CPU Package Substrates Manufacturer
CPU Package Substrates Manufacturer,CPU Package Substrates are specialized materials crucial for the performance and reliability of central processing units (CPUs). These substrates provide a stable platform for mounting and interconnecting the CPU chip to other components on the motherboard. They are engineered to withstand high temperatures and electrical stress, ensuring efficient heat dissipation and electrical signal integrity. CPU Package Substrates feature advanced materials like ceramics or organic substrates with embedded metal layers for improved thermal conductivity and signal transmission. Their design supports high-speed data processing and low-power consumption, making them essential components in modern computing devices ranging from laptops and desktops to servers and embedded systems.
What is a CPU Package Substrate?
A CPU Package Substrate is a crucial component in the assembly of central processing units (CPUs). It serves as the interface between the silicon die of the CPU and the package that houses it. This substrate facilitates electrical connections between the CPU die and the package’s external pins, ensuring efficient data transmission and power distribution.
Typically made from advanced materials like fiberglass-reinforced epoxy (FR4) or more specialized substrates such as ceramic, these substrates are designed to withstand high temperatures, provide excellent electrical insulation, and support the intricate circuitry necessary for CPU operation. The substrate also plays a role in heat dissipation, helping to manage the thermal output of the CPU.
Manufacturing processes for CPU package substrates involve precision etching, drilling, and plating to create intricate patterns of conductive traces that connect the CPU die to the package pins. These processes ensure reliability and performance under demanding conditions, making CPU package substrates integral to the functionality and longevity of modern processors.
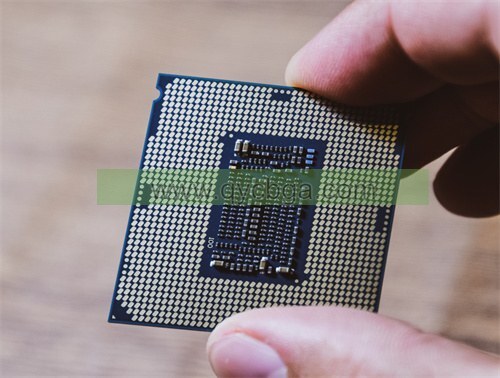
CPU Package Substrates Manufacturer
What are the CPU Package Substrate Design Guidelines?
Design guidelines for CPU package substrates typically include several key considerations to ensure optimal performance and reliability of the processor. Here are some common guidelines:
- Material Selection:Choose a substrate material that meets thermal, electrical, and mechanical requirements. Common materials include FR4 for standard applications and more advanced materials like ceramic or metal core substrates for high-performance CPUs.
- Layer Configuration: Determine the number of layers needed based on the complexity of the CPU design. More layers allow for denser routing of signal traces and power planes, reducing signal interference and optimizing power distribution.
- Signal Integrity: Design controlled impedance traces to minimize signal loss, reflection, and cross-talk. Proper routing techniques, such as avoiding right-angle bends and maintaining consistent trace widths, are crucial for maintaining signal integrity.
- Thermal Management: Incorporate thermal vias, thermal pads, or metal core substrates to efficiently dissipate heat generated by the CPU. Thermal vias connect the top and bottom layers of the substrate to transfer heat away from the die to the heat sink or cooling solution.
- Power Distribution: Design robust power delivery networks (PDNs) with adequate power and ground planes. Use low impedance paths for power distribution to minimize voltage drops and ensure stable operation of the CPU.
- Dimensional Accuracy: Ensure precise dimensional control to match the CPU die and package dimensions accurately. This ensures proper alignment during assembly and minimizes mechanical stress on the substrate.
- Manufacturability: Consider manufacturability factors such as panelization, fiducial markings for alignment, and solder mask requirements. These factors facilitate efficient production and assembly processes.
- Reliability and Testing: Design for reliability by considering factors such as solder joint reliability, thermal cycling, and mechanical shock resistance. Conduct thorough testing to validate electrical performance and reliability under various operating conditions.
By adhering to these design guidelines, engineers can optimize the performance, reliability, and manufacturability of CPU package substrates, ensuring robust operation of the processor in diverse applications.
What is the CPU Package Substrate Fabrication Process?
The fabrication process for CPU package substrates involves several steps to create the complex circuitry that connects the CPU die to the external package pins. Here’s a general overview of the fabrication process:
- Substrate Material Selection: Choose a suitable substrate material based on the CPU’s thermal, electrical, and mechanical requirements. Common materials include FR4 for standard applications and more advanced materials like ceramic or metal core substrates for high-performance CPUs.
- Panel Preparation: Prepare substrate panels of appropriate sizes for fabrication. The panels are typically made from laminates of the chosen substrate material.
- Drilling: Use precision drilling machines to create holes (vias) in the substrate panels. These vias serve various purposes, including component mounting, electrical connections between layers, and thermal management.
- Inner Layer Imaging: Apply a photo-sensitive material (photoresist) to the substrate panels. Use photolithography techniques to expose the photoresist through a photomask, creating patterns for the inner layer circuitry.
- Copper Plating: Electroplate copper onto the panel surfaces and inside the drilled vias to form conductive traces and vias. The excess copper is typically removed by chemical etching, leaving behind the desired circuit patterns.
- Lamination: Bond multiple substrate layers together using heat and pressure to create a multi-layered stack. Each layer contributes to the complex interconnections needed for the CPU.
- Outer Layer Imaging: Apply another layer of photoresist and expose it to light through a photomask to define the outer layer circuit patterns. Copper is deposited and etched as before to form the outer layer traces.
- Surface Finish: Apply a surface finish to protect exposed copper traces and facilitate soldering during component assembly. Common surface finishes include immersion gold (ENIG), immersion silver, or organic solderability preservatives (OSP).
- Solder Mask Application: Apply solder mask ink over the substrate surface, leaving openings (exposed pads) for component attachment and electrical testing. The solder mask protects copper traces from oxidation and facilitates soldering.
- Silkscreen Printing: Optionally, apply markings and legends using silkscreen printing to indicate component placement, polarity, and other critical information.
- Final Inspection and Testing: Conduct rigorous quality checks and electrical testing to ensure the substrate meets design specifications and performance requirements.
- Routing and Singulation: After testing, the substrate panels are routed to separate individual CPU package substrates. This step ensures each substrate is ready for final assembly with the CPU die and other components.
By following these fabrication steps with precision and quality control measures, manufacturers can produce high-performance CPU package substrates that meet the stringent demands of modern processors.
How do you manufacture a CPU Package Substrate?
Manufacturing a CPU package substrate involves a series of intricate processes to create the essential interface between the CPU die and the external package. Here’s a detailed overview of the manufacturing process:
- Substrate Material Selection: Choose a substrate material based on the CPU’s thermal, electrical, and mechanical requirements. Common materials include FR4 for standard applications and ceramic or metal core substrates for high-performance CPUs.
- Panel Preparation: Prepare substrate panels of appropriate sizes from laminates of the chosen substrate material. These panels will undergo several processing steps to create the multi-layered substrate.
- Drilling: Use precision drilling machines to create holes (vias) in the substrate panels. These vias serve various purposes, including component mounting, electrical connections between layers, and thermal management.
- Inner Layer Imaging: Apply a photo-sensitive material (photoresist) to the substrate panels. Use photolithography techniques to expose the photoresist through a photomask, defining the patterns for the inner layer circuitry. The exposed areas allow for copper deposition.
- Copper Plating: Electroplate copper onto the panel surfaces and inside the drilled vias to form conductive traces and connections between layers. Excess copper is typically removed by chemical etching, leaving behind the desired circuit patterns.
- Lamination: Bond multiple substrate layers together using heat and pressure to create a multi-layered stack. Each layer contributes to the complex interconnections needed for the CPU substrate.
- Outer Layer Imaging: Apply another layer of photoresist and expose it to light through a photomask to define the outer layer circuit patterns. Copper is deposited and etched as before to form the outer layer traces.
- Surface Finish: Apply a surface finish to protect exposed copper traces and facilitate soldering during component assembly. Common surface finishes include immersion gold (ENIG), immersion silver, or organic solderability preservatives (OSP).
- Solder Mask Application: Apply solder mask ink over the substrate surface, leaving openings (exposed pads) for component attachment and electrical testing. The solder mask protects copper traces from oxidation and facilitates soldering.
- Silkscreen Printing: Optionally, apply markings and legends using silkscreen printing to indicate component placement, polarity, and other critical information.
- Final Inspection and Testing: Conduct rigorous quality checks and electrical testing to ensure the substrate meets design specifications and performance requirements. This includes checking for dimensional accuracy, electrical continuity, and insulation resistance.
- Routing and Singulation: After testing, the substrate panels are routed to separate individual CPU package substrates. This step ensures each substrate is ready for final assembly with the CPU die and other components.
- Assembly: Mount the CPU die onto the substrate using die attach methods, such as adhesive bonding or soldering. Wire bonding or flip-chip bonding techniques are used to connect the die’s pads to the substrate’s electrical traces.
- Encapsulation: Encapsulate the assembled substrate and CPU die with a protective material, such as molding compound or underfill resin. This protects the assembly from mechanical damage and environmental factors.
- Final Testing: Perform final functional testing and validation to ensure the CPU package substrate operates reliably under specified conditions. This includes thermal cycling tests, electrical performance tests, and sometimes, reliability testing over extended periods.
By following these manufacturing steps with precision and quality control measures, manufacturers produce CPU package substrates that meet the stringent requirements of modern processors in terms of performance, reliability, and longevity.
How much should a CPU Package Substrate cost?
The cost of a CPU package substrate can vary significantly based on several factors, including materials used, substrate complexity, manufacturing processes, and volume production quantities. Here are some key considerations influencing the cost:
- Substrate Material: Different materials (e.g., FR4, ceramic, metal core) vary in cost. Ceramic substrates, known for high performance, typically cost more than FR4 due to their superior thermal and electrical properties.
- Layer Count: The number of layers in the substrate affects manufacturing complexity and cost. High-layer count substrates require more intricate processes and materials, increasing production costs.
- Manufacturing Processes: Advanced fabrication techniques, such as precision drilling, copper plating, and photolithography, add to the substrate’s manufacturing cost. Additional processes like surface finish application and testing also contribute.
- Design Complexity: Substrates with complex circuit patterns, fine pitch traces, and stringent design requirements may require more sophisticated manufacturing equipment and expertise, influencing costs.
- Volume Production: Economies of scale apply—larger production runs generally lower the cost per substrate due to optimized production efficiencies and reduced setup costs per unit.
- Quality and Reliability Standards:Meeting stringent quality standards and reliability requirements through rigorous testing and validation processes can add to the overall cost.
- Supplier and Location: Costs can vary based on the substrate manufacturer’s capabilities, location, and overhead expenses.
To provide a rough estimate, CPU package substrates can range in cost from a few dollars to tens of dollars per unit, depending on the above factors. Custom substrates designed for specialized applications or high-performance CPUs typically command higher prices due to their advanced materials and manufacturing requirements.
For precise pricing, it’s advisable to consult with substrate manufacturers or suppliers who can provide detailed quotes based on specific design requirements, quantities, and desired quality standards.
What is CPU Package Substrate base material?
The base material for CPU package substrates can vary depending on the specific requirements of the CPU and its intended application. Some common base materials used for CPU package substrates include:
- FR4 (Flame Retardant 4): FR4 is a widely used substrate material for standard CPUs. It is an epoxy-based laminate reinforced with woven glass fibers, providing good electrical insulation and mechanical strength at a relatively low cost.
- Ceramic: Ceramic substrates, such as alumina (Al2O3) or aluminum nitride (AlN), are used for high-performance CPUs. Ceramic offers excellent thermal conductivity, allowing for efficient heat dissipation, as well as high electrical insulation and stability over a wide temperature range.
- Metal Core Substrates: Metal core substrates, typically aluminum or copper, are used in CPUs that require enhanced thermal management. These substrates have a metal core for heat dissipation, with dielectric layers for electrical insulation and signal routing.
- Composite Materials: Some advanced CPU substrates may use composite materials combining elements of ceramics and polymers to achieve specific thermal, electrical, and mechanical properties tailored to the CPU’s requirements.
The choice of substrate base material depends on factors such as thermal management needs, electrical performance requirements, mechanical strength, cost considerations, and the overall performance goals of the CPU design. Each material has its advantages and is selected based on the specific application and performance criteria of the CPU package.
Which company makes CPU Package Substrates?
CPU Package Substrates are manufactured by several globally renowned companies, each with its own unique technologies and manufacturing capabilities. Here are some of the major manufacturers of CPU Package Substrates:
- Nippon Denso Corporation: As a leading Japanese manufacturer of electronic components, Nippon Denso specializes in the development and production of high-performance CPU Package Substrates.
- Murata Manufacturing Co., Ltd.: As a global leader in electronic component manufacturing, Murata Manufacturing has extensive experience and technological expertise in the field of high-density and high-performance circuit boards.
- Texas Instruments: As a global leader in semiconductor and electronic solutions, Texas Instruments not only manufactures high-performance CPU Package Substrates but also provides related solutions and technical support.
- Intel Corporation: As a global leader in semiconductor manufacturing and technology innovation, Intel has advanced technologies and expertise in the design and manufacturing of CPU Package Substrates.
- Samsung Electronics: As one of the largest electronics companies in South Korea, Samsung Electronics has also made significant achievements and technological accumulation in the manufacturing of high-performance CPU Package Substrates.
Our company is also capable of producing high-quality CPU Package Substrates, equipped with advanced manufacturing equipment and a skilled technical team. We specialize in providing customized solutions to customers, including the design and manufacturing of CPU Package Substrates based on various materials such as FR4, ceramics, metal core, and others. Our production processes adhere strictly to international standards, ensuring that our products meet the quality and performance requirements of our customers. Whether in thermal management, electrical performance, or mechanical strength, we can provide customized solutions tailored to meet the diverse requirements of CPU Package Substrates in different application environments.
What are the 7 qualities of good customer service?
The seven qualities of good customer service are essential for creating positive interactions and building strong relationships with customers. Here they are:
- Responsiveness: Good customer service involves being prompt and proactive in addressing customer inquiries, requests, or issues. Responding quickly shows customers that their concerns are valued and that you are committed to helping them promptly.
- Empathy: Demonstrating empathy means understanding and sharing the feelings of your customers. It involves listening attentively to their concerns, showing compassion, and acknowledging their emotions to build trust and rapport.
- Communication Skills: Effective communication is crucial in customer service. This includes clear and concise verbal communication, active listening to fully understand customer needs, and the ability to explain solutions or information in a way that is easily understood.
- Problem-Solving Skills: Good customer service requires the ability to resolve issues efficiently and effectively. This involves identifying the root cause of problems, offering viable solutions, and taking ownership to ensure the customer’s needs are met.
- Professionalism: Maintaining a professional demeanor at all times demonstrates respect and competence to customers. This includes being courteous, respectful, and maintaining a positive attitude even in challenging situations.
- Knowledgeability: Customers expect knowledgeable support when they reach out for assistance. Having a thorough understanding of your products or services, as well as company policies and procedures, enables you to provide accurate information and advice to customers.
- Customer Focus: Good customer service is ultimately about prioritizing the needs and satisfaction of customers. This involves being proactive in anticipating their needs, going above and beyond to exceed expectations, and consistently striving to deliver exceptional service.
By embodying these qualities, organizations can cultivate a customer-centric culture that fosters loyalty, satisfaction, and positive word-of-mouth recommendations.
FAQs
What is a CPU Package Substrate?
A CPU Package Substrate is a crucial component in electronic devices that serves as a platform to mount and interconnect the CPU (Central Processing Unit) die with external components and the motherboard. It provides electrical pathways for signals, power delivery, and thermal management.
What materials are used to make CPU Package Substrates?
CPU Package Substrates can be made from various materials depending on performance requirements. Common materials include FR4 (Flame Retardant 4), ceramic (alumina or aluminum nitride), and metal core substrates (aluminum or copper). Each material offers specific benefits such as thermal conductivity, electrical properties, and mechanical strength.
What are the key considerations in designing CPU Package Substrates?
Design considerations include thermal management to dissipate heat generated by the CPU, routing of high-speed signals with controlled impedance, ensuring adequate power delivery with low impedance paths, and mechanical stability to withstand assembly and operating conditions.
How are CPU Package Substrates manufactured?
The manufacturing process involves several steps, including substrate material selection, drilling vias for electrical connections, copper plating for conductive traces, lamination of multiple layers, application of solder mask and surface finish, and final testing and inspection to ensure quality and reliability.
What are the benefits of using ceramic substrates for CPU packages?
Ceramic substrates offer excellent thermal conductivity, allowing efficient heat dissipation from the CPU die. They also provide high electrical insulation, stability over a wide temperature range, and durability, making them suitable for high-performance CPUs in demanding applications.
How do CPU Package Substrates contribute to overall system performance?
CPU Package Substrates play a critical role in enhancing system performance by providing reliable electrical connections between the CPU die and other components, optimizing signal integrity, managing thermal dissipation effectively, and ensuring overall system reliability.
What are some challenges in designing and manufacturing CPU Package Substrates?
Challenges include achieving fine-pitch design requirements for high-density circuits, managing thermal issues to prevent overheating, ensuring compatibility with advanced packaging technologies, and meeting stringent reliability standards for long-term operation.