Advanced Cavity PCB Manufacturer
Advanced Cavity PCB Manufacturer,Advanced Cavity PCBs represent a cutting-edge solution in electronic circuitry, featuring intricately designed voids within the board structure. These cavities serve a multitude of purposes, including enhanced thermal management, electromagnetic interference (EMI) shielding, and mechanical stability. By strategically incorporating these voids, Advanced Cavity PCBs excel in dissipating heat generated by high-power components, ensuring optimal performance and reliability even in demanding environments. Moreover, the ability to shield sensitive electronics from EMI ensures signal integrity and reduces the risk of interference, making them ideal for applications where reliability is paramount. With their versatility and advanced design, Advanced Cavity PCBs find applications across various industries, including aerospace, automotive, telecommunications, and power electronics. Their ability to meet the stringent requirements of modern electronic systems underscores their importance in driving innovation and advancing technological capabilities.
What is an Advanced Cavity PCB?
An Advanced Cavity PCB, also known as an AC-PCB, is a specialized type of printed circuit board designed for specific applications requiring enhanced thermal management, electromagnetic interference (EMI) shielding, and mechanical stability. These PCBs incorporate cavities or voids within the board structure, which can be filled with various materials like thermal interface materials (TIMs) or encapsulants to improve heat dissipation.
The cavities in an AC-PCB serve multiple purposes. Firstly, they provide space for components that generate heat, allowing for more efficient cooling through the use of heatsinks or other thermal management solutions. Additionally, these voids can act as chambers for shielding sensitive components from electromagnetic interference, reducing the risk of signal degradation or cross-talk.
The construction of AC-PCBs involves intricate design and manufacturing processes to ensure the precise placement of components and cavities while maintaining electrical integrity and reliability. Advanced fabrication techniques such as controlled-depth milling or laser drilling are often employed to create the cavities with high precision.
AC-PCBs find applications in a variety of industries, including aerospace, automotive, telecommunications, and power electronics, where thermal management and EMI shielding are critical for performance and reliability. They are particularly beneficial in high-power and high-frequency electronic systems where traditional PCBs may struggle to meet thermal and electromagnetic requirements.
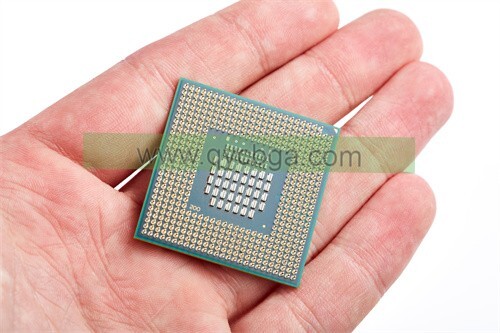
Advanced Cavity PCB Manufacturer
What are the Advanced Cavity PCB Design Guidelines?
Designing Advanced Cavity PCBs requires careful consideration of various factors to ensure optimal performance and reliability. Here are some advanced cavity PCB design guidelines:
- Thermal Management: Incorporate sufficient thermal vias and heat dissipation structures to facilitate efficient heat transfer from components to the board’s exterior. Ensure that the cavities are strategically positioned to maximize airflow and cooling.
- Cavity Placement: Place cavities strategically to accommodate high-power components or sensitive electronics that require thermal isolation or EMI shielding. Consider the overall board layout and component placement to minimize signal interference and optimize thermal performance.
- EMI Shielding: Design cavities with appropriate dimensions and shielding materials to provide effective electromagnetic interference (EMI) shielding for sensitive components. Ensure proper grounding and shielding connections to minimize EMI leakage.
- Material Selection: Choose PCB materials with high thermal conductivity and low dielectric loss for enhanced thermal management and signal integrity. Consider using specialized laminates with embedded heat spreaders or conductive fillers for improved thermal performance.
- Cavity Fill Materials: Select suitable cavity fill materials such as thermal interface materials (TIMs), encapsulants, or conformal coatings to enhance thermal conductivity, mechanical stability, and EMI shielding. Ensure compatibility with surrounding components and PCB materials.
- Structural Integrity:Design cavities and board structures to maintain mechanical strength and rigidity while minimizing weight and size. Consider the impact of cavity design on PCB bending and flexural properties, especially in applications with harsh operating conditions.
- Signal Integrity:Minimize signal distortion and cross-talk by carefully routing signal traces away from cavities and ensuring proper impedance matching. Use differential signaling and ground planes to reduce electromagnetic interference and maintain signal integrity.
- Manufacturability: Optimize the design for manufacturability by considering the capabilities and limitations of the chosen fabrication processes, such as controlled-depth milling, laser drilling, or cavity filling techniques. Provide clear documentation and guidelines for assembly and testing.
By following these advanced cavity PCB design guidelines, engineers can create PCBs that meet the demanding requirements of modern electronic systems, ensuring optimal performance, reliability, and thermal management.
What is the Advanced Cavity PCB Fabrication Process?
The fabrication process for Advanced Cavity PCBs involves several specialized steps to create the cavities and integrate thermal management and EMI shielding features. Here’s an overview of the advanced cavity PCB fabrication process:
- Design Preparation: The process begins with detailed design preparation using computer-aided design (CAD) software. Engineers create a comprehensive layout that includes the placement of components, routing of traces, and design of cavities according to specific thermal and EMI shielding requirements.
- Material Selection: Choose appropriate PCB materials with high thermal conductivity and suitable dielectric properties to meet the thermal management and performance requirements of the application. Specialized laminates with embedded heat spreaders or conductive fillers may be selected for enhanced thermal performance.
- Cavity Creation: Advanced cavity PCBs require precise cavity creation techniques such as controlled-depth milling or laser drilling. CNC (Computer Numerical Control) machines are used to mill or drill cavities with high accuracy and repeatability according to the design specifications.
- Cavity Filling: Once the cavities are created, they are filled with thermal interface materials (TIMs), encapsulants, or other cavity fill materials to enhance thermal conductivity, mechanical stability, and EMI shielding. The filling process must be carefully controlled to ensure uniform coverage and compatibility with surrounding components.
- Layer Stacking: If the PCB design involves multiple layers, the individual layers are stacked together and laminated using heat and pressure to form a single integrated structure. This process bonds the layers together and ensures electrical connectivity between them.
- Copper Plating: Copper plating is applied to the surface of the PCB to create conductive traces and pads according to the circuit design. The plating process involves electroplating copper onto the substrate followed by etching to define the desired trace patterns.
- Surface Finishing:Surface finishing techniques such as solder mask application and surface plating are performed to protect the copper traces, enhance solderability, and improve the overall reliability of the PCB. Options for surface finishes include HASL (Hot Air Solder Leveling), ENIG (Electroless Nickel Immersion Gold), and OSP (Organic Solderability Preservatives).
- Quality Control and Testing: Throughout the fabrication process, rigorous quality control measures are implemented to ensure the accuracy, reliability, and performance of the finished PCBs. Testing procedures may include electrical continuity testing, thermal profiling, and dimensional inspection to verify compliance with design specifications.
By following these specialized fabrication steps, manufacturers can produce Advanced Cavity PCBs with superior thermal management, EMI shielding, and mechanical stability, meeting the demanding requirements of modern electronic systems.
How do you manufacture an Advanced Cavity PCB?
Manufacturing an Advanced Cavity PCB involves a series of specialized processes to create the cavities and integrate thermal management and EMI shielding features. Here’s a step-by-step overview of the manufacturing process:
- Design Preparation: Engineers begin by preparing the PCB design using CAD (Computer-Aided Design) software. They determine the layout of components, routing of traces, and placement of cavities based on the specific requirements of the application.
- Material Selection: Choose PCB materials with high thermal conductivity and appropriate dielectric properties to meet the thermal management and performance criteria. Specialized laminates with embedded heat spreaders or conductive fillers may be selected for enhanced thermal performance.
- Cavity Creation: Utilize advanced machining techniques such as controlled-depth milling or laser drilling to create cavities in the PCB substrate. CNC (Computer Numerical Control) machines are employed to precisely mill or drill the cavities according to the design specifications.
- Cavity Filling:Once the cavities are created, they are filled with thermal interface materials (TIMs), encapsulants, or other cavity fill materials to improve thermal conductivity, mechanical stability, and EMI shielding. The filling process must be carefully controlled to ensure uniform coverage and compatibility with surrounding components.
- Layer Stacking: If the PCB design involves multiple layers, the individual layers are stacked together and laminated using heat and pressure to form a single integrated structure. This process bonds the layers together and ensures electrical connectivity between them.
- Copper Plating: Apply copper plating to the surface of the PCB to create conductive traces and pads according to the circuit design. The plating process involves electroplating copper onto the substrate followed by etching to define the desired trace patterns.
- Surface Finishing: Apply surface finishes such as solder mask and surface plating to protect the copper traces, enhance solderability, and improve overall reliability. Surface finish options include HASL (Hot Air Solder Leveling), ENIG (Electroless Nickel Immersion Gold), and OSP (Organic Solderability Preservatives).
- Quality Control and Testing: Implement rigorous quality control measures throughout the manufacturing process to ensure the accuracy, reliability, and performance of the finished PCBs. Testing procedures may include electrical continuity testing, thermal profiling, and dimensional inspection to verify compliance with design specifications.
By following these specialized manufacturing steps, manufacturers can produce Advanced Cavity PCBs with superior thermal management, EMI shielding, and mechanical stability, meeting the demanding requirements of modern electronic systems.
How much should an Advanced Cavity PCB cost?
The cost of an Advanced Cavity PCB can vary widely depending on several factors such as the complexity of the design, the number of layers, the materials used, the size of the board, and the quantity ordered. Generally, Advanced Cavity PCBs tend to be more expensive than standard PCBs due to the additional processes involved in creating cavities, integrating thermal management features, and implementing EMI shielding.
As a rough estimate, the cost of an Advanced Cavity PCB can range from tens to hundreds or even thousands of dollars per unit. A simple single-layer Advanced Cavity PCB with basic thermal management features may cost less compared to a complex multi-layer board with intricate cavity designs and advanced materials.
To get an accurate cost estimate for an Advanced Cavity PCB, it’s essential to consult with PCB manufacturers or suppliers who can provide quotes based on your specific requirements and design specifications. They can take into account factors such as material costs, manufacturing complexity, and volume discounts to provide a detailed cost breakdown for your project.
What is the Advanced Cavity PCB base material?
The choice of base material for Advanced Cavity PCBs depends on the specific requirements of the application, particularly in terms of thermal management, mechanical stability, and electrical performance. Some commonly used base materials for Advanced Cavity PCBs include:
- High Thermal Conductivity Laminates: These laminates are specifically designed to dissipate heat efficiently from components to the board’s exterior. They typically feature high thermal conductivity materials such as aluminum or copper filled resins, allowing for effective heat spreading and dissipation.
- Metal Core PCBs (MCPCBs): MCPCBs feature a metal core (usually aluminum or copper) that provides excellent thermal conductivity and mechanical stability. The metal core acts as a heat sink, absorbing and dissipating heat generated by components mounted on the PCB.
- Ceramic-based Substrates: Ceramic substrates offer exceptional thermal properties, high mechanical strength, and excellent electrical insulation. They are suitable for applications requiring superior thermal management and reliability, such as high-power electronics and RF/microwave systems.
- Thermally Conductive Dielectric Materials: Some Advanced Cavity PCBs use thermally conductive dielectric materials with enhanced thermal conductivity properties to improve heat dissipation while maintaining electrical insulation. These materials may include filled epoxies, polyimides, or specialized thermoplastics.
- Metal-backed PCBs: Metal-backed PCBs feature a metal layer bonded to the substrate, providing enhanced thermal conductivity and mechanical stability. These PCBs are commonly used in applications where heat dissipation is critical, such as LED lighting, power electronics, and automotive systems.
The choice of base material depends on various factors such as thermal requirements, mechanical constraints, signal integrity considerations, and cost considerations. Engineers and designers select the most suitable base material based on the specific needs of the application to ensure optimal performance and reliability of the Advanced Cavity PCB.
Which company makes Advanced Cavity PCB?
Currently, many companies manufacture Advanced Cavity PCBs, with some leading manufacturers including internationally renowned PCB manufacturers such as Foxconn, Thomson, Hitachi Chemical, Epson, and others. Additionally, there are specialized manufacturers and suppliers focused on high-performance PCBs, such as Rogers Corporation in the United States, Hitachi Chemical in Japan, and Ventec International Group in Italy.
As for our company, we are a professional PCB manufacturer with advanced production equipment and a skilled technical team capable of producing various types of PCBs, including Advanced Cavity PCBs. We have extensive experience and expertise in PCB manufacturing and can meet the personalized needs of our customers.
Our company has the following advantages and characteristics that enable us to produce high-quality Advanced Cavity PCBs:
- Advanced equipment and technology: We have advanced PCB production equipment and technology, including high-precision CNC milling machines, laser drilling machines, multi-layer lamination presses, etc., capable of realizing complex cavity designs and precise processing.
- Years of experience and expertise:Our team has many years of PCB manufacturing experience and professional knowledge, with rich experience and skills in the design, processing, and quality control of Advanced Cavity PCBs.
- Customized services: We provide personalized customized services, allowing us to tailor various types and specifications of Advanced Cavity PCBs according to the needs of our customers, including material selection, layer stacking design, cavity design, etc.
- Strict quality control: We adhere to international standards and quality management systems, ensuring that each batch of Advanced Cavity PCBs undergoes rigorous quality inspection and testing to meet the requirements and standards of our customers.
In summary, our company has advanced equipment, extensive experience, and professional knowledge to provide high-quality Advanced Cavity PCBs to our customers, along with personalized customized services to meet various needs and requirements.
What are the 7 qualities of good customer service?
Good customer service is essential for building strong relationships with customers and ensuring their satisfaction. Here are seven qualities that contribute to excellent customer service:
- Responsiveness: Being responsive means promptly addressing customer inquiries, concerns, or issues. Responding in a timely manner shows customers that their needs are valued and helps build trust and loyalty.
- Empathy: Empathy involves understanding and acknowledging the customer’s feelings, concerns, and perspectives. Showing empathy demonstrates that you care about the customer’s experience and are committed to helping them find a solution to their problem.
- Clarity: Providing clear and concise communication is crucial for effective customer service. Clear communication helps prevent misunderstandings and ensures that customers have a clear understanding of the information or instructions provided.
- Professionalism: Maintaining professionalism in interactions with customers conveys competence, reliability, and respect. Professionalism includes being polite, courteous, and maintaining a positive attitude, even in challenging situations.
- Flexibility: Being flexible means adapting to the unique needs and preferences of each customer. Flexibility may involve offering customized solutions, accommodating special requests, or being willing to make exceptions when appropriate.
- Problem-solving skills: Good customer service representatives possess strong problem-solving skills to effectively address customer issues and find satisfactory solutions. They are resourceful, creative, and persistent in resolving problems to the customer’s satisfaction.
- Follow-up: Following up with customers after resolving their issues or completing a transaction shows that you value their feedback and are committed to their satisfaction. Follow-up may involve checking in to ensure that the issue has been resolved to their satisfaction or seeking feedback on their experience.
By embodying these qualities, businesses can provide exceptional customer service that fosters positive relationships, builds loyalty, and enhances the overall customer experience.
FAQs
What are the benefits of using Advanced Cavity PCBs?
Advanced Cavity PCBs offer several benefits, including improved thermal management, enhanced EMI shielding, reduced signal interference, and increased mechanical stability. They are ideal for applications requiring high-power components or sensitive electronics.
How are cavities created in Advanced Cavity PCBs?
Cavities in Advanced Cavity PCBs are created using specialized machining techniques such as controlled-depth milling or laser drilling. CNC (Computer Numerical Control) machines are used to mill or drill the cavities with high precision according to the design specifications.
What materials are used in Advanced Cavity PCBs?
Advanced Cavity PCBs can be constructed using a variety of materials depending on the specific requirements of the application. Common materials include high thermal conductivity laminates, metal-core PCBs, ceramic-based substrates, and thermally conductive dielectric materials.
What applications are Advanced Cavity PCBs suitable for?
Advanced Cavity PCBs are suitable for a wide range of applications, including aerospace, automotive, telecommunications, power electronics, LED lighting, and RF/microwave systems. They are particularly beneficial in high-power and high-frequency electronic systems where thermal management and EMI shielding are critical.
How do Advanced Cavity PCBs compare to standard PCBs?
Advanced Cavity PCBs offer several advantages over standard PCBs, including improved thermal performance, enhanced EMI shielding, and increased mechanical stability. However, they may also be more complex to design and manufacture, resulting in higher costs.
Can Advanced Cavity PCBs be customized?
Yes, Advanced Cavity PCBs can be customized to meet the specific requirements of the application. Customization options include cavity design, material selection, layer stacking, and thermal management features. Working with an experienced PCB manufacturer can help ensure that the PCB meets the desired specifications.
These FAQs provide a basic understanding of Advanced Cavity PCBs and their