Wire Bonding BGA Substrates Manufacturer
Wire Bonding BGA Substrates Manufacturer,Wire Bonding BGA (Réseau de billes) substrates are a type of packaging technology used in semiconductor devices. In this method, semiconductor dies are mounted onto a substrate, typically made of ceramic or organic laminate, using die attach materials such as epoxy or solder. The substrate contains a grid array of metal pads or bumps, onto which thin wires (usually made of gold or aluminum) are bonded to establish electrical connections between the die and the substrate. This wire bonding process provides the necessary electrical pathways for the integrated circuit to communicate with external components. WBGA substrates offer advantages such as high-density interconnections, compact form factor, and flexibility in routing connections, making them suitable for applications requiring complex designs with a large number of input-output connections. De plus, the wire bonding technique allows for precise alignment and reliable connections, contributing to the overall reliability and performance of semiconductor devices.
What is a WBGA substrate?
A WBGA substrate, or Wire Bonded Grid Array substrate, is a type of packaging technology used in integrated circuits (Ics) or microchips. It’s a method to connect the semiconductor die to the package’s leads or pins.
In a WBGA package, the semiconductor die is typically mounted on a ceramic or organic substrate. This substrate contains a grid array of metal pads or bumps, which serve as connection points for wire bonding. Wire bonding is a process where thin wires (usually made of gold or aluminum) are used to connect the semiconductor die to the substrate’s pads. These wires provide electrical connections between the internal circuitry of the die and the external leads of the package.
The advantage of WBGA packaging is its ability to accommodate a large number of connections in a relatively small area, making it suitable for high-density integrated circuits with many input-output connections. De plus, the wire bonding process allows for flexibility in routing the connections, which can be beneficial for complex IC designs.
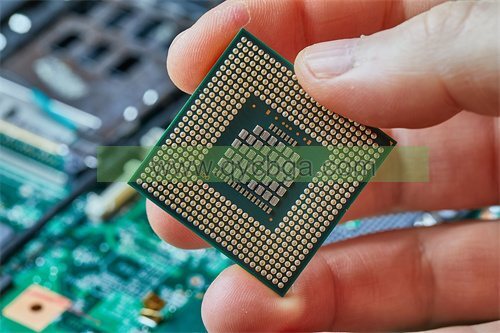
Wire Bonding BGA Substrates Manufacturer
What are the WBGA Design Guidelines?
WBGA (Wire Bonded Grid Array) design guidelines typically include considerations for various aspects of the packaging and interconnection process. These guidelines aim to ensure successful manufacturing, reliable operation, and optimal performance of the integrated circuits. Here are some common WBGA design guidelines:
- Pad Layout: The layout of the metal pads or bumps on the substrate should follow specific design rules to ensure proper alignment with the semiconductor die’s bonding pads. Pad pitch, pad size, and pad spacing are critical parameters to consider.
- Wire Bonding Requirements: Guidelines for wire bonding include wire diameter, bond pad metallization, bond pad size, and bond pad pitch. These parameters ensure reliable wire bonding connections between the die and the substrate.
- Package Dimensions: Dimensions of the WBGA package, including length, width, and thickness, should adhere to industry standards and specific application requirements.
- Thermal Considerations: Thermal management is crucial to prevent overheating of the semiconductor die during operation. Design guidelines may include recommendations for the selection of substrate materials, thermal vias, and heat dissipation mechanisms.
- Intégrité du signal: Signal integrity considerations involve minimizing signal degradation and electromagnetic interference (EMI) within the package. This may include proper placement of signal traces, ground planes, and power distribution networks.
- Assembly and Manufacturing: Design guidelines should facilitate the assembly and manufacturing processes, including pick-and-place equipment compatibility, soldering techniques, and inspection methods.
- Reliability Requirements: WBGA packages must meet reliability standards to ensure long-term performance under various environmental conditions, such as temperature cycling, humidity, and mechanical stress. Guidelines may include recommendations for underfill materials, conformal coatings, and package sealing.
- Electrical Performance: Design guidelines should address electrical performance parameters, such as impedance matching, signal propagation delay, and power distribution efficiency.
- Testability: Testability considerations involve designing the WBGA package for ease of testing during manufacturing and assembly. Guidelines may include provisions for built-in self-test (BIST) fonctionnalités, test access points, and boundary scan techniques.
- Compliance and Standards: Design guidelines should ensure compliance with industry standards and regulations, such as JEDEC standards for semiconductor packaging and IPC standards for electronic assembly.
These guidelines may vary depending on the specific requirements of the application, the complexity of the integrated circuit, and the manufacturing capabilities of the semiconductor packaging facility. Adhering to WBGA design guidelines is essential for achieving successful product development and commercialization.
What is the WBGA Fabrication Process?
The fabrication process for a WBGA (Wire Bonded Grid Array) package involves several steps to manufacture the substrate, attach the semiconductor die, perform wire bonding, and encapsulate the assembly. Here’s an overview of the typical WBGA fabrication process:
- Fabrication du substrat:
– The process begins with the fabrication of the substrate, which serves as the base for mounting the semiconductor die and providing electrical interconnections.
– Substrates can be made of various materials such as ceramic or organic laminate.
– During substrate fabrication, layers of insulating material are deposited, and metal layers are patterned to create the grid array of pads or bumps where the semiconductor die will be attached.
- Die Attachment:
– Semiconductor dies, which contain the integrated circuits, are typically fabricated separately using semiconductor manufacturing processes.
– The semiconductor die is attached to the substrate using die attach materials such as epoxy or solder.
– Precision alignment equipment ensures accurate placement of the die on the substrate.
- Liaison par fil:
– Wire bonding is the process of making electrical connections between the semiconductor die and the substrate’s pads.
– Thin wires, typically made of gold or aluminum, are bonded to the bond pads on the die and the corresponding pads on the substrate using ultrasonic or thermosonic bonding techniques.
– Wire bonding provides the electrical connections necessary for the integrated circuit to communicate with the external environment.
- Encapsulation:
– After wire bonding, the assembly is encapsulated to protect the semiconductor die and wire bonds from environmental factors such as moisture, contaminants, and mechanical stress.
– Encapsulation materials, such as epoxy molding compounds (EMCs) or glob tops, are dispensed over the wire bonded assembly.
– The encapsulation material is then cured, forming a protective covering over the semiconductor die and wire bonds.
- Singulation:
– Once encapsulation is complete, the substrate undergoes singulation to separate individual WBGA packages from the manufacturing panel.
– Singulation can be achieved using techniques such as sawing or laser cutting to cut the substrate along predefined scribe lines or streets.
- Essais et inspections:
– Finished WBGA packages undergo testing and inspection to ensure they meet quality and reliability standards.
– Testing may include electrical testing to verify functionality, as well as visual inspection and automated optical inspection (AOI) to detect defects in the packaging process.
- Emballage et expédition:
– Finally, the tested and inspected WBGA packages are packaged and prepared for shipping to customers or downstream assembly facilities.
– Packaging may involve placing the WBGA packages in trays or reels for transportation and storage.
Throughout the fabrication process, strict quality control measures are employed to ensure the reliability and performance of the WBGA packages. Each step is carefully executed to meet the requirements of the intended application and industry standards.
How do you manufacture a WBGA substrate?
Manufacturing a WBGA (Wire Bonded Grid Array) substrate involves several steps to create the base upon which semiconductor dies will be mounted and interconnected. Here’s an overview of the typical process:
- Substrate Material Selection:
– The first step is to select the substrate material. Common materials used for WBGA substrates include ceramics (such as alumina or aluminum nitride) and organic laminates (comme FR-4).
– The choice of substrate material depends on factors such as thermal conductivity, Propriétés électriques, and cost.
- Substrate Preparation:
– The substrate material undergoes preparation to ensure it is clean and free from contaminants.
– Surface treatments such as cleaning, gravure, and chemical processes may be employed to prepare the substrate for subsequent manufacturing steps.
- Layer Deposition and Patterning:
– Multiple layers of insulating material and metal traces are deposited onto the substrate using techniques such as thin-film deposition or screen printing.
– Photolithography and etching processes are then used to pattern the metal traces and create the grid array of pads or bumps where the semiconductor die will be attached.
- Finition de surface:
– The exposed metal surfaces on the substrate are treated with a surface finish to improve solderability and prevent oxidation.
– Les finitions de surface courantes comprennent l’or par immersion de nickel chimique (ENIG), organic solderability preservatives (OSP), and electroplated solder (such as electroplated tin or solder).
- Through-Hole Formation (Optionnel):
– Dans certains cas, through-holes may be drilled or punched through the substrate to provide additional mechanical support or thermal vias for heat dissipation.
– Through-holes can also be used for alignment during subsequent assembly processes.
- Essais et inspections:
– Throughout the substrate manufacturing process, quality control measures are employed to ensure the substrates meet dimensional tolerances, surface finish specifications, and other quality criteria.
– Testing and inspection may include visual inspection, dimensional measurement, electrical testing, and surface analysis techniques.
- Emballage et expédition:
– Once manufactured, the WBGA substrates are packaged and prepared for shipping to semiconductor assembly facilities or customers.
– Packaging may involve placing the substrates in trays, boxes, or reels for transportation and storage.
It’s important to note that the specific manufacturing process for WBGA substrates may vary depending on factors such as substrate material, design complexity, and manufacturing capabilities of the fabrication facility. Adherence to industry standards and quality control practices is essential to ensure the reliability and performance of the substrates in semiconductor packaging applications.How much should a WBGA substrate cost?
The cost of a WBGA substrate depends on various factors, including its size, complexité, materials used, and manufacturing volume. Prices can range from a few dollars for simple substrates to hundreds of dollars for high-performance or customized designs.
What is a WBGA substrate base material?
The base material used for a WBGA (Wire Bonded Grid Array) substrate can vary depending on the specific requirements of the application and manufacturing preferences. Common materials used for WBGA substrates include ceramics and organic laminates. Here’s a brief overview of each:
- Substrats céramiques:
– Ceramics such as alumina (Al2O3) or aluminum nitride (Aln) are commonly used as base materials for WBGA substrates.
– Ceramic substrates offer excellent thermal conductivity, which helps dissipate heat generated by the semiconductor devices.
– They also provide good dimensional stability and mechanical strength, making them suitable for high-reliability applications.
– Toutefois, ceramic substrates tend to be more expensive than organic laminates and may require specialized fabrication processes.
- Organic Laminates:
– Organic laminates, such as epoxy-based materials like FR-4 (Flame Retardant 4), are widely used as base materials for WBGA substrates.
– Organic laminates are cost-effective and readily available, making them popular for high-volume manufacturing.
– They offer good electrical insulation properties and can be fabricated using standard PCB (Printed Circuit Board) Procédés de fabrication, which may include etching, forage, and plating.
– Toutefois, organic laminates typically have lower thermal conductivity compared to ceramics, which may limit their suitability for high-power applications or environments with stringent thermal requirements.
The choice of base material for a WBGA substrate depends on factors such as thermal management requirements, electrical performance specifications, Considérations relatives aux coûts, and the intended application environment. Designers and manufacturers select the most appropriate material based on these factors to ensure the reliability, performance, and cost-effectiveness of the WBGA packages.
Which company manufactures WBGA substrates?
Many companies manufacture WBGA (Wire Bonded Grid Array) substrates, including Amkor Technology in the United States, Shinko Electric Industries in Japan, Samsung Electro-Mechanics in South Korea, and ASE Group in China. These companies have rich experience and technology in the field of WBGA substrate manufacturing, offering various types of substrates to meet different customer needs and application scenarios.
As for our company, we have advanced manufacturing processes and technology to produce high-quality WBGA substrates. Our manufacturing process covers every aspect from substrate design to the final product, strictly adhering to international standards and industry best practices. Equipped with state-of-the-art equipment and tools, including precision lithography equipment, automated etching systems, high-speed metal deposition equipment, and precise inspection and testing devices, our production line ensures top-notch quality and performance.
Here are the key features and advantages of our WBGA substrate manufacturing capability:
- High-Quality Manufacturing: We employ stringent quality control measures to ensure that each substrate meets customer requirements and standards. Our manufacturing process is carefully designed to ensure product reliability, performance, and consistency.
- Customized Services: We can customize various types of WBGA substrates according to customer requirements, including different materials, taille, layers, and electrical performance characteristics. Our engineering team can collaborate with customers to provide professional design advice and technical support.
- Quick Delivery: With efficient production capacity and flexible production scheduling systems, we can deliver customer orders promptly. We prioritize communication and collaboration with customers to ensure on-time delivery of high-quality products.
- Continuous Improvement: We are committed to continuously improving our manufacturing processes and technological capabilities to meet evolving market demands and customer requirements. We invest in research and development and technological innovation to maintain a competitive edge in the field of WBGA substrate manufacturing.
In summary, our company has the capability to manufacture high-quality, customized WBGA substrates and is willing to collaborate with customers to drive the development and progress of the electronics industry.
Quels sont les 7 Qualités d’un bon service à la clientèle?
Good customer service is essential for building strong relationships with customers and fostering loyalty. Here are seven qualities that contribute to excellent customer service:
- Empathie: Empathizing with customers and understanding their needs and concerns is crucial for providing effective support. By showing empathy, customer service representatives can connect with customers on a personal level and demonstrate that their issues are understood and valued.
- Active Listening: Active listening involves paying full attention to what the customer is saying, asking clarifying questions, and paraphrasing to ensure understanding. This skill helps customer service representatives gather relevant information, address customer concerns accurately, and make customers feel heard and respected.
- Patience: Patience is key when dealing with customers who may be frustrated, confused, or upset. Customer service representatives should remain calm and composed, even in challenging situations, and take the time necessary to resolve issues thoroughly and satisfactorily.
- Compétences en résolution de problèmes: Effective problem-solving skills enable customer service representatives to identify root causes of issues, explore possible solutions, and implement appropriate actions to resolve customer problems. Being proactive and resourceful in finding solutions demonstrates competence and builds trust with customers.
- Communication claire: Clear and concise communication is essential for conveying information effectively and ensuring mutual understanding between customer service representatives and customers. Using simple language, avoiding jargon, and providing relevant information in a straightforward manner enhance the customer experience.
- Flexibility:Being flexible and adaptable allows customer service representatives to adjust their approach based on individual customer needs and preferences. Flexibility may involve accommodating special requests, offering alternatives, or tailoring solutions to meet unique circumstances, enhancing customer satisfaction and loyalty.
- Follow-Up: Following up with customers after resolving their issues shows that their satisfaction is a priority and helps ensure that their needs have been fully addressed. Whether through a follow-up call, Messagerie électronique, or survey, proactive follow-up demonstrates commitment to customer care and provides an opportunity to gather feedback for continuous improvement.
En incarnant ces qualités, organizations can deliver exceptional customer service experiences that foster customer loyalty, positive word-of-mouth, and long-term business success.
Foire aux questions (Frequently Asked Questions)
What is a WBGA substrate?
A WBGA substrate is a type of packaging technology used in integrated circuits (Ics) or microchips. It serves as the base upon which the semiconductor die is mounted and interconnected, typically using wire bonding techniques.
What are the advantages of WBGA substrates?
WBGA substrates offer advantages such as high-density interconnections, compact form factor, and flexibility in routing connections. They are suitable for integrated circuits with a large number of input-output connections and complex designs.
What materials are used for WBGA substrates?
WBGA substrates can be made from materials such as ceramics (e.g., alumina, nitrure d’aluminium) or organic laminates (e.g., FR-4). The choice of material depends on factors like thermal conductivity, cost, and application requirements.
How are semiconductor dies attached to WBGA substrates?
Semiconductor dies are typically attached to WBGA substrates using die attach materials such as epoxy or solder. Precision alignment equipment is used to ensure accurate placement of the die on the substrate.
What is wire bonding, and how is it used in WBGA substrates?
Wire bonding is a process of making electrical connections between the semiconductor die and the substrate’s pads using thin wires (usually made of gold or aluminum). Wire bonding provides the electrical connections necessary for the integrated circuit to communicate with the external environment.
What are the typical dimensions of WBGA substrates?
WBGA substrates come in various sizes and configurations depending on the specific application requirements. Typical dimensions include the length, width, and thickness of the substrate, as well as the pitch and size of the grid array of pads.
What factors affect the reliability of WBGA substrates?
Several factors can affect the reliability of WBGA substrates, including thermal management, Propriétés du matériau, wire bonding quality, and environmental conditions. Proper design, Procédés de fabrication, and testing are essential to ensure the reliability of WBGA packages.
What industries commonly use WBGA substrates?
WBGA substrates are commonly used in industries such as telecommunications, Électronique automobile, consumer electronics, and aerospace. They are suitable for a wide range of applications requiring high-density interconnections and compact packaging.