High Frequency Cavity PCB Manufacturer
High Frequency Cavity PCB Manufacturer,High Frequency Cavity PCBs are engineered to excel in applications that require precise signal transmission at elevated frequencies. These circuit boards feature specially designed cavities or recesses to minimize signal path lengths and enhance electrical performance. The cavity structure helps reduce signal loss, electromagnetic interference, and parasitic effects, making them ideal for high-speed communications, RF, and microwave applications. Constructed from high-quality materials with low dielectric loss, High Frequency Cavity PCBs offer superior thermal management and reliability. Their advanced design supports high-density component placement and ensures optimal performance in demanding electronic environments.
What is a High Frequency Cavity PCB?
A High Frequency Cavity PCB (Printed Circuit Board) is a specialized type of PCB designed for high-frequency applications, such as those found in radio frequency (RF) and microwave technologies. These PCBs are engineered to handle signals in the gigahertz (GHz) range with minimal signal loss and interference, making them crucial for applications in telecommunications, satellite communications, radar systems, and advanced electronics.
The key feature of a High Frequency Cavity PCB is the incorporation of a cavity structure within the board. This cavity can be used to house components or create specific electromagnetic environments to improve signal integrity. The design often involves the use of low-loss, high-dielectric materials, such as PTFE (Polytetrafluoroethylene) or ceramic substrates, to minimize signal attenuation and distortion.
These PCBs are also characterized by their precise fabrication techniques, which include careful control of layer thicknesses and spacing to maintain consistent impedance and reduce signal reflections. High Frequency Cavity PCBs may have multiple layers with complex interconnections and shielding to manage high-frequency signal propagation and reduce electromagnetic interference (EMI).
Overall, High Frequency Cavity PCBs are essential for high-performance electronic systems where signal integrity and minimal loss are critical. Their advanced design and materials help ensure reliable operation in demanding environments.
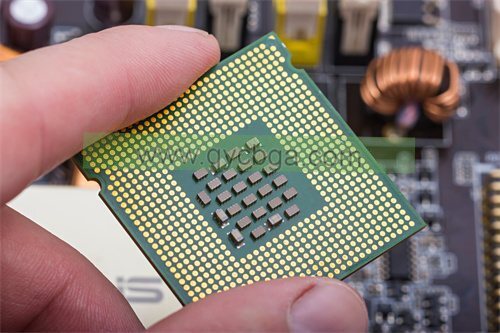
High Frequency Cavity PCB Manufacturer
What are the High Frequency Cavity PCB Design Guidelines?
Designing High Frequency Cavity PCBs requires adherence to specific guidelines to ensure optimal performance and signal integrity. Here are some key design guidelines:
- Material Selection: Use low-loss, high-dielectric constant materials such as PTFE (Teflon) or ceramics. These materials help minimize signal attenuation and maintain consistent impedance.
- Impedance Control: Maintain precise impedance control throughout the PCB. This involves careful design of trace widths and spacing, as well as using appropriate dielectric materials to match the impedance of the transmission lines.
- Layer Stack-Up: Design the layer stack-up to include appropriate ground planes and signal layers. Ensure that the dielectric thickness between layers is consistent to avoid impedance variations.
- Cavity Design: If incorporating cavities, ensure they are designed to avoid resonance issues that can interfere with signal integrity. Cavity dimensions should be optimized to support the desired frequency range.
- Signal Integrity: Use high-frequency simulation tools to analyze signal integrity and predict potential issues such as signal loss, crosstalk, and reflections. Implement appropriate measures like controlled impedance traces and proper termination techniques.
- Shielding and Grounding: Implement effective shielding and grounding practices to reduce electromagnetic interference (EMI). Use ground planes and shielding layers to isolate high-frequency signals and reduce noise.
- Via Design: Minimize the use of vias or use high-frequency via designs to reduce signal degradation. When vias are necessary, ensure they are properly designed to handle high-frequency signals with minimal inductance.
- Component Placement: Place high-frequency components strategically to minimize trace lengths and avoid sharp bends in high-frequency traces. Ensure that components are positioned to support the signal flow and maintain impedance continuity.
- Thermal Management: High-frequency PCBs can generate heat, so incorporate thermal management techniques such as heat sinks or thermal vias to dissipate heat and maintain reliable operation.
- Testing and Validation:Perform thorough testing and validation of the PCB design using high-frequency test equipment to ensure that the design meets performance specifications and functions as intended in the operational environment.
Following these guidelines helps ensure that High Frequency Cavity PCBs deliver high performance and reliability in demanding applications.
What is the High Frequency Cavity PCB Fabrication Process?
The fabrication process for High Frequency Cavity PCBs involves several specialized steps to ensure that the board meets the required performance standards for high-frequency applications. Here’s an overview of the typical fabrication process:
- Material Selection:Choose high-frequency laminate materials such as PTFE (Teflon) or ceramics, which have low dielectric loss and high dielectric constant properties.
- Material Preparation: Prepare the base laminate by cutting it to the desired size and thickness. Ensure the surface is clean and free from contaminants.
- Cavity Formation: If the design includes cavities, use techniques such as machining or etching to create the cavity structures within the laminate. This step requires precision to ensure that the cavities are of the correct dimensions and do not introduce unwanted resonances.
- Layer Deposition: Deposit copper layers onto the laminate using processes like electroplating or sputtering. These copper layers will form the conductive traces and planes on the PCB.
- Photoresist Application: Apply a photoresist layer to the copper surface. This light-sensitive material will be used to define the circuit patterns.
- Pattern Transfer: Use photolithography to transfer the circuit design onto the photoresist layer. Expose the photoresist to UV light through a mask that contains the circuit pattern. The exposed areas of the photoresist will harden, while the unexposed areas remain soluble.
- Etching: Remove the unexposed photoresist and etch away the unwanted copper to reveal the circuit pattern. This process creates the necessary conductive traces and pads on the PCB.
- Drilling: Drill holes for vias and component leads using precision drilling machines. High-frequency PCBs often require special techniques to minimize signal degradation through vias.
- Plating and Metallization: Plate the drilled holes with copper to ensure electrical connections between different layers of the PCB. This step is critical for maintaining signal integrity through vias.
- Cavity Filling (if needed): Fill cavities with materials such as dielectric fillers or additional layers to ensure structural integrity and performance consistency.
- Lamination: Laminate the various layers of the PCB together under heat and pressure. This step involves aligning the layers precisely to maintain consistent impedance and signal integrity.
- Surface Finish: Apply a surface finish such as HASL (Hot Air Solder Leveling), ENIG (Electroless Nickel Immersion Gold), or others to protect the copper traces and prepare the PCB for soldering components.
- Testing and Inspection: Conduct rigorous testing and inspection of the PCB to check for defects, verify impedance control, and ensure that the board meets performance specifications. This may include high-frequency testing, visual inspection, and electrical testing.
- Cutting and Routing:Cut the PCB to its final shape and route any additional features or slots as required by the design.
- Final Assembly: Prepare the PCB for assembly by cleaning it and applying solder mask and silkscreen layers if necessary. The PCB is now ready for component placement and soldering.
This fabrication process ensures that High Frequency Cavity PCBs are produced with the precision and quality necessary for high-performance applications.
How do you manufacture a High Frequency Cavity PCB?
Manufacturing a High Frequency Cavity PCB involves several specialized processes tailored to ensure optimal performance for high-frequency applications. Here’s a step-by-step overview of the manufacturing process:
- Design and Specification: Begin with detailed design specifications for the PCB, including high-frequency requirements, cavity dimensions, material selection, and layer stack-up. This design phase often uses specialized software for high-frequency simulation and layout.
- Material Selection: Choose appropriate high-frequency laminate materials, such as PTFE (Teflon) or ceramic-based substrates, that offer low dielectric loss and high dielectric constant properties. These materials are crucial for minimizing signal attenuation and maintaining consistent impedance.
- Material Preparation: Cut the laminate to the required size and thickness. The surface of the laminate is then cleaned to ensure good adhesion of subsequent layers.
- Cavity Formation: Create cavities in the laminate using precision machining techniques. This can involve drilling, routing, or laser cutting to form cavities that accommodate components or modify electromagnetic properties. The dimensions and positioning of the cavities must be precisely controlled to avoid resonances and maintain performance.
- Copper Deposition: Deposit copper layers onto the laminate using methods such as electroplating or sputtering. These layers will form the conductive traces, planes, and pads on the PCB.
- Photoresist Application: Apply a photoresist layer to the copper surface. This light-sensitive material will be used to create the circuit pattern.
- Pattern Transfer: Use photolithography to transfer the circuit design onto the photoresist layer. Expose the photoresist to UV light through a mask that contains the circuit pattern. The exposed areas of the photoresist will harden, while the unexposed areas will remain soluble.
- Etching: Remove the unexposed photoresist and etch away the excess copper to reveal the circuit pattern. This process creates the conductive traces and pads necessary for the PCB.
- Drilling and Via Formation: Drill holes for vias and component leads with precision drilling equipment. For high-frequency applications, special care is taken to reduce signal degradation through vias.
- Plating and Metallization: Plate the drilled holes with copper to create electrical connections between different layers of the PCB. This step is crucial for ensuring signal integrity through vias.
- Cavity Filling (if applicable): If the design requires, fill the cavities with dielectric materials or additional layers to maintain structural integrity and performance consistency.
- Lamination: Laminate the layers together under heat and pressure. This step involves aligning the layers precisely to maintain consistent impedance and signal integrity.
- Surface Finish: Apply a protective surface finish such as HASL (Hot Air Solder Leveling), ENIG (Electroless Nickel Immersion Gold), or others. This finish protects the copper traces and prepares the PCB for soldering components.
- Testing and Inspection: Perform rigorous testing and inspection of the PCB. This includes high-frequency testing, visual inspection, and electrical testing to ensure that the PCB meets performance specifications and is free from defects.
- Cutting and Routing: Cut the PCB to its final shape and route any additional features or slots as required by the design.
- Final Assembly: Prepare the PCB for assembly by cleaning it and applying solder mask and silkscreen layers if needed. The PCB is now ready for component placement and soldering.
This manufacturing process ensures that High Frequency Cavity PCBs are produced with the precision, quality, and performance required for high-frequency and demanding applications.
How much should a High Frequency Cavity PCB cost?
The cost of a High Frequency Cavity PCB can vary widely depending on several factors, including the complexity of the design, the materials used, the size of the board, and the quantity ordered. Here are some key factors that influence the cost:
- Material Costs: High-frequency PCBs typically use specialized materials like PTFE (Teflon) or ceramics, which are more expensive than standard FR4 materials. The cost of these materials can significantly impact the overall price.
- Design Complexity: More complex designs, such as those with intricate cavity structures or multiple layers, will increase the manufacturing cost. High-frequency PCBs often require precise impedance control and specialized features, which can add to the cost.
- Cavity Formation: The process of creating cavities, whether through machining, laser cutting, or other methods, adds to the manufacturing cost. The precision required for cavity formation also affects the price.
- Quantity Ordered: The cost per unit typically decreases with larger order quantities due to economies of scale. However, smaller runs or prototypes will generally cost more per unit.
- Layer Count: PCBs with more layers are more expensive to manufacture. High-frequency PCBs with multiple layers and complex interconnections can be significantly costlier.
- Testing and Quality Assurance: Comprehensive testing and quality assurance processes, including high-frequency performance testing, can add to the overall cost.
- Surface Finish: The choice of surface finish (e.g., ENIG, HASL, etc.) can affect the cost. High-frequency applications may require more expensive finishes to ensure signal integrity.
- Lead Time: Expedited manufacturing processes or rush orders may incur additional costs.
Overall, the cost of a High Frequency Cavity PCB is influenced by the interplay of these factors, and getting a precise quote from a PCB manufacturer based on your specific design and requirements is essential for accurate budgeting.
What is High Frequency Cavity PCB Base Material?
The base material of a High Frequency Cavity PCB is crucial for ensuring that the board performs optimally at high frequencies. The choice of base material affects signal integrity, dielectric losses, and overall PCB performance. Here are the primary base materials used:
- PTFE (Polytetrafluoroethylene): Commonly known as Teflon, PTFE is a high-performance dielectric material with very low dielectric loss and excellent electrical insulation properties. It is ideal for high-frequency applications due to its stable dielectric constant and low signal attenuation.
- Ceramic Substrates: Ceramic materials, such as alumina (Al2O3) or barium titanate (BaTiO3), are used for high-frequency PCBs where a high dielectric constant and low loss tangent are required. Ceramic substrates are typically used in applications where high thermal conductivity and low signal loss are critical.
- Liquid Crystal Polymer (LCP):LCP is a high-frequency material with low dielectric loss and excellent dimensional stability. It is used in applications requiring high-frequency performance and reliability in harsh environments.
- High-Density Interconnect (HDI) Materials: For complex designs with fine features and high-frequency requirements, HDI materials may be used. These materials are designed to support high-density interconnections and offer low dielectric loss and controlled impedance.
- Epoxy-Glass Laminates: While not as specialized as PTFE or ceramics, some high-frequency PCBs use advanced epoxy-glass laminates with specially formulated resins to offer improved dielectric properties compared to standard FR-4 materials. These materials are often used in moderately high-frequency applications.
- Aluminum-based Laminates: In some cases, aluminum-based laminates are used for high-frequency applications due to their excellent thermal management properties. These laminates typically have a copper layer on an aluminum base and are used where thermal dissipation is a key concern.
Choosing the right base material is essential for achieving optimal performance in high-frequency applications and ensuring the reliability and efficiency of the PCB.
Which company makes High Frequency Cavity PCBs?
In the field of high-frequency applications, several companies specialize in producing High Frequency Cavity PCBs (Printed Circuit Boards) and offer specialized design and manufacturing services for these complex circuit boards. Here are some well-known companies in this field:
- Rogers Corporation: Rogers is a global leader in high-frequency materials and specializes in manufacturing high-frequency PCBs. Their high-performance PCB materials, such as the RO4000 and RO3000 series, are widely used in high-frequency, high-speed, and RF applications.
- Arlon Electronic Materials: Arlon offers a range of high-frequency materials, particularly for high-frequency and high-power applications. Their products include high-performance PTFE and ceramic substrates.
- Isola Group: Isola is a well-known PCB material supplier that provides high-performance materials for high-frequency PCBs, including the FR408HR and other high-frequency materials.
- Taconic: Taconic supplies various high-frequency PCB materials, including PTFE and ceramic substrates. Their products are used in wireless communication, radar, and other high-frequency applications.
- Shenzhen Kinwong Electronic Co., Ltd.: Kinwong is a prominent company in the PCB industry, offering a range of PCB manufacturing services, including high-frequency cavity PCBs.
- MCL (Microwave Circuits Ltd.): MCL focuses on microwave and high-frequency circuit board manufacturing, providing high-performance high-frequency cavity PCB solutions.
Our company also manufactures High Frequency Cavity PCBs. We have advanced manufacturing equipment and a professional technical team capable of producing circuit boards that meet high-frequency application requirements. The advantages of our high-frequency cavity PCBs include:
- High-Frequency Material Selection: We use materials such as PTFE, ceramics, and other high-performance substrates to ensure signal integrity and low loss characteristics in high-frequency applications.
- Precision Cavity Processing: Our manufacturing capabilities include precise cavity formation techniques, whether through machining or laser cutting, to ensure accuracy and consistency of cavity dimensions.
- Advanced Production Processes: We employ advanced production processes, including photolithography, etching, drilling, and plating, to ensure high quality and performance of high-frequency circuit boards.
- Rigorous Testing and Inspection: We conduct thorough testing and inspection throughout the production process to ensure that each high-frequency cavity PCB meets performance requirements for high-frequency applications.
- Custom Solutions: We offer customized high-frequency cavity PCB solutions based on specific customer needs, including different materials, layer counts, and cavity designs.
We are committed to providing high-quality, high-performance high-frequency cavity PCBs, helping our customers achieve excellent performance and reliability in various high-frequency applications.
What are the 7 qualities of good customer service?
Good customer service is essential for building strong customer relationships and ensuring satisfaction. Here are seven key qualities of excellent customer service:
- Empathy: Understanding and sharing the feelings of the customer is crucial. Empathetic service involves listening to the customer’s concerns and showing genuine care for their issues. This helps build a strong emotional connection and demonstrates that the company values its customers.
- Responsiveness: Timely and efficient responses to customer inquiries, complaints, and requests are vital. Good customer service means addressing issues promptly and keeping customers informed throughout the process.
- Knowledgeability: Service representatives should have a deep understanding of the company’s products or services and be able to provide accurate information. Knowledgeable staff can answer questions effectively and resolve issues more efficiently.
- Patience: Handling customers calmly and patiently, even in challenging situations, is essential. Patience helps in resolving issues without frustration and ensures that customers feel heard and valued.
- Professionalism: Maintaining a courteous, respectful, and professional demeanor at all times is important. Professionalism includes using polite language, dressing appropriately, and adhering to company policies and procedures.
- Consistency: Providing a consistent level of service across all interactions and touchpoints ensures reliability. Customers should receive the same high level of service whether they are contacting the company via phone, email, or in person.
- Personalization: Tailoring interactions to meet the individual needs and preferences of customers enhances their experience. Personalization involves addressing customers by name, understanding their history with the company, and offering solutions that fit their specific needs.
These qualities collectively contribute to creating a positive and memorable customer experience, fostering loyalty, and encouraging repeat business.
FAQs
What is a High Frequency Cavity PCB?
A High Frequency Cavity PCB is a type of printed circuit board designed to operate efficiently at high frequencies, such as those used in RF (radio frequency) and microwave applications. It includes cavity structures to enhance performance and reduce signal loss.
What are the benefits of using High Frequency Cavity PCBs?
High Frequency Cavity PCBs offer benefits such as reduced signal attenuation, improved signal integrity, better electromagnetic interference (EMI) shielding, and enhanced performance for high-frequency applications.
What materials are used in High Frequency Cavity PCBs?
Common materials include PTFE (Teflon), ceramic substrates, liquid crystal polymers (LCP), and high-density interconnect (HDI) materials. These materials help minimize dielectric loss and maintain consistent impedance.
What industries use High Frequency Cavity PCBs?
They are used in industries such as telecommunications, satellite communications, radar systems, automotive electronics, and high-speed computing, where high-frequency performance is critical.
How are High Frequency Cavity PCBs manufactured?
The manufacturing process involves selecting high-frequency materials, forming cavities using precision techniques, depositing copper layers, applying photoresist, pattern transferring, etching, drilling, plating, and conducting rigorous testing.
What are common design considerations for High Frequency Cavity PCBs?
Design considerations include material selection, impedance control, cavity dimensions, signal integrity, shielding, grounding, and thermal management.
How do you choose the right material for a High Frequency Cavity PCB?
Choose materials based on the required dielectric properties, frequency range, thermal management needs, and cost considerations. PTFE and ceramic are common choices for high-frequency applications.