High Frequency Antenna PCB Manufacturer
High Frequency Antenna PCB Manufacturer,High Frequency Antenna PCBs are specialized printed circuit boards engineered for the efficient transmission and reception of high-frequency signals in various wireless communication and sensing applications. These PCBs are meticulously designed to meet the demanding requirements of high-frequency systems, incorporating advanced features to optimize antenna performance and signal integrity.
At the core of High Frequency Antenna PCBs lies the selection of high-quality substrate materials with low dielectric constants, such as PTFE-based laminates or specialized FR-4 variants. These materials minimize signal loss and maintain stable electrical properties across a wide frequency range. Precision trace routing and impedance matching techniques are employed to ensure minimal signal distortion and maximum energy transfer.
Furthermore, solid grounding and RF shielding are implemented to minimize electromagnetic interference and enhance signal purity. Component placement is carefully optimized to minimize signal path lengths and maximize antenna efficiency.
In essence, High Frequency Antenna PCBs serve as the backbone of high-performance wireless systems, enabling seamless connectivity and reliable data transmission in applications ranging from telecommunications and IoT devices to radar systems and satellite communication.
What is a High Frequency Antenna PCB?
A High Frequency Antenna PCB refers to a printed circuit board (PCB) designed specifically to accommodate high-frequency signals, typically used in applications like wireless communication, RFID (Radio Frequency Identification), radar systems, and more. These PCBs are engineered with features to optimize the performance of antennas operating at high frequencies.
Here are some key characteristics of High Frequency Antenna PCBs:
- Material Selection: The choice of substrate material is critical for high-frequency PCBs. Materials with low dielectric constants, such as PTFE (Polytetrafluoroethylene) or FR-4 with special additives, are often preferred to minimize signal loss and maintain signal integrity.
- Precise Traces: The traces on the PCB are meticulously designed to match the impedance of the antenna and minimize signal reflections. This requires precise control over trace width, spacing, and impedance matching techniques like microstrip or stripline configurations.
- Grounding: Proper grounding is crucial for high-frequency PCBs to minimize electromagnetic interference (EMI) and ensure signal stability. Ground planes are strategically placed on the PCB to provide a low-impedance path for return currents and reduce radiation losses.
- Component Placement: Components on the PCB are placed carefully to minimize signal distortion and interference. High-frequency components such as amplifiers, filters, and matching networks are positioned to minimize trace lengths and maintain signal integrity.
- RF Shielding: To prevent interference from external sources and maintain signal purity, high-frequency PCBs often incorporate RF shielding techniques. This may include the use of shielded enclosures or dedicated shielding layers within the PCB stackup.
- Testing and Validation: High-frequency PCBs undergo rigorous testing and validation procedures to ensure they meet performance requirements. This may involve impedance testing, signal integrity analysis, and antenna performance testing in simulated or real-world environments.
Overall, High Frequency Antenna PCBs are specialized circuit boards optimized for the efficient transmission and reception of high-frequency signals, crucial for a wide range of wireless communication and sensing applications.
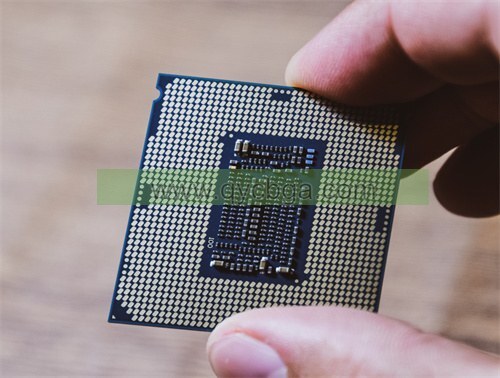
High Frequency Antenna PCB Manufacturer
What are the High Frequency Antenna PCB Design Guidelines?
Designing a high-frequency antenna PCB requires careful consideration of various factors to ensure optimal performance. Here are some key guidelines to follow:
- Frequency Consideration: Understand the frequency range over which the antenna will operate. Different frequencies require different antenna designs and PCB layouts.
- Substrate Selection: Choose a substrate material with low dielectric constant and low loss tangent to minimize signal attenuation. Common materials include PTFE (such as Rogers RO4003) and specialized FR-4 variants.
- Trace Width and Impedance Matching: Design transmission lines (traces) with appropriate widths to match the desired characteristic impedance, typically 50 ohms for RF applications. Use impedance matching techniques (like microstrip or stripline) to ensure signal integrity.
- Grounding: Implement a solid ground plane on one or both sides of the PCB to provide a low-impedance return path for RF signals and minimize electromagnetic interference (EMI).
- Component Placement: Place components, especially high-frequency ones like RF amplifiers and filters, as close to the antenna as possible to minimize trace lengths and signal losses.
- Antenna Placement: Position the antenna on the PCB to optimize radiation patterns and minimize coupling with other components or structures on the board.
- RF Shielding: Incorporate RF shielding techniques, such as grounded metal enclosures or dedicated shielding layers within the PCB stackup, to minimize interference from external sources.
- Via Placement: Minimize the number of vias used in high-frequency signal paths to reduce signal discontinuities and reflections. When vias are necessary, use high-quality, low-loss vias.
- Testing and Validation: Perform thorough testing and validation of the PCB design, including impedance matching verification, signal integrity analysis, and antenna performance testing in simulated or real-world environments.
- Environmental Considerations: Consider the operating environment of the antenna system, including temperature, humidity, and mechanical stress, and design the PCB to withstand these conditions.
By following these guidelines, you can design a high-frequency antenna PCB that meets performance requirements and ensures reliable operation in wireless communication and sensing applications.
What is the High Frequency Antenna PCB Fabrication Process?
The fabrication process for a high-frequency antenna PCB involves several steps to ensure the precise manufacture of the board according to design specifications. Here’s a general outline of the process:
- Design Preparation:The process begins with the preparation of the PCB design files using specialized PCB design software. This includes layout design, trace routing, component placement, and generation of fabrication files such as Gerber files and drill files.
- Material Selection: Choose the appropriate substrate material for the high-frequency antenna PCB. Common materials include PTFE-based laminates like Rogers RO4003 or specialized FR-4 variants with low dielectric constants.
- Prepreg Cutting and Panelization: Prepreg material is cut to the required dimensions and stacked with copper-clad laminate sheets to form a panel. The panelization process involves arranging multiple PCBs on a single panel to optimize fabrication efficiency.
- Copper Cladding and Etching: A layer of copper foil is bonded to both sides of the substrate panel. The copper is then selectively etched away using chemical processes, leaving behind the desired copper traces and pads according to the PCB design.
- Drilling: Precision drilling machines are used to drill holes for through-holes, vias, and component mounting pads according to the PCB design specifications. Laser drilling may be used for high-density interconnect (HDI) PCBs or microvias in high-frequency designs.
- Surface Treatment: Surface treatment processes such as copper surface cleaning, desmear, and metallization are applied to enhance the adhesion of the substrate to the copper layers and improve solderability.
- Solder Mask Application: A solder mask layer is applied over the copper traces and pads to protect them from oxidation and facilitate soldering during assembly. The solder mask is cured using ultraviolet (UV) light and then coated with a protective finish.
- Silkscreen Printing: Component designators, logos, and other markings are printed onto the PCB surface using silkscreen printing techniques. This helps identify components and provides assembly instructions.
- Final Inspection and Testing: The fabricated PCBs undergo visual inspection, dimensional verification, and electrical testing to ensure they meet quality standards and adhere to the design specifications.
- Routing and Separation: Individual PCBs are separated from the panel using routing or scoring techniques. Any remaining rough edges or burrs are removed, and the PCBs are cleaned to remove debris and contaminants.
- Packaging and Shipping: The finished PCBs are packaged according to customer requirements and shipped to the assembly facility for component placement and soldering.
By following these steps carefully, manufacturers can fabricate high-quality high-frequency antenna PCBs that meet the performance requirements of various wireless communication and sensing applications.
How do you manufacture a High Frequency Antenna PCB?
Manufacturing a high-frequency antenna PCB involves a specialized process to ensure the precise fabrication of the board according to design specifications. Here’s a detailed overview of the manufacturing process:
- Preparation of Design Files: The process begins with the preparation of PCB design files using specialized software. These files include layout design, trace routing, component placement, and generation of fabrication files such as Gerber files and drill files.
- Material Selection: Choose the appropriate substrate material for the high-frequency antenna PCB. Common materials include PTFE-based laminates like Rogers RO4003 or specialized FR-4 variants with low dielectric constants. The choice of material depends on factors such as frequency range, signal integrity requirements, and thermal properties.
- Panelization and Material Preparation:Prepreg material is cut to the required dimensions and stacked with copper-clad laminate sheets to form a panel. The panelization process involves arranging multiple PCBs on a single panel to optimize fabrication efficiency.
- Copper Cladding and Etching: A layer of copper foil is bonded to both sides of the substrate panel. The copper is then selectively etched away using chemical processes, leaving behind the desired copper traces and pads according to the PCB design. The etching process is critical for achieving precise trace widths and maintaining signal integrity.
- Drilling: Precision drilling machines are used to drill holes for through-holes, vias, and component mounting pads according to the PCB design specifications. Laser drilling may be used for high-density interconnect (HDI) PCBs or microvias in high-frequency designs. Careful attention is paid to drill accuracy and registration to ensure proper alignment of holes with copper features.
- Surface Treatment: Surface treatment processes such as copper surface cleaning, desmear, and metallization are applied to enhance the adhesion of the substrate to the copper layers and improve solderability. These treatments help prepare the PCB surface for subsequent assembly processes.
- Solder Mask Application: A solder mask layer is applied over the copper traces and pads to protect them from oxidation and facilitate soldering during assembly. The solder mask is typically applied using a screen printing process and cured using ultraviolet (UV) light. Precision is crucial to ensure proper coverage of the copper features while maintaining clearance around pads and vias.
- Silkscreen Printing: Component designators, logos, and other markings are printed onto the PCB surface using silkscreen printing techniques. This helps identify components and provides assembly instructions. Silkscreen printing is performed after solder mask application and curing to ensure durability and legibility of the markings.
- Final Inspection and Testing: The fabricated PCBs undergo thorough inspection and testing to ensure they meet quality standards and adhere to the design specifications. Visual inspection, dimensional verification, and electrical testing may be performed to detect any defects or discrepancies. Any non-conforming PCBs are either reworked or discarded to maintain quality control.
- Routing and Separation: Once the PCBs pass inspection, they are separated from the panel using routing or scoring techniques. Any remaining rough edges or burrs are removed, and the PCBs are cleaned to remove debris and contaminants. The separated PCBs are then packaged according to customer requirements and shipped to the assembly facility for component placement and soldering.
By following these steps meticulously, manufacturers can produce high-quality high-frequency antenna PCBs that meet the stringent performance requirements of various wireless communication and sensing applications.
How much should a High Frequency Antenna PCB cost?
The cost of a high-frequency antenna PCB can vary widely depending on several factors, including the complexity of the design, the choice of materials, the manufacturing processes involved, the quantity ordered, and the supplier/vendor. However, here’s a rough estimate to give you an idea:
- Design Complexity: The complexity of the PCB design, including the number of layers, the density of components, the intricacy of the routing, and the sophistication of the features (such as impedance matching structures), can significantly influence the cost. More complex designs typically require more time and resources to manufacture, leading to higher costs.
- Material Selection: The choice of substrate material can have a significant impact on the cost of the PCB. High-performance materials like PTFE-based laminates (e.g., Rogers RO4003) tend to be more expensive than standard FR-4 materials due to their superior electrical properties and performance characteristics.
- Manufacturing Processes: Specialized manufacturing processes, such as laser drilling for microvias or impedance-controlled etching for high-frequency traces, can add to the overall cost of production. These processes require advanced equipment and expertise, which may result in higher fabrication costs.
- Quantity Ordered: Economies of scale often apply in PCB manufacturing, meaning that larger quantities typically result in lower per-unit costs. Ordering higher volumes of high-frequency antenna PCBs can help reduce the cost per unit through bulk discounts and optimized production efficiencies.
- Supplier/Vendor Pricing: The pricing policies of PCB suppliers or manufacturers can vary, so it’s essential to obtain quotes from multiple vendors to compare prices. Factors such as location, reputation, lead times, and additional services (e.g., assembly, testing) can also influence the overall cost.
As a rough estimate, the cost of a high-frequency antenna PCB can range from tens to hundreds of dollars per unit for small to medium quantities, with costs decreasing as the volume increases. For a precise cost estimate, it’s recommended to consult with PCB suppliers or manufacturers and provide them with detailed specifications of your design and requirements. They can provide tailored quotes based on your specific needs and volume expectations.
What is the High Frequency Antenna PCB Base Material?
The base material for high-frequency antenna PCBs plays a crucial role in determining the performance, reliability, and cost of the PCB. Here are some common base materials used for high-frequency antenna PCBs:
- PTFE-Based Laminates: Polytetrafluoroethylene (PTFE) based laminates, such as those offered by Rogers Corporation (e.g., Rogers RO4003), are popular choices for high-frequency applications. PTFE has a low dielectric constant (εr) and low dissipation factor (Df), which helps minimize signal loss and maintain signal integrity at high frequencies. These laminates offer excellent electrical properties, thermal stability, and dimensional stability, making them suitable for demanding RF and microwave applications.
- Hybrid Laminates: Hybrid laminates combine PTFE with other materials, such as woven glass or ceramic fillers, to achieve specific performance characteristics. For example, PTFE-based laminates with woven glass reinforcement offer improved mechanical strength and dimensional stability compared to pure PTFE laminates. Ceramic-filled PTFE laminates may offer enhanced thermal conductivity for applications requiring efficient heat dissipation.
- Specialized FR-4 Variants: While FR-4 is a standard substrate material used in PCB manufacturing, specialized variants with low-loss characteristics are available for high-frequency applications. These materials typically incorporate additives or modifications to reduce dielectric loss and maintain signal integrity at higher frequencies. Examples include FR-4 materials with low-loss epoxy resin systems or reduced glass content.
- Ceramic Substrates: Ceramic substrates, such as alumina (Al2O3) or aluminum nitride (AlN), offer excellent thermal conductivity and stability over a wide temperature range. These materials are suitable for high-power and high-frequency applications where efficient heat dissipation is critical. However, ceramic substrates may be more expensive and less flexible than organic substrates like PTFE or FR-4.
- Metal Core PCBs: Metal core PCBs (MCPCBs) feature a metal core, typically aluminum or copper, sandwiched between layers of dielectric material. The metal core provides excellent thermal conductivity and heat dissipation, making MCPCBs well-suited for high-power and high-frequency applications. However, the choice of dielectric material for the PCB layers will influence the electrical performance and cost.
When selecting the base material for a high-frequency antenna PCB, it’s essential to consider factors such as dielectric constant, dissipation factor, thermal properties, mechanical strength, cost, and manufacturability. Conducting thorough material characterization and testing can help ensure the chosen substrate meets the performance requirements of the antenna system.
Which company makes High Frequency Antenna PCBs?
Many companies produce high-frequency antenna PCBs, with major suppliers including Rogers Corporation, Taconic Advanced Dielectric Division, Isola Group, and others. These companies offer various high-performance substrate materials such as PTFE-based composites, low dielectric constant FR-4 variants, and ceramic substrates to meet the needs of various high-frequency applications.
For our company, we can also manufacture high-frequency antenna PCBs. Our manufacturing capabilities and strengths enable us to meet the demand for high-frequency antenna PCBs. Here are some advantages and capabilities that we can provide:
- Professional Team:We have an experienced engineering team and technical personnel with expertise in designing and manufacturing high-frequency PCBs. They can understand customer requirements and provide customized solutions based on specific needs.
- Advanced Equipment: We are equipped with advanced PCB manufacturing equipment and processes, including precision drilling machines, line drawing machines, chemical etching equipment, and more. These machines ensure precise manufacturing and consistency of high-frequency PCBs.
- High-Quality Materials: We select high-quality substrate materials such as PTFE-based composites or low dielectric constant FR-4 variants to ensure excellent electrical performance and signal integrity for high-frequency PCBs.
- Quality Control:We implement stringent quality control processes, monitoring and inspecting every stage from material procurement to production. We are committed to delivering high-quality products to ensure stable and reliable performance.
- Customer Service: We prioritize communication and collaboration with customers, understanding their needs, and providing customized solutions. Our customer service team is dedicated to providing support and assistance to ensure smooth project execution and customer satisfaction.
In summary, our company possesses the expertise, advanced equipment, high-quality materials, and strict quality control processes required for designing and manufacturing high-frequency antenna PCBs. We are committed to providing customized solutions and ensuring high performance and reliability of our products.
What are the 7 qualities of good customer service?
Good customer service is characterized by several key qualities that contribute to a positive customer experience and foster long-term relationships. Here are seven qualities often associated with good customer service:
- Responsiveness: Good customer service involves promptly addressing customer inquiries, concerns, and requests. Whether it’s answering phone calls, responding to emails, or assisting customers in person, being responsive shows that you value their time and are committed to helping them.
- Empathy: Empathy involves understanding and sharing the feelings of others, including customers. Good customer service representatives demonstrate empathy by actively listening to customers, acknowledging their concerns, and showing genuine concern for their needs and emotions.
- Clear Communication: Effective communication is essential for good customer service. This includes conveying information clearly and concisely, using language that is easy for customers to understand, and avoiding jargon or technical terms that may confuse them. Clear communication helps to ensure that customers receive accurate information and know what to expect.
- Problem-Solving Skills: Good customer service often involves resolving customer issues and addressing their problems effectively. This requires strong problem-solving skills, the ability to think creatively, and a willingness to explore different solutions to meet the customer’s needs. Customer service representatives who can effectively solve problems demonstrate their commitment to customer satisfaction.
- Professionalism: Professionalism encompasses a range of qualities, including politeness, respectfulness, and reliability. Good customer service representatives maintain a professional demeanor at all times, regardless of the situation, and treat customers with courtesy and respect. Professionalism helps to build trust and credibility with customers and enhances their overall experience.
- Knowledgeability: Customers expect customer service representatives to be knowledgeable about the products or services they are providing support for. Good customer service involves having a deep understanding of the company’s offerings, policies, and procedures, as well as the ability to answer customer questions accurately and confidently. Knowledgeable representatives can provide valuable guidance and assistance to customers, helping to build trust and loyalty.
- Follow-Up: Good customer service doesn’t end after the initial interaction. Following up with customers after their inquiries or issues have been resolved shows that you care about their satisfaction and are committed to ensuring a positive experience. Follow-up can involve sending thank-you emails, checking in to ensure that the customer’s needs have been met, or seeking feedback to identify areas for improvement.
By embodying these qualities, organizations can deliver exceptional customer service that not only meets but exceeds customer expectations, leading to increased satisfaction, loyalty, and advocacy.
FAQs (Frequently Asked Questions)
What is a High Frequency Antenna PCB?
A High Frequency Antenna PCB is a printed circuit board designed specifically for high-frequency applications, typically used in wireless communication, radar systems, RFID, and other RF devices. It incorporates specialized features to optimize antenna performance and signal integrity at high frequencies.
What are the key features of High Frequency Antenna PCBs?
Key features of High Frequency Antenna PCBs include precise trace routing, impedance matching structures, solid grounding, low-loss substrate materials (such as PTFE-based laminates), and RF shielding to minimize interference and maintain signal integrity.
What materials are commonly used in High Frequency Antenna PCBs?
Common materials used in High Frequency Antenna PCBs include PTFE-based laminates (e.g., Rogers RO4003), specialized FR-4 variants with low dielectric constants, and ceramic substrates. These materials offer excellent electrical properties and performance characteristics required for high-frequency applications.
How are High Frequency Antenna PCBs different from standard PCBs?
High Frequency Antenna PCBs are designed and manufactured to meet the specific requirements of high-frequency applications, which demand superior signal integrity, low loss, and precise impedance matching. They incorporate specialized features and materials optimized for RF performance, unlike standard PCBs used in low-frequency applications.
What factors should be considered when designing High Frequency Antenna PCBs?
Important factors to consider when designing High Frequency Antenna PCBs include frequency range, substrate material selection, trace routing for impedance matching, grounding techniques, RF shielding, component placement, and environmental considerations such as temperature and humidity.
How can I ensure the quality of High Frequency Antenna PCBs?
Ensuring the quality of High Frequency Antenna PCBs involves rigorous design validation, material selection, manufacturing processes, and testing. It’s essential to work with experienced PCB manufacturers with expertise in high-frequency applications and adhere to industry standards and best practices.
What are some common applications of High Frequency Antenna PCBs?
High Frequency Antenna PCBs are used in a wide range of applications, including wireless communication systems (such as 5G, Wi-Fi, and cellular networks), radar systems, satellite communication, RF sensors, RFID tags, and aerospace and defense electronics. They play a critical role in enabling wireless connectivity and data transmission in various industries.