We implement strict quality control procedures to ensure that each manufactured MC-LCB meets customer specifications and industry standards. We conduct comprehensive inspections and testing, including electrical testing, visual inspection, and final functional verification.
- Customer Support:We provide comprehensive customer support services, including technical consultation, design recommendations, and after-sales support. We work closely with our customers to ensure their needs are met and provide optimal solutions.
As our company, we are committed to providing customers with high-quality, reliable, and cost-effective Minimum Clearance LED Circuit Boards. Our manufacturing capabilities and professional team enable us to meet the requirements of various LED applications and offer customized solutions to our customers.
What are the 7 qualities of good customer service?
Seven qualities of good customer service include:
- Responsiveness:Good customer service involves being prompt in addressing customer inquiries, concerns, and requests. Responding to customers in a timely manner demonstrates attentiveness and a commitment to meeting their needs.
- Empathy:Empathy is the ability to understand and share the feelings of customers. It involves listening to their concerns, acknowledging their emotions, and showing genuine concern for their well-being. Empathetic customer service fosters trust and strengthens customer relationships.
- Professionalism:Professionalism entails conducting oneself with integrity, respect, and competence in all customer interactions. It involves maintaining a courteous demeanor, adhering to company policies and procedures, and providing accurate and reliable information to customers.
- Effective Communication:Good communication skills are essential for delivering excellent customer service. This includes clear and concise verbal and written communication, active listening to understand customer needs, and the ability to convey information in a manner that is easily understood.
- Problem-solving Skills:Good customer service involves the ability to effectively address customer issues and resolve problems in a timely manner. This requires critical thinking, resourcefulness, and the willingness to take ownership of customer concerns until they are satisfactorily resolved.
- Adaptability:In today’s dynamic business environment, adaptability is crucial for providing exceptional customer service. This involves being flexible and responsive to changing customer needs, preferences, and circumstances, and adjusting service delivery accordingly.
- Customer Focus:Customer-focused service means prioritizing the needs and satisfaction of customers above all else. It involves going above and beyond to exceed customer expectations, anticipating their needs, and proactively seeking opportunities to enhance their experience.
By embodying these qualities, businesses can cultivate a customer-centric culture and deliver exceptional service that fosters customer loyalty and drives business success.
FAQs
What is a Minimum Clearance LED Circuit Board (MC-LCB)?
A MC-LCB is a printed circuit board designed specifically for LED applications, with carefully considered spacing requirements between conductive traces, components, and the board’s edge to ensure safe operation and prevent electrical shorts.
What are the key features of MC-LCBs?
MC-LCBs feature minimum clearance distances between conductive elements to prevent electrical arcing or short circuits, thermal management measures to dissipate heat generated by LEDs, and reliability-enhancing design considerations specific to LED applications.
What are the advantages of using MC-LCBs in LED applications?
MC-LCBs offer enhanced safety, reliability, and performance for LED applications. They ensure proper electrical insulation, effective heat dissipation, and adherence to industry standards, resulting in improved longevity and efficiency of LED lighting systems.
What factors should be considered when designing MC-LCBs?
Design considerations for MC-LCBs include minimum clearance requirements, thermal management strategies, material selection, component placement, and adherence to relevant safety and performance standards.
What are the common applications of MC-LCBs?
MC-LCBs are used in a wide range of LED applications, including lighting fixtures for residential, commercial, and industrial settings, automotive lighting systems, signage, displays, and specialty lighting products.
How are MC-LCBs manufactured?
The manufacturing process for MC-LCBs involves designing the circuit layout, selecting appropriate materials, fabricating the PCBs with precise spacing requirements, assembling components, and conducting quality control testing to ensure compliance with specifications and standards.
What are the cost considerations for MC-LCBs?
The cost of MC-LCBs can vary based on factors such as design complexity, material selection, manufacturing volume, production techniques, additional services, and supplier choices. Requesting quotes from PCB manufacturers can provide specific cost estimates based on project requirements.