Minimum Clearance Antenna PCB Manufacturer
Minimum Clearance Antenna PCB Manufacturer,Minimum Clearance Antenna PCBs are specialized printed circuit boards designed to accommodate antennas with precise clearance requirements, ensuring optimal wireless communication performance. These PCBs are engineered with meticulous attention to detail, incorporating specific clearance distances between the antenna and other components or metallic traces. By maintaining proper clearance, these PCBs minimize signal interference, prevent signal degradation, and maximize signal strength. Commonly used in compact electronic devices such as smartphones, IoT devices, wearables, and wireless sensors, Minimum Clearance Antenna PCBs play a crucial role in enabling reliable wireless connectivity in space-constrained environments. The fabrication process involves advanced manufacturing techniques and materials selection to meet stringent performance criteria. With their compact design and optimized performance, Minimum Clearance Antenna PCBs contribute to the seamless integration of antennas into electronic devices, ensuring robust and efficient wireless communication capabilities.
What is a Minimum Clearance Antenna PCB?
A Minimum Clearance Antenna PCB refers to a printed circuit board (PCB) designed to accommodate an antenna with specific clearance requirements to ensure optimal performance. This type of PCB is engineered with precise dimensions and materials to minimize interference and maximize signal strength for wireless communication.
The term “minimum clearance” indicates the minimum distance required between the antenna and other components or metallic traces on the PCB to prevent signal degradation or short circuits. These antennas are often used in applications where space is limited, such as in small electronic devices like smartphones, IoT devices, or wearables.
Designing a Minimum Clearance Antenna PCB involves careful consideration of various factors, including antenna type, frequency range, PCB material properties, and electromagnetic interference (EMI) shielding. Engineers use specialized software and simulation tools to optimize the PCB layout for signal integrity and antenna performance.
By ensuring proper clearance and integration into the PCB design, Minimum Clearance Antenna PCBs help devices achieve reliable wireless connectivity without sacrificing space or performance. This technology is crucial for modern wireless communication systems, enabling seamless connectivity in a wide range of applications.
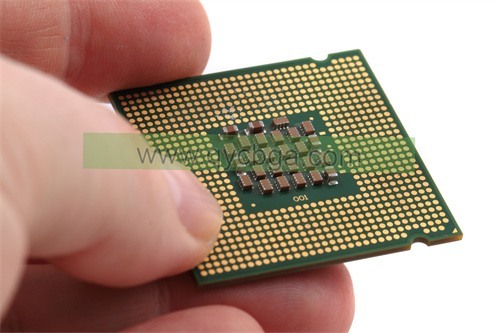
Minimum Clearance Antenna PCB Manufacturer
What are the PCB Design Guidelines for Minimum Clearance Antenna PCBs?
Designing a PCB with a minimum clearance antenna requires careful attention to several key guidelines to ensure optimal performance. Here are some important considerations:
- Clearance Distance: Maintain the minimum clearance distance between the antenna and other components, especially metallic elements such as traces, vias, and components. This distance is typically specified by the antenna manufacturer and depends on factors like frequency, antenna type, and surrounding materials.
- Ground Plane:Ensure a continuous and solid ground plane beneath the antenna. A well-designed ground plane helps to minimize RF interference and improve antenna efficiency. Avoid placing components or traces directly beneath the antenna, as this can affect radiation patterns and impedance matching.
- Antenna Orientation: Place the antenna on the PCB in the optimal orientation for the desired radiation pattern and coverage. Consider the device’s physical layout and intended usage to determine the best placement for the antenna.
- PCB Material Selection:Choose PCB materials with low dielectric constant (εr) and loss tangent (tanδ) to minimize signal loss and maintain impedance matching. Common materials for high-frequency applications include FR-4, Rogers, or PTFE-based substrates.
- Impedance Matching:Ensure proper impedance matching between the antenna and the transmission line on the PCB to minimize signal reflections and maximize power transfer. Use impedance matching techniques such as matching networks or tapered transmission lines to achieve the desired impedance.
- EMI Shielding:Incorporate EMI shielding techniques to reduce electromagnetic interference from external sources and other electronic components on the PCB. This can include adding shielding cans, ground planes, or ferrite beads to suppress unwanted RF noise.
- Avoid RF Absorbing Materials:Steer clear of materials that absorb RF energy, such as certain plastics or conductive coatings, near the antenna. These materials can attenuate the signal and degrade antenna performance.
- Test and Validation:Perform thorough testing and validation of the PCB design to verify antenna performance, including parameters such as impedance matching, radiation pattern, and gain. Use RF test equipment such as network analyzers and spectrum analyzers to characterize the antenna’s behavior in real-world conditions.
By following these PCB design guidelines, engineers can create Minimum Clearance Antenna PCBs that deliver reliable wireless connectivity and optimal performance for various applications.
What is the Minimum Clearance Antenna PCB Fabrication Process?
The fabrication process for Minimum Clearance Antenna PCBs follows standard PCB manufacturing procedures with some additional considerations specific to antenna integration. Here’s a general overview of the fabrication process:
- Design Phase:Begin by designing the PCB layout using CAD (Computer-Aided Design) software. Incorporate the antenna design into the layout, ensuring proper clearance distances and placement according to design guidelines. Verify the design through simulations to optimize antenna performance.
- Material Selection:Choose the appropriate PCB material based on factors such as frequency range, dielectric constant, and thermal properties. Common materials for high-frequency applications include FR-4, Rogers, or PTFE-based substrates. Ensure that the selected material meets the requirements for impedance matching and signal integrity.
- Substrate Preparation:Prepare the substrate material by cutting it to the desired size and shape. Clean the substrate surface to remove any contaminants that could affect adhesion or conductivity.
- Copper Cladding:Apply a thin layer of copper foil to both sides of the substrate material using lamination or bonding techniques. The copper layer forms the conductive traces, pads, and ground planes of the PCB.
- Antenna Integration:Integrate the antenna into the PCB layout according to the design specifications. Place the antenna on the substrate with the required clearance distances from other components and metallic elements. Ensure proper orientation and alignment for optimal radiation patterns.
- Etching:Use chemical etching or mechanical milling techniques to remove excess copper from the substrate, leaving behind the desired conductive traces and antenna patterns. Etching is typically performed using photolithography to define the pattern before selective copper removal.
- Drilling:Drill holes in the substrate for component mounting and through-hole connections. Ensure precise alignment and hole placement according to the PCB design.
- Surface Finish:Apply a surface finish to the PCB to protect the copper traces from oxidation and provide solderability for component attachment. Common surface finishes include HASL (Hot Air Solder Leveling), ENIG (Electroless Nickel Immersion Gold), and OSP (Organic Solderability Preservatives).
- Component Assembly:Mount electronic components onto the PCB using soldering techniques such as reflow soldering or wave soldering. Place components carefully to avoid interfering with the antenna and maintain clearance distances.
- Testing and Validation:Conduct electrical testing and validation of the fabricated PCB to verify antenna performance, impedance matching, and signal integrity. Use RF test equipment such as network analyzers and spectrum analyzers to characterize the antenna’s behavior under real-world conditions.
- Final Inspection:Perform a final inspection of the fabricated PCB to ensure quality and adherence to design specifications. Check for any defects or inconsistencies that could affect performance or reliability.
By following these fabrication steps and paying close attention to antenna integration and clearance requirements, engineers can produce Minimum Clearance Antenna PCBs that meet the desired performance criteria for wireless communication applications.
How do you manufacture a Minimum Clearance Antenna PCB?
Manufacturing a Minimum Clearance Antenna PCB involves several steps, each critical for ensuring the antenna’s optimal performance. Here’s a detailed process:
- Design and Layout:Begin by designing the PCB layout using specialized CAD software. Integrate the antenna design into the layout while adhering to minimum clearance requirements specified by the antenna manufacturer. Ensure that the antenna is positioned for optimal performance and radiation pattern.
- Material Selection:Choose the appropriate PCB material based on factors such as frequency range, dielectric constant, and thermal properties. Common materials for high-frequency applications include FR-4, Rogers, or PTFE-based substrates. Select a material that meets impedance matching requirements and provides good signal integrity.
- Substrate Preparation:Prepare the PCB substrate by cutting it to the desired size and shape. Clean the substrate surface thoroughly to remove any contaminants that could affect adhesion or conductivity.
- Copper Cladding:Apply a thin layer of copper foil to both sides of the substrate using lamination or bonding techniques. The copper layer forms the conductive traces, pads, and ground planes of the PCB. Ensure that the copper thickness is suitable for the antenna design and impedance matching requirements.
- Antenna Integration:Integrate the antenna into the PCB layout according to the design specifications. Place the antenna on the substrate with the required clearance distances from other components and metallic elements. Pay attention to proper orientation and alignment for optimal radiation patterns.
- Etching:Use chemical etching or mechanical milling techniques to remove excess copper from the substrate, leaving behind the desired conductive traces and antenna patterns. Etching is typically performed using photolithography to define the pattern before selective copper removal.
- Drilling: Drill holes in the substrate for component mounting and through-hole connections. Ensure precise alignment and hole placement according to the PCB design.
- Surface Finish:Apply a surface finish to the PCB to protect the copper traces from oxidation and provide solderability for component attachment. Common surface finishes include HASL (Hot Air Solder Leveling), ENIG (Electroless Nickel Immersion Gold), and OSP (Organic Solderability Preservatives).
- Component Assembly:Mount electronic components onto the PCB using soldering techniques such as reflow soldering or wave soldering. Place components carefully to avoid interfering with the antenna and maintain clearance distances.
- Testing and Validation:Conduct electrical testing and validation of the manufactured PCB to verify antenna performance, impedance matching, and signal integrity. Use RF test equipment such as network analyzers and spectrum analyzers to characterize the antenna’s behavior under real-world conditions.
- Final Inspection:Perform a final inspection of the manufactured PCB to ensure quality and adherence to design specifications. Check for any defects or inconsistencies that could affect performance or reliability.
By following these manufacturing steps and paying close attention to antenna integration and clearance requirements, manufacturers can produce Minimum Clearance Antenna PCBs that meet the desired performance criteria for wireless communication applications.
How much should a Minimum Clearance Antenna PCB cost?
The cost of a Minimum Clearance Antenna PCB can vary widely depending on several factors, including:
- Complexity of Design:The complexity of the PCB design, including the number of layers, size, and intricacy of the antenna pattern, can significantly impact the cost. More complex designs may require advanced manufacturing processes and specialized materials, resulting in higher costs.
- Materials:The choice of PCB substrate material, copper thickness, and surface finish can affect the cost. High-frequency materials such as Rogers or PTFE-based substrates tend to be more expensive than standard FR-4, while surface finishes like ENIG are costlier than HASL.
- Manufacturing Process:The manufacturing process used to produce the PCB, including etching, drilling, and component assembly, can influence the cost. Advanced processes such as laser drilling or selective plating may incur additional expenses compared to standard techniques.
- Volume and Batch Size:The quantity of PCBs ordered and the batch size can impact the unit cost. Larger volume orders typically benefit from economies of scale, with lower per-unit costs compared to small production runs.
- Testing and Quality Assurance:Testing and validation processes, including electrical testing and inspection for defects, contribute to the overall cost. Higher levels of testing and quality assurance may result in higher prices but ensure better reliability and performance.
- Supplier and Location:The choice of PCB manufacturer or supplier and their location can affect the cost due to differences in labor, overhead, and shipping expenses. Offshore manufacturers may offer lower prices but could have longer lead times and potential quality issues.
As a rough estimate, the cost of a Minimum Clearance Antenna PCB can range from a few dollars to several tens or even hundreds of dollars per unit, depending on the aforementioned factors. For precise pricing, it’s recommended to obtain quotes from multiple PCB manufacturers based on your specific design requirements and volume needs.
What is the Minimum Clearance Antenna PCB base material?
The choice of base material for a Minimum Clearance Antenna PCB depends on various factors such as frequency range, dielectric constant, thermal properties, and cost considerations. However, certain materials are commonly used due to their suitability for high-frequency applications and antenna integration. Here are some typical base materials for Minimum Clearance Antenna PCBs:
- FR-4 (Flame Retardant 4):FR-4 is a widely used standard substrate material for PCBs due to its good electrical properties, mechanical strength, and cost-effectiveness. It is suitable for antennas operating at lower frequencies and offers moderate dielectric constant and loss tangent.
- Rogers Materials:Rogers Corporation produces a range of high-frequency laminates specifically designed for RF and microwave applications. Materials such as RO3000 series or RO4000 series offer low dielectric loss, tight control of dielectric constant, and excellent stability over a wide frequency range, making them ideal for high-performance antennas.
- PTFE-Based Substrates:Polytetrafluoroethylene (PTFE) based materials, such as Teflon, offer superior electrical properties, including low dielectric constant, low loss tangent, and high thermal stability. These materials are suitable for high-frequency antennas where signal integrity and performance are critical.
- Ceramic Substrates:Ceramic substrates provide excellent electrical properties, thermal conductivity, and dimensional stability, making them suitable for high-power and high-frequency applications. Alumina (Al2O3) and Aluminum Nitride (AlN) are commonly used ceramic materials for antennas operating at microwave frequencies.
- Flexible Substrates:For applications requiring flexibility or conformal antenna designs, flexible substrates such as polyimide (e.g., Kapton) or liquid crystal polymer (LCP) can be used. These materials offer good electrical properties and mechanical flexibility, allowing for compact and versatile antenna designs.
The selection of the base material depends on the specific requirements of the antenna design, including operating frequency, impedance matching, size constraints, and environmental factors. It’s essential to choose a material that provides the desired electrical performance while meeting cost and manufacturability considerations.
Which company manufactures Minimum Clearance Antenna PCBs?
Many companies offer manufacturing services for customized Minimum Clearance Antenna PCBs. These companies are typically professional printed circuit board manufacturers with advanced equipment and technology capable of meeting the requirements of high-frequency and high-performance antennas. Some globally renowned PCB manufacturers and suppliers, such as Rogers Corporation in the United States, Samsung Chemical in Japan, and Delta Electronics in Taiwan, provide such services.
As for our company, we have extensive experience and a professional team capable of producing Minimum Clearance Antenna PCBs. Our manufacturing processes and equipment have been carefully selected and optimized to ensure the production of high-quality, high-performance antenna PCBs. Our strengths include:
- Professional Team:We have an experienced team of engineers familiar with antenna design and the latest technologies and best practices in PCB manufacturing.
- Advanced Equipment:We are equipped with advanced production equipment, including high-precision chemical etching machines, laser drilling machines, and automated assembly lines, ensuring the accuracy and consistency of PCB manufacturing.
- Quality Control:We strictly adhere to a quality management system, including full-process control from raw material procurement to finished product inspection, ensuring that each step meets international standards and customer requirements.
- Fast Delivery: We have efficient production processes and flexible production arrangements, allowing us to provide fast delivery cycles according to customer needs.
- Customized Service:We can customize Minimum Clearance Antenna PCBs according to customer-specific requirements, including customization of dimensions, materials, impedance matching, and other aspects.
In summary, our company has the capability to produce high-quality Minimum Clearance Antenna PCBs and provide customized solutions according to customer needs. We are committed to providing customers with high-quality products and satisfactory services, working together with them to achieve business goals.
What are the 7 qualities of good customer service?
Good customer service is essential for building strong relationships with customers and fostering loyalty. Here are seven qualities that characterize effective customer service:
- Responsiveness:Good customer service involves being prompt and responsive to customer inquiries, concerns, and requests. Responding quickly to customer needs demonstrates attentiveness and a commitment to providing timely assistance.
- Empathy:Empathy is the ability to understand and share the feelings of others. Good customer service representatives empathize with customers’ situations, show genuine concern for their issues, and strive to address their needs with compassion and understanding.
- Communication Skills:Effective communication is key to delivering good customer service. Customer service representatives should possess excellent verbal and written communication skills, listening attentively to customers, explaining solutions clearly, and maintaining a positive and professional demeanor at all times.
- Problem-Solving Abilities:Good customer service involves being able to resolve customer issues and problems effectively. Customer service representatives should be resourceful, proactive, and capable of finding creative solutions to meet customers’ needs and exceed their expectations.
- Product Knowledge:Having a thorough understanding of the products or services offered is crucial for providing good customer service. Customer service representatives should be knowledgeable about the features, benefits, and usage of the products or services to address customer inquiries and provide accurate information and assistance.
- Adaptability: Every customer interaction is unique, and good customer service requires adaptability to different situations and customer preferences. Customer service representatives should be flexible and adaptable, tailoring their approach to meet the needs and preferences of individual customers.
- Professionalism:Good customer service is characterized by professionalism in every interaction. Customer service representatives should conduct themselves with integrity, courtesy, and respect, treating all customers with dignity and maintaining confidentiality when necessary.
By embodying these qualities, organizations can deliver exceptional customer service experiences that build trust, loyalty, and satisfaction among their customer base.
FAQs
What is a Minimum Clearance Antenna PCB?
A Minimum Clearance Antenna PCB is a printed circuit board specifically designed to accommodate an antenna with precise clearance requirements to ensure optimal performance for wireless communication.
Why is clearance important in antenna PCB design?
Clearance is important in antenna PCB design to minimize interference and maximize signal strength. Maintaining proper clearance distances between the antenna and other components or metallic traces helps prevent signal degradation or short circuits.
What factors influence the clearance requirements for antenna PCBs?
Clearance requirements for antenna PCBs are influenced by factors such as antenna type, frequency range, surrounding materials, and electromagnetic interference (EMI) considerations.
What are the common applications of Minimum Clearance Antenna PCBs?
Minimum Clearance Antenna PCBs are used in various applications where space is limited and reliable wireless communication is crucial, such as smartphones, IoT devices, wearables, and wireless sensors.
How are Minimum Clearance Antenna PCBs manufactured?
Manufacturing Minimum Clearance Antenna PCBs involves following standard PCB fabrication processes with additional considerations for antenna integration, such as maintaining precise clearance distances and optimizing material selection.
What are the advantages of using Minimum Clearance Antenna PCBs?
The advantages of using Minimum Clearance Antenna PCBs include optimized wireless performance, reduced interference, space-saving design, and enhanced reliability in wireless communication applications.
How can I ensure the optimal performance of a Minimum Clearance Antenna PCB?
To ensure optimal performance, it’s essential to carefully design the PCB layout, select appropriate materials, maintain proper clearance distances, and perform thorough testing and validation of the antenna’s behavior under real-world conditions.